Kneader
The kneader is widely used in silicone rubber, ink, dumping, dyes, rubber, plastics, medicine, cellulose, carbon, starch, chewing gum, bubble gum, chocolate biscuit ceramics, synthetic resins, pulp, magnetic recording materials, emulsion explosives, Adhesives, building waterproof coatings, cosmetics, polymers, and various coloring materials industries.
Advantages of Dispersion Kneader:
- low grinding fineness
- Wide range of applications
- high working efficiency
Application

Coating

Cosmetic

Battery

Graphite

Agrochemistry

Adhesives
Hot sale Kneader
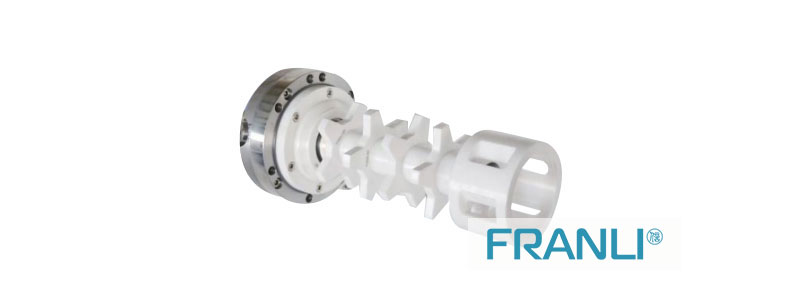
• Easy installation of the bead mill machine: The best features of this bead mill machine are: You can easily install it wherever you want. This task is so simple, and effortless. And due to this feature, it is extremely popular among other equipment. You can find the bead mill working principle so effective, and you can perform all the mixing tasks effectively without adding so much effort. As this machine is very bulky and cheap, it needs only a few minutes to install. In this way, you can reduce the labor charges and other exhausting jobs. So, you can stay worry-free about how to install this machine? As the company has made this task easier for you.
• Efficient work performance of this bead mill machine: As we know, the bead mill working principle has been created in such a way that you can achieve higher and efficient work performance on this bead mill machine. If you are looking for quality and stable work, these bead mill machines are the best option to get a consistent mixture of any particular material. You can use this bead mill for paint, ink, and coating industries. And, it is a comfortable and easy method to perform all the mixing and dispersing activities without wasting so much time. So, here bead mill working process is so necessary to obtain the desired results for the company.
• Contains grinding media of 2-3 mm size: It is the necessary feature of the bead mill working process as it includes the grinding media. In this area, grinding and other dispersing activities take place that they turn into a fine mixture. You can use a bead mill for paint, ink, and coating industries, where mixing works have been done regularly. It contains grinding media of 2-3 mm size that is enough to transform all the material to a smooth and fine paste. For this purpose, bead mill manufacturers have added advanced technology to this machine to provide consistent and quality work performances for the company. In this way, you can get a higher productivity ratio. And you can reach the peak of the higher conversion rate. Thus, these bead mill machines are ideal for fabrication companies to get their desired goals with full efficacy.
• Easy operation of the bead mill machine: It is a great feature of this SMP Agitator bead mill machine as bead mill manufacturers create this bead mill machine with advanced technology. And, with this quality, the operation of this sand grinding mill is extremely comfortable. You do not need to call any professional to do the same, and you can do it yourself without adding so much effort. So, it is another best feature to consider about this bead mill machine.
• Easy to clean the bead mill machine: This sand grinding mill is remarkably best for the fabrication companies to enhance the overall growth and production. As we know, while we use any bead mill machine, we need to clean it so that we can get hygienic work performance. For this purpose, companies manufacture this bead mill machine in a way that you can clean it comfortably without making yourself exhausted. You can go through the bead mill pdf and other relative documents that provide you the guidelines of clean this bead mill machine.
• Easy to maintain the bead mill machine: Maintaining is also a matter of concern as it requires your time and money. For this purpose, you can check the bead mill pdf and manual provided by the company at the time of purchase. You can either contact the company or read the manual carefully to know all the information about the bead mill machine. And, you can find this process is extremely simple to perform. So, you can get this bead mill machine without spending so many amounts on it. And, in this way you can concentrate on the work performance of the company.
