Features to consider while buying a double planetary mixer
It is considered the most exciting prospect in terms of purchasing as well as replacing your first double planetary mixer. It is extremely vital to ensure that you are investing in equipment pieces like the double planetary mixer to resolve your issues for now before you select just any old version of the planetary mixer. As you are growing in the proper direction, the double planetary mixer can add efficiency and streamline your support to your business here.
Selecting the planetary model
It is the kind of model type that one is using if you are seeking a massive range of functionalities for your mixers. They will be dedicated to the denser dough, including the ones for the bread or pizzas, then you can go ahead with the spiral one if you look for this kind of mixer.
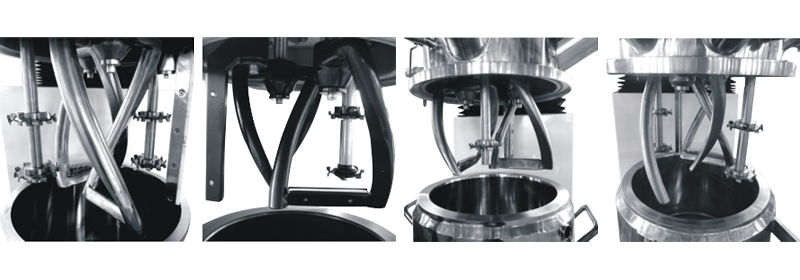
Claw type double planetary mixer
Determining the motor capacity through absorption ratio

Features to Look For
In terms of viscosity along with the dense applications here, the vacuum planetary mixer along with the planetary dispersers is used commonly. By orbiting all around the vessel here, the agitators can easily rotate along their own axes. The outcomes here are extremely thorough with the mixing action irrespective of the rheology of the product here. Until the state of the homogenous is achieved here, the batch components are being thoroughly recombined and moved from a single area of the vessel to the rest. These planetary mixers are also being used with the vacuum drying equipment as well as granulation aside from their main usage at the compounding of the formulations of the higher viscosity.
Let us go through a few of the guidelines here that can assist you in terms of selecting the best vacuum planetary mixer.
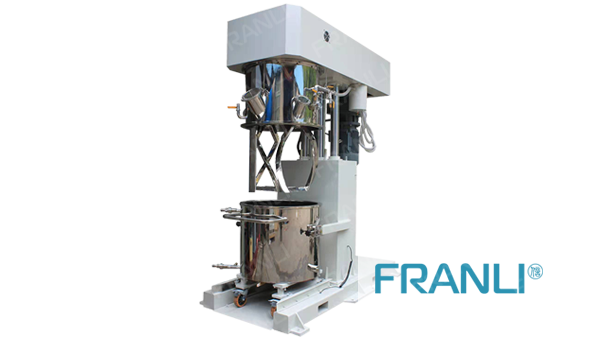
The range of viscosity in terms of application
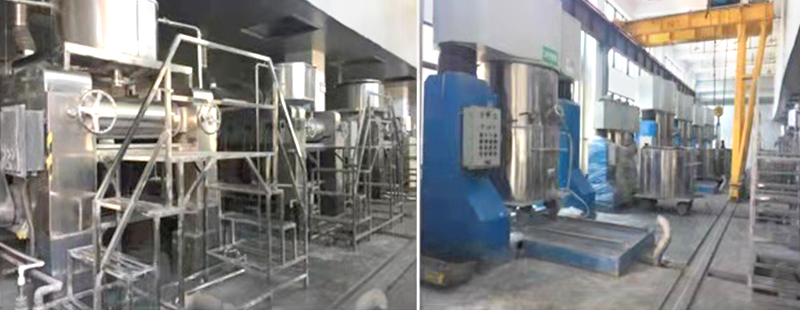
The need for high-speed agitations
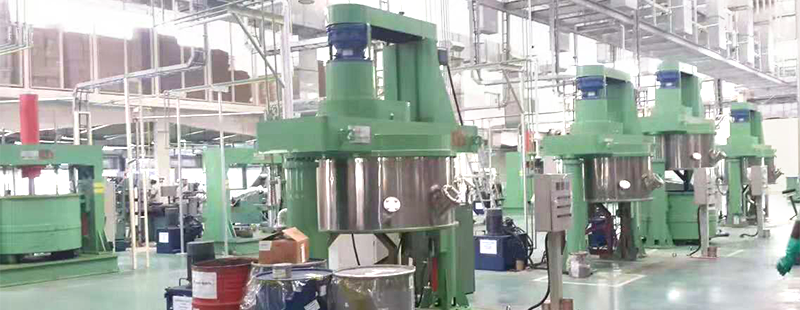
Preventing the climbing issues
There are a few of the materials that generally tend to climb up through the vertical flights of the stirrer that are rectangular ones and out through the mixing vessels, whether they are within the double planetary mixer or that of the disperser. The intensive cleanup is necessitated through the characteristic migration of the materials of the batches that reduces the efficiencies in terms of mixing.
Optimizing the discharge process
Copyright Notice :
This article only represents the author’s point of view.
