Home » Ink production equipment-three roll mill
Ink production equipment-three roll mill
The three roll mill is one of the most important dispersing equipment for the production of ink or slurry products, and the most effective grinding and dispersing equipment for high-viscosity materials. Mainly used for grinding fluid slurry and paste materials of various paints, inks, pigments, plastics, cosmetics, soap, ceramics, rubber, grains, etc.
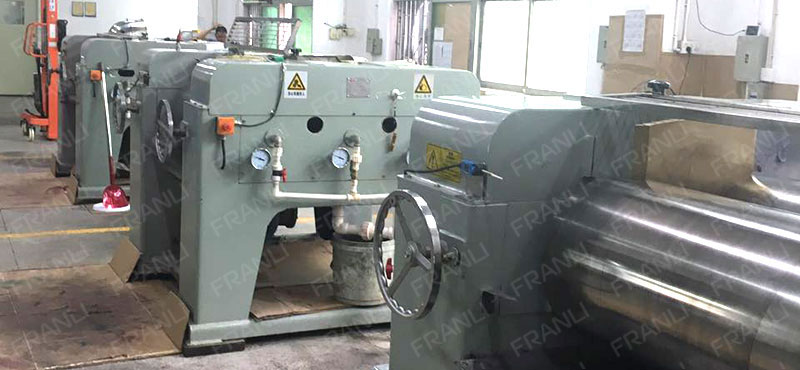
Working principle of three roll mill
The three roll mill is composed of a motor, a transmission device, a drum, a frame, a feeding and discharging device, a regulating device, a cooling system, and other components. There are three rollers installed on an iron frame, which can be installed horizontally or slightly inclined. The dispersion effect is achieved through the mutual squeezing of the surfaces of the three rollers and the friction and shearing effects of different speeds. The steel drum can be hollow and cooled by water. Because the rotation direction of the three drums is different (the speed increases sequentially from the feed roller to the discharge roller), it produces a good grinding effect.
The slurry mainly relies on the pressure and shear force between the rollers to overcome the cohesive force between the powder particles on the three roll mill, so that they are broken into fine particles and fully dispersed in the solvent and resin. When the particle aggregates enter the gap between the rollers, The shearing force in the tangential direction of the contact part of the rollers has the greatest effect. In actual operation, large particles or clumps in the slurry do not initially enter between the rollers and continue to perform a “rod-like” rotating motion until The volume of the slurry on the roller is very small, and the oversized particles enter between the rollers and are crushed or adhered to the surface of the roller (so at the end of each grinding pass, the slurry on the roller needs to be shoveled off with a spatula. And re-enter the grinding to ensure the uniformity of grinding).
The three roll mill is a high-pressure (very small roller pitch) production equipment. Once human limbs and foreign objects (clothing, shovel) are caught in the feeding roller or other gaps, it may cause serious consequences of machine destruction and death. Therefore, the entire operation In the process, pay special attention to the safety of personnel.
How to choose a three roll mill?
(1) The quality of the roller
The quality of a three roll mill depends largely on the quality of the three rollers, and the quality of the rollers depends on the alloy materials and casting methods used. The casting of rollers used cold casting in the past, but centrifugal casting is now used. The new method can obtain a wear-resistant surface layer of 10-18mm thick. The high-quality surface layer can be ground several times, generally every time. 0.3-0.5mm, it can be reground at least 3-4 times, beyond this number of times, the gear of the roller shaft needs to be replaced or corrected.
The hardness of the anti-damage layer on the surface of the roller is controlled by the composition of the metal, and the good hardness is generally in the range of 550-600 Bush hardness.
(2) Roller size
For the mechanical processing of the roller surface, the main problem is the height of the roller (that is, the circumferential length of the middle section of the roller is greater than the circumferential length of the two ends). If there is no middle height, once the pressure is too high during grinding, the pressure will appear in the grinding The distribution on the line is not uniform, so the discharge is uneven.
(3) Feeding method
In the three roll mill operation project, feeding is labor-intensive work. The feeding is to shovel the slurry from the bucket little by little and then put it on the three roll mill. The small three roll mill for the production sample is supplied The material strength is acceptable, but the feeding strength of the mass-produced three roll mill is very high. To solve this problem, at present, large-scale inclined three roll mills abroad need to be equipped with automatic feeding devices. There are three common types: dumping, pumping Type, and squeeze type feeding device.
The influence of parameter setting on grinding effect
(1) Pressure
Adjusting the pressure between the rollers is the most important step in the operation of a three roll mill. When the machine is started, if it is a model with a fixed middle roller, you need to adjust the pressure of the feeding roller and the discharging roller to make the slurry in the grinding process. The medium energy is evenly scraped off by the blade. If the pressure is too large or too small, the discharge will be uneven. You can judge whether the pressure is reasonable according to the discharge state.