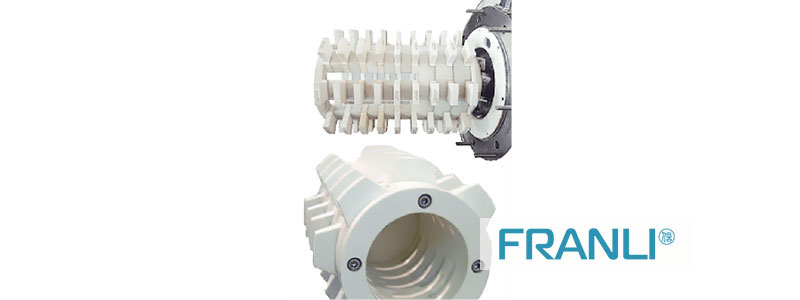
Also, you can use SMP Agitator bead mill in paint industry, ink, and other coating work companies to make all the mixing and grinding activities easier and more manageable. To get this bead mill machine, you search for those companies that deal in these machines and other equipment. For this purpose, you can get a quote or related other information about the bead mill machine.
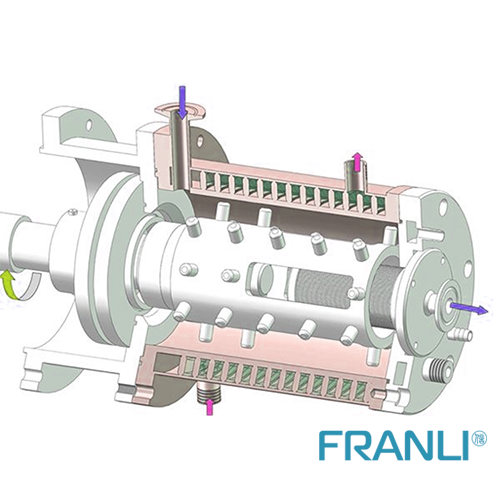
Hydraulic TRH type
Hydraulic Three Roll Mill, which is a full hydraulic auto-controlling system equipment. 1- Cooling system: an individual cooling system for each roller. 2- hydraulic control: hydraulic control pressure blades, roller gaps, etc. 3- Optional installation:PLC system with SIEMENS touching screen, FRANLI engineer set formulas of grinding according to different viscosity materials.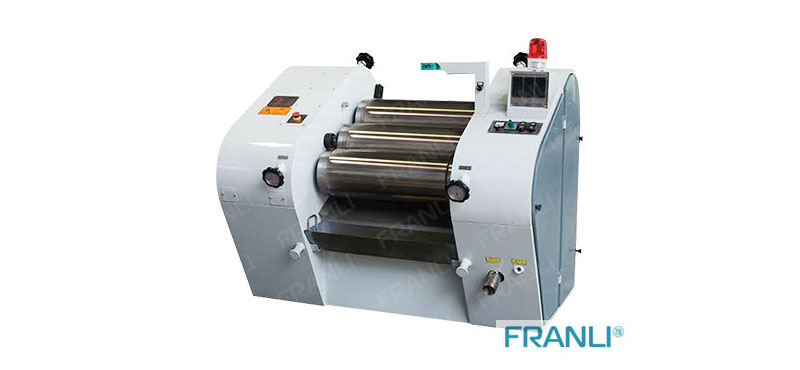
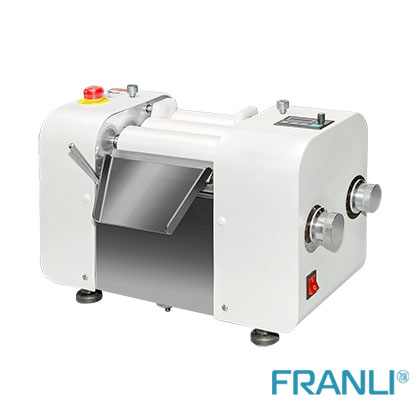
Vertical type for Grinding Powder
Also, we have a vertical three-roll mill for grinding powder and chocolate. We have 3 rollers, 4 rollers, and even 5 rollers, which are all vertical types. We export to the soap industry and chocolate companies.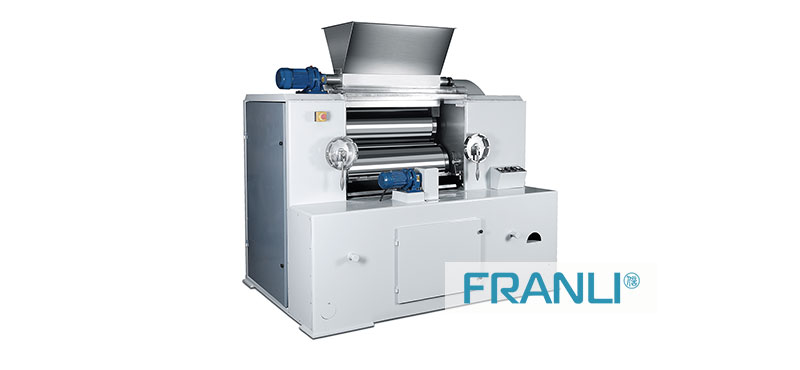
Heating type
