Home » Grinding equipment needed to make cosmetics
Grinding equipment needed to make cosmetics
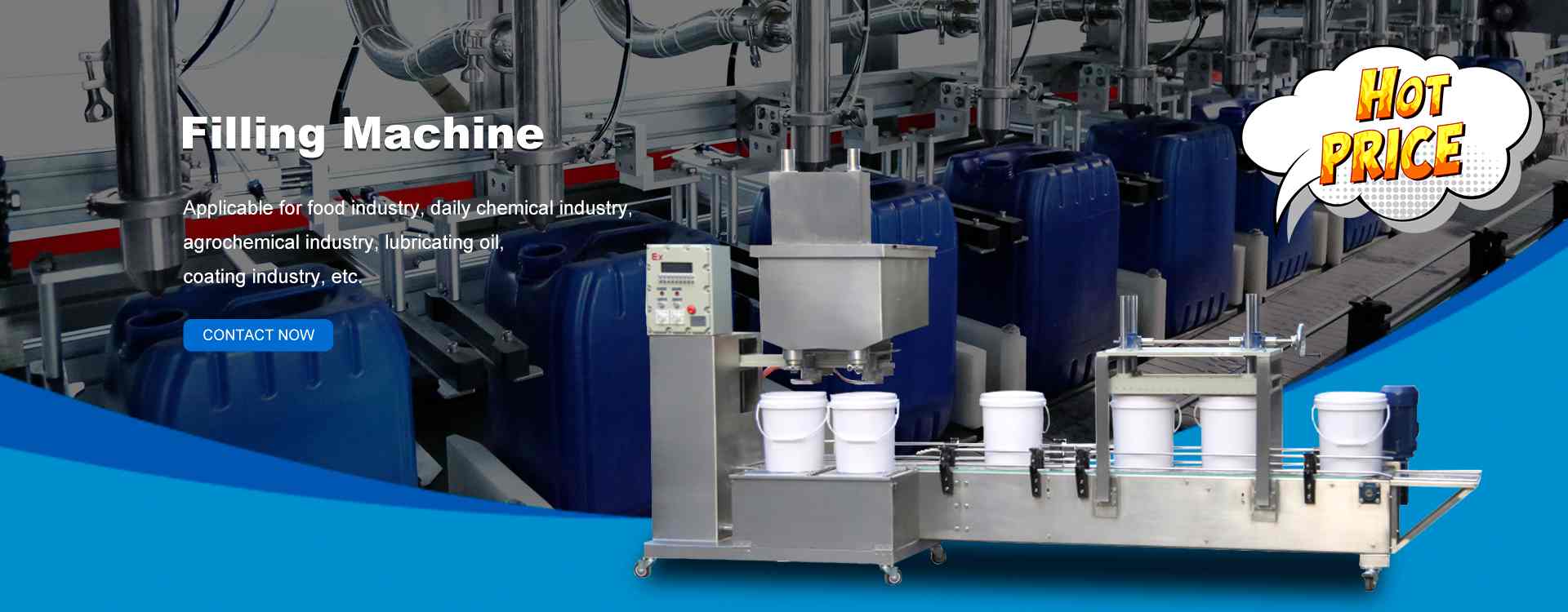
Cosmetics belong to the category of fine chemicals. The vast majority of cosmetics production uses compound technology, which has the characteristics of fewer chemical reactions and strict hygiene requirements. The production equipment can be roughly divided into:
(1) Product manufacturing equipment;
(2) Forming, filling, and packaging equipment.

Emulsion preparation technology
The commonly used equipment for cream cosmetics mainly includes various types of mixing equipment, homogenization equipment, three roll mills, vacuum degassing equipment, etc.
Emulsification equipment
Mixing equipment
1. Vertical mixer
2. Bedroom mixer
3. Eccentric mixer
4. Mobile mixer
This type of mixing equipment has the advantages of portability, flexibility, and simplicity, and is suitable for small-scale laboratory research and production.