When grinding materials, it will generally grind several times according to the fineness requirements of the final product. The setting pressure of the three roll mill is usually increased one by one to ensure that the wetting and dispersing process of the agglomerated particles is a “gradual” process. So it is more stable and controllable.
(2) Temperature
When using a three roll mill, the adjustment of the roller temperature is also very important. This includes two aspects. The first is the friction between the rollers themselves and the friction between the rollers and the slurry, which causes the rollers to increase in temperature, and then The temperature of the slurry increases with the increase of the temperature of the roller so that the decrease in viscosity affects the output. On the other hand: if the slurry temperature is too high, the temperature difference with the ambient temperature is too large, it is easy to cause the condensed water to condense on the surface of the product, which affects the performance of the product.
(3) Blade
The blade must be flat. The uneven blade is not only easy to irregularly wear the surface of the roller, but also may cause excessive local friction, causing the local temperature of the roller to be too high (accelerating the wear and aging process of the roller surface).
The width of the knife-edge is appropriate. The width and narrowness refer to the width and narrowness of the inclined surface of the knife edge. Too wide makes the knife-edge easy to curl. When the slurry is discharged, it is driven by the curling edge to rotate together, so that there are too many bubbles in the slurry (affecting the judgment of the grinding end Or production efficiency); too narrow, the front is not sharp, affecting the output efficiency.
Installation position: The installation position of the blade is generally on the horizontal connection of two adjacent rollers, too high or too low will affect the output. The contact angle between the blade and the roller is also very important. This angle refers to the angle between the blade and the contact point. If it is too small, it is easy to wear, and if it is too large, it is easy to wear the blade. Increase the angle to find a balance between efficiency and cost
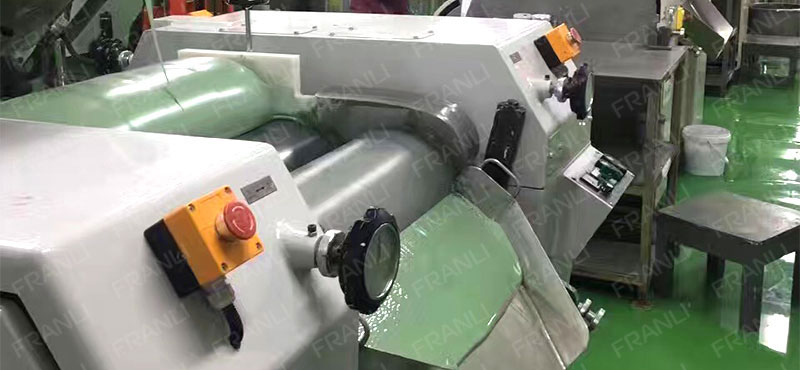
Tips for finding the best device
Copyright Notice :
This article only represents the author’s point of view.
This article is published under the authorization of the author.
Source: Franli
This article address : Ink production equipment-three roll mill
Related Products
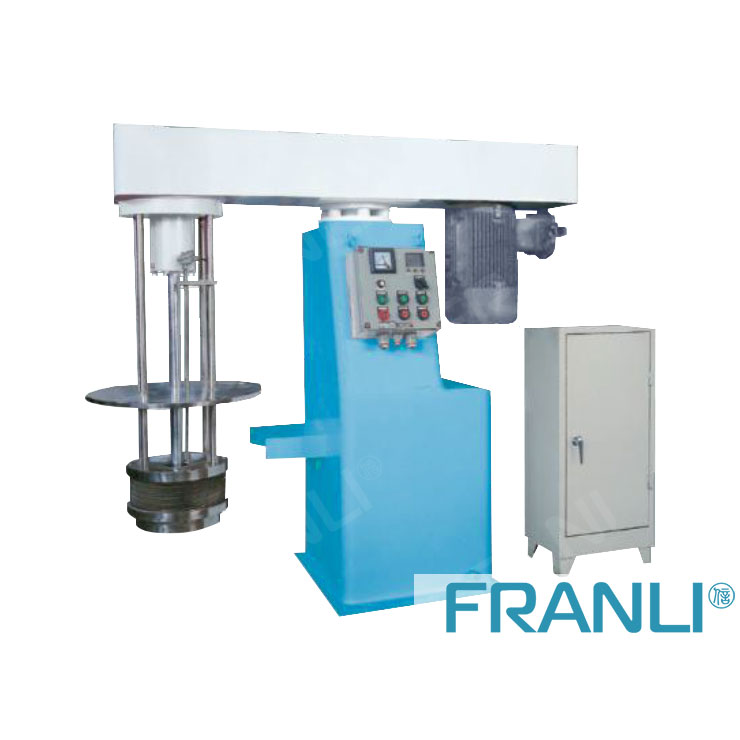
Immersion Mill
FRANLI immersion mill is a new type of discontinuous ultrafine mill integrating grinding and dispersing. After many studies and data, it is shown that this immersion mill is especially suitable for the production and grinding of small batches and multi-variety products.
