Home » Three Roll Mill
Three roll mill
Three roll mills are widely used in a variety of chemical industries, from medium to high viscosity productions. FRANLI machine can break open all kinds of pigment, UV ink, offset ink, decorative paints, and Lubricants, it also can catch the greatest fineness in cosmetics/ lipstick and electronics industries.
Three roll mill video
Three Roll Mills mostly mill high viscosity material lipstick, ink, soap, etc. Cooling system: Control individual roller control the temperature according to and materials control individual roller control and temperature according to and materials control individual roller control the temperature according to materials. Franli three roll mill can get 1-5um according to different material control individual roller control the temperature according to materials. Discharging material is keeping one level. The roller gap is the same. Fully-Safty system to protect operations.
Welcome to send inquiry to us and let’s make a win win business together !
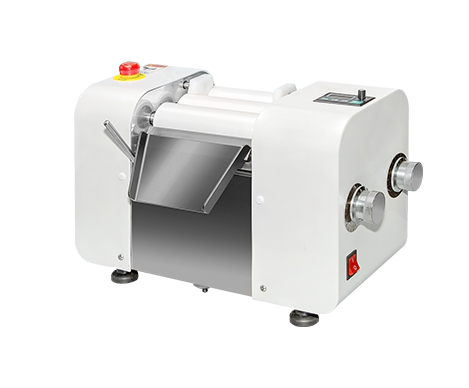
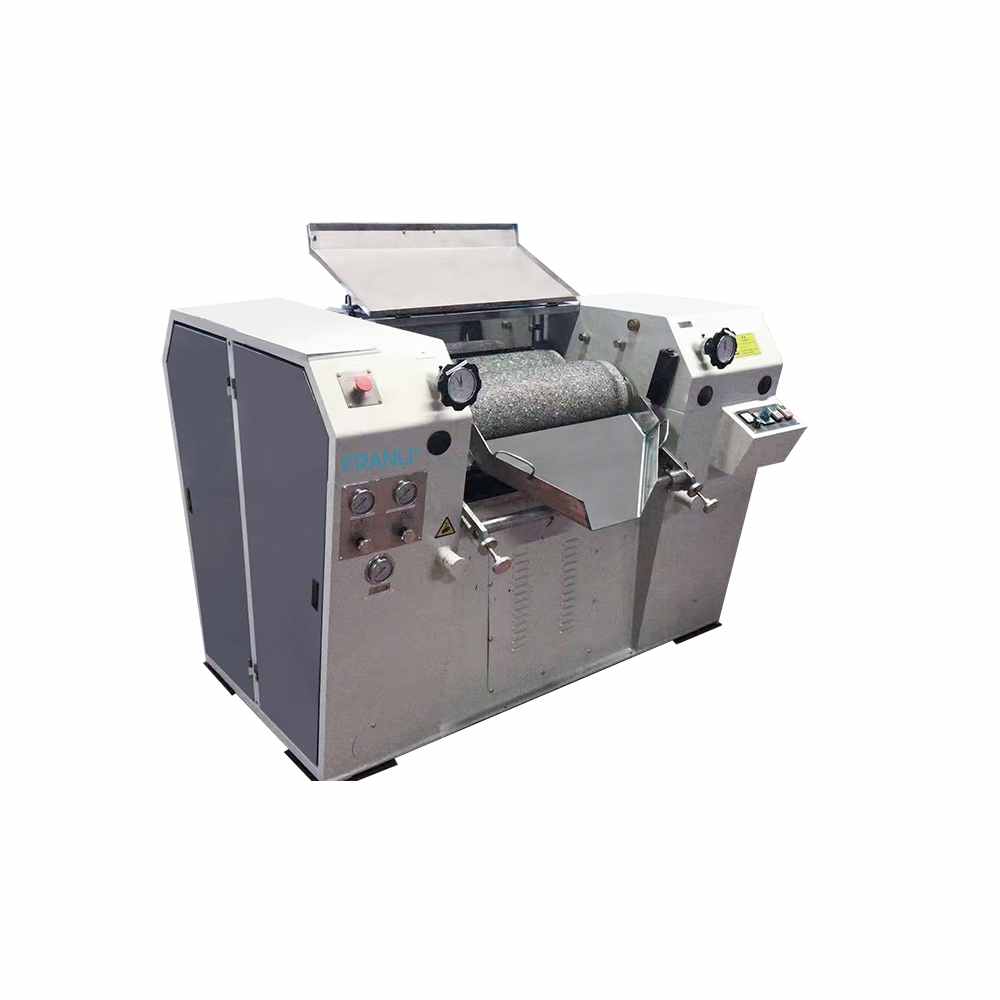
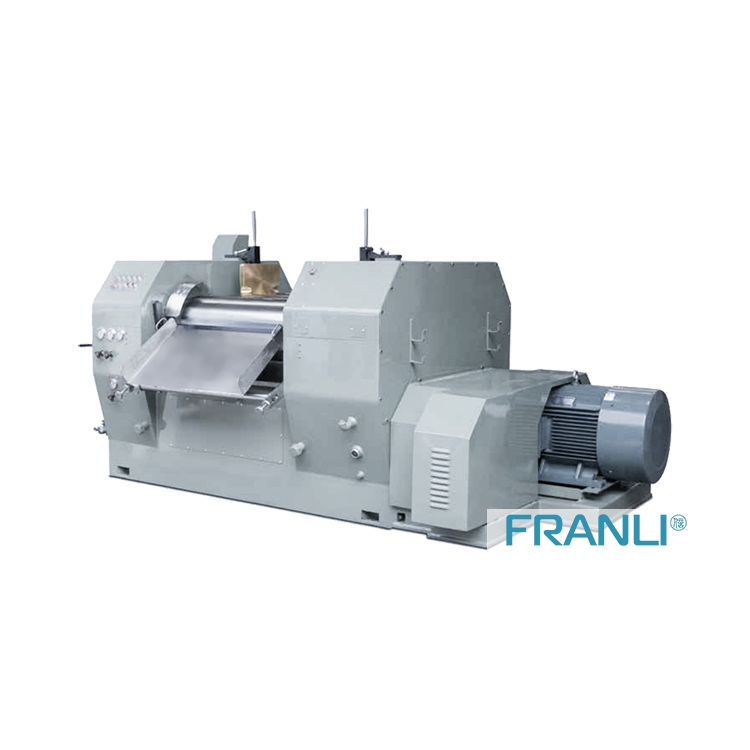
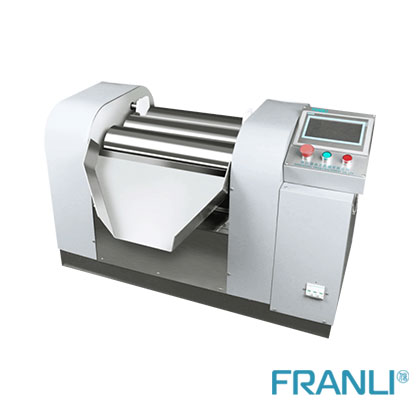
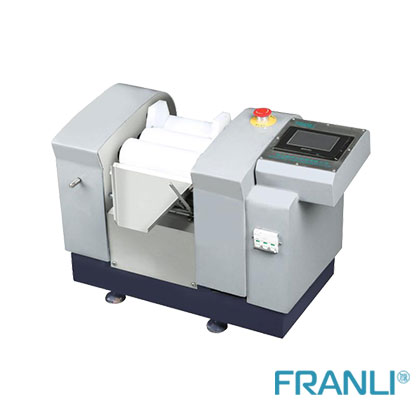
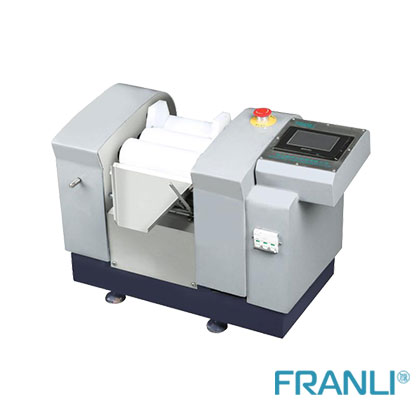
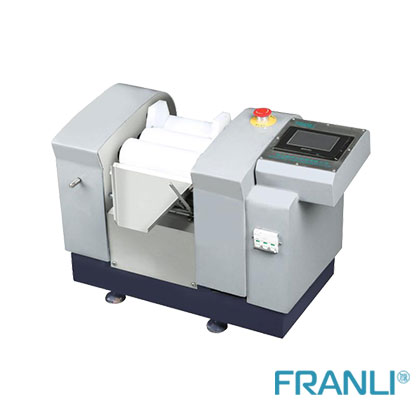
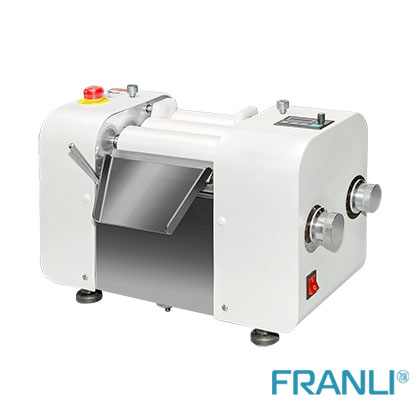
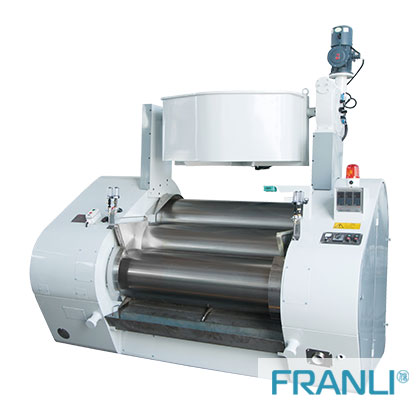
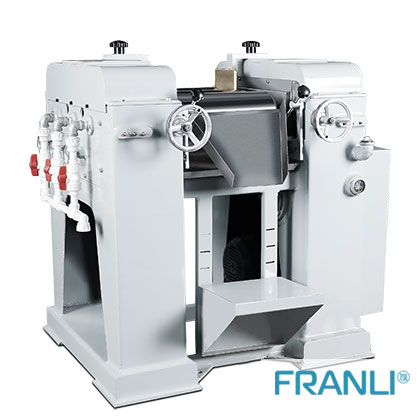
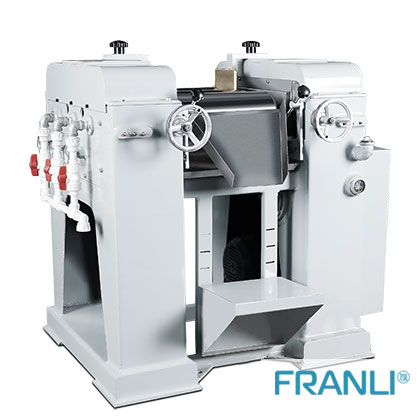
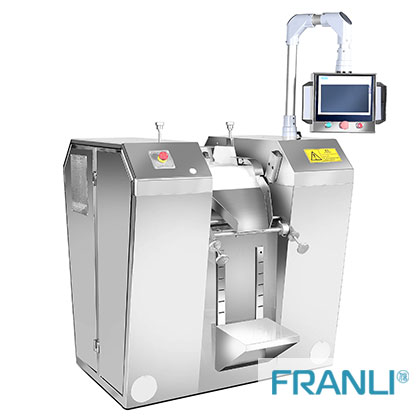
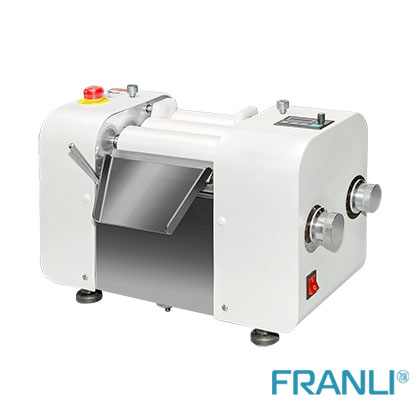
Guidelines For Three roll mill
Three roll mill is the most effective grinding and dispersing equipment for high viscosity materials. It is mainly used for the grinding of various paints, inks, pigments, plastics, cosmetics, soaps, ceramics, rubber, and other liquid slurries and paste-like materials.
Three roller mill, with easy operating and safe cleaning. FRANLI nowadays has a different model of manual Triple Roller Mill, Hydraulic type, and Lab type. They have their advantages and features to meet different requirements.
We have different series of Three Roll Mill.
TRS &TRM Manual type
Three Roll Mill, their gap of the roller is controlled by adjustable wheels. TRS three roller mill is an updated type based on S triple roll.
1-TRS machine transfer gears that soak in oil (oil box). Keeping longer life of the operation, less noise.