The mixing efficiency is related to the design of the paddle of the mixer. According to the different blades, it can be divided into paddle agitator, propeller agitator, turbine agitator. This type of equipment is generally used for premixing the oil phase and the water phase.
Homogeneous emulsification equipment
Vacuum homogenizing emulsifier
It is composed of a sealed vacuum container part and a stirring part. The mixing part consists of a homogeneous mixer and a frame mixer with a scraper. The stirring speed of the homogeneous mixer is mostly 350~3500r/min, which can be steplessly adjusted; the speed of the scraper stirrer is 10~100r/ min, is slow stirring, its function is to promote the heat transfer of the heat transfer surface during heating and cooling, so that the temperature in the container is uniform, and it has good thermal efficiency.
The front end of the scraper agitator is equipped with a scraper made of polyvinyl fluoride and cyclobutadiene. Due to the hydraulic pressure, it contacts the inner wall of the container, effectively scraping and transferring materials from the inner wall to accelerate the effect of heat exchange.
The vacuum homogenizing emulsifier is also equipped with a series of auxiliary facilities, including heating and cooling interlayers and insulation layers, as well as various measuring instruments such as thermometers, viscosity agents, tachometers, vacuum gauges, and material flow sensors.
The advantages of vacuum homogenizing emulsifier are:
(2) As the stirring and emulsification are carried out in a vacuum state, the materials will no longer be lost due to evaporation, and the contact between the emulsified body and the air is reduced and avoided, the contamination of the product by bacteria is reduced, and the deterioration of the product will not be caused by oxidation.
(3) Under vacuum conditions, the speed of the stirrer is accelerated, which improves the emulsification efficiency.
Other mixing equipment
1. Three roll mill

The three roll mill is widely used in the wet grinding of raw materials in the fine chemical industry such as paint, ink, ink, coating, plastic, rubber, medicine, food, cosmetics, etc. It has multiple functions such as crushing, dispersing, emulsifying, homogenizing, and toning.
In the cosmetics manufacturing process, the three-roll grinder is a widely used grinding equipment, especially in the production of cold cream, lipstick, liquid foundation, and other products.
The three roll mill is composed of body, discharge plate, cooling system, rolls, baffle plate, electrical switch or electrical control system, hand wheel, transmission system, and other components. Among them, the most critical component is installed in a cast-iron frame. Three rolls with different rotation speeds are made of stainless steel or granite. Both ends of the roll shaft are equipped with large and small gears for speed change.
For different types of products and different requirements for the fineness of the paste, the gap between the front and rear rolls and the middle roll can be adjusted according to the actual requirements of the production quality.
2. Kneader

Generally, the rotation speed of the two blades of the kneader is different, the speed range is 30-60r/min, and the speed ratio range is 1.0-1.9, which can be adjusted appropriately according to actual requirements during operation.
Filling equipment
Liquid filling equipment
1. Atmospheric filling machine
The atmospheric liquid filling machine is a simple type of filling equipment that relies on the weight of the liquid to fill under normal pressure.
This type of filling machine is divided into two types: timing filling and constant volume filling. It is suitable for filling low-viscosity and gas-free liquids such as perfume, lotion, toner, toilet water, etc. The most notable features of this type of filling machine are simple principle, low equipment cost, and simple maintenance; but the quantitative method of atmospheric liquid filling machine is relatively simple, and the filling loss is large. For some high-cost cosmetic products or high viscosity, The emulsion is not applicable.
2.Pressure filling machine
The working process is divided into three stages: filling, sealing, and inflating.
The liquid filling metering cylinder and the liquid filling head are responsible for quantitative liquid filling, cover, and press rolling, and pneumatic components are responsible for the fluid whose boiling point is below room temperature-propellant (nitrogen, trichlorofluoromethane, dichlorodifluoromethane, etc. are mostly used in cosmetics) ) Press into the bottle under high pressure and squeeze the air out of the spray can.
3. Paste and viscous emulsion canning equipment
The filling equipment adopting the mechanical pressure method mainly includes piston type, scraper pump type, and gear pump type. The piston-type is currently a type of filling equipment commonly used in the cosmetics industry.
