Home » Grinding Media for Bead Mill | Zirconia Beads & Zirconium Silicate Beads
Grinding Media for Bead Mill | Zirconia Beads & Zirconium Silicate Beads
Bead Mill
The bead mill is suitable for ultrafine grinding, mainly used for submicron grinding in electronic slurry, metal powder, nano-ceramics, pigments and dyes, pesticides, pharmaceuticals, and other industries.
Application: Paint, Adhesive, Battery, Pharmaceutical industry, Cosmetic
These bead mills mainly use grinding balls as the medium, and use impact, extrusion, and friction to achieve the final grinding effect, which mainly depends on the size and hardness of the grinding beads, the filling rate of the grinding beads, and the collision frequency adjustment between the grinding beads and the particles.
Requirements for grinding media used in bead mill
1. The particle size of the material and its hardness determine the energy required for crushing/dispersion.
2. The collision frequency between the grinding beads and the particles will affect the crushing/dispersion speed. (The collision frequency is controlled by the agitator speed and the size of the grinding beads)
3. The size of the gap between the grinding beads will affect the final size of the particles. Generally, the smaller the size of the grinding beads, the more collisions there are between the grinding beads and the particles.
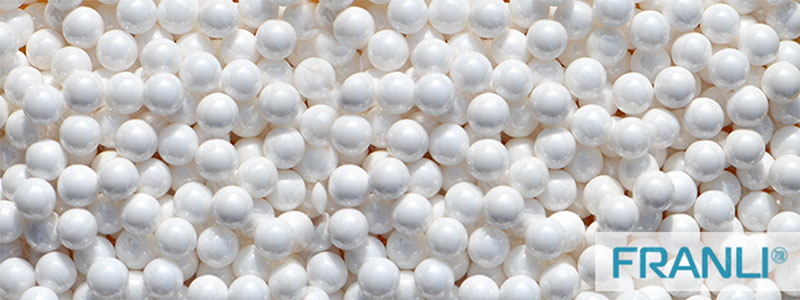
Under the same conditions, the higher the density of the grinding beads, the greater the energy provided and the higher the grinding efficiency, but at the same time, the wear on the components in the bead mill cavity will also be relatively large, so low-density grinding beads are suitable for low-viscosity slurries, and high-density grinding beads are suitable for high-viscosity slurries.
Among the grinding media of bead mills, zirconium oxide beads are the most common grinding beads. They are mainly used for ultrafine grinding and dispersion of “zero pollution” and high viscosity and high hardness materials, such as electronic ceramics, magnetic materials, zirconium oxide, silicon oxide, zirconium silicate, titanium dioxide, etc., medicine, food, pigments, dyes, inks, and special chemical industries.
Zirconium silicate beads are also a common medium in bead mill grinding. Their internal microcrystalline structure is uniform and delicate, and they have a very ideal grinding effect. Compared with zirconium oxide beads, zirconium silicate beads have a lower density and are not as efficient as zirconium oxide beads. However, high-density grinding media are not suitable for all bead mills. Their toughness is not as good as zirconium oxide beads. Their main disadvantage is that they are prone to bead breakage during high-speed grinding, so zirconium silicate beads are mainly used in vertical bead mills with lower speeds.
Particle size (size) of grinding media
Bead size is the most important factor in crushing and dispersion processing. The size of the grinding beads determines the contact area between the grinding beads and the material. The size of the grinding beads affects the efficiency of crushing and dispersion. The energy generated by the grinding beads in the crushing chamber, the collision frequency between the grinding beads and the sample particles, and the gaps between the grinding beads are the key factors affecting the efficiency of particle grinding and dispersion.
Selection of grinding bead size in the crushing process
The degree of energy applied by the grinding beads to the particles is determined by the grinding bead size and the agitator speed. Therefore, when crushing particles with large particle sizes or strong hardness, large grinding beads and high speed should be selected because high-intensity energy needs to be applied to the particles. For the grinding of submicron samples, it is recommended to use relatively small grinding beads of φ0.05~0.3mm for processing. When crushing hard particles such as silica, alumina, and hard natural ores, grinding beads of Ø 0.3mm or more are usually used as grinding media.
When performing crushing, large grinding beads are not always selected. The size of the grinding beads will affect the final size of the particles. When crushing tiny particles below 200nm, grinding beads of Ø 0.1mm or Ø 0.3mm should be used for crushing. Small grinding beads can shorten the processing time because the contact area between small grinding beads and particles is large, and the collision frequency between grinding beads and particles is increased. If the particles are soft, the impact energy required is small, and smaller grinding beads can be selected to improve the processing efficiency. Such soft particles include calcium carbonate, iron oxide, pesticides, and pharmaceutical chemicals.
