Vertical sand mill
Vertical sand mills are mainly used in batteries, digital consumables, ceramic materials, mineral pigments, rare earth materials, cosmetics, pharmaceutical preparations, and other industries. For the grinding of materials, vertical sand mills have a very strong role, not only high efficiency, advanced, Because its own grinding cavity is relatively narrow and the gap between the levers is small, with the cooling system and control system of the sand mill, the production efficiency of the entire production line can be improved many times.
Advantages of Vertical sand mills:
- low grinding fineness
- Wide range of applications
- high working efficiency
Application

Coating

Cosmetic

Battery

Graphite

Agrochemistry

Adhesives
Frequently Asked Questions
In today’s sand mill market, as the most widely used high-end refined powder grinding equipment, each has its structural design and improvement, especially the design of the dispersing disc, which is even more diverse, but it is the layout of the grinding cylinder. In terms of form, it is mainly divided into horizontal and vertical.
The development of sand mills has probably gone through the following stages:
The first stage: vertical stirring mill (bottom screen separator + rod type grinding original);
The second stage: vertical disc sand mill (disc + top screen separator);
The third stage: Vertical pin sand mill (rod type + top gap separator);
The fourth stage: horizontal disc sand mill (disc + dynamic rotor centrifugal separator);
The fifth stage: horizontal pin rod circulating sand mill (rod type + super large filter area separator).
The invention of the vertical sand mill improves the shortcomings of the vertical agitating mill such as low rotation speed, large media size, low grinding efficiency, and wide product particle size distribution so that the grinding equipment market has completely entered the era of sand mills.
However, due to the structural limitations of the early vertical sand mills, there were some problems, such as the low filling rate and uneven distribution of the grinding media under the influence of gravity. After avoiding these shortcomings, it quickly squeezed the market and gradually became the mainstream of fine grinding equipment.
But this does not mean that the vertical sanding machine will be replaced. There is still room for optimization and it has its unique advantages. Compared with the traditional horizontal sand mill, the vertical sand mill with this structure design can effectively solve the leakage of shaft seal damage, the blockage of the bead grading network, the inability to grind with ultra-fine beads, the uneven product particles, and the low production efficiency. The five major problems of high consumption.
How to solve the shortcomings of traditional vertical and horizontal sand mills through structural optimization and improvement?
- Feeding and discharging materials are different from traditional horizontal machines. The feed is conveyed to the grinding cavity by driving the screw thread, and the material is extracted from the grinding cavity by the suction of the pump when the material is discharged. No additional mechanical seal is required, and the leakage and pollution problems caused by the damage of the shaft seal are prevented from the root cause.
- The grinding process makes full use of the principles of centrifugal classification and fluid mechanics. The grinding chamber is divided into two grinding zones inside and outside by the stirring rotor, inner stator, and classification turbine. The raw material particles will undergo centrifugal classification inside for classification and grinding, and the materials and beads are also separated by centrifugation.
- The grading cycle grinding enhances the grinding effect. The material first enters the outer grinding zone and moves along the outer grinding void between the rotor and the cylinder along with the beads. After reaching the bottom, it moves along the inner grinding zone between the rotor and the inner stator to near the axis and then moves there. The role of two classifications. Finally, the small particles are discharged to the outer circulation cylinder in time, and the large particles are discharged to the outer grinding area to continue to participate in the next grinding cycle, which not only prevents the over-grinding of the small particles, but also increases the grinding times of the large particles, and the final product size The distribution span is small.
This method of centrifugal force classification solves the problem of screen clogging, and the classification grinding also effectively utilizes vertical gravity to allow the raw material particles to circulate up and down inside, lengthening the grinding channel and also allowing the particles to be more uniformly dispersed. Better grinding effect. In the whole grinding process, the equipment energy is mainly used for the effective grinding of large particles, which maximizes the useful work of the equipment, realize high-efficiency and energy-saving grinding, and improves the grinding efficiency of the equipment.