Copyright Notice :
This article only represents the author’s point of view.
This article is published under the authorization of the author.
Source: Franli
This article address : Grinding equipment needed to make cosmetics
Related Products
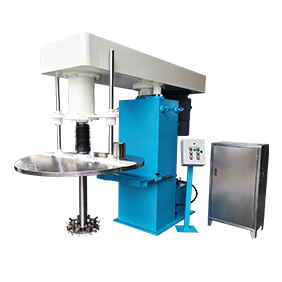
High Speed Disperser
Architectural waterproof coating production equipment The preparation process of the high-speed disperser machine mainly includes the dispersion of pigments and fillers, grinding, coating preparation, toning, etc.
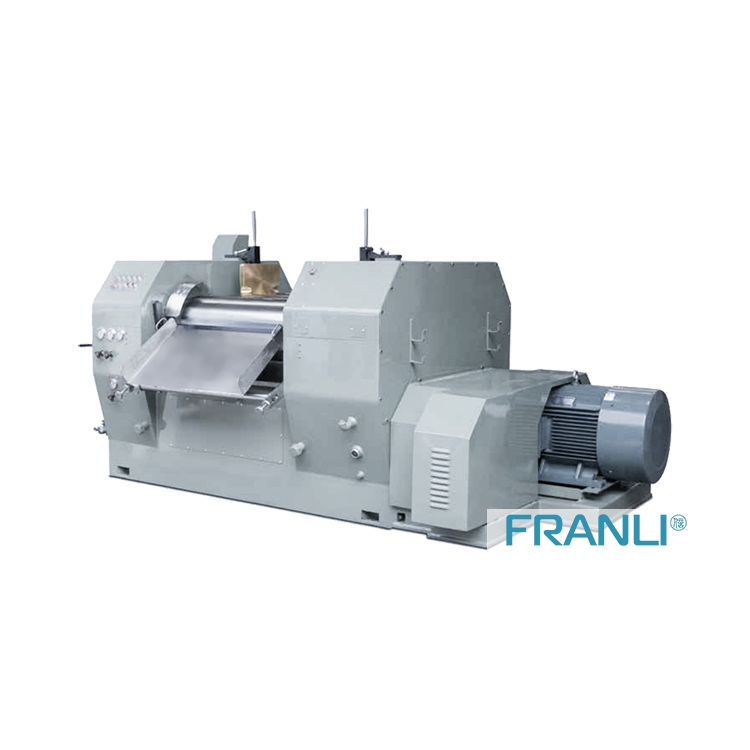
Heating three roll mill
Heating three roll mill is a common type of three-roll mill, mainly used in the grinding of high-viscosity materials.
News
Laboratory Reactor: Guide to Stirring System
The laboratory reactor is composed of a pot body, a pot cover, an agitator, a jacket, a support and transmission device, a shaft seal device, etc.
Grinding Media for Bead Mill | Zirconia Beads & Zirconium Silicate Beads
Bead mills mainly use grinding balls as media, and use impact, extrusion, and friction to achieve the final grinding effect, which mainly depends on the size and hardness of the grinding beads, the filling rate of the grinding beads, and the collision frequency adjustment between the grinding beads and the particles.
Overview of Laboratory Reactor
Laboratory reactors, also known as lab reactors, are essential tools in scientific research, product development, and process optimization. These reactors provide a controlled environment for conducting chemical reactions, mixing, dispersing, and homogenizing processes.
Bead mills | Manufacturing technology in various industries
Bead mills, also known as sand mills or grinding mills, are versatile machines widely used across various industries for the wet grinding and dispersion of solid particles in liquid media.
Ribbon Blender Mixer Equipment
A ribbon blender mixer, also known as a ribbon mixer or horizontal ribbon blender, is a powerful industrial machine designed for thorough and efficient blending of various materials.
What is A Stainless Steel Reactor?
Stainless steel reactors are essential equipment in various industries, including chemical, pharmaceutical, biotechnology, and food processing.