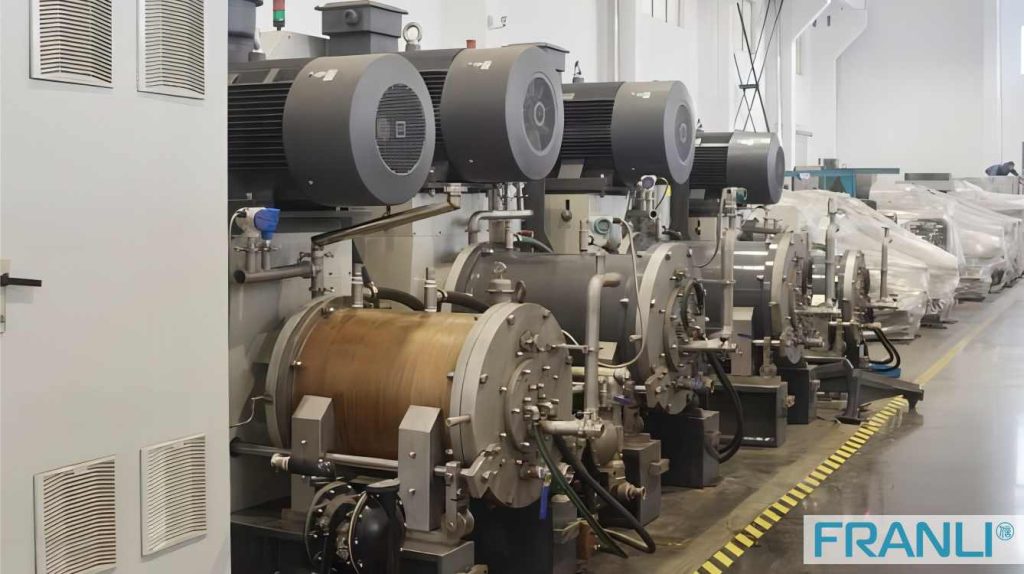
When crushing tiny particles below 200nm, the selection of grinding bead size is particularly important. Compared with small grinding beads, the gaps between large grinding beads are larger, so the number of times the grinding beads contact the particles will be small, and the crushing efficiency will be low. Therefore, small grinding beads should be used when crushing fine particles. In the selection of grinding bead size, the size of the grinding bead should be 10 to 30 times the maximum particle size in the raw material and 1000 to 3000 times the target particle size. For example, when crushing calcium carbonate, when the maximum particle size in the raw material is 10μm and the target particle size is 100nm, it is recommended to select grinding beads with Ø 0.1mm.
Bead selection in dispersion processing
In dispersion processing, the basic concept of selecting bead size is similar to that in pulverization processing, but the conditions that need to be considered are different. The biggest difference is that different bead sizes cause different degrees of damage to primary particles. The impact energy required for dispersion must not damage primary particles and disperse agglomerated particles.
Since each particle is made to a target size and provides appropriate properties for the final product, particle damage needs to be avoided. When the impact energy is too large, not only will the primary particles be damaged, but the fine fragments produced will act as a binder to cause the particles to re-aggregate. In this case, the particles in the slurry cannot be dispersed even after a long period of treatment.
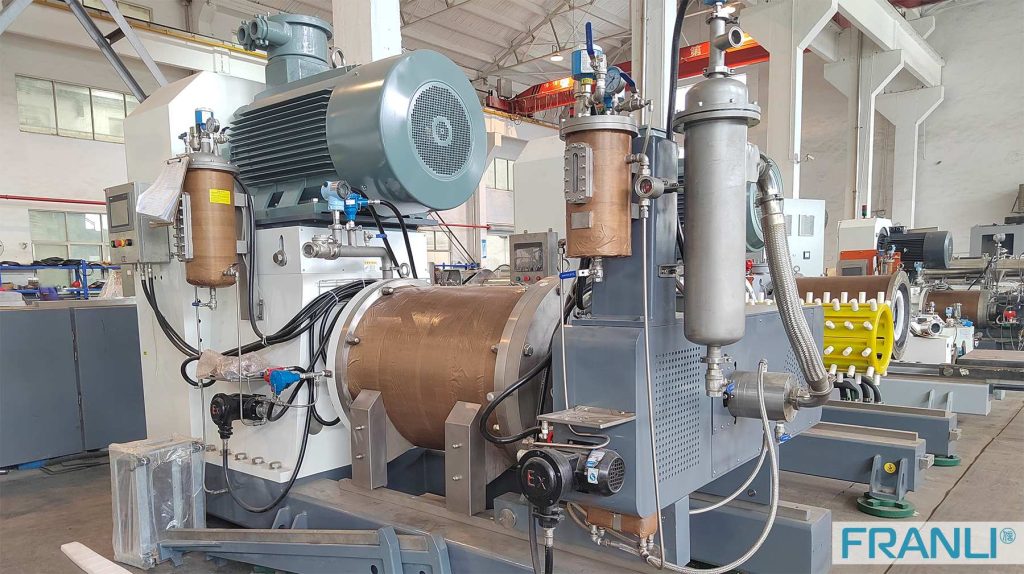
Therefore, the impact energy of the beads needs to be moderate, neither too strong nor too weak. To maintain the integrity of nanoparticles in dispersion processing, that is, to achieve low-damage dispersion of nanoparticles, it is important to use small beads to maintain low-impact energy. In addition, small beads increase the collision frequency between the beads and particles, improving the processing efficiency.