Hot sale sand mill(Bead mill)
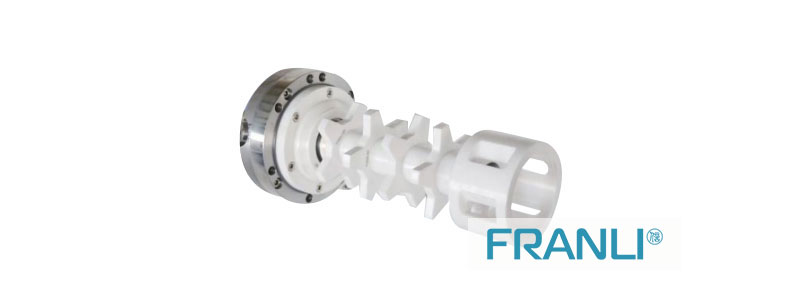
• Easy installation of the bead mill machine: The best features of this bead mill machine are: You can easily install it wherever you want. This task is so simple, and effortless. And due to this feature, it is extremely popular among other equipment. You can find the bead mill working principle so effective, and you can perform all the mixing tasks effectively without adding so much effort. As this machine is very bulky and cheap, it needs only a few minutes to install. In this way, you can reduce the labor charges and other exhausting jobs. So, you can stay worry-free about how to install this machine? As the company has made this task easier for you.
• Efficient work performance of this bead mill machine: As we know, the bead mill working principle has been created in such a way that you can achieve higher and efficient work performance on this bead mill machine. If you are looking for quality and stable work, these bead mill machines are the best option to get a consistent mixture of any particular material. You can use this bead mill for paint, ink, and coating industries. And, it is a comfortable and easy method to perform all the mixing and dispersing activities without wasting so much time. So, here bead mill working process is so necessary to obtain the desired results for the company.
• Contains grinding media of 2-3 mm size: It is the necessary feature of the bead mill working process as it includes the grinding media. In this area, grinding and other dispersing activities take place that they turn into a fine mixture. You can use a bead mill for paint, ink, and coating industries, where mixing works have been done regularly. It contains grinding media of 2-3 mm size that is enough to transform all the material to a smooth and fine paste. For this purpose, bead mill manufacturers have added advanced technology to this machine to provide consistent and quality work performances for the company. In this way, you can get a higher productivity ratio. And you can reach the peak of the higher conversion rate. Thus, these bead mill machines are ideal for fabrication companies to get their desired goals with full efficacy.
• Easy operation of the bead mill machine: It is a great feature of this SMP Agitator bead mill machine as bead mill manufacturers create this bead mill machine with advanced technology. And, with this quality, the operation of this sand grinding mill is extremely comfortable. You do not need to call any professional to do the same, and you can do it yourself without adding so much effort. So, it is another best feature to consider about this bead mill machine.
• Easy to clean the bead mill machine: This sand grinding mill is remarkably best for the fabrication companies to enhance the overall growth and production. As we know, while we use any bead mill machine, we need to clean it so that we can get hygienic work performance. For this purpose, companies manufacture this bead mill machine in a way that you can clean it comfortably without making yourself exhausted. You can go through the bead mill pdf and other relative documents that provide you the guidelines of clean this bead mill machine.
• Easy to maintain the bead mill machine: Maintaining is also a matter of concern as it requires your time and money. For this purpose, you can check the bead mill pdf and manual provided by the company at the time of purchase. You can either contact the company or read the manual carefully to know all the information about the bead mill machine. And, you can find this process is extremely simple to perform. So, you can get this bead mill machine without spending so many amounts on it. And, in this way you can concentrate on the work performance of the company.
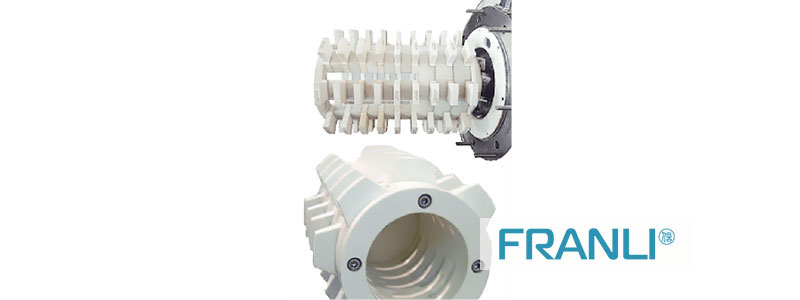
Also, you can use SMP Agitator bead mill in paint industry, ink, and other coating work companies to make all the mixing and grinding activities easier and more manageable. To get this bead mill machine, you search for those companies that deal in these machines and other equipment. For this purpose, you can get a quote or related other information about the bead mill machine.
