Home » Exploring the benefits of wet and dry grinding with the help of bead mill
Exploring the benefits of wet and dry grinding with the help of bead mill
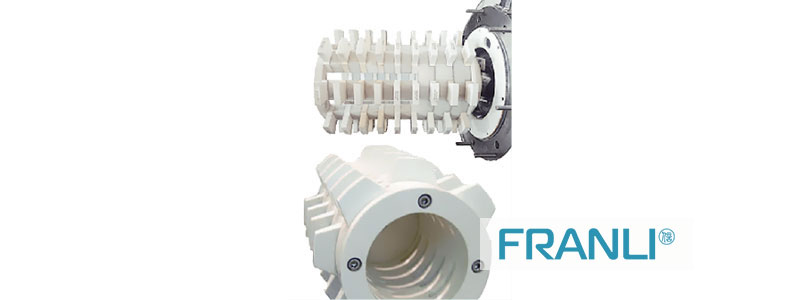
Exploring the definitions of grinding, micronization, milling, wet/dry, and likewise
So, what do we understand by micronization here within the technology of particles? The term here is a lot more specific, mainly referring to the reduction in particles in the size range of sub-10 micron. So, every micronizing is associated with grinding, but not all grinding is going down to the particle level of micronizing for the bead milling process.
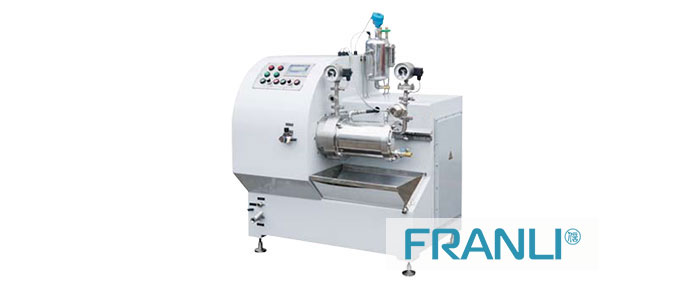
The terminologies involved here with the wet and dry grinding are often the overarching words describing basically each of the two other bead mill working principles here. The processes here are quite different, although the goals here lie to be the same. Dry grinding under the bead mill working principle makes use of the contact of the particle to particle for the reduction in size along with getting the wet grinding involved here with dispersing of the bead mill into the liquid with the use of solid grinding media in terms of reduction in size.
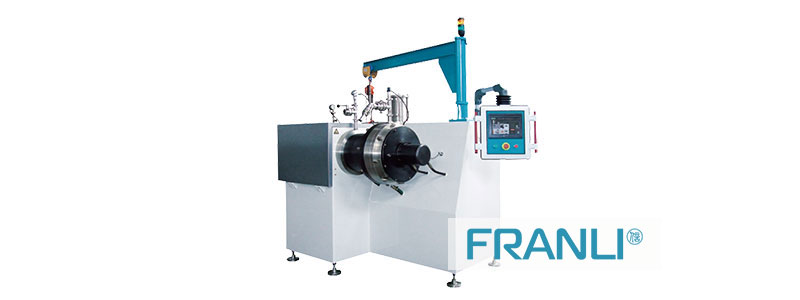
Similarities & differences between wet and dry grinding
Dry grinding is making use of a single pass process where the material is going in and is expelled once in a bead mill, for instance. There is the slurry that is exposed to the grinding media over and over for a longer time if required till the size desired for the particle is achieved here, being a process of recirculation as used by the bead mill manufacturers.
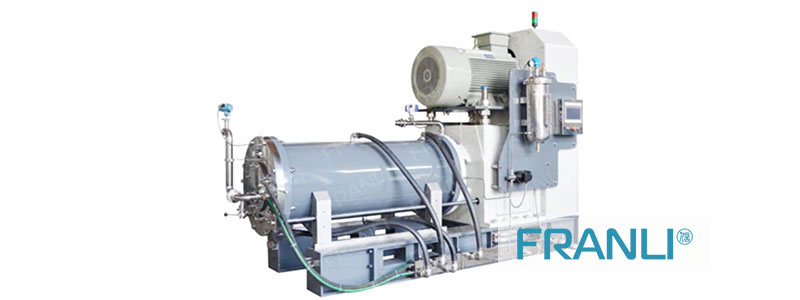
There might be plenty of abrasives within the material that can over time damage the tool here in terms of dry grinding and in knowing the bead mill price. The carrier fluid of the wet grinding or the material here should be compatible chemically with surfactants and solvents that can eat off the grinding media of the equipment as well as the parts that are used for agitating the media itself.