Franli also offers a heating hydraulic three roll mill for rubber, EVA, PVS, and color masterbatch. As this type of machine grinds high viscosity material, we specially design the gear quality. This type is been Heated by oil or steam. Franli three roll mill machine are full automatic PLC controlling, hydraulic system, stable operation, reliable quality. We choose the international brand parts. Standrad parts, ABB VFD, Siemens Motor, SKF or NSK bearings, SEW or Nord reducer. A roller is 45-55mm thickness of metal, cast steel. You can widely choose ceramic, alloy, granite rollers for your material. If you have several formulas of material, we can set up formulas in the PLC system, your workers only need to choose numbers on touching the screen, don’t need to waste time to adjust the rollers’ gap or the pressure of the blade.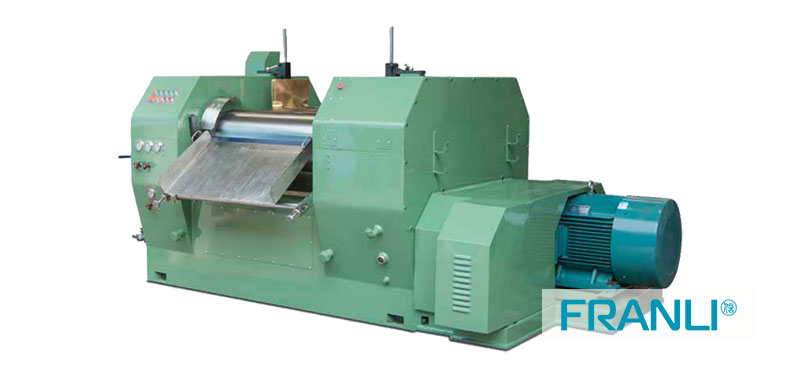
Related production lines
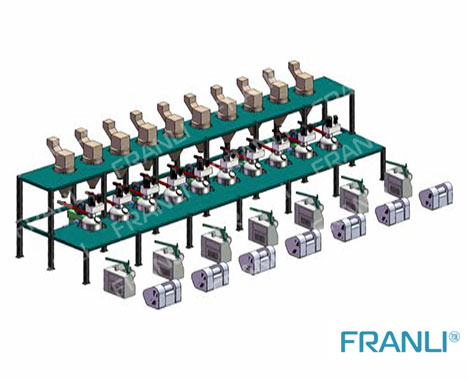
Offset Ink machine line
FRANLI is specialized in offset ink full line production for 20+ years. Helped customer save the cost, save the man power, also save the space.
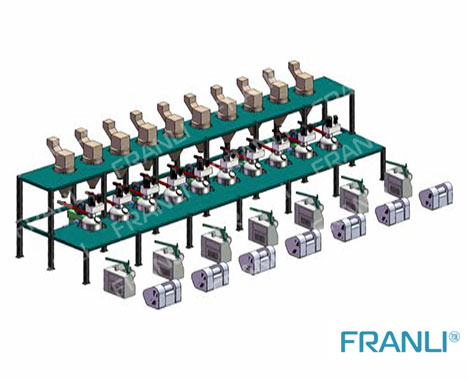
Offset Ink machine line
FRANLI is specialized in offset ink full line production for 20+ years. Helped customer save the cost, save the man power, also save the space.
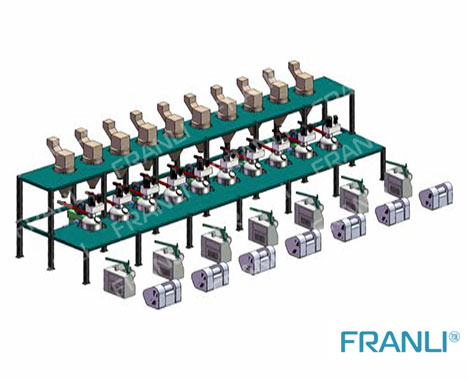
Offset Ink machine line
FRANLI is specialized in offset ink full line production for 20+ years. Helped customer save the cost, save the man power, also save the space.