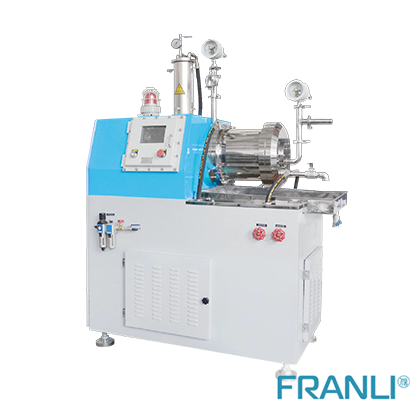
Bead mill for paint
The application fields of liquid coatings are very wide, so a bead mill for grinding high-quality and high-fineness coatings is required.
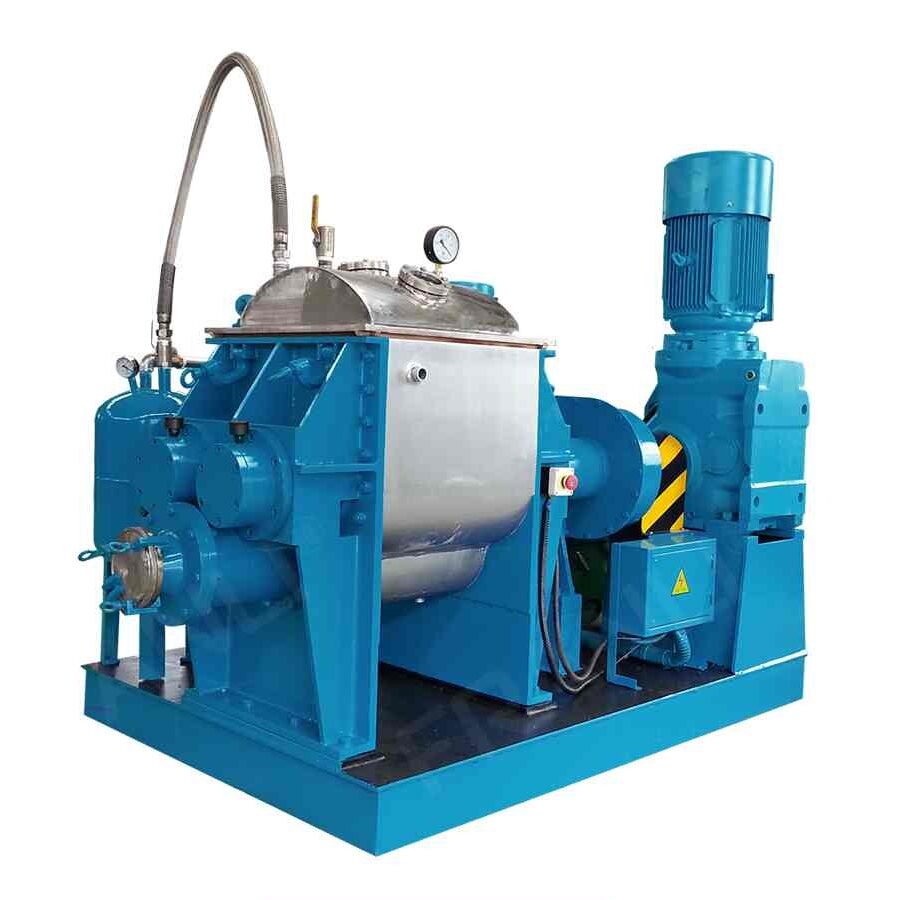
Z Blade Mixer|Shearing and mixing
The FRANLI z blade mixer is a mixer used for evenly mixing semi-solid materials. The mixer contained a U trough bowl with two Z shape blades that rotate in opposite directions for accurate blending of particles.
News
Laboratory Reactor: Guide to Stirring System
The laboratory reactor is composed of a pot body, a pot cover, an agitator, a jacket, a support and transmission device, a shaft seal device, etc.
Grinding Media for Bead Mill | Zirconia Beads & Zirconium Silicate Beads
Bead mills mainly use grinding balls as media, and use impact, extrusion, and friction to achieve the final grinding effect, which mainly depends on the size and hardness of the grinding beads, the filling rate of the grinding beads, and the collision frequency adjustment between the grinding beads and the particles.
Overview of Laboratory Reactor
Laboratory reactors, also known as lab reactors, are essential tools in scientific research, product development, and process optimization. These reactors provide a controlled environment for conducting chemical reactions, mixing, dispersing, and homogenizing processes.
Bead mills | Manufacturing technology in various industries
Bead mills, also known as sand mills or grinding mills, are versatile machines widely used across various industries for the wet grinding and dispersion of solid particles in liquid media.
Ribbon Blender Mixer Equipment
A ribbon blender mixer, also known as a ribbon mixer or horizontal ribbon blender, is a powerful industrial machine designed for thorough and efficient blending of various materials.
What is A Stainless Steel Reactor?
Stainless steel reactors are essential equipment in various industries, including chemical, pharmaceutical, biotechnology, and food processing.