Home » The factors affecting high & low viscosity fluids with high speed disperser
The factors affecting high & low viscosity fluids with high speed disperser
The end results that are the desired ones are mainly quite uniform and well-blended into mixtures when you are blending high as well as lowered viscosities of liquid with the help of a high speed disperser. While blending these substances together with the higher viscous materials or blending higher viscosity fluids without any additional help can be a challenge in itself in terms of attaining the desired uniformity levels.
High & low viscosity liquids
High & low viscosity liquids
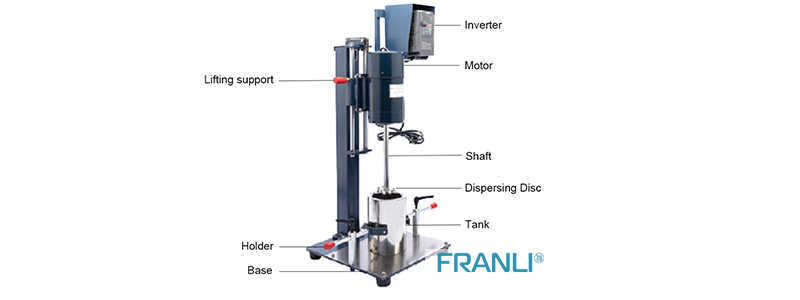
Deciding between disperser and mixer
· Shear
This is the process that mainly happens at the number of Reynolds and occurs due to the differed velocities of the various streamlines. An additional amount of heat is thereby generated, and particles tend to wear off as an outcome of the stress having been created among the particles due to the shear. In the process of deagglomeration, shear is quite helpful but can prove to be detrimental once attempting in terms of sustaining the size of the particles during the mixing process.
· Temperature boundaries
An additional amount of equipment is required for heating or cooling out the system when the temperature here is maintained to almost a certain range of the mixing done through the high speed disperser. There is an extra cost that is associated with each of these devices here in terms of installing, operating, or maintaining them.
· Economic considerations
The idea of mixing or the system of dispersing you may wish for your project does not make the most in terms of economic viewpoints. The product can be of greater demand to that of the cost of the system, but the additional startup time is also anticipated here in terms of the amount of time the product is taking for manufacturing and the profit that is projected.
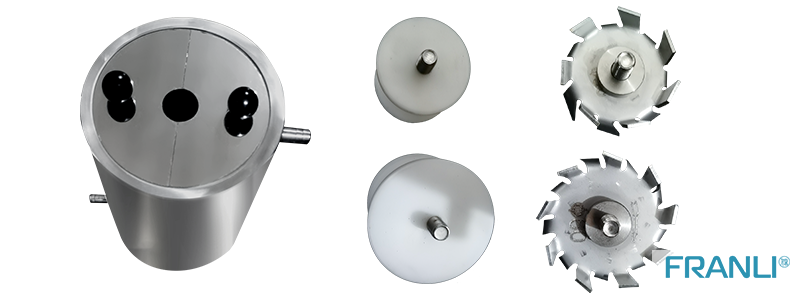
Difference between dispersing, mixing, and milling
MIXING
The flow of the material all through the vessel or the high speed dispersion mixer is dependent on the kind and the size of every particle along with the impeller’s rotating speed in terms of mixing.
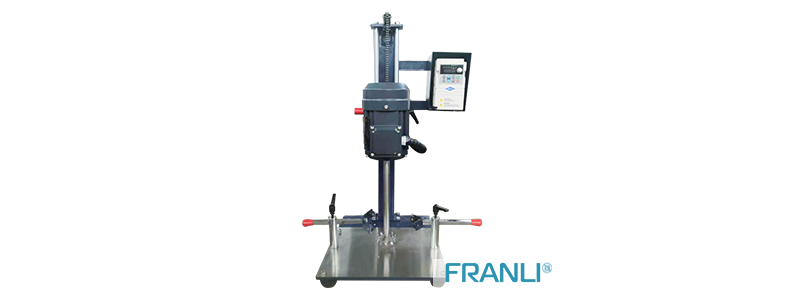
DISPERSING
The main aim of the dispersion is to mix the solids with the liquids or vice versa with the help of the high speed disperser. The end product here should be possessing the finer materials having the goal to achieve an even spread of particles within the liquid here. The machine would be taking the particles and breaking them down for de-agglomerating them to create a mixture of homogenous material with the help of dispersion. The complete surface area is completely inaccessible due to the liquid solution if the particles remain agglomerated or grouped together. Dispersion, therefore, breaks them and exposes their surface area further on. Wetting is the terminology used here.
Dispersion is generally driven by the sheer process, while mixing is driven by the flow. The action needed for dispersing the particles along the spectrum that is soluble is created by the impeller edge. The process here needs a greater amount of energy and higher speed compared to the other conventional methods for mixing.