2- Cooling control system: TRS three roller machine installed thermometer, easily check material temp. Three rolls are normally connected with Chiller.
3- normally Reach 10-20um by first passing grinding
1- Cooling system: an individual cooling system for each roller.
2- hydraulic control: hydraulic control pressure blades, roller gaps, etc.
3- Optional installation:PLC system with SIEMENS touching screen, FRANLI engineer set formulas of grinding according to different viscosity materials.
While three roller mill, transfer gears with Grease, cant check chain well. But it is still widely used in Soap, printing industries.
Hydraulic TRH type
Hydraulic Three Roll Mill, which is a full hydraulic auto-controlling system equipment.
1- Cooling system: an individual cooling system for each roller.
2- hydraulic control: hydraulic control pressure blades, roller gaps, etc.
3- Optional installation:PLC system with SIEMENS touching screen, FRANLI engineer set formulas of grinding according to different viscosity materials.
Lab TRL Type
Lab three roll mill with PLC Touching Screen,which is widely used in medicine, ink, cosmetics, and electronics industries. Small size, digital number auto-operation. Which smarter, safer, and faster. Which is customized for different material requirements.
Vertical type for Grinding Powder
Also, we have a vertical three-roll mill for grinding powder and chocolate. We have 3 rollers, 4 rollers, and even 5 rollers, which are all vertical types. We export to the soap industry and chocolate companies.
Heating type
Franli also offers a heating hydraulic three roll mill for rubber, EVA, PVS, and color masterbatch. As this type of machine grinds high viscosity material, we specially design the gear quality. This type is been Heated by oil or steam. Franli three roll mill machine are full automatic PLC controlling, hydraulic system, stable operation, reliable quality. We choose the international brand parts. Standrad parts, ABB VFD, Siemens Motor, SKF or NSK bearings, SEW or Nord reducer. A roller is 45-55mm thickness of metal, cast steel. You can widely choose ceramic, alloy, granite rollers for your material. If you have several formulas of material, we can set up formulas in the PLC system, your workers only need to choose numbers on touching the screen, don’t need to waste time to adjust the rollers’ gap or the pressure of the blade.
About the feeding system, we have several kinds for different viscosity of the material. Such as a feeding pressure machine, also called an extruder machine. And feeding system is installed on the top with a single reducer motor. While if your material is a crazy high viscosity, and small batch production, we suggest that it’s better to feed material into rollers by manual scrapper.
Our package is a standard export wooden case, and our factory is close by shanghai port, fast delivery, and cheaper shipment. Welcome to connect with us. we will choose a suitable three roll mill for your material. Of course, you are welcomed to send us your material for the first trial before offering an order.
The production of high-quality carbon black is inseparable from the role of the three roll mill. FRANLI series three roll mill can perfectly realize the method of uniformly dispersing carbon black pulp. The main function of the three roll mill is to rely on pressure and shear force to overcome the cohesion of carbon black to achieve the purpose of pulverizing and dispersing carbon black.
The carbon black three roll mill, with a minimum processing capacity of 0.02L/hour to a maximum of 20L/hour, perfectly solves the user’s transition from laboratory testing to small and medium-scale trial production. The highly innovative design makes the device more compact and can be easily placed on the laboratory desktop. The very friendly human-machine interface is realized by the full-touch industrial control screen. The unique online gap correction and recipe menu functions make it easier to use the equipment so that users no longer face the cold equipment, but control it in an interactive operation mode.
Carbon black is widely used in rubber, plastics, coatings, inks, etc. It can be used as a reinforcing agent, colorant, conductive material, anti-ultraviolet agent, etc. Structural properties affect the application, and its particle size, structure, and surface functional groups have a great impact on the application properties. The particle size of carbon black is an important property. The smaller the particle size, the larger the specific surface area, and the improvement in blackness, tinting strength, conductivity, reinforcement, and UV resistance, but its dispersibility decreases, such as in plastics. , The difficulty of dispersion in coatings and inks increases, and the viscosity increases. Coating and ink liquid systems are prone to poor dispersion problems such as flocculation, thickening, agglomeration, and delamination, which have a lot to do with dispersion equipment. Many carbon black manufacturers use kneaders to disperse color paste, but there are problems such as dead corners and uneven dispersion in stirring, which makes the product less than expected.