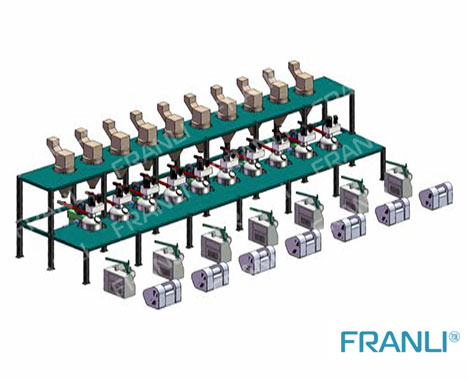
Offset Ink machine line
FRANLI is specialized in offset ink full line production for 20+ years. Helped customer save the cost, save the man power, also save the space.
Technical Parameter
Guidelines For Dispersion Kneader
The Kneaders are widely used in the rubber and dispersion kneader products trade, for example, in the manufacture of tires, cables, rubber tapes and tubes, rubber sports shoes, semi-finished sealing twin-screw kneader and calcium plastics. It is also linked to the mixing and in-plant production of paints, stains, ceramics, pharmaceuticals, tapes, and films.
To actively respond to the market’s requirements for low carbonization, Franli has specially developed the kneader with characteristics such as desulfurization and denitration catalysts. According to different purposes, the kneader can be made into vacuum, pressure, atmospheric, Normal temperature, high temperature, low temperature, etc.
The temperature adjustment method of a kneader can be the jacket, halfpipe, far-infrared tile, steam, hot water, heat transfer oil, electric heating, cooling water, chilled water, and other methods. Various security, measurement, control, recording, and other instruments can be installed on the kneader. To improve product quality and customer experience, advanced technologies such as hollow mixing paddle heating, paperless recording, PLC full-process automatic program control, and centralized computer control have been designed.
This unit is the best new mixing tool in the rubber and plastics industry. All its performance figures are at or near excellent levels for the same products in different countries. The unit is of low-cost design, compact structure and small area, easy to install and produce, simple and reliable in operation, easy to clean the mixer, easy to change the dye frequently, good cooling and heating, uniform in mixing and laboratory kneader, and the fully enclosed design not only protects but also has a good sealing effect and long service life.
Working principle and design features
The machine comprises a motor, cover press, main body, mixing chamber and rotor mechanism, gearbox, air control system, tilting machine, heating/cooling system, rubber belt transmission and base, etc.
The essential difference between the Kneader and the conventional mixer is the absence of a sliding block and the rotor tilting at the mixing chamber’s inlet by 140° to its axis during discharge. An electric motor weaves the mixing chamber through a cycloidal gearbox, worm wheel, and worm gear. An eyelash press is attached to the unit. During the unit’s operation, the top plunger of the eyelash press is driven by a cylinder that exerts pressure on the rubber material.
The mixing chamber, the rotor, and the Hiram are equipped with a cooling (or heating) device. According to the principle, the amount of water used in each half can be regulated by employing a valve. The connecting pipes for cooling water, inlet and outlet, and steam inlet and outlet must be interchanged.
The rotor drive system kneader mixer rubber. The rotor is driven from the primary motor by a rubber belt. The reduction and transmission gears drive the inlet and tail rotors in reverse drive rotation.
The rotor surface is sealed by a Teflon-filled O-ring and an alloy ring, the design of which is a kneader machine for rubber mixing. No grease is used in this sealant.
Lubrication system
The machine’s lubrication system consists of three elements:
- Lubrication of the gearbox
- Lubrication of the worm wheel of the tilting machine
- Lubrication of the worm
- The individual tool
For lubrication of the stepper gearbox, worm wheel, and worm gear, splash lubrication is used from a tank located at the installation site of the kneader mixer manufacturer. Q/Sy8051-79120 EP industrial gear oil or 18 homogeneous gear oil, step gear using 90kg; 250 artificial worm gear oil, worm wheel field of oblique machine using 15kg; lubrication of the opposite work to determine the position of the five levels of lubrication Check the lubrication and lubricants table 1 to be filled.