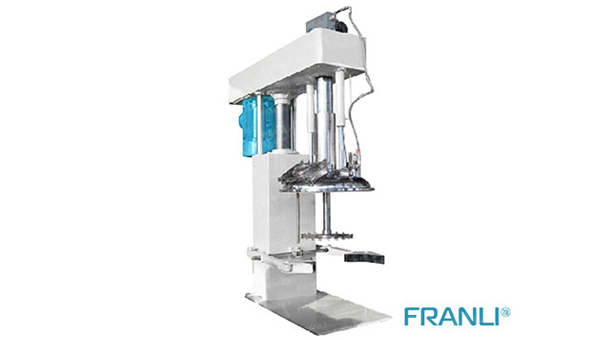
MILLING
The mill can thereby be adapted, and the temperature of the environment controls can be attained at the desired outcomes as it all depends on the final best size of the particle. In the market today, you are sure to come across different kinds of mills, and the process of selecting one can be quite tough. The suppliers of the equipment also offer trial services to make sure of the right match between the application and equipment, although there are various factors to investigate while selecting a high speed disperser unit.
To conclude
Copyright Notice :
This article only represents the author’s point of view.
This article is published under the authorization of the author.
Source: Franli
This article address : The factors affecting high & low viscosity fluids with high speed disperser
Related Products
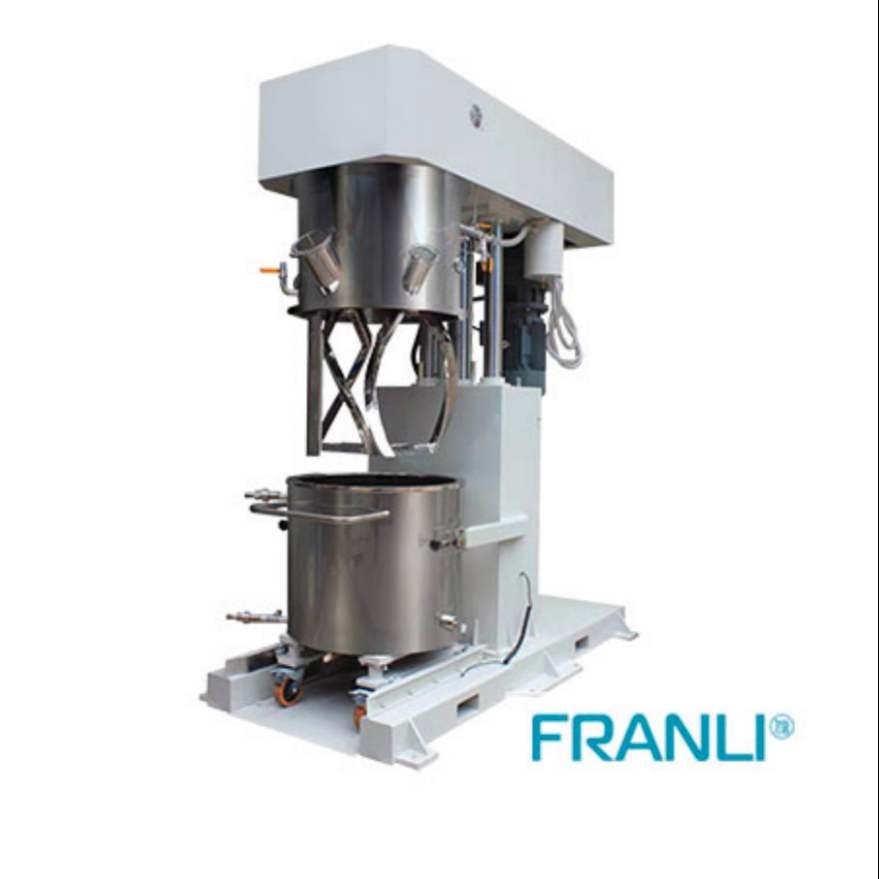
Vacuum Double Planetary Mixer
A Vacuum double planetary mixer is an essential part of any industry to mixing particular material. A double planetary mixer contains two blades that help mix by revolving on their axis in the vessel.
