Home » The Most Reliable Ointment Mill Machine For Industry
The Most Reliable Ointment Mill Machine For Industry
With the advancement of new technology globally, the cosmetic industries have also increased as more people have realized the need to apply cosmetics to their bodies for nourishment and beauty. In the past, cosmetics were meant only for women, but nowadays even men apply the same. This phenomenon has made more industries come up with more advanced machines to grind, conglomerate, and refine chemicals used to manufacture cosmetics. This machine uses high shear force to dissolve active molecules and standardized viscous materials. An ointment mill machine is a well-known machine for grinding molecules into smaller particles in the ointment industries. People globally prefer ointments that penetrate deeply into the skin, and that is why these industries must manufacture machines that have high precision in grinding a material into finer particles. As people pay more attention to the quality of cosmetics manufactured, industries are also on watch for the type, nature, and quality of the roll mill machine used to meet the customers’ demands.
Working principle of ointment mill machine in the ointment industry
Rollers running at varying speeds grind the particle sizes, creating shearing actions. The guides on top of the rollers aid the material onto the backseat of the rollers. The material then moves through the mill onto the scraper plate. If the required level of trituration has been attained, then the material may be dispensed. Ointment mill cleaning is accomplished by rotating the equipment, spraying alcohol on paper towels, and manually rotating the roller during cleaning. The best machine is the one that produces desirable results at a shorter duration.
There are different types of three roll mills.
● Hydraulic three roll mills
● Laboratory three roll mill
● Manual three-roll mill
Advantages of three roll-mills machines:
The machine produces tiny particles which are uniform. The pressure-induced to the materials breaks down into finer particles to produce a quality product. Three-roll mill is often used in various grades of the cosmetics industry from medium viscosity production to high grade. Using high-end machinery, it can decompose various pigments, inks, paints, and lubricants. These machines have been modified in such a way that it generates less heat.
It’s environment friendly due to the generation of less noise to the surrounding. Customers prefer machines that make less noise as more noise may cause hearing problems.
The machines help in saving energy due to their nature in low friction between particles. Particles rubbing against each other uses more energy. For three roll mills, the case is different as the force of friction is low.
Generation of less dust from the milling materials:
Conclusion:
Different types of three-roll mills function differently. Manual, hydraulic, and laboratory types offer desirable services. These machines are simple and faster to operate. They are also environmentally friendly due to their production of less noise and dust.
The Franli Company offers the best ointment mill machine that operates faster and accurately. Most of the companies prefer machines that do not require more labor and also generate effective outputs. For this case, we are recommending this company for quality services.
Copyright Notice :
This article only represents the author’s point of view.
This article is published under the authorization of the author.
Source: Franli
This article address : The Most Reliable Ointment Mill Machine For Industry
Related Products
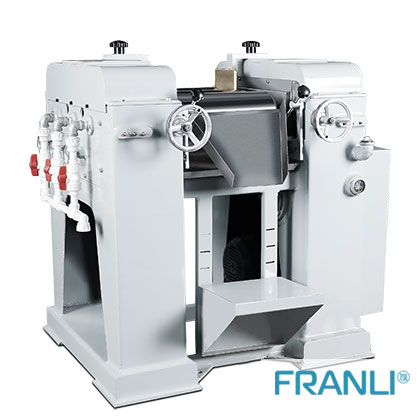
Manual 3 roll mill
FRANLI Manual three roll mill is widely used in milling paste material including paint, inks, China ink, pigment, coatings, food, cosmetics, and so on. (Not applicable for roller corrosion material). It is also used in cable material, artificial plastics, soap…
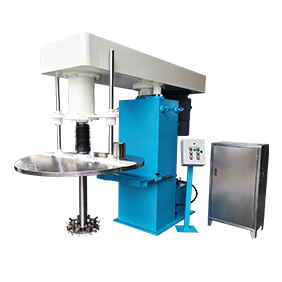
High Speed Disperser
Architectural waterproof coating production equipment The preparation process of the high-speed disperser machine mainly includes the dispersion of pigments and fillers, grinding, coating preparation, toning, etc.
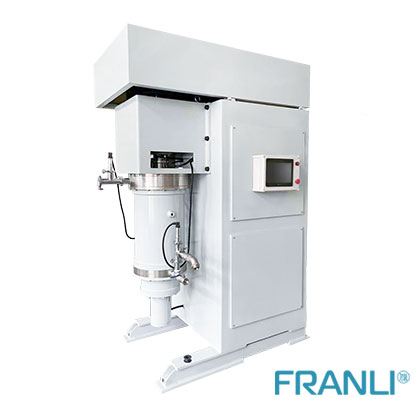
Pearl Mill
The pearl mill grinding chamber with pins, specially designed grinding shaft. We install an advanced cooling system for high temperature of viscosity material. Pearl mill has a German mechanical seal, NSK bearings. Which avoids the leaking of material.
News
Laboratory Reactor: Guide to Stirring System
The laboratory reactor is composed of a pot body, a pot cover, an agitator, a jacket, a support and transmission device, a shaft seal device, etc.
Grinding Media for Bead Mill | Zirconia Beads & Zirconium Silicate Beads
Bead mills mainly use grinding balls as media, and use impact, extrusion, and friction to achieve the final grinding effect, which mainly depends on the size and hardness of the grinding beads, the filling rate of the grinding beads, and the collision frequency adjustment between the grinding beads and the particles.
Overview of Laboratory Reactor
Laboratory reactors, also known as lab reactors, are essential tools in scientific research, product development, and process optimization. These reactors provide a controlled environment for conducting chemical reactions, mixing, dispersing, and homogenizing processes.
Bead mills | Manufacturing technology in various industries
Bead mills, also known as sand mills or grinding mills, are versatile machines widely used across various industries for the wet grinding and dispersion of solid particles in liquid media.
Ribbon Blender Mixer Equipment
A ribbon blender mixer, also known as a ribbon mixer or horizontal ribbon blender, is a powerful industrial machine designed for thorough and efficient blending of various materials.
What is A Stainless Steel Reactor?
Stainless steel reactors are essential equipment in various industries, including chemical, pharmaceutical, biotechnology, and food processing.