Electrical operating system
For more information about the machine’s electrical and pneumatic operating system, please refer to the “X(S)N-75 x 30 kneader mixer Electrical Components Manual”.
Setting, adjustment, and control of the operation
Depending on the suitability of the technical flow for the particular workshop, the machine can be placed on the same floor for the following operations. The machine should be anchored on a stable and level foundation. Mews according to the foundation drawing kneader machine specification. Install lifting software and rigging equipment with a maximum load capacity of 10 tons.
The environment in which the equipment is located has an essential effect on its efficiency. Two conditions must therefore be met to use the kit: firstly, the ambient temperature around the equipment must be maintained between 0°C and 40°C around the rubber kneader, and secondly, the equipment must be placed in an area with good air circulation. There should also be enough space in front of the equipment for inspection and maintenance when installing the equipment.
Before installation, the various parts of the equipment should be thoroughly cleaned to remove any rust. The mixing cabinet rotor and gearbox, bucket, and housing should be assembled. If they are visible during installation, they should not be disassembled and reassembled. Make a table for the bottom and base of the motor in the mu program. With a table tolerance of less than 0.05 mm/m, mount the engine and the cutter in the housing.
Connect the air control tubes to the corresponding cooling water or heating steam tubes to ensure that the connections do not leak. The rotor, kneader application cabinet, left and right panels, top flap, and all other surfaces that come in contact with the paste are chrome plated. Therefore, care should be taken during installation and maintenance not to damage the chrome layer with heavy objects.
Please do not disassemble parts of gearboxes or inclined augers unless specifically required. Check that the lubricating oil has not expired in all areas, drain it if any, clean the inside and fill it with new oil.
Finally, check that the assembly bolts are in place and that all connections are correct. Turn the main motor rotor and check that all parts are working correctly. After checking that there is no binding or knocking, re-do the gland bolts to grow, harden the parts, and make adjustments.
By placing the appropriate amount of mixer kneader oil in the misting device, turning on the air source, and pressing the right button, it is possible to check for smooth and reliable high splash and dab motion as the correct direction of motor rotation. After checking that all parts of the water (steam) and compressed air lines are connected and that each lubrication layer is lubricated correctly, you can proceed with the inspection.
1) If each lubrication layer is correct:
2) when starting the Hiram vertical movement and the mixing chamber inclined movement, let the machine run idle for two hours to adjust the versatility and reliability of each moving part before starting it under load.
The load test is divided into three parts:
3) 40% of the effective material power is applied first,
4) 70% of the effective material power is used
5) a whole load test is performed, and rubber kneader machine price is fixed. The load test ensures that the gears work stably, without jerking or abnormal noise. Each shift section is versatile and reliable.
After the work is stopped, the gears’ meshing is checked, and if everything is normal, the machine is ready for production and use. The most reputable firm that possesses various sorts of machines with top notch quality and proper functioning is undoubtedly Franli.
Related production lines
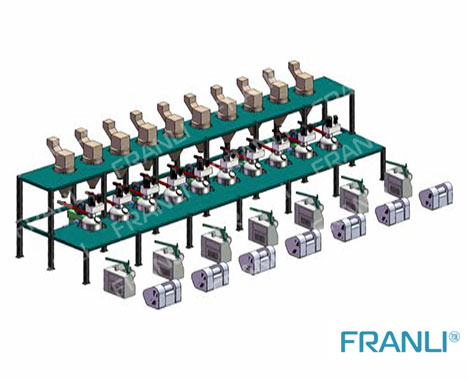
Offset Ink machine line
FRANLI is specialized in offset ink full line production for 20+ years. Helped customer save the cost, save the man power, also save the space.
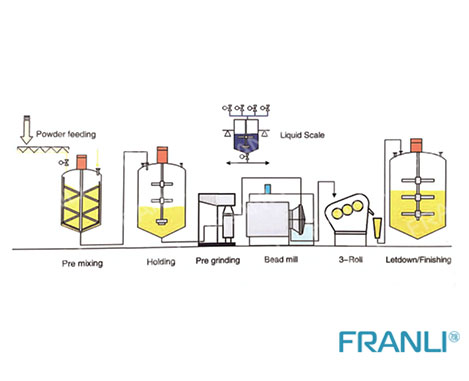
Offset Ink, UV Ink machine line
The FRANLI engineering company, offer the full set of UV INK Production Line, we can make the full drawing according with your factory size, formulas, weather and safety system.
