Home » Offset Ink
Offset Ink
There are many types of offset inks, but the requirements for the machine are mainly three-roller and dual shaft mixer for production. We provide the entire process production line, and also provide the ultimate after-sales service.
Offset ink needs a butterfly mixer, twin shaft disperser (high speed and low speed), high viscosity bead mill, and hydraulic three roll mill. Why should need two kinds of mixer machine? Pre-mixing and then adjusting mixer after add additional chemicals.
3. Dyno mill for offset ink, which is designed for high viscosity material;
3). Grinding medium adopts 0.8-2.5mm, which can make the discharging material reach 5-15um
4). Higher sealing of double mechanical seal, which avoids the material leaking when operation.
5. Three roll mill for offset ink match after the dyno mill is perfectly matched for offset ink production. Franli three roll mill with hydraulic system, which has high efficiency for grinding, and the three rolls are with frequency control, which can fit different viscosity of materials. Controllable pressure and gap of rolls, make the adjustment accuracy to keep the stable discharging.
Related Products
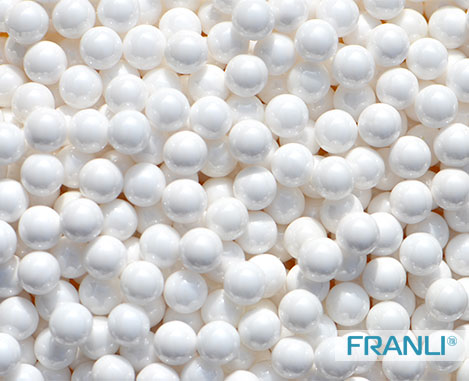
Zirconia beads for sale|Zirconia beads price
Zirconia beads, also known as zirconia grinding balls, zirconia ceramic balls, zirconia beads, ultra-fine grinding media, zirconia grinding balls.
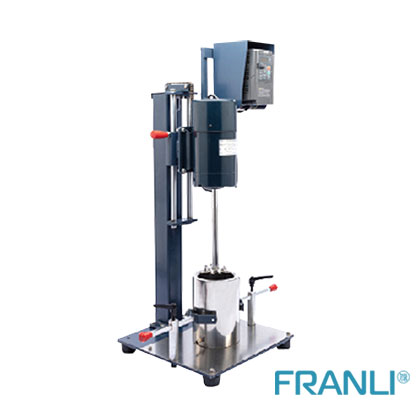
Laboratory high speed disperser
The laboratory high speed disperser can realize multiple functions in one machine, and perfectly realize the functions of dispersion, grinding, stirring, etc.
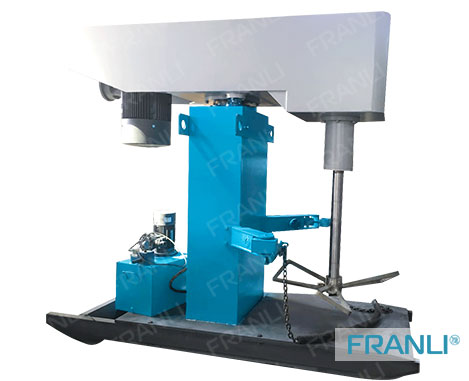
Butterfly Disperser
This kind of butterfly mixer is used in offset ink, putty etc industry. The butterfly dispersing mixer is a product with the functions of dispersing and stirring (wall scraping) developed on the basis of a single-axis hydraulic lifting disperser.
After Sales Support
News
Laboratory Reactor: Guide to Stirring System
The laboratory reactor is composed of a pot body, a pot cover, an agitator, a jacket, a support and transmission device, a shaft seal device, etc.
Grinding Media for Bead Mill | Zirconia Beads & Zirconium Silicate Beads
Bead mills mainly use grinding balls as media, and use impact, extrusion, and friction to achieve the final grinding effect, which mainly depends on the size and hardness of the grinding beads, the filling rate of the grinding beads, and the collision frequency adjustment between the grinding beads and the particles.
Overview of Laboratory Reactor
Laboratory reactors, also known as lab reactors, are essential tools in scientific research, product development, and process optimization. These reactors provide a controlled environment for conducting chemical reactions, mixing, dispersing, and homogenizing processes.
Bead mills | Manufacturing technology in various industries
Bead mills, also known as sand mills or grinding mills, are versatile machines widely used across various industries for the wet grinding and dispersion of solid particles in liquid media.
Ribbon Blender Mixer Equipment
A ribbon blender mixer, also known as a ribbon mixer or horizontal ribbon blender, is a powerful industrial machine designed for thorough and efficient blending of various materials.
What is A Stainless Steel Reactor?
Stainless steel reactors are essential equipment in various industries, including chemical, pharmaceutical, biotechnology, and food processing.