Pearl Mill
Franli manufacturer produces pearl mills for both high viscosity and low viscosity. pearl Mill is also called vertical bead mill, high viscosity pearl mill used in offset ink, printing ink, screen printing ink, condensed ink, gravure ink, letterpress ink, carbon black, and other high viscosity material. While low viscosity of pearl mill used in automotive paint, topcoat, clear coat, printing ink, and digital ink, etc.
Advantages of pearl mill:
- low grinding fineness
- Wide range of applications
- high working efficiency
Application

Coating

Cosmetic

Battery

Graphite

Agrochemistry

Adhesives
Frequently Asked Questions
The main aspect to make sure of the efficiency along with profitability is minimizing the material waste brought over by the milling with the use of pearl mill. If the process of milling is not optimized here, milling with a pearl mill can generate an excess of the metal swarf, including the debris and the chips. So, how can one minimize the waste brought about by the pearl mill?
The following would be a few of the methods that can be implemented by the manufacturers in order to minimize the waste brought about by milling:
1: Recycling the Metal Swarf
Collecting and recycling the metal chips or the debris that are produced through the milling process is considered as one of the initial ways in which waste generation can be minimized. It is basically done with the help of a third party in several of the manufacturing centers.
However, there are a few companies that have already started with the use of specialized equipment that can help recycle and reuse the metal wastes internally. With the processing of the metal waste, it is sent to the other companies with the effective maximization of their potential revenues is the benefit that tags along.
The manufacturers can effectively bypass the expense of transferring their chips to the other company by internalizing the recycling process. It is, however, this method that is not effective for every manufacturer, mainly the ones who deal with several various metal alloys, as they could be well-worth studying for a few of those naturally.
2: Increasing Consistency of the Process
When there are the parts that can be constantly reworked for meeting with a set of tolerance over the production is one of the ways in which the metal shavings are produced significantly in excess. It might also have to be thrown out with the new part milled within its place if the part that is milled is significantly more. This can effectively delay production and can also produce twice as much more waste.
The production of the waste can also be reduced dramatically along with preventing the delays of the production that are caused by the excessive parts of remanufacturing here with the increased consistency over the processes here.
The use of factory automation is one of the ways in which they can make sure of the consistency of the process in terms of the milling operations. Great consistencies can be maintained from part to part in terms of minimizing the need for the reworks to almost nothing that is a lengthy parameter that is programmed within the machines here.
The waste from the metals is therefore reduced significantly.
3: Minimizing Physical Prototypes Reliance
The part that can help you witness whether they are able to endure the difficulties of whatever the process flows is used for is an older standby here for several of the manufacturers. It needs a lot of work in terms of milling, as well as the tool in terms of producing the waste would be in creating a physical prototype.
The design needs to be worked on with the production line having been retooled with several new parts and the tools that need to be machined all over again here if the first prototype fails here. It can therefore be producing a lot of metal scraps here.
The manufacturers would save a lot of time, resources, and energy, preventing the production of the waste that can be pretty incidental to the prototype of the manufacturing process, eliminating every physical prototype that is present.
In terms of identifying the potential risks and correcting them without the proper need of having to commit for a single inch of wire to get the manufacturing process done is made possible through this.
The manufactures can greatly reduce their metal waste in terms of production of the milling processes. Here are simply a few of the potential ways here.
In terms of creating the products out of the raw or the half-formed materials with some of the commonest of them included within the turning and the milling process here is ensured through the manufacturing companies who are making use of several of the machining processes here. The mill would be used here in terms of removing the materials from the workpieces and thereby altering the size as well as the shape of the workpiece here with the milling and turning process. So, how are they different here?
What Is Turning?
Through turning the lathe basically helps in removing the material through the rotating workpiece, including a cutting tool through the turning process. The workpiece here moves as the cutting tool stays stationary here through this process.
The other process included here is boring, involving the use of lathe here. The stationary cutting tool here presses against the rotating workpiece through the process of turning and boring. The turning here is designed for the removal of the material from the exterior region of the workpiece, while the boring is designed specifically for the removal of the material from the interior part of the workpiece here. Boring is used for enlarging the pre-drilled holes within the workpiece with the removal of the materials from the inner walls of the holes, for instance, here.
What Is Milling?