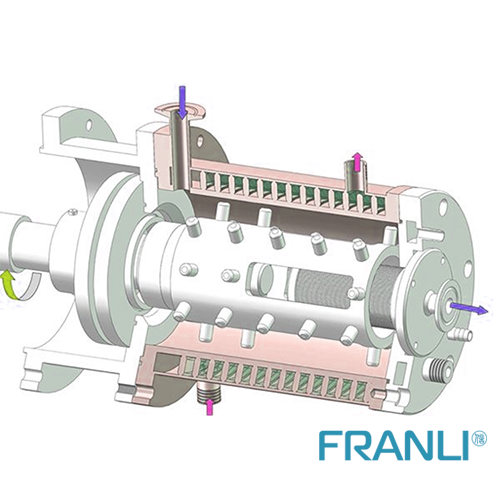
Hydraulic TRH type
Hydraulic Three Roll Mill, which is a full hydraulic auto-controlling system equipment. 1- Cooling system: an individual cooling system for each roller. 2- hydraulic control: hydraulic control pressure blades, roller gaps, etc. 3- Optional installation:PLC system with SIEMENS touching screen, FRANLI engineer set formulas of grinding according to different viscosity materials.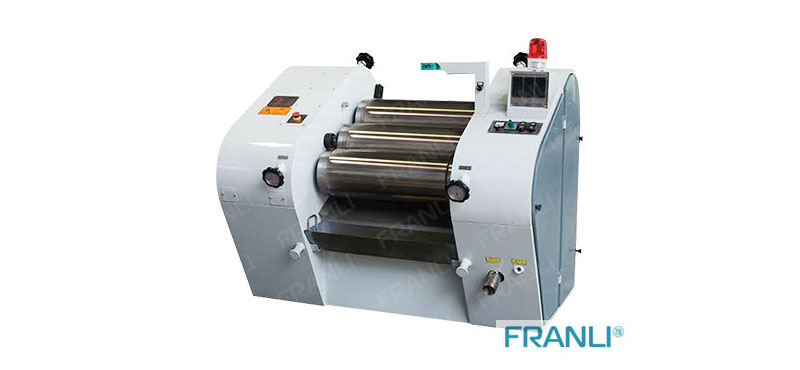
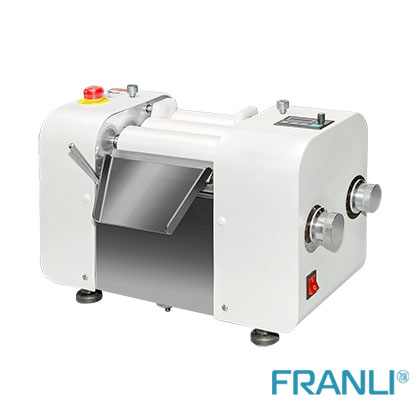
Vertical type for Grinding Powder
Also, we have a vertical three-roll mill for grinding powder and chocolate. We have 3 rollers, 4 rollers, and even 5 rollers, which are all vertical types. We export to the soap industry and chocolate companies.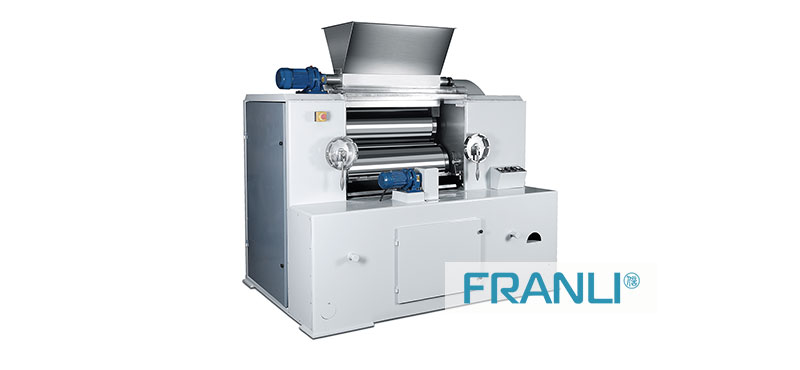
Heating type
Franli also offers a heating hydraulic three roll mill for rubber, EVA, PVS, and color masterbatch. As this type of machine grinds high viscosity material, we specially design the gear quality. This type is been Heated by oil or steam. Franli three roll mill machine are full automatic PLC controlling, hydraulic system, stable operation, reliable quality. We choose the international brand parts. Standrad parts, ABB VFD, Siemens Motor, SKF or NSK bearings, SEW