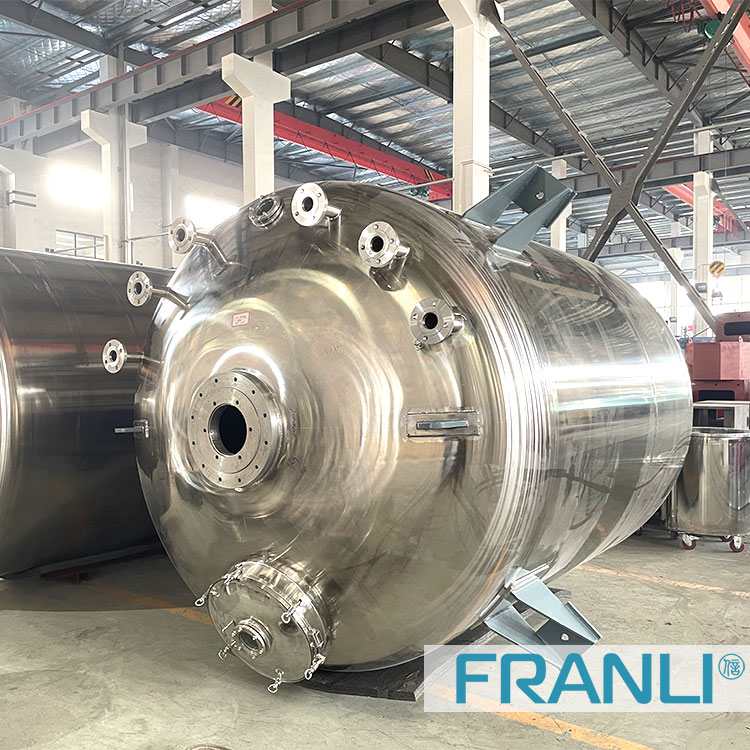
Stainless Steel Reactor
The reaction vessel is a comprehensive reaction vessel. The structure, function, and configuration accessories of the reaction vessel are designed according to the reaction conditions.
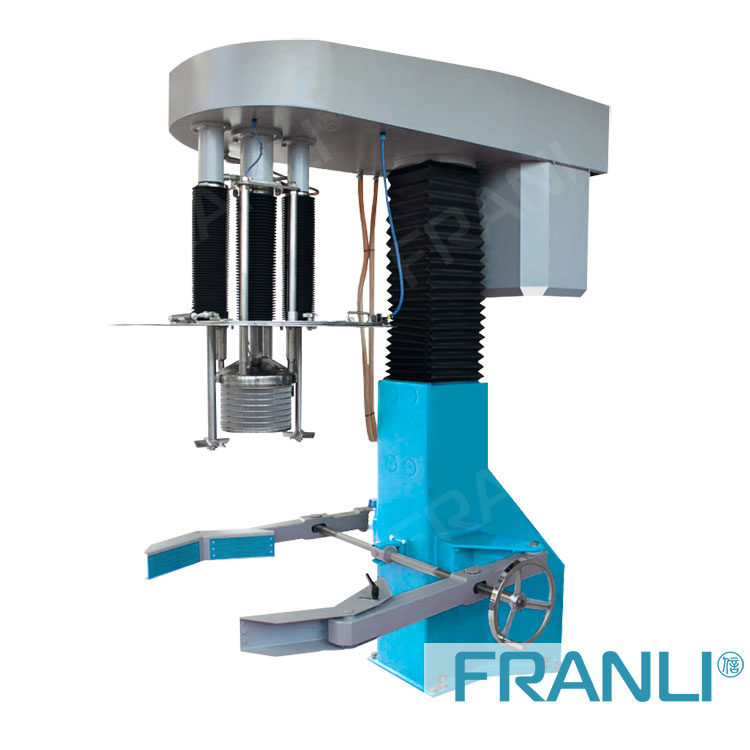
Basket Mill With Mixer
Basket mill with mixer is an indispensable equipment in coatings, ink, cosmetics, and other industries. Its main function is to provide multi-functional dispersion.
News
Laboratory Reactor: Guide to Stirring System
The laboratory reactor is composed of a pot body, a pot cover, an agitator, a jacket, a support and transmission device, a shaft seal device, etc.
Grinding Media for Bead Mill | Zirconia Beads & Zirconium Silicate Beads
Bead mills mainly use grinding balls as media, and use impact, extrusion, and friction to achieve the final grinding effect, which mainly depends on the size and hardness of the grinding beads, the filling rate of the grinding beads, and the collision frequency adjustment between the grinding beads and the particles.
Overview of Laboratory Reactor
Laboratory reactors, also known as lab reactors, are essential tools in scientific research, product development, and process optimization. These reactors provide a controlled environment for conducting chemical reactions, mixing, dispersing, and homogenizing processes.
Bead mills | Manufacturing technology in various industries
Bead mills, also known as sand mills or grinding mills, are versatile machines widely used across various industries for the wet grinding and dispersion of solid particles in liquid media.
Ribbon Blender Mixer Equipment
A ribbon blender mixer, also known as a ribbon mixer or horizontal ribbon blender, is a powerful industrial machine designed for thorough and efficient blending of various materials.
What is A Stainless Steel Reactor?
Stainless steel reactors are essential equipment in various industries, including chemical, pharmaceutical, biotechnology, and food processing.