The milling process that includes the mills for the removal of the material from the workpiece that is stationary along with the rotating cutting tool here is done in this process. The principle here works according to that of the turning with the help of the cutting tools that can press against the workpiece, thereby removing the material from within it. The rotation process is what differentiates between these two. The cutting tool rotates in this milling operation here.
In Conclusion
Franli is a highly famed company that offers the manufacturing and processing of the mills like the pearl mill. They also use various methods in terms of determining the kind of equipment and the tool they need to manufacture. They each offer here some distinct advantages when they are being used in this manufacturing industry through the use of different mechanisms.
Hot sale Bead mill
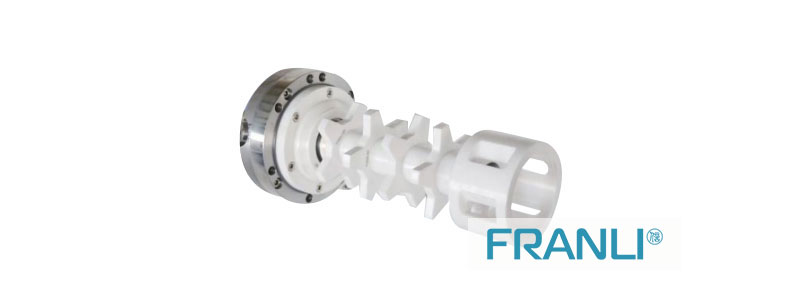
• Easy installation of the bead mill machine: The best features of this bead mill machine are: You can easily install it wherever you want. This task is so simple, and effortless. And due to this feature, it is extremely popular among other equipment. You can find the bead mill working principle so effective, and you can perform all the mixing tasks effectively without adding so much effort. As this machine is very bulky and cheap, it needs only a few minutes to install. In this way, you can reduce the labor charges and other exhausting jobs. So, you can stay worry-free about how to install this machine? As the company has made this task easier for you.
• Efficient work performance of this bead mill machine: As we know, the bead mill working principle has been created in such a way that you can achieve higher and efficient work performance on this bead mill machine. If you are looking for quality and stable work, these bead mill machines are the best option to get a consistent mixture of any particular material. You can use this bead mill for paint, ink, and coating industries. And, it is a comfortable and easy method to perform all the mixing and dispersing activities without wasting so much time. So, here bead mill working process is so necessary to obtain the desired results for the company.
• Contains grinding media of 2-3 mm size: It is the necessary feature of the bead mill working process as it includes the grinding media. In this area, grinding and other dispersing activities take place that they turn into a fine mixture. You can use a bead mill for paint, ink, and coating industries, where mixing works have been done regularly. It contains grinding media of 2-3 mm size that is enough to transform all the material to a smooth and fine paste. For this purpose, bead mill manufacturers have added advanced technology to this machine to provide consistent and quality work performances for the company. In this way, you can get a higher productivity ratio. And you can reach the peak of the higher conversion rate. Thus, these bead mill machines are ideal for fabrication companies to get their desired goals with full efficacy.
• Easy operation of the bead mill machine: It is a great feature of this SMP Agitator bead mill machine as bead mill manufacturers create this bead mill machine with advanced technology. And, with this quality, the operation of this sand grinding mill is extremely comfortable. You do not need to call any professional to do the same, and you can do it yourself without adding so much effort. So, it is another best feature to consider about this bead mill machine.
• Easy to clean the bead mill machine: This sand grinding mill is remarkably best for the fabrication companies to enhance the overall growth and production. As we know, while we use any bead mill machine, we need to clean it so that we can get hygienic work performance. For this purpose, companies manufacture this bead mill machine in a way that you can clean it comfortably without making yourself exhausted. You can go through the bead mill pdf and other relative documents that provide you the guidelines of clean this bead mill machine.
• Easy to maintain the bead mill machine: Maintaining is also a matter of concern as it requires your time and money. For this purpose, you can check the bead mill pdf and manual provided by the company at the time of purchase. You can either contact the company or read the manual carefully to know all the information about the bead mill machine. And, you can find this process is extremely simple to perform. So, you can get this bead mill machine without spending so many amounts on it. And, in this way you can concentrate on the work performance of the company.