or Nord reducer. A roller is 45-55mm thickness of metal, cast steel. You can widely choose ceramic, alloy, granite rollers for your material. If you have several formulas of material, we can set up formulas in the PLC system, your workers only need to choose numbers on touching the screen, don’t need to waste time to adjust the rollers’ gap or the pressure of the blade.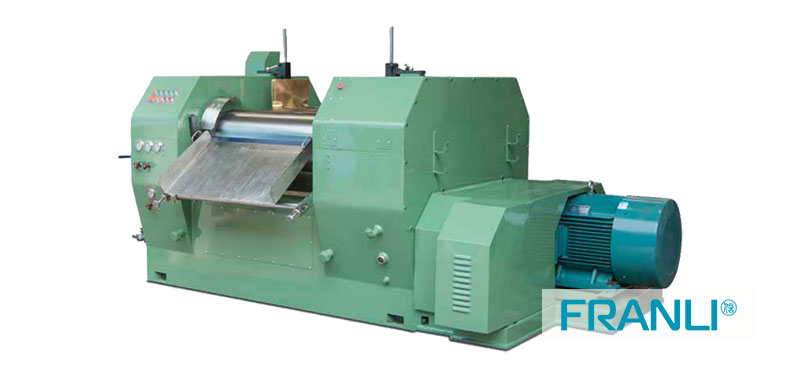
Related production lines
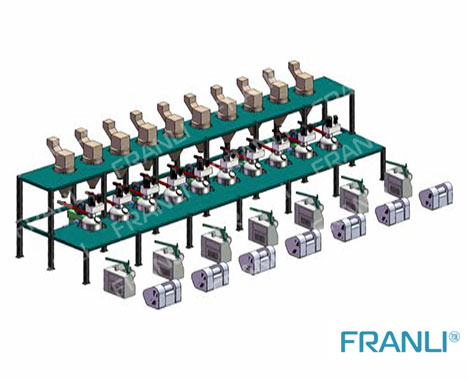
Offset Ink machine line
FRANLI is specialized in offset ink full line production for 20+ years. Helped customer save the cost, save the man power, also save the space.
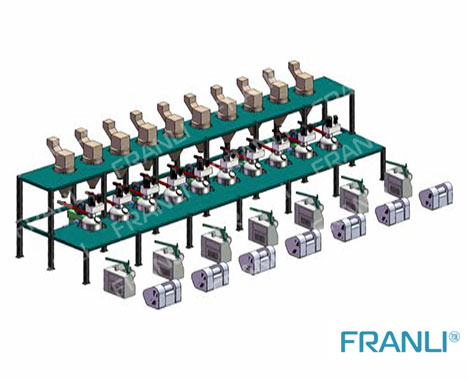
Offset Ink machine line
FRANLI is specialized in offset ink full line production for 20+ years. Helped customer save the cost, save the man power, also save the space.
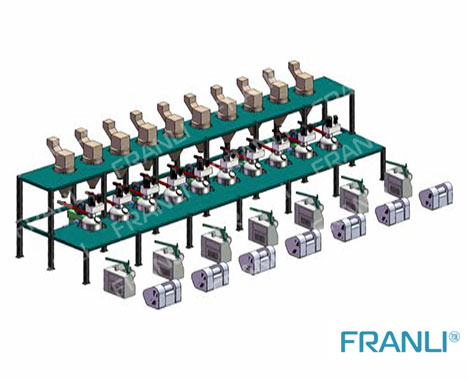
Offset Ink machine line
FRANLI is specialized in offset ink full line production for 20+ years. Helped customer save the cost, save the man power, also save the space.
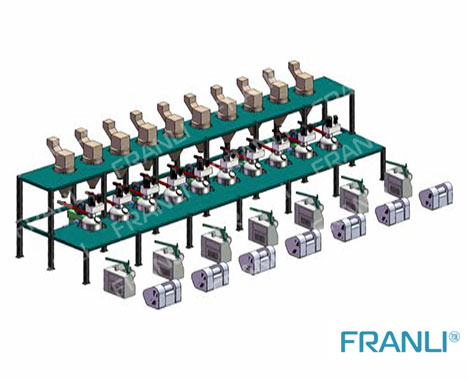
Offset Ink machine line
FRANLI is specialized in offset ink full line production for 20+ years. Helped customer save the cost, save the man power, also save the space.
