Home » Three Roll Mills: Their mechanism, advantages, types, and tips to find the best product
Three Roll Mills: Their mechanism, advantages, types, and tips to find the best product
Mechanism
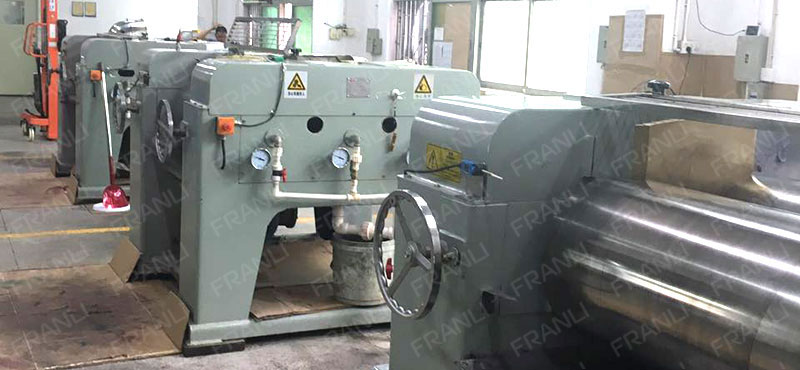
Advantages
• User-friendly:
• Flexibility
• High utility:
• Provides greater flexibility as per production volume:
Types of three roll mills
• SG roll mills
• Hydraulic roll mill types
• Lab type roll mills
• Vertical roller mills
• Heating type
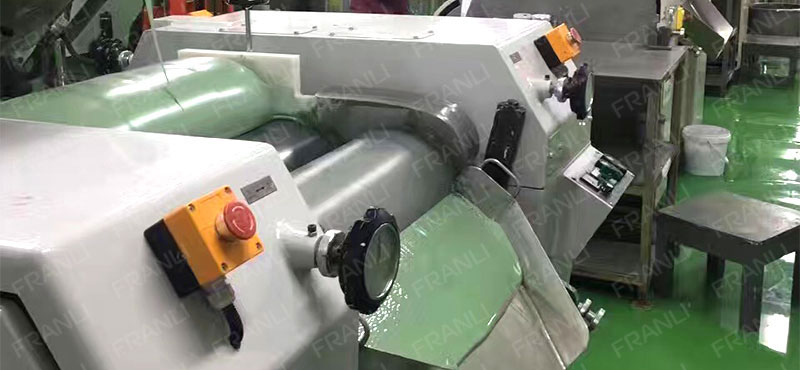
Tips for finding the best device
Copyright Notice :
This article only represents the author’s point of view.
This article is published under the authorization of the author.
Source: Franli
This article address : Three Roll Mills: Their mechanism, advantages, types, and tips to find the best product
Related Products
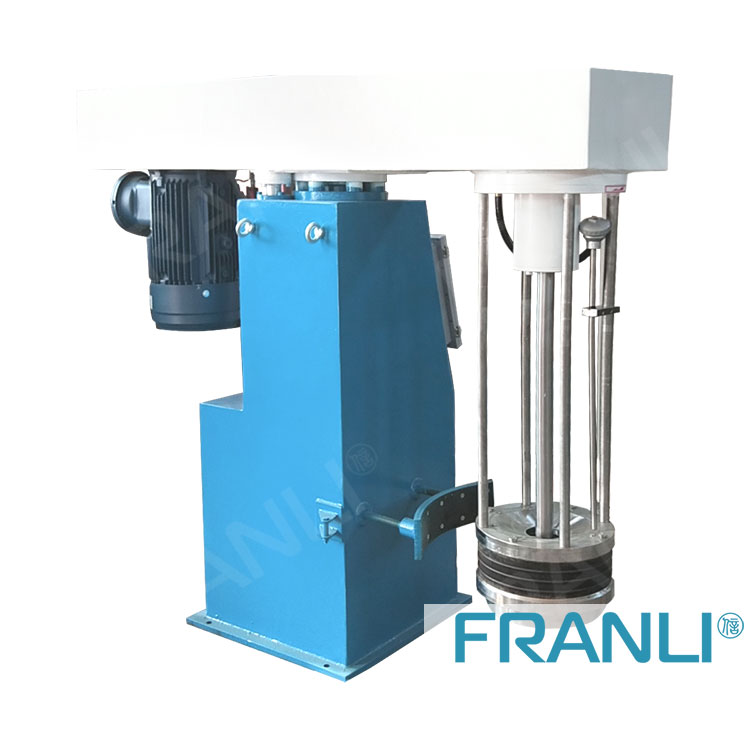
Basket Mill
Franli Basket Mill focuses on low energy, no hot spots, controlling constant temperature, higher production, the flexibility of batch size, and a wide range of product viscosities that can be processed well.