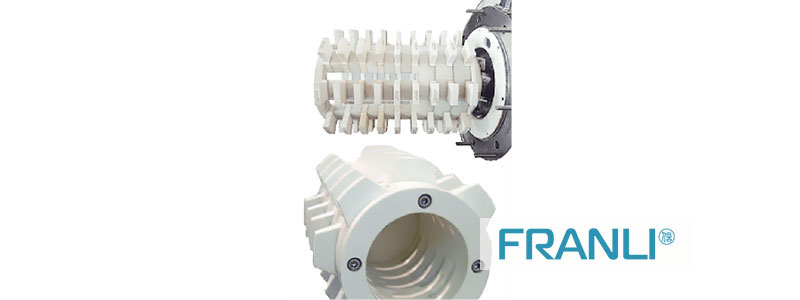
Also, you can use SMP Agitator bead mill in paint industry, ink, and other coating work companies to make all the mixing and grinding activities easier and more manageable. To get this bead mill machine, you search for those companies that deal in these machines and other equipment. For this purpose, you can get a quote or related other information about the bead mill machine.
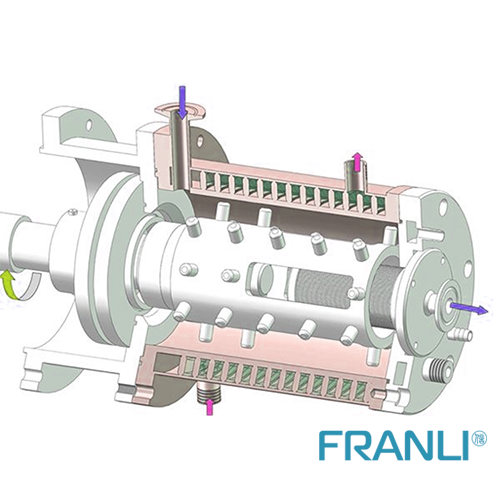
Hydraulic TRH type
Hydraulic Three Roll Mill, which is a full hydraulic auto-controlling system equipment. 1- Cooling system: an individual cooling system for each roller. 2- hydraulic control: hydraulic control pressure blades, roller gaps, etc. 3- Optional installation:PLC system with SIEMENS touching screen, FRANLI engineer set formulas of grinding according to different viscosity materials.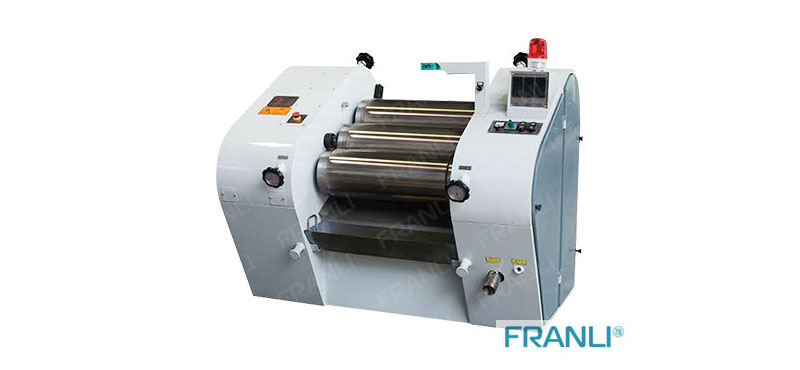
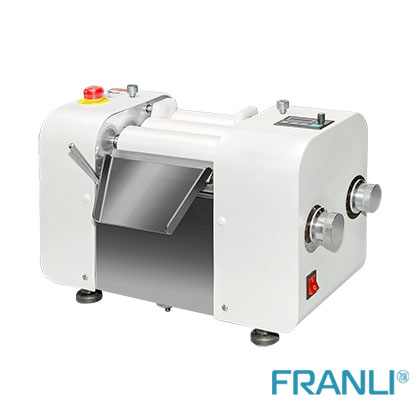
Vertical type for Grinding Powder
Also, we have a vertical three-roll mill for grinding powder and chocolate. We have 3 rollers, 4 rollers, and even 5 rollers, which are all vertical types. We export to the soap industry and chocolate companies.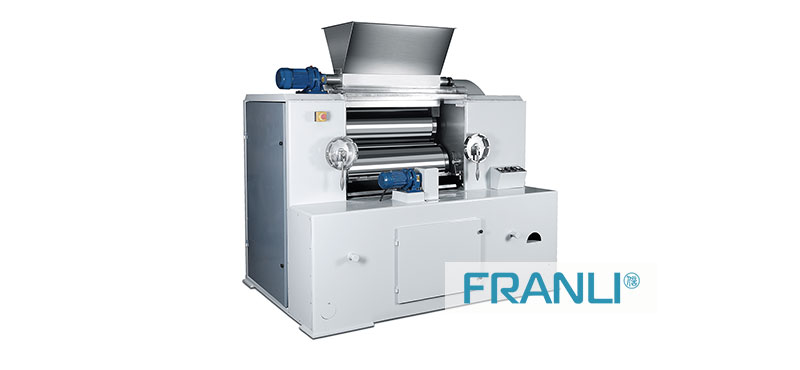
Heating type