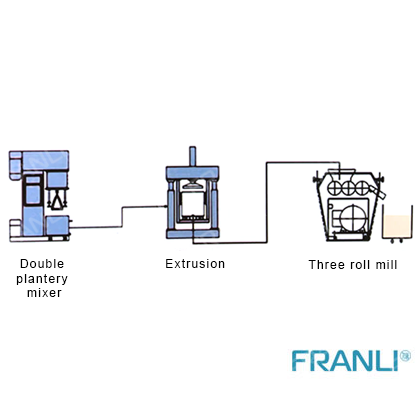
PCB INK Machine line
FRANLI supplies all equipments for the production of PCB inks, from the powder feeding station to the filling part.
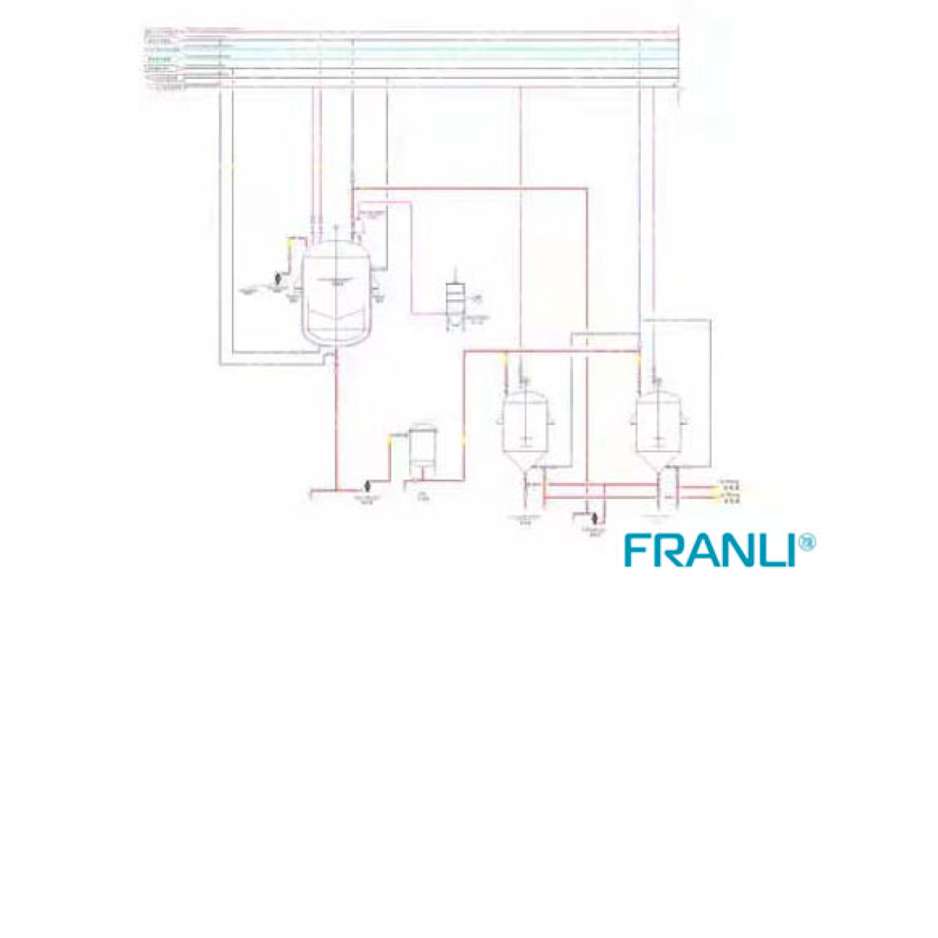
EW-pesticide line
The EW production line mainly mixes raw materials, solvents, and emulsifiers through a reactor (oil-based).
