Home » Guide to Bead Mills
Guide to Bead Mills
Bead Mill
The Bead mill is one of the main grindings and dispersing equipment in paint production. Bead mills for coatings are mainly divided into four categories: vertical, horizontal, basket, and special-shaped bead mills. Not only that. The bead mill can also be used in industries such as dyes, paints, inks, medicine, magnetic powder, ferrite, photosensitive film, pesticides, papermaking, and cosmetics. It is one of the most outstanding machines among wet grinding equipment.
Details of Bead Mill
- The frame of Bead Mill
- Grinding system of bead mill
- Double mechanical seal of bead mill
- The transmission system of the bead mill
- Grinding cylinder of bead mill
Application: Paint, Adhesive, Battery, Pharmaceutical industry, Cosmetic
There are two types of bead mills, namely vertical bead mills, and horizontal bead mills, and vertical and horizontal bead mills can be divided into open or closed dispersing disc bead mills, rod pin or Conical annulus bead mills; and dispersive disc horizontal bead mills and horizontal pin or horizontal conical annular bead mills. At present, the bead mill is the essence of domestic and foreign models. It has particularly high efficiency and can achieve high efficiency and high continuity of work. The entire work process can achieve extremely low pollution or zero pollution, and users can use it easily. , The bead mill produced by FRANLI has a favorable price, the structure of the whole machine is compact, and the appearance is also repeatedly designed by the designer. On the premise of satisfying the use, it also satisfies the user’s visual experience, especially with strong practicability.
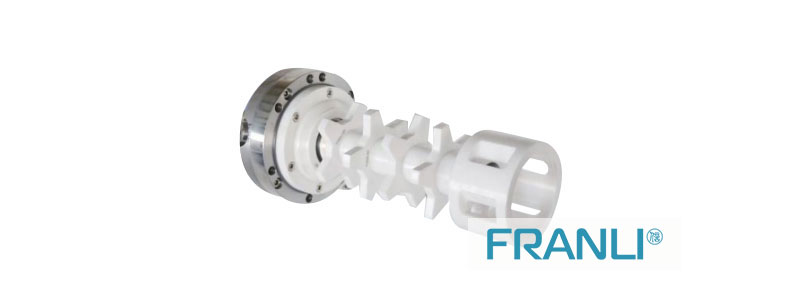
The bead mill is mainly composed of a motor, a transmission device (such as a hydraulic coupling), the main shaft, a grinding drum, a dispersion device, a separation device, a feeding system, a shaft seal, a frame, a running protection device, and a grinding and dispersing medium. The operation protection of the bead mill can be realized by the micro-intelligent electronic technology of relay and programmable controller.
The bead mill uses the material pump to feed the solid-liquid phase mixture material pre-dispersed and wetted by the mixer into the cylinder. The particles and the grinding medium produce more intense collision, friction and shearing action to achieve the purpose of speeding up the grinding of fine particles and dispersing aggregates. The bead mill grinds the dispersed material, separates the grinding medium through the dynamic separator, and flows out from the discharge pipe.
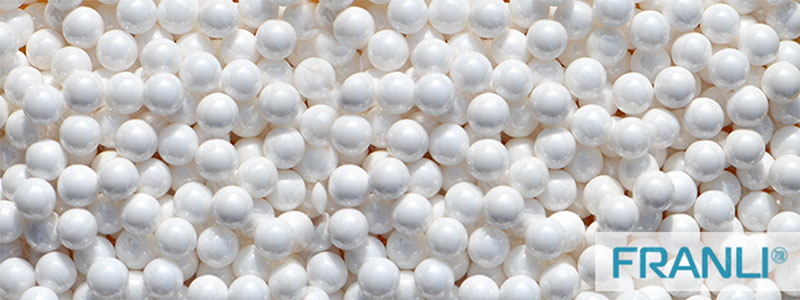
Selection of bead mill barrel
Then when choosing the barrel material of the nano-bead mill, generally choose stainless steel (of course, special materials can be selected from special materials, such as ceramics). Stainless steel has good corrosion resistance and durability. Of course, it is necessary to Look at the mechanical seal, the mechanical seal circulating fluid of the nano bead mill can reduce the damage to the product from air pollution; there are two materials for the grinding drum rotor, one is a disc grinding disc, and the other is a rod pin. These two types of grinding discs can meet the needs of users well, mainly depending on your choice of grinding thickness.
Selection of grinding media for bead mills
The horizontal bead mill is especially suitable for dispersing and grinding products with high viscosity and fine particle size. The media and materials to be milled should be selected according to what you want to produce. The horizontal nano bead mill is an interval separation device. In this way, the material and the grinding medium can be easily separated and operated; as long as the design of the nano-bead mill is reasonable, the production efficiency is very good; check the convenience of changing the zirconium beads and whether the design is reasonable in cleaning; of course, the important thing is safety Whether the protection settings are safe.