Franli also offers a heating hydraulic three roll mill for rubber, EVA, PVS, and color masterbatch. As this type of machine grinds high viscosity material, we specially design the gear quality. This type is been Heated by oil or steam. Franli three roll mill machine are full automatic PLC controlling, hydraulic system, stable operation, reliable quality. We choose the international brand parts. Standrad parts, ABB VFD, Siemens Motor, SKF or NSK bearings, SEW or Nord reducer. A roller is 45-55mm thickness of metal, cast steel. You can widely choose ceramic, alloy, granite rollers for your material. If you have several formulas of material, we can set up formulas in the PLC system, your workers only need to choose numbers on touching the screen, don’t need to waste time to adjust the rollers’ gap or the pressure of the blade.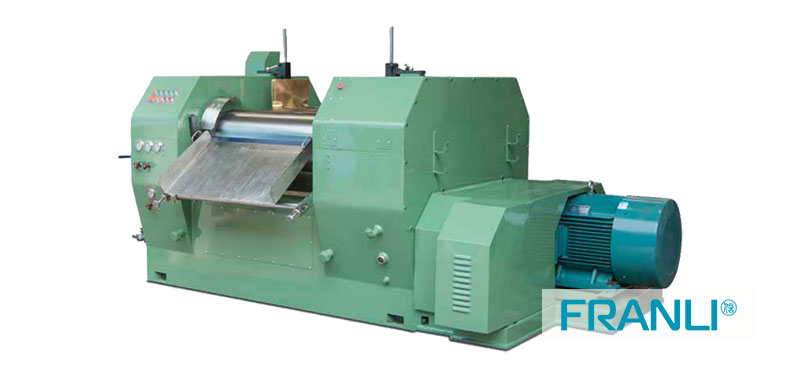
Related production lines
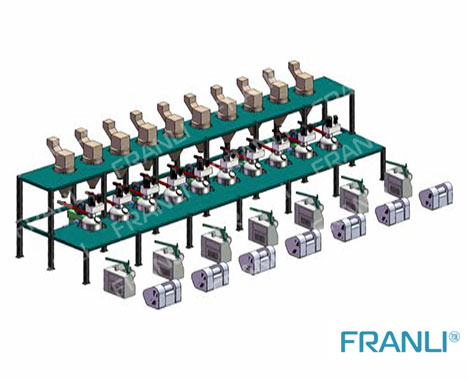
Offset Ink machine line
FRANLI is specialized in offset ink full line production for 20+ years. Helped customer save the cost, save the man power, also save the space.
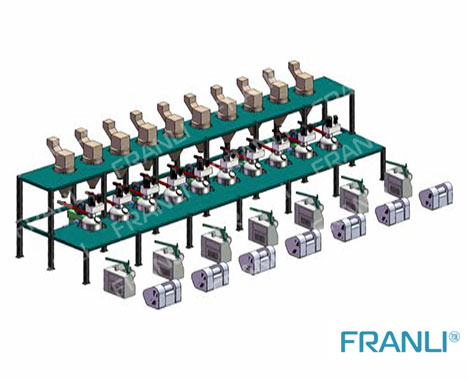
Offset Ink machine line
FRANLI is specialized in offset ink full line production for 20+ years. Helped customer save the cost, save the man power, also save the space.