It is extremely important that the grinding media of the equipment do not end up within the product itself, irrespective of it being dry or wet.
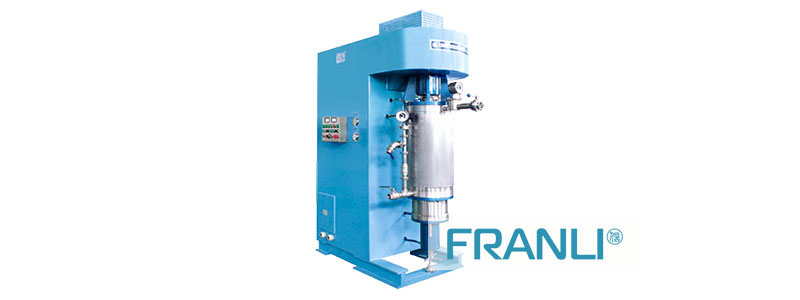
Making the right selections
If there is a specific pyrotechnic material going through the dry grinding is something that needs to be checked. Compared to the wet grinding, the product here has greater characteristics compared to the rest. This alone is enough to go ahead in selecting dry.
The other set of considerations here is the size of the target particle here. Dry grinding allows the particles to head down to the size of a single-digit micron in general. The particles are therefore reduced down to the range of the bead grinding machine by the regular wet grinding method. Wet is the ideal way to achieve your required specifications, while the simplicity of dry grinding would often be considered as the first method included here with the goal of achieving the smaller size.
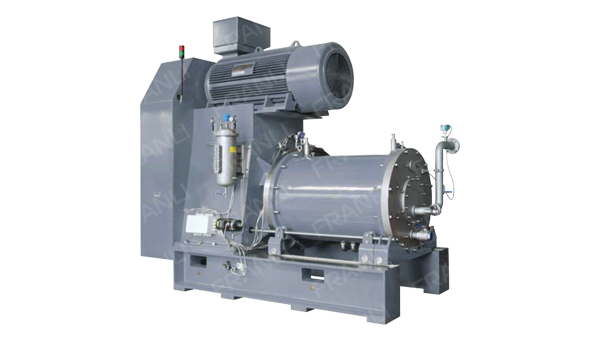
Considerations to be taken
Packaging is also considered a factor of consideration in terms of the bead mill design. Packaging needs to be able to keep up to a determined number of barrels as grinding is a continuous affair here.
It comes into play here with the need to formulate for the dry as well as wet grinding processes. It is highly efficient in terms of including a lot of particle solid within the mix here since it is extremely obvious. It would be required here in terms of getting additional additives that are detrimental based on the earlier trials as well as the experiences of the bead mill design.
There is a quality of assurance processes within the house that is included within the testing capabilities of the analytical lab. It is vital enough to have the services available for making sure of the end quality of the product while this might not be determining a single method over the rest present here.
It is endless when it comes to the list of materials that can be dry or wet ground with the help of a bead mill.
So, you can name it the way you like, be it grinding or milling, as one thing applies to both the methods proven out, with each needing the upfront guidance of the experts like that of company like Franli and their dedicated capabilities.
Copyright Notice :
This article only represents the author’s point of view.
This article is published under the authorization of the author.