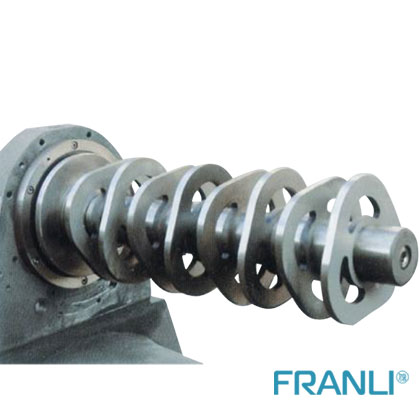
The operation process of the bead mill
1.Preparation before starting the bead mill:
(1) Observe the relevant matters in the safety regulations.
(2) All connectors are fastened and reliable, and the safety devices are complete.
(3) The amount of lubricating oil added to each rotating part has been added according to the regulations. (Note: The lubricating oil of the hydraulic coupling should be checked and confirmed by professional maintenance personnel)
(4) All electrical interlocking devices are put into normal use.
(5) Check to confirm that the material outlet of the bead mill and the outlet of the grinding medium are closed.
(6) Check the sealing liquid level and confirm that the setting value of the sealing pressure chain has been adjusted and set as required.
- Do not use pure water as the sealing fluid. It is recommended to add 30~50% ethylene glycol to the water as the sealing fluid.
- The sealing liquid level should not be lower than the specified minimum scale value.
- The set values of sealing pressure and flow need to be set by professional maintenance personnel, and operators cannot adjust them without authorization.
- The sealing system is put into operation, and the pressure and flow are within the specified setting range.
- The adjustment of sealing fluid flow and pressure is realized by adjusting the regulating valve on the sealing fluid safety device installed on the machine. (Facing the pressure gauge, the knob on the right can adjust the flow, and the knob on the left can adjust the pressure)
(7) Confirm that the grinding media has been loaded as required. If the requirements are not met, professionals should be notified to join.
- The filling of grinding media needs to be carried out by the operator in this position under the guidance of the designated personnel.
- When the filling is complete, close the inlet for grinding media.
(8) Open the cooling water inlet valve, start the cooling water supply system, confirm that the system is working normally, the tank path is unblocked, and adjust the cooling water inlet pressure, the maximum cannot exceed 300 kph.
(9) Open the valve of the bead mill feed valve outlet pipeline storage tank and the feed pipeline outlet valve.
(10) Open the feed pump inlet valve to prepare to start the feed pump.
- A funnel is installed at the suction port of the pump, open the cock of the three-way valve on the inlet pipeline of the feed pump (the handle is vertically upward to open), pour clean water into the pump through the cock, and turn the cock handle clockwise to the horizontal after full Location.
- There may be pressure in the pipeline, be careful when opening the cock.
(11) After N times of driving or long-term parking, the liquid should be injected into the pump before starting the pump.
2.Boot process
(1) Open the control box and confirm that the maintenance switch is in the “0” position (this switch can only adjust the voltage when it is instructed).
(2) After receiving the driving instruction, power on the system and observe the current indication on the control panel.
(3) Press the feed pump and stirring operation button on the control panel to start the system. (Note: The operation of the agitator is interlocked with the feeding pump. After the feeding pump is started, the stirring must be started within 20 seconds, otherwise, the pump will stop feeding. When the agitator is started, the pump must be within 20 seconds. is put into operation, otherwise, the agitator will stop.)
(4) If the machine is not started or the current is too high, the operator must shut down immediately, and can only restart the machine after the fault is cleared (shutdown can be done by pressing the agitation stop and pump stop buttons on the control box).
(5) Adjust the feed flow through the adjustment button of the feed pump, and control the feed pressure within the set range.
(6) Precautions for the normal operation of the machine:
- Observe the changes in voltage and current on the control panel.
- Observe the pressure and backflow of the sealing fluid, and check whether the outlet pipeline of the sealing fluid is overheated. Drain the sealant leak bottle every day.
- Observe that the leakage of the sealing fluid cannot exceed the allowable value.
- Observe the changes in cooling water pressure, flow, and temperature, and adjust the water volume and pressure in time.
3.Notes on shutdown:
(1) After receiving the stop instruction, press the “Stop stirring” and “Stop pump” buttons on the control panel to stop the operation of the bead mill.
(2) Connect clean water to the feeding pipeline, close the main valve of the material, and clean the bead mill until the liquid at the outlet of the bead mill is clear.
(3) Close the valve on the inlet and outlet pipelines, open the discharge valve on the bead mill, and drain the residual liquid.
(4) Close the cooling water inlet and outlet valves.
(5) After confirming that there is no liquid in the bead mill, and the pressure gauge shows that there is no positive pressure in the system, the inlet and outlet valves of the sealing liquid can be closed.
(6) Cut off the power supply of the bead mill system.
4.Emergency shutdown processing in emergencies:
(1) This equipment is equipped with an interlocking device, which will automatically stop in the event of water, power, material, or sealing fluid. Emergency stop button on the control panel. In the following cases, the emergency manual stop should be performed (in the case of the failure of the interlock device).