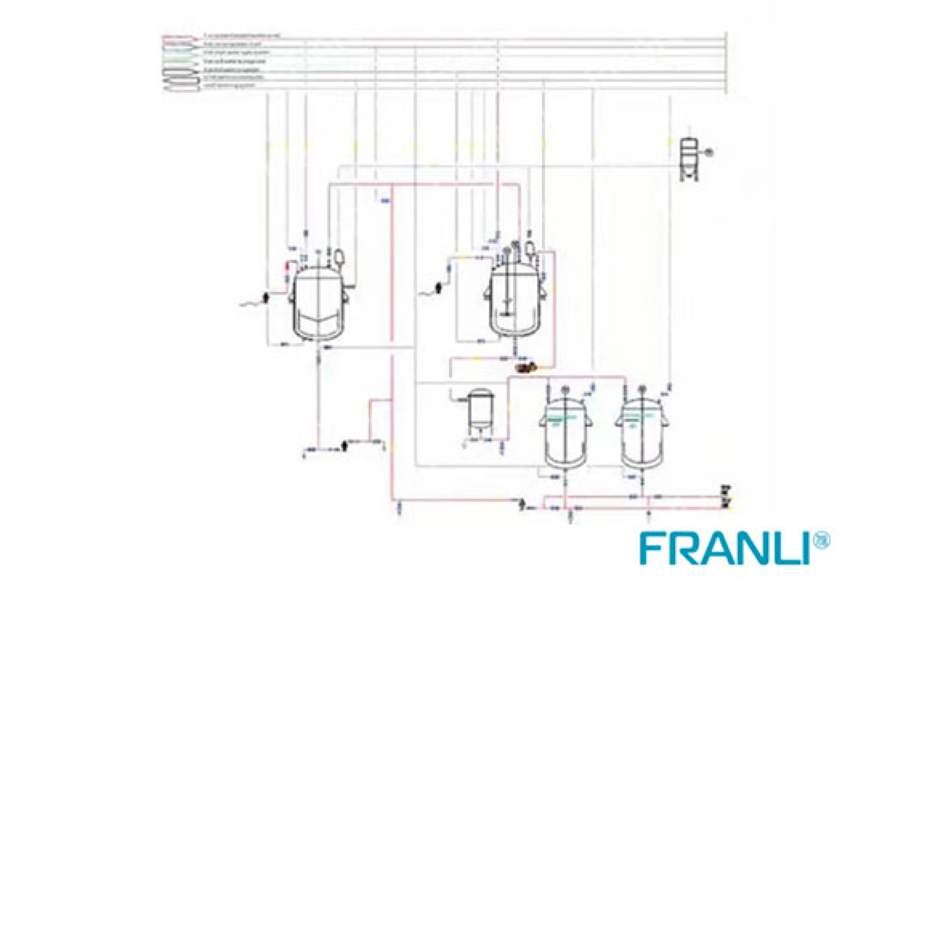
SL_EC pesticide line
The EC production line is mainly composed of an agitator mixer, bag filter, filling machine, etc.
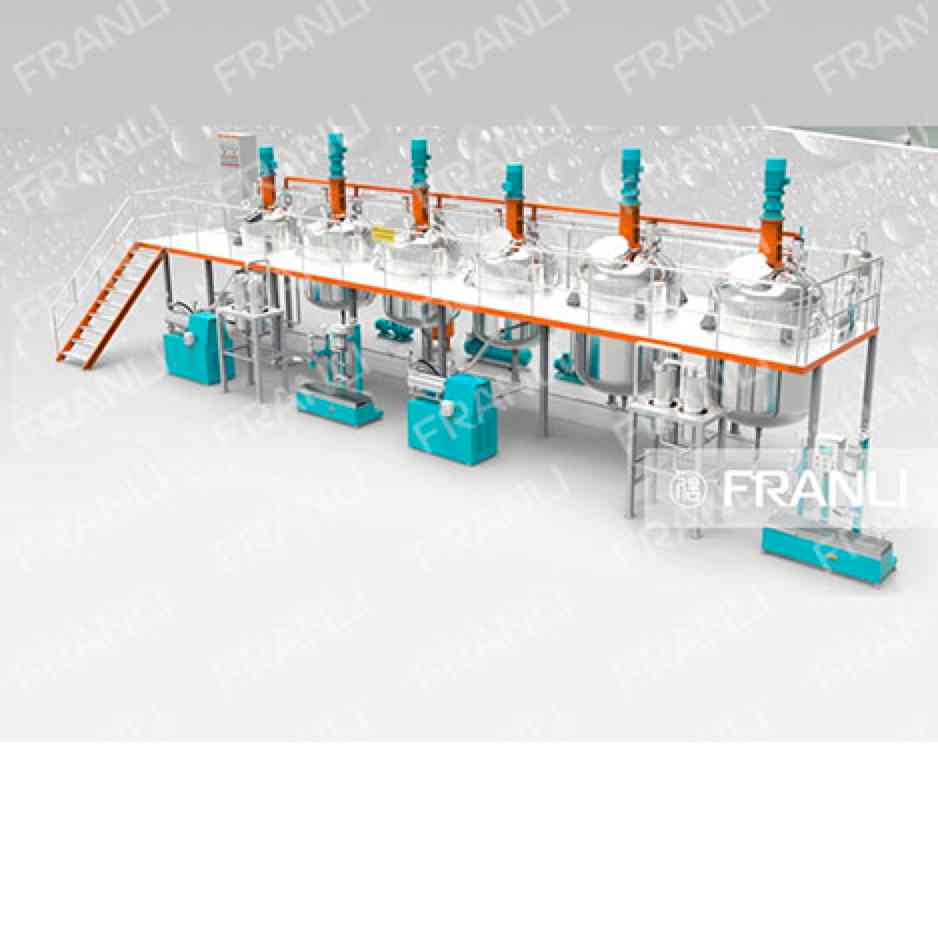
Automotive Paint machine line
The automotive paint machine line is mainly for the production and grinding of automotive