Guidelines For Sand Mill
The sand mill machine adopts the eccentric disc grinding structure and is arranged in a certain order. This system overcomes the shortcomings of the uneven distribution of the grinding media of the traditional grinding machine so that the grinding media can get the maximum energy transfer and the grinding efficiency is high.
The energy of grinding is very intensive, continuous processing can also be achieved, and the material can also be continuously ground and discharged. The components of the sand mill are very simple, mainly composed of the body, the grinding cylinder, the sand grinding disc (lever), the grinding medium, the motor, and the feeding pump. The production efficiency of the sand mill can be self-adjusted, not only by feeding The speed of the pump is controlled, and the fineness of the material can be controlled by different grinding media. Generally speaking, there are many kinds of grinding media for sand mills, the most common ones are zirconia beads, glass beads, zirconium silicate beads, etc.
There are many advantages of vertical sand mills. The sand mill adopts vertical or rod-pin type. The design of the whole machine adopts a closed cavity design. Compared with the traditional horizontal sand mill in the past, this design method reduces Several shortcomings of the old-fashioned sand mill, such as uneven distribution of grinding media and poor particle size distribution after grinding, which are perfectly overcome. When grinding materials, the grinding discs must be installed on the stirring shaft in a certain order, so as to cause damage to the machine or insufficient grinding fineness.
Vertical sand mill with excellent cooling performance
- The material is pre-cooled in the eddy current guiding gap;
- In the outer grinding chamber, also has a very effective cooling function for the stator and rotor.
- The material can be effectively cooled when the material is turned back at the bottom of the stator.
- When the material flows through the inner grinding chamber, the stator and rotor are effectively cooled.
- When the material on the inner surface of the rotor is in constant eddy current motion, it can bring strong cooling to the inner grinding chamber.
The advantages of a vertical sand mill for application fields
Why are vertical sand mills recognized from various fields? This mainly depends on its own advantages, such as paint, varnish, agrochemical, ink, chemical, paper, and other fields, but also has certain advantages.
- Can make car paint, high solids, and water-based products more lustrous;
- It can make heavy coatings have higher resistance;
- High photosensitive pigments can be achieved at the nanoscale;
- Can produce higher quality dyeing slurry;
- It can make high-quality packaging and silver foil ink more glossy and transparent;
- It can make the special inkjet products more high-quality.
According to different material types, it is also necessary to choose different types of sand mills. For example, there are many kinds of inks, and to produce different kinds of inks, it is generally necessary to choose a suitable model.
Related production lines
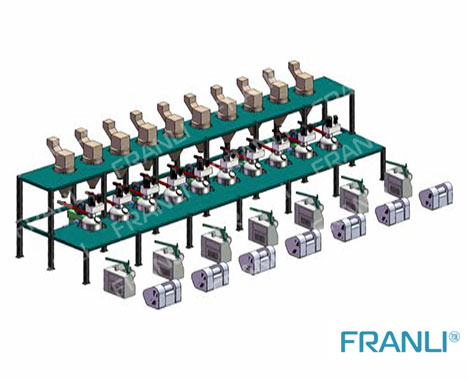
Offset Ink machine line
FRANLI is specialized in offset ink full line production for 20+ years. Helped customer save the cost, save the man power, also save the space.
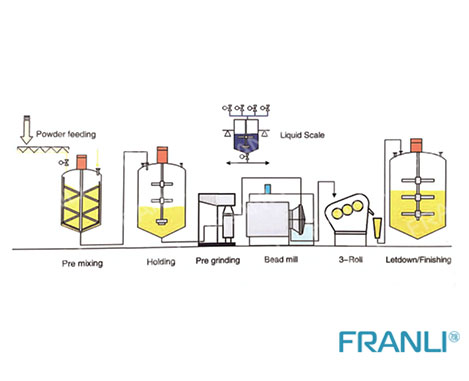
Offset Ink, UV Ink machine line
The FRANLI engineering company, offer the full set of UV INK Production Line, we can make the full drawing according with your factory size, formulas, weather and safety system.