While the three roll mill under FRANLI is running, there is no leakage, uniform discharge, good parallelism of the rollers, and no displacement after use; the carbon black slurry is diluted and tested by scanning electron microscopy (SEM), and it is found that there is no large The micelles showed good dispersibility and met customer requirements.
Advantages of FRANLI three roll mill
① Three roll mill adopts one cycle, it is possible to completely realize the homogenization and dispersion of the material, reduce the particle size, and break the agglomerated particles. The result is a homogeneous slurry that provides the perfect basis for further processing of the material.
②The three roll mill can adjust the distance between each roller with a touch screen to ensure perfect parallelism of the rollers. The elastically tensioned blade socket ensures constant blade pressure and does not require readjustment during operation.
③Rollers of different materials can be used, the choice of roller and scraper material – from stainless steel to alumina, silicon carbide, and zirconia – to meet various needs.
④The safety device on the three roll mill ensures the maximum safety of the operator, and the machine can be cleaned easily and quickly.
⑤FRANLI’s first IoT and intelligent three-roll mill solution in the industry solves the problems that customers encounter in the use of data that cannot be quantitatively analyzed, data is lost, equipment is independent of each other, and cannot be managed and controlled through the Internet. It allows customers to analyze the data of the equipment, assign and manage the authority of the employees, and keep the whole process record and backup of the equipment operation process, which is conducive to the research, design, and development of processing parameters. In addition, the intelligent IoT platform can also be connected to equipment platforms such as mixers, three-roll mills, feeders, and homogenizers, and can be connected to online viscometers, mid-infrared, particle size analyzers, and other instruments for online monitoring.
Application of three roll mill in lipstick production
Problems with using a three roll mill lipstick
The three roll mill is one of the most important dispersing equipment used to produce ink or paste products, and it is also the most effective grinding and dispersing equipment for high-viscosity materials.
The three roll mill is mainly used for the grinding of various paints, inks, pigments, plastics, cosmetics, soaps, ceramics, rubber, electronic pastes, and other fluid slurries and paste-like materials.
The working principle of the three roll mill
The three roll mill is mainly composed of an electric motor, transmission device, drum, frame, feeding and discharging device, adjustment device, cooling system, and other components, and has three rollers installed on the iron frame. The material can be selected according to different materials, generally, there are ceramic rollers, stainless steel rollers, marble rollers, etc., and it can be installed horizontally or slightly inclined. The state of the grinding material of the three roller mills is mainly through the mutual extrusion of the surfaces of the three rollers, and the friction and shearing action of different speeds, to achieve the best effect of grinding and dispersion. The steel drum can be hollow and cooled by water. Due to the different rotation directions of the three drums (the rotation speed increases sequentially from the feeding roller to the discharging roller), it produces a good grinding and dispersing effect.
Grinding slurry using a three roll mill
By adjusting the distance between the three rollers of the three-roller, the slurry has corresponding pressure and shearing force during grinding, and also easily overcomes the cohesive force between the powder particles, breaking into fine particles and fully dispersed in solvents and resins. When the particles enter the gap between the rollers, the shear force of the three roll mills is the largest in the tangential direction of the roller contact part. In actual operation, the large particles or agglomerates in the slurry are just beginning When put into the feed port of the three roll machine, it cannot enter between the rollers, and it continues to perform a “rod-like” rotating motion until the volume of the slurry on the roller is very small, and the oversized particles enter the roller. During the grinding process, it is crushed or adhered to the surface of the roller (so at the end of each grinding, the slurry on the roller needs to be shoveled with a spatula and re-entered for grinding to ensure the uniformity of grinding).
Precautions for operating a three roll mill
The three roller mills are high-pressure (very small roll distance) wet grinding equipment, so safe operation is very important. When the three rollers are working, the non-workers on site need to keep a certain distance from the three rollers. Beware of personal limbs and foreign objects (clothing, shovels) getting caught in the feed rollers or other gaps, resulting in personal safety problems.
How to choose a three roll mill?
Choosing the right three roll mill has always been the most common problem for many users, which not only affects the user’s experience but such as human and material resources, production requirements, etc. When the manufacturer meets the after-sales service and the price is moderate, the quality, size, and feeding method of the three roller mills are more things we need to think about.
(1) The quality of the three roller mill
The quality problem of the three roller mill often exists on its three rollers, and different rollers will choose different materials