paint, Automotive paint has many layers, such as Primer/electrophoretic layer, Medium coat, Colored coat, and Clearcoat.
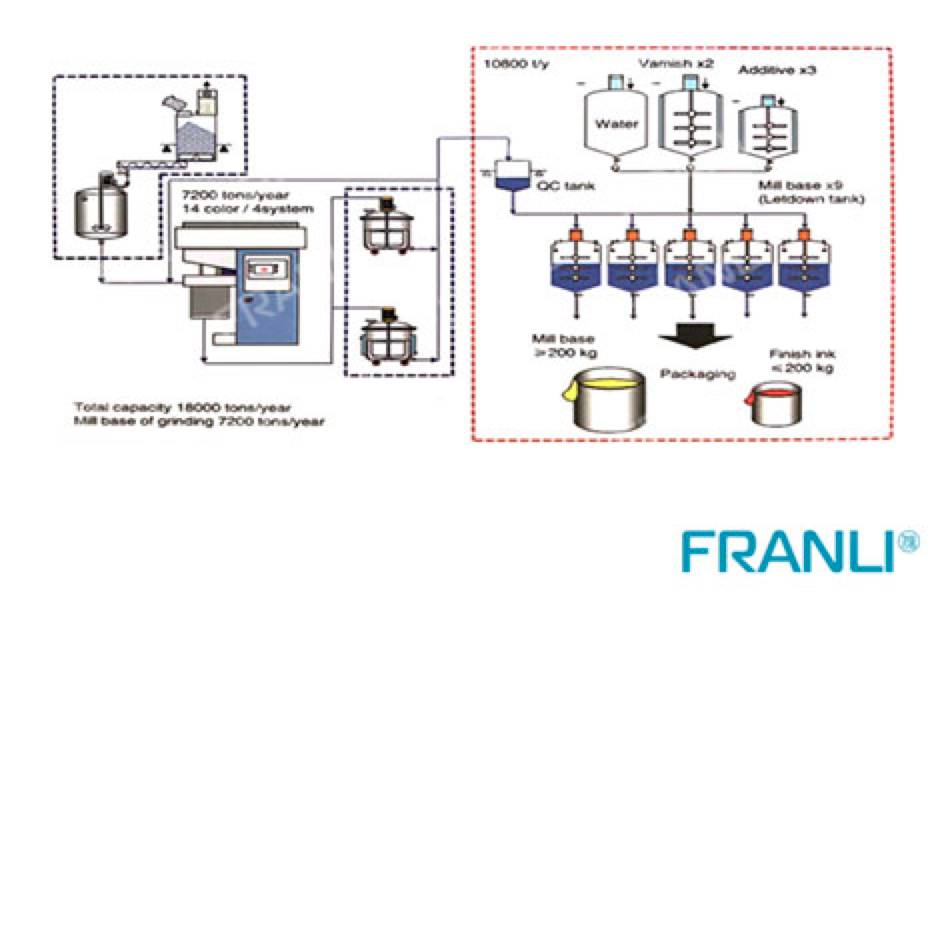
Digital Ink machine line
Franli has professional experience for digital ink machine line, we offered hundreds customers to expand production, or build up new project.