Source: Franli
This article address : Exploring the benefits of wet and dry grinding with the help of bead mill
Related Products
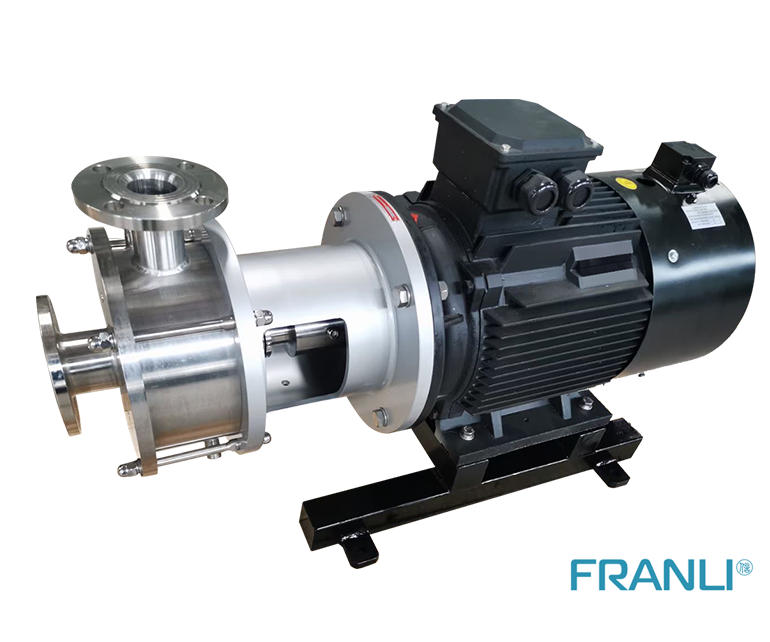
Inline Homogenizer
The Inline homogenizer is mainly used for mixing and homogenizing materials, dispersing, and emulsifying, and it is versatile and versatile. The inline homogenizer is generally used as a primary and intermediate material for mixing, and homogenizing.
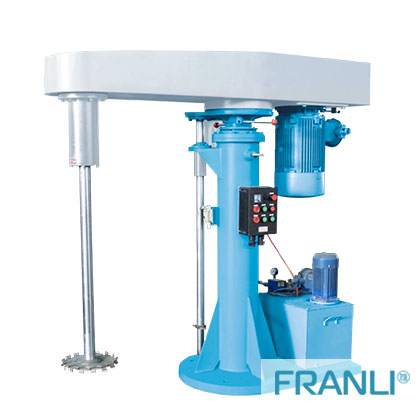
HSD High Speed Disperser
FRANLI high-speed disperser is widely used in coatings, paints, dyes, inks, latex paints, adhesives, papermaking, silica gel, putty powder, color pastes, and other chemical industries, and it can be used with three-roll mills, bead mills, and reactors.
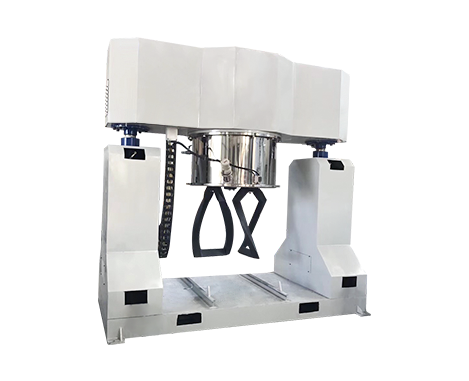
Double planet mixer
Double planet mixer is a new type of mixing equipment with high performance, high speed, easy cleaning, and maintenance. The two agitators of the equipment revolve around the axis while rotating.
News
Laboratory Reactor: Guide to Stirring System
The laboratory reactor is composed of a pot body, a pot cover, an agitator, a jacket, a support and transmission device, a shaft seal device, etc.
Grinding Media for Bead Mill | Zirconia Beads & Zirconium Silicate Beads
Bead mills mainly use grinding balls as media, and use impact, extrusion, and friction to achieve the final grinding effect, which mainly depends on the size and hardness of the grinding beads, the filling rate of the grinding beads, and the collision frequency adjustment between the grinding beads and the particles.
Overview of Laboratory Reactor
Laboratory reactors, also known as lab reactors, are essential tools in scientific research, product development, and process optimization. These reactors provide a controlled environment for conducting chemical reactions, mixing, dispersing, and homogenizing processes.
Bead mills | Manufacturing technology in various industries
Bead mills, also known as sand mills or grinding mills, are versatile machines widely used across various industries for the wet grinding and dispersion of solid particles in liquid media.
Ribbon Blender Mixer Equipment
A ribbon blender mixer, also known as a ribbon mixer or horizontal ribbon blender, is a powerful industrial machine designed for thorough and efficient blending of various materials.
What is A Stainless Steel Reactor?
Stainless steel reactors are essential equipment in various industries, including chemical, pharmaceutical, biotechnology, and food processing.