Home » The development history of sand mill
The development history of sand mill
In today’s sand mill market, as the most widely used high-end refined powder grinding equipment, each has its structural design and improvement, especially the design of the dispersing disc, which is even more diverse, but it is the layout of the grinding cylinder. In terms of form, it is mainly divided into horizontal and vertical.
The working principle of a lab three-roll mill
The second stage: vertical disc sand mill (disc + top screen separator);
The third stage: Vertical pin sand mill (rod type + top gap separator);
The fourth stage: horizontal disc sand mill (disc + dynamic rotor centrifugal separator);
The fifth stage: horizontal pin rod circulating sand mill (rod type + super large filter area separator).
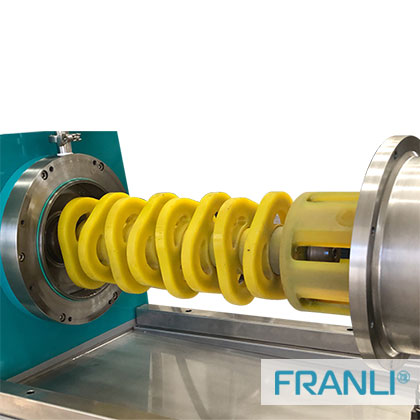
However, due to the structural limitations of the early vertical sand mills, there were some problems, such as the low filling rate and uneven distribution of the grinding media under the influence of gravity. After avoiding these shortcomings, it quickly squeezed the market and gradually became the mainstream of fine grinding equipment.
But this does not mean that the vertical sanding machine will be replaced. There is still room for optimization and it has its unique advantages. Compared with the traditional horizontal sand mill, the vertical sand mill with this structure design can effectively solve the leakage of shaft seal damage, the blockage of the bead grading network, the inability to grind with ultra-fine beads, the uneven product particles, and the low production efficiency. The five major problems of high consumption.
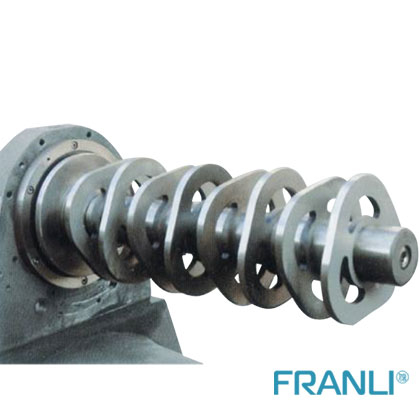
How to solve the shortcomings of traditional vertical and horizontal sand mills through structural optimization and improvement?
2. The grinding process makes full use of the principles of centrifugal classification and fluid mechanics. The grinding chamber is divided into two grinding zones inside and outside by the stirring rotor, inner stator, and classification turbine. The raw material particles will undergo centrifugal classification inside for classification and grinding, and the materials and beads are also separated by centrifugation.
3. The grading cycle grinding enhances the grinding effect. The material first enters the outer grinding zone and moves along the outer grinding void between the rotor and the cylinder along with the beads. After reaching the bottom, it moves along the inner grinding zone between the rotor and the inner stator to near the axis and then moves there. The role of two classifications. Finally, the small particles are discharged to the outer circulation cylinder in time, and the large particles are discharged to the outer grinding area to continue to participate in the next grinding cycle, which not only prevents the over-grinding of the small particles, but also increases the grinding times of the large particles, and the final product size The distribution span is small.
This method of centrifugal force classification solves the problem of screen clogging, and the classification grinding also effectively utilizes vertical gravity to allow the raw material particles to circulate up and down inside, lengthening the grinding channel and also allowing the particles to be more uniformly dispersed. Better grinding effect. In the whole grinding process, the equipment energy is mainly used for the effective grinding of large particles, which maximizes the useful work of the equipment, realize high-efficiency and energy-saving grinding, and improves the grinding efficiency of the equipment.
Copyright Notice :
This article only represents the author’s point of view.
This article is published under the authorization of the author.