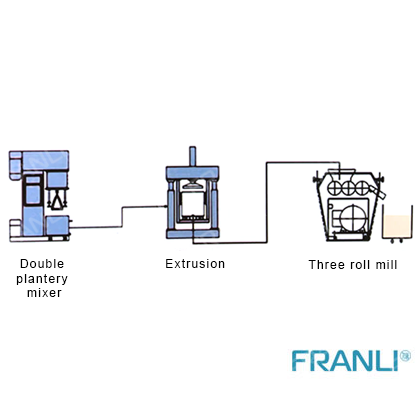
PCB INK Machine line
FRANLI supplies all equipments for the production of PCB inks, from the powder feeding station to the filling part.
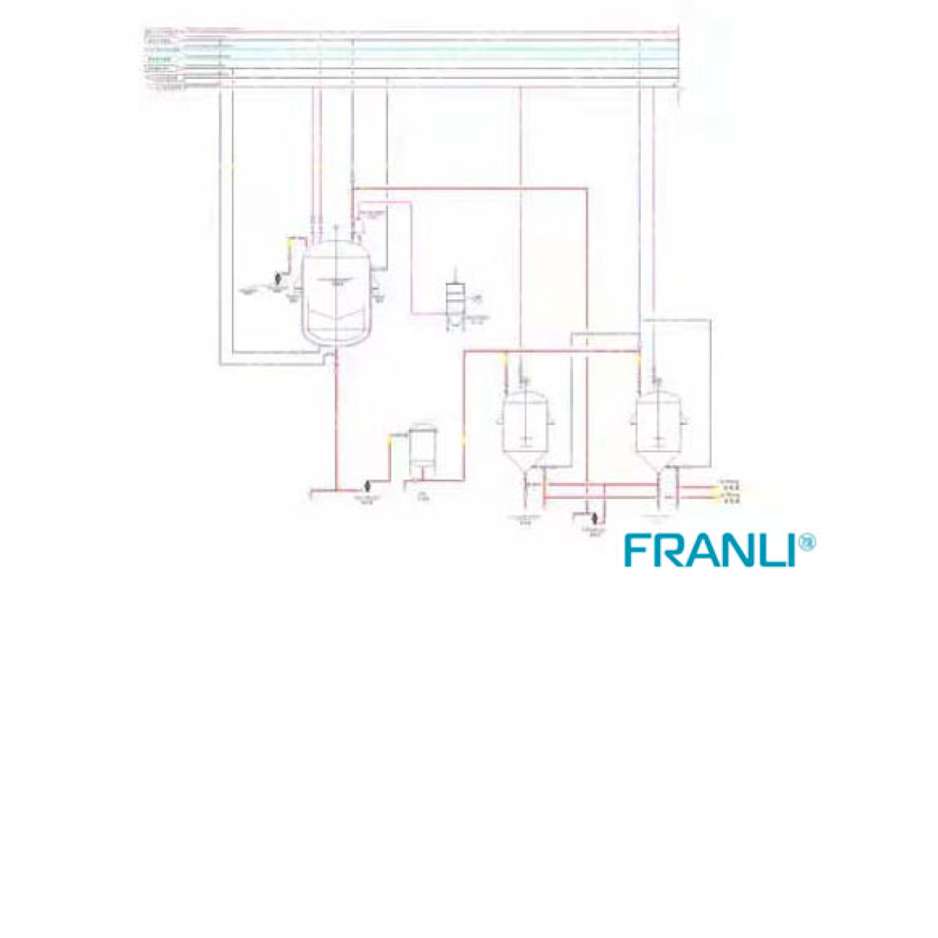
EW-pesticide line
The EW production line mainly mixes raw materials, solvents, and emulsifiers through a reactor (oil-based).