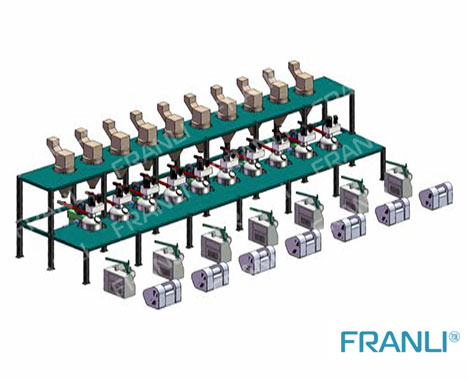
Offset Ink machine line
FRANLI is specialized in offset ink full line production for 20+ years. Helped customer save the cost, save the man power, also save the space.
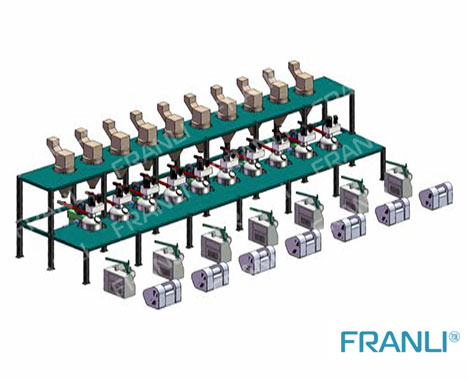
Offset Ink machine line
FRANLI is specialized in offset ink full line production for 20+ years. Helped customer save the cost, save the man power, also save the space.
Guidelines For Pearl Mill
The commonest machining process that is available now is through milling with the help of a pearl mill. The pearl mill is responsible for milling over a wide range of materials that includes wood, plastics, and metals. It inclines over the specific projects that depend profoundly on the needs and complexities of the design that are specific to the pearl mill.
The pearl mill grinding chamber with pins, specially designed grinding shaft. We install an advanced cooling system for high temperature of viscosity material. pearl mill has a German mechanical seal, NSK bearings. Which avoids the leaking of material. Magnetic filter reaches 8000 Gauss. Volume variable piston-type grinding chamber energy density and barrel pressure to attain the best dispersion and milling results.
The advantages of pearl Mill:
1. Conic grinding and mixing tank provides the best grinding effect.
2.Self-cleaning, high-precision separating ring, and grinding media with 0.8-2.5mm are acceptable.
3.Grinding area made of special anti-wearing alloy material ensures long service life.
4. Internal circulated cooling/heating integrated system suiting temperature-sensitive material (optional).
We export to TOKA ink, PEONY, Kingswood Inks, Toyo Ink, etc. We offer a warranty of 2 years for customers all over the world, offer overseas installation and training. Standard wooden case packages.
Related production lines
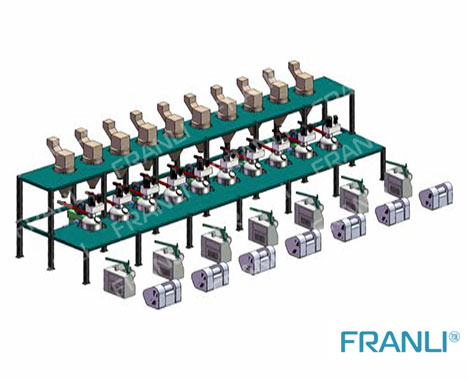
Offset Ink machine line
FRANLI is specialized in offset ink full line production for 20+ years. Helped customer save the cost, save the man power, also save the space.
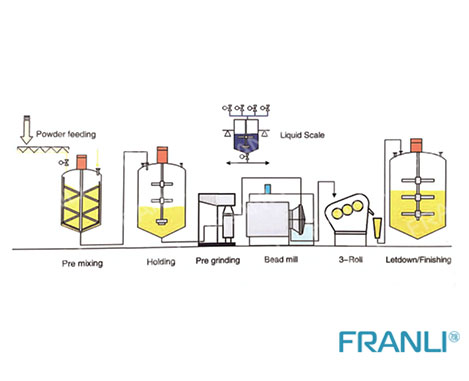
Offset Ink, UV Ink machine line
The FRANLI engineering company, offer the full set of UV INK Production Line, we can make the full drawing according with your factory size, formulas, weather and safety system.