In dispersion processing, smaller beads need to be selected because the particle size of primary particles is very small. The ideal bead size should be 1,000 to 2,000 times the original primary particle. In many modern dispersion practices, the size of primary particles is mainly 10nm to 200nm, so the beads selected in the dispersion process are smaller than the beads selected in the pulverization process. For example, when the primary particle is 100nm, the bead size is usually selected below 100μm. In modern nanomaterials, the primary particle is less than or equal to 50nm. However, in the dispersion process of 10nm, it is necessary to select beads of φ30μm or smaller. In special cases, it is recommended to select beads of φ20μm or smaller.
Welcome to send inquiry to us and let’s make a win win business together !
Guidelines For Bead Mill
Bead Mill(sand mill) helps many factories to improve production. Grinding for low viscosity, well-flowing material. Self-cycling cooling system. Don’t need the cooling pump. Franli produces Disc Bead Mill, Pin Bead mill, Turbine Nano Bead mill, etc. Optional material of inner chamber and disc: hardness Alloy, Zirconia, PU.
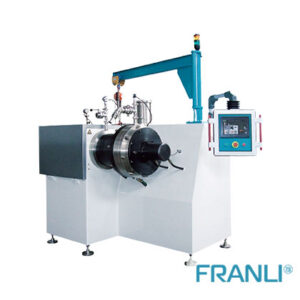
DYNO MILL – A DYNAMIC WAY TO GRIND EASIER
Dyno mill is nothing but an agitator bead mill. It is widely used in the production of paints, coatings, agrochemistry, and pharmaceutical products.
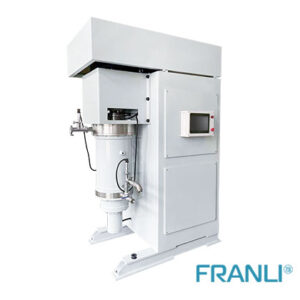
Role of Pearl Mill in the Nano Industry
Pearl Mill can handle both high and low viscosity materials. One is for Nano grinding materials, while the other is for high viscosity materials like offset ink. The operation of the Pearl Mill is straightforward, and all maintenance; may be handled quickly and efficiently. Adding grinding media from the feeding hole is simple.
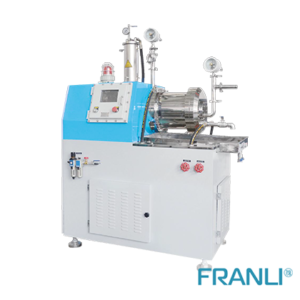
Guide to Bead Mills
The Bead mill is one of the main grindings and dispersing equipment in paint production. Bead mills for coatings are mainly divided into four categories: vertical, horizontal, basket, and special-shaped bead mills.
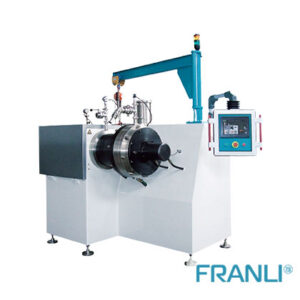
Dyno Mill|Coating & Inks
Dyno mill is a type of bead mill machine which is used in the coating industry specifically, in the manufacturing of inks products.
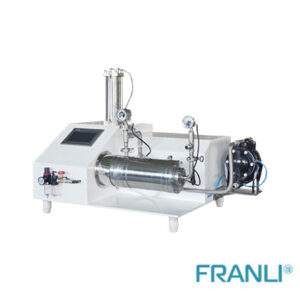
The structure and type of laboratory bead mill
The laboratory bead mill in the chemical experimental equipment, also known as the lab sand mill, is a kind of grinding equipment compared with the bead mill for industrial production.
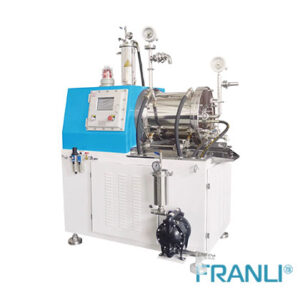
High Viscosity Material Grinding – Bar Pin Bead Mill
The bar pin bead mill is a machine suitable for ultra-fine dispersion and nano-scale grinding of water-based and solvent-based materials. The bar pin bead mill is one of the most widely used production types of equipment. With its very stable performance and sophisticated technology, it has been recognized by a wide range of users. The key thing to know is the characteristics of the bar pin bead mill, which is also the key to people’s favor of it.