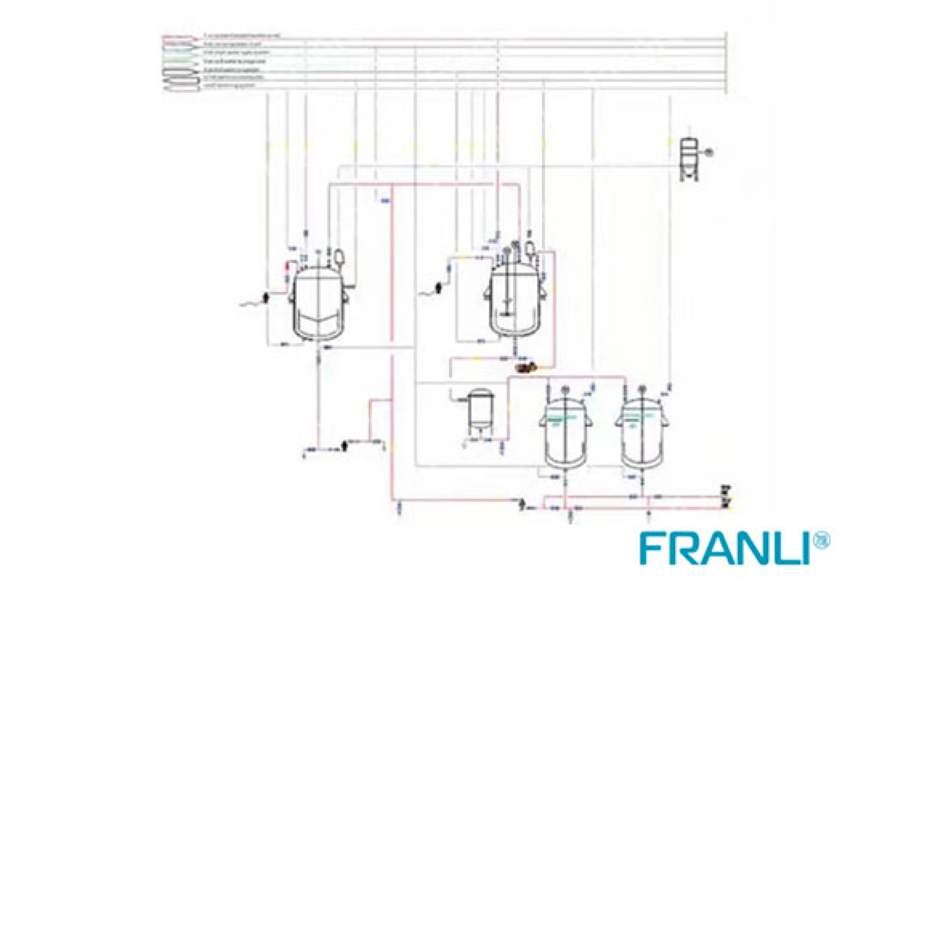
SL_EC pesticide line
The EC production line is mainly composed of an agitator mixer, bag filter, filling machine, etc.
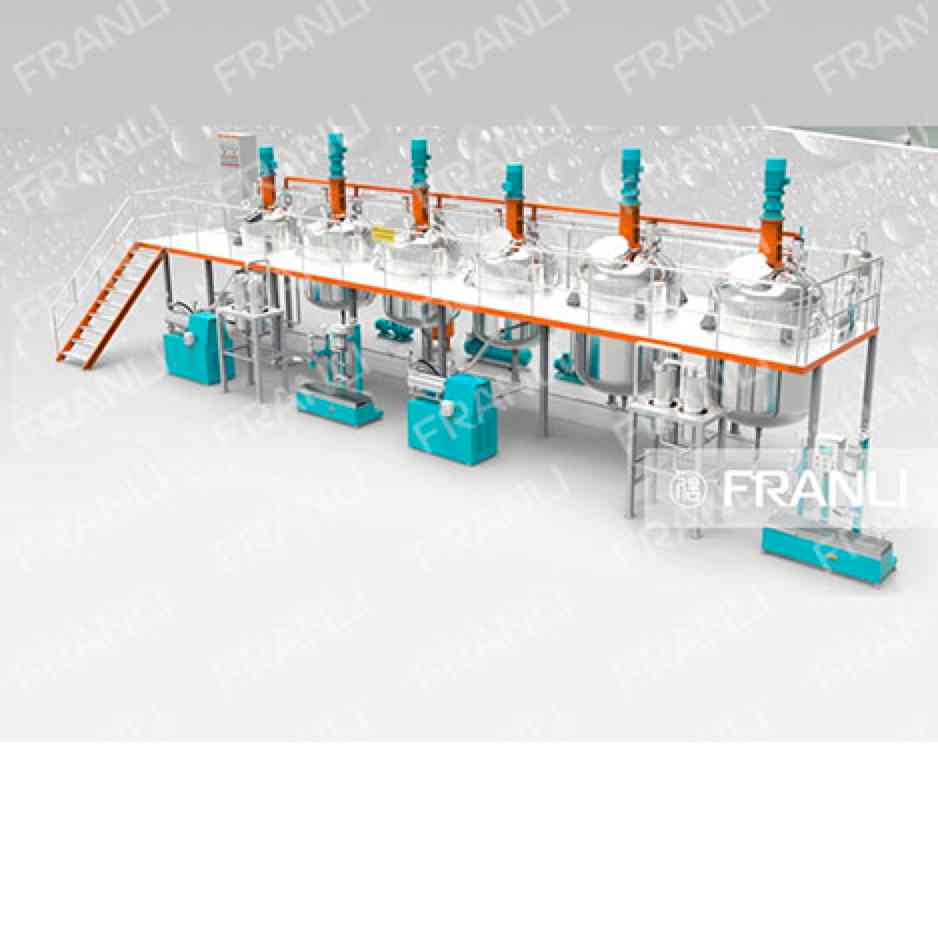
Automotive Paint machine line
The automotive paint machine line is mainly for the production and grinding of automotive paint, Automotive paint has many layers, such as Primer/electrophoretic layer, Medium coat, Colored coat, and Clearcoat.