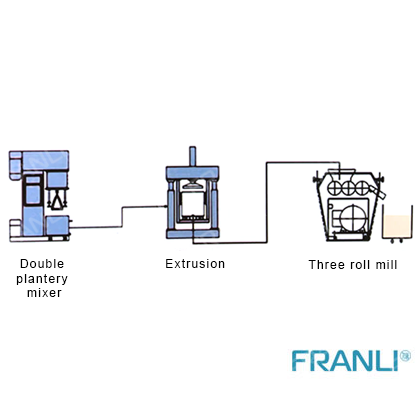
PCB INK Machine line
FRANLI supplies all equipments for the production of PCB inks, from the powder feeding station to the filling part.
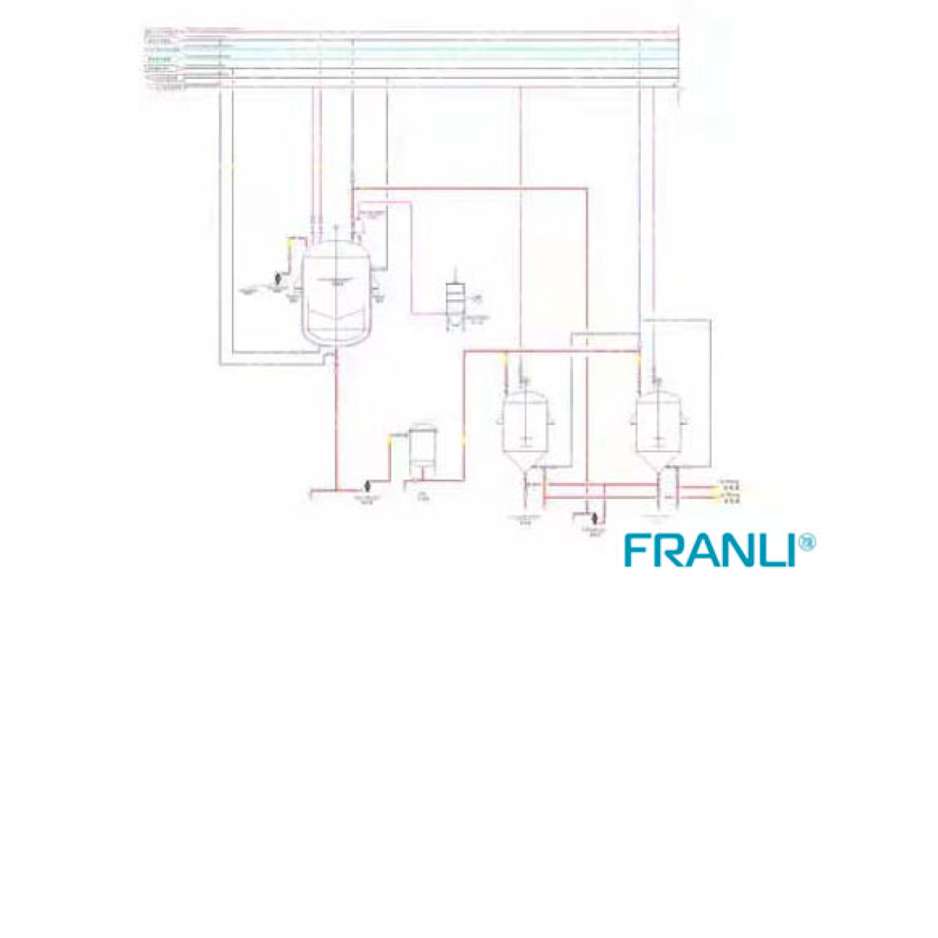
EW-pesticide line
The EW production line mainly mixes raw materials, solvents, and emulsifiers through a reactor (oil-based).