Source: Franli
This article address : The development history of sand mill
Related Products
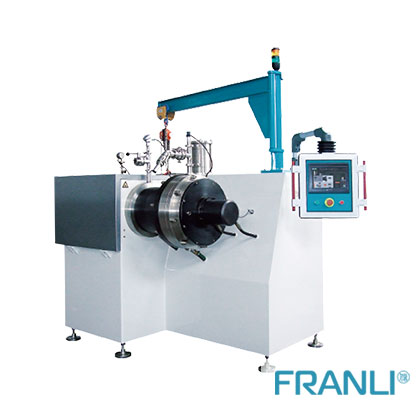
Dyno mills
Dyno mills are also widely used in inks. In the production of different types of ink, the structure of the dyno mill is also different. Probably follow the following rules, gravure ink: production generally uses pin or disc type dyno mill; rotary offset p
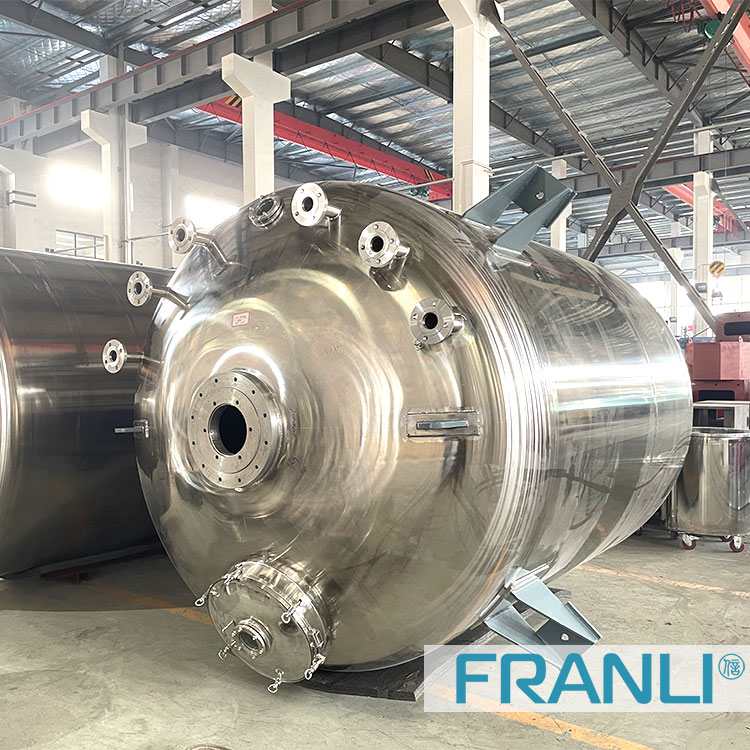
Stainless Steel Reactor
The reaction vessel is a comprehensive reaction vessel. The structure, function, and configuration accessories of the reaction vessel are designed according to the reaction conditions.
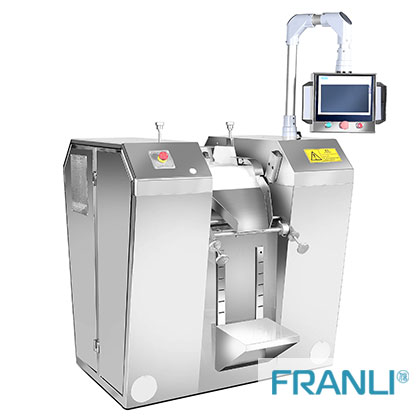
Hydraulic Three Roll Mill
FRANLI Hydraulic three roll mill has a unique Hydraulic system, which controls pressure roller, discharging blade, two sides holders, etc, which system can improve production capacity compared with normal same size three roll mill.
News
Laboratory Reactor: Guide to Stirring System
The laboratory reactor is composed of a pot body, a pot cover, an agitator, a jacket, a support and transmission device, a shaft seal device, etc.
Grinding Media for Bead Mill | Zirconia Beads & Zirconium Silicate Beads
Bead mills mainly use grinding balls as media, and use impact, extrusion, and friction to achieve the final grinding effect, which mainly depends on the size and hardness of the grinding beads, the filling rate of the grinding beads, and the collision frequency adjustment between the grinding beads and the particles.
Overview of Laboratory Reactor
Laboratory reactors, also known as lab reactors, are essential tools in scientific research, product development, and process optimization. These reactors provide a controlled environment for conducting chemical reactions, mixing, dispersing, and homogenizing processes.
Bead mills | Manufacturing technology in various industries
Bead mills, also known as sand mills or grinding mills, are versatile machines widely used across various industries for the wet grinding and dispersion of solid particles in liquid media.
Ribbon Blender Mixer Equipment
A ribbon blender mixer, also known as a ribbon mixer or horizontal ribbon blender, is a powerful industrial machine designed for thorough and efficient blending of various materials.
What is A Stainless Steel Reactor?
Stainless steel reactors are essential equipment in various industries, including chemical, pharmaceutical, biotechnology, and food processing.