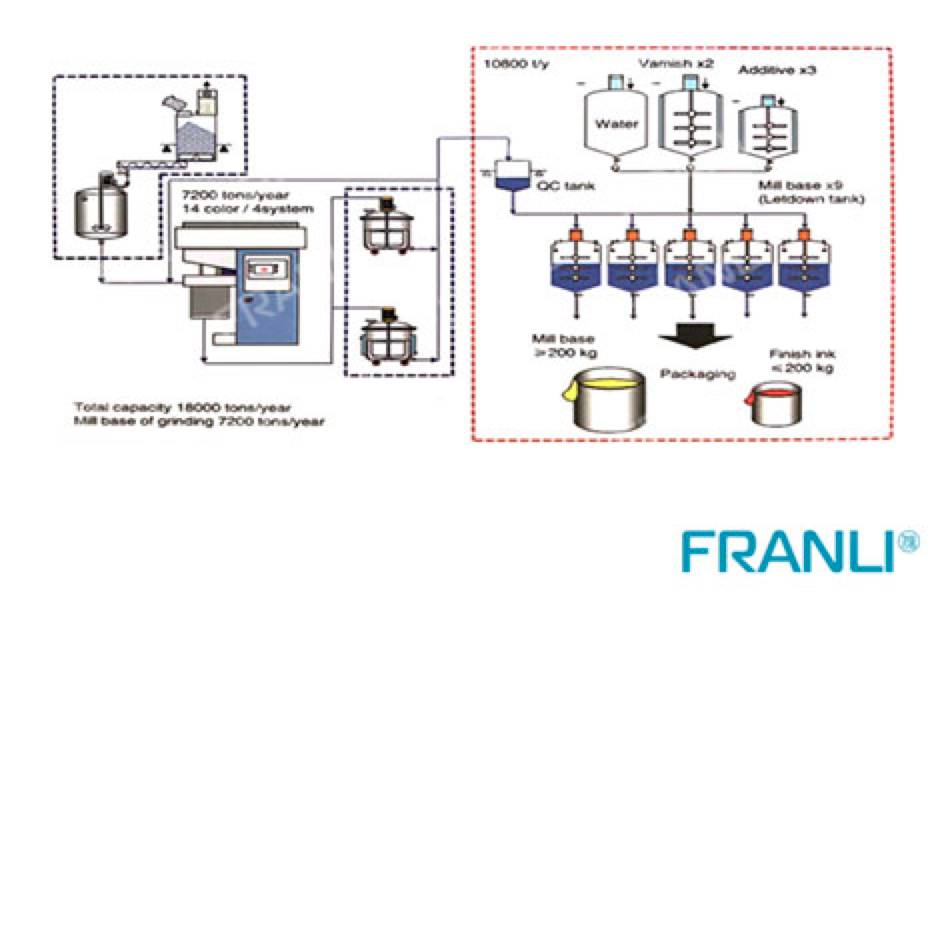
Digital Ink machine line
Franli has professional experience for digital ink machine line, we offered hundreds customers to expand production, or build up new project.