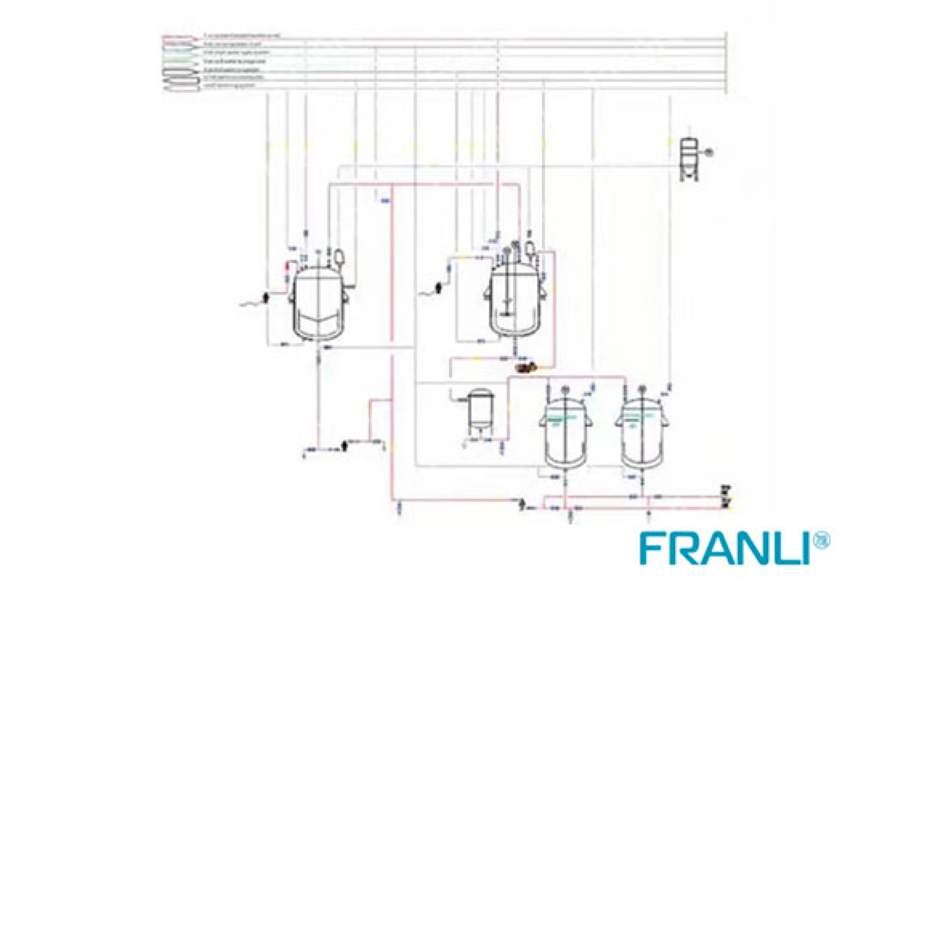
SL_EC pesticide line
The EC production line is mainly composed of an agitator mixer, bag filter, filling machine, etc.
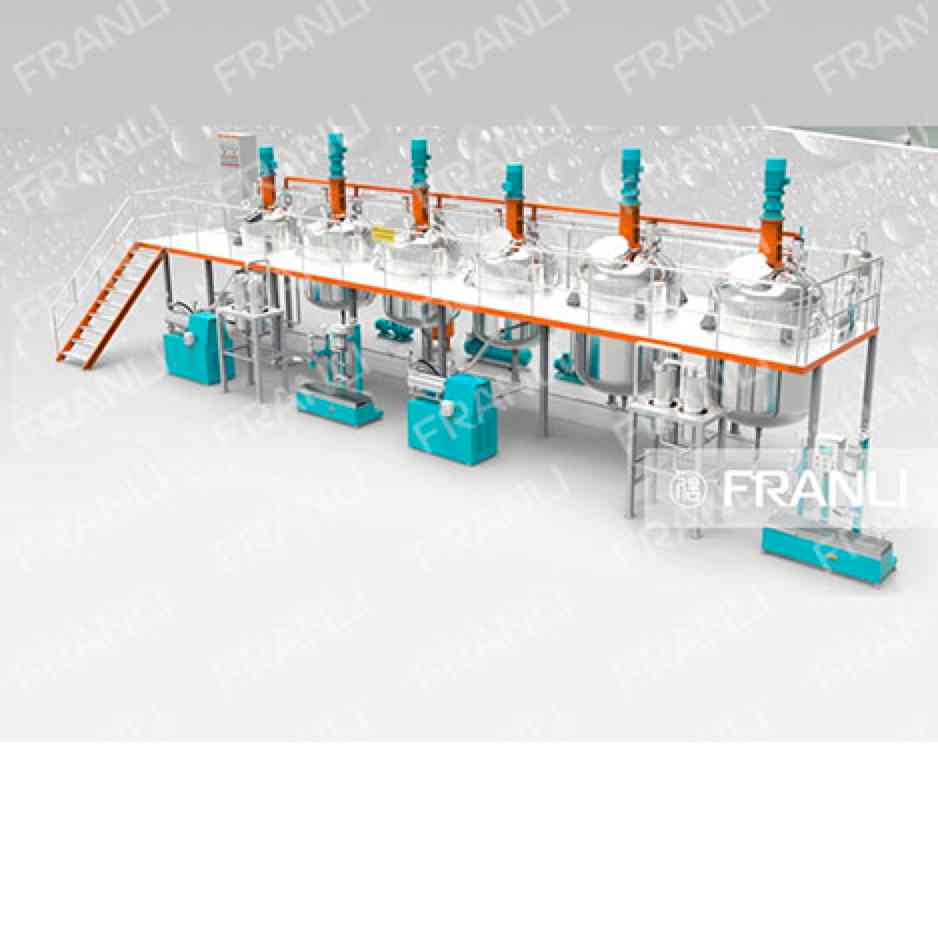
Automotive Paint machine line
The automotive paint machine line is mainly for the production and grinding of automotive paint, Automotive paint has many layers, such as Primer/electrophoretic layer, Medium coat, Colored coat, and Clearcoat.