This article is published under the authorization of the author.
Source: Franli
This article address : Features to consider while buying a double planetary mixer
Related Products
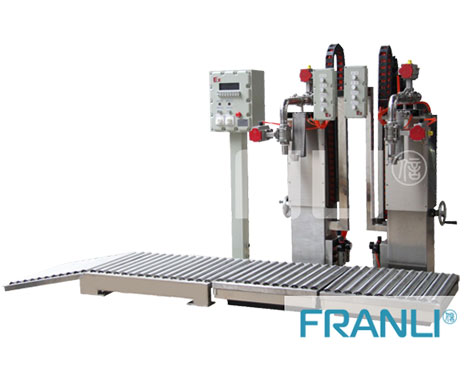
Drum Filling Machine
Drum filling machine is widely used in paint and ink industries. The drum has two kinds of material, plastic or metal. And there are many types of drums
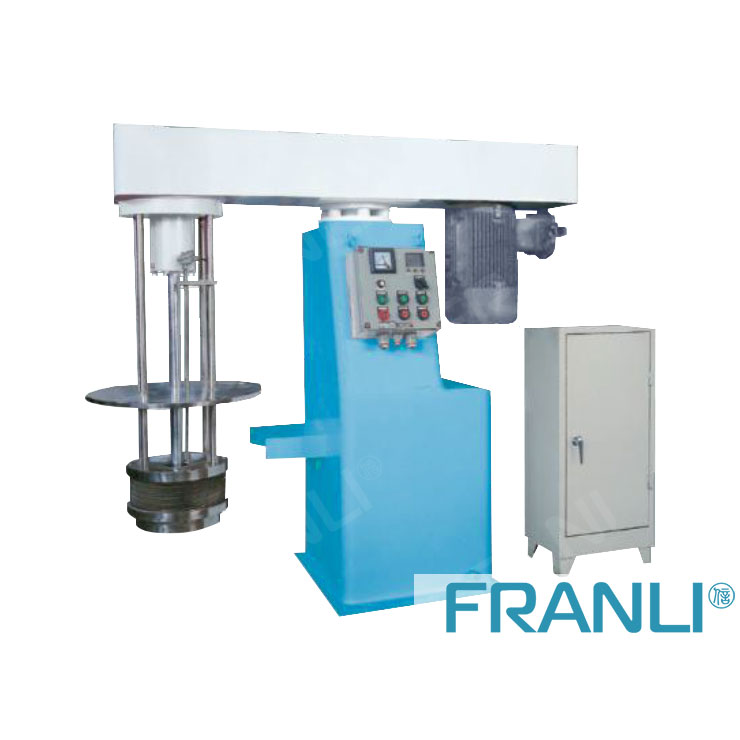
Immersion Mill
FRANLI immersion mill is a new type of discontinuous ultrafine mill integrating grinding and dispersing. After many studies and data, it is shown that this immersion mill is especially suitable for the production and grinding of small batches and multi-variety products.
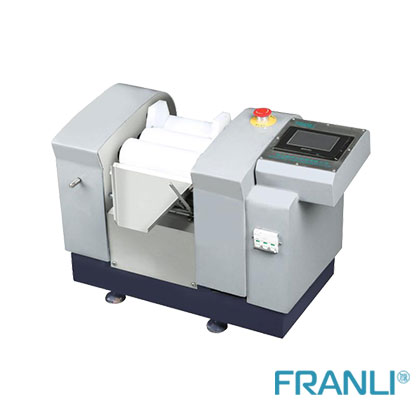
Triple roller mill
Three-roller mills are also called triple roller mills. In daily work, they can be divided into Lab triple roller mills and production triple roller mills. They are mainly used in ink, paint, paint and other industries.
News
Laboratory Reactor: Guide to Stirring System
The laboratory reactor is composed of a pot body, a pot cover, an agitator, a jacket, a support and transmission device, a shaft seal device, etc.
Grinding Media for Bead Mill | Zirconia Beads & Zirconium Silicate Beads
Bead mills mainly use grinding balls as media, and use impact, extrusion, and friction to achieve the final grinding effect, which mainly depends on the size and hardness of the grinding beads, the filling rate of the grinding beads, and the collision frequency adjustment between the grinding beads and the particles.
Overview of Laboratory Reactor
Laboratory reactors, also known as lab reactors, are essential tools in scientific research, product development, and process optimization. These reactors provide a controlled environment for conducting chemical reactions, mixing, dispersing, and homogenizing processes.
Bead mills | Manufacturing technology in various industries
Bead mills, also known as sand mills or grinding mills, are versatile machines widely used across various industries for the wet grinding and dispersion of solid particles in liquid media.
Ribbon Blender Mixer Equipment
A ribbon blender mixer, also known as a ribbon mixer or horizontal ribbon blender, is a powerful industrial machine designed for thorough and efficient blending of various materials.
What is A Stainless Steel Reactor?
Stainless steel reactors are essential equipment in various industries, including chemical, pharmaceutical, biotechnology, and food processing.