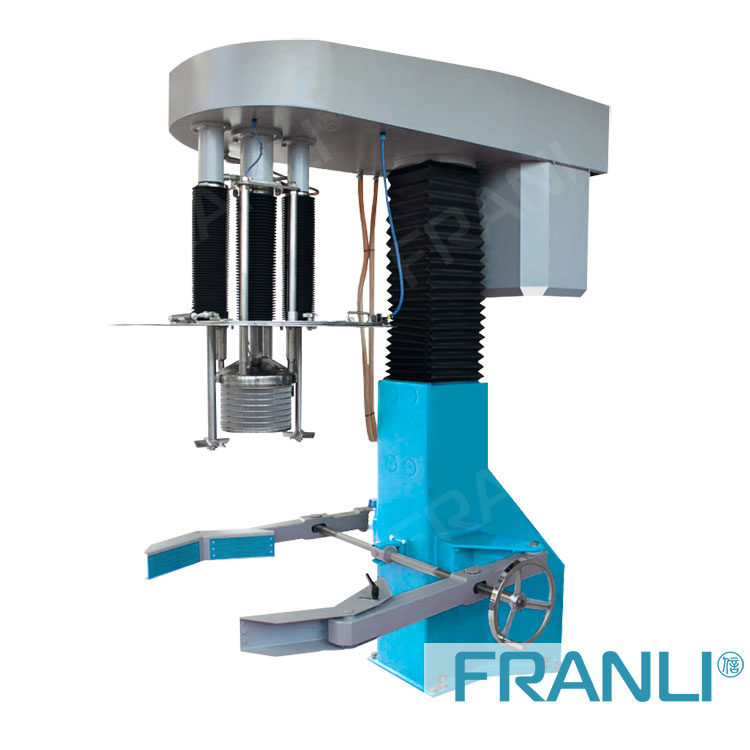
Basket Mill With Mixer
Basket mill with mixer is an indispensable equipment in coatings, ink, cosmetics, and other industries. Its main function is to provide multi-functional dispersion.
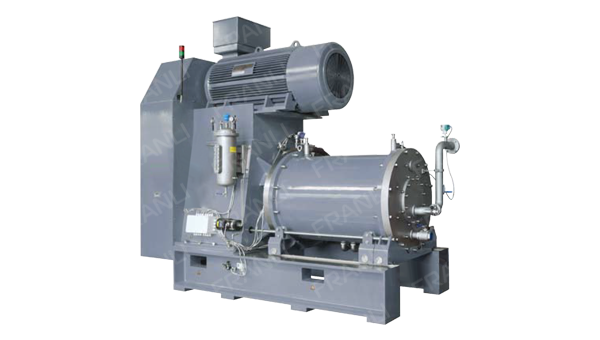
Agitator bead mill
Agitator bead mill’s pins are uniform distributed type, pre-milling your material when feeding material into chamber. The agitator bead mill has a stronger power motor, material milled by bead, and pins in the chamber.
News
Laboratory Reactor: Guide to Stirring System
The laboratory reactor is composed of a pot body, a pot cover, an agitator, a jacket, a support and transmission device, a shaft seal device, etc.
Grinding Media for Bead Mill | Zirconia Beads & Zirconium Silicate Beads
Bead mills mainly use grinding balls as media, and use impact, extrusion, and friction to achieve the final grinding effect, which mainly depends on the size and hardness of the grinding beads, the filling rate of the grinding beads, and the collision frequency adjustment between the grinding beads and the particles.
Overview of Laboratory Reactor
Laboratory reactors, also known as lab reactors, are essential tools in scientific research, product development, and process optimization. These reactors provide a controlled environment for conducting chemical reactions, mixing, dispersing, and homogenizing processes.
Bead mills | Manufacturing technology in various industries
Bead mills, also known as sand mills or grinding mills, are versatile machines widely used across various industries for the wet grinding and dispersion of solid particles in liquid media.
Ribbon Blender Mixer Equipment
A ribbon blender mixer, also known as a ribbon mixer or horizontal ribbon blender, is a powerful industrial machine designed for thorough and efficient blending of various materials.
What is A Stainless Steel Reactor?
Stainless steel reactors are essential equipment in various industries, including chemical, pharmaceutical, biotechnology, and food processing.