- Stop material.
- Stop the cooling water or the cooling water flow is insufficient.
- Stop sealing fluid or leaking sealing fluid.
- There is a large amount of liquid leaking from the seal.
- Power outages. (The system will automatically stop after a power failure, but the power supply of the system should be cut off)
- When the system detection index exceeds the chain setting value.
(2) Emergency manual stop should be taken in one of the following situations.
- Personal injury caused by equipment.
- There is abnormal sound in the bead mill, loose joints, and a lot of leakage from the pipe interface.
- The feeding pump has abnormal sound, and the temperature rise of the bearing part exceeds 50℃.
- Broken rotating belt.
- Fragments of the polyurethane lining in the bead mill were found in the material.
(3) After the emergency stop, stop the operation of the auxiliary system of the bead mill in the normal order and clean it.
(4)Daily maintenance of bead mill:
(1) Change the sealing fluid every 4 weeks.
(2) Professionals are required to perform a fault-free inspection of the control unit cut-off switch every week.
(3) Add lubricating oil to the bead mill every 3 months.
(4) Remove the safety cover every 3 months and check the tension of the V-belt.
Welcome to send inquiry to us and let’s make a win win business together !
Guidelines For Bead Mill
Bead Mill(sand mill) helps many factories to improve production. Grinding for low viscosity, well-flowing material. Self-cycling cooling system. Don’t need the cooling pump. Franli produces Disc Bead Mill, Pin Bead mill, Turbine Nano Bead mill, etc. Optional material of inner chamber and disc: hardness Alloy, Zirconia, PU.
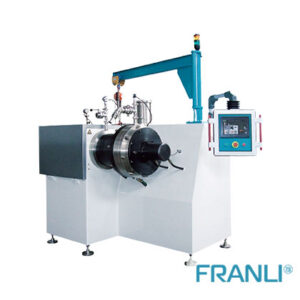
DYNO MILL – A DYNAMIC WAY TO GRIND EASIER
Dyno mill is nothing but an agitator bead mill. It is widely used in the production of paints, coatings, agrochemistry, and pharmaceutical products.
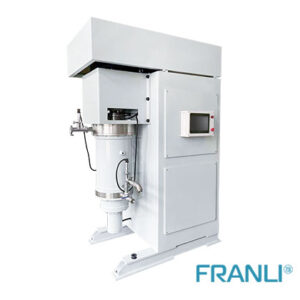
Role of Pearl Mill in the Nano Industry
Pearl Mill can handle both high and low viscosity materials. One is for Nano grinding materials, while the other is for high viscosity materials like offset ink. The operation of the Pearl Mill is straightforward, and all maintenance; may be handled quickly and efficiently. Adding grinding media from the feeding hole is simple.
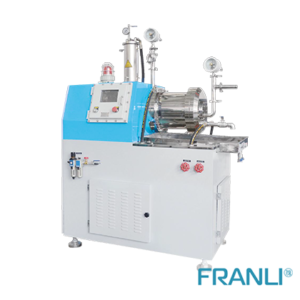
Guide to Bead Mills
The Bead mill is one of the main grindings and dispersing equipment in paint production. Bead mills for coatings are mainly divided into four categories: vertical, horizontal, basket, and special-shaped bead mills.
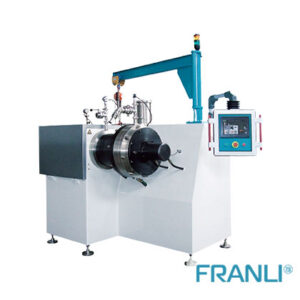
Dyno Mill|Coating & Inks
Dyno mill is a type of bead mill machine which is used in the coating industry specifically, in the manufacturing of inks products.
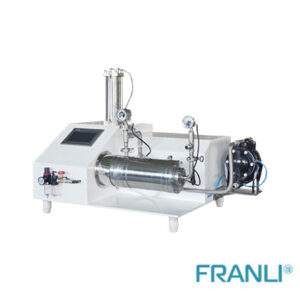
The structure and type of laboratory bead mill
The laboratory bead mill in the chemical experimental equipment, also known as the lab sand mill, is a kind of grinding equipment compared with the bead mill for industrial production.
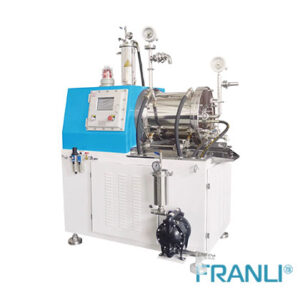
High Viscosity Material Grinding – Bar Pin Bead Mill
The bar pin bead mill is a machine suitable for ultra-fine dispersion and nano-scale grinding of water-based and solvent-based materials. The bar pin bead mill is one of the most widely used production types of equipment. With its very stable performance and sophisticated technology, it has been recognized by a wide range of users. The key thing to know is the characteristics of the bar pin bead mill, which is also the key to people’s favor of it.