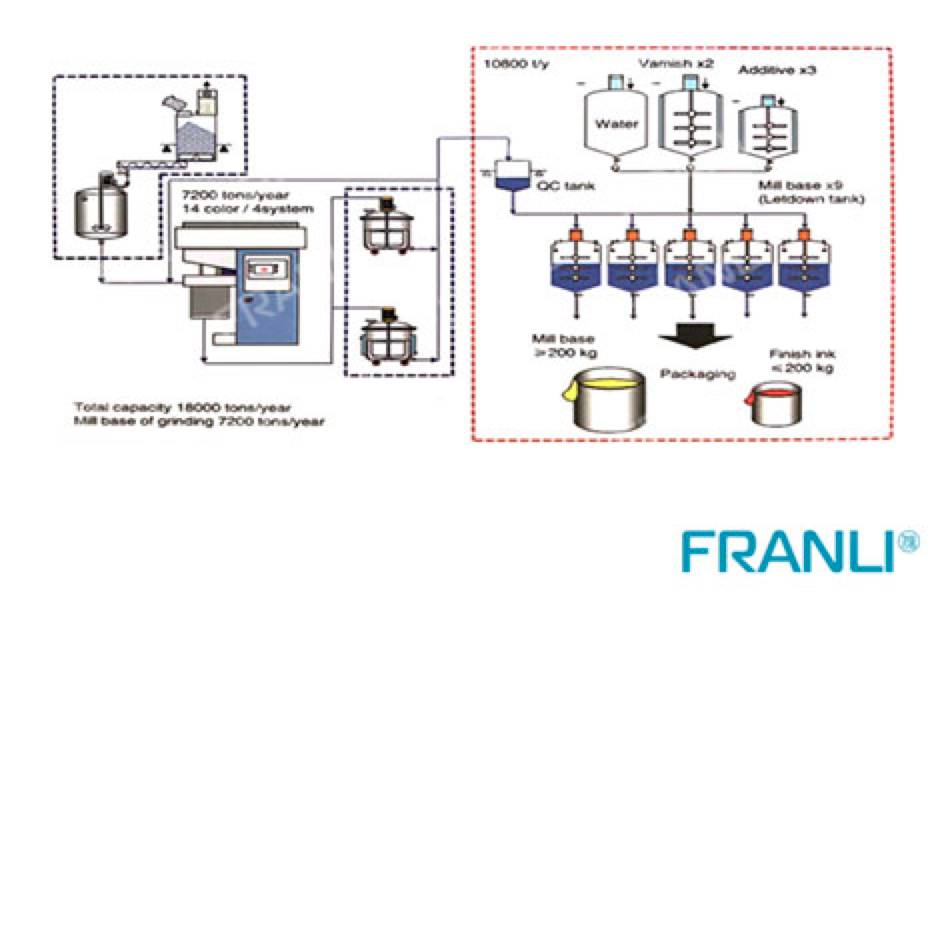
Digital Ink machine line
Franli has professional experience for digital ink machine line, we offered hundreds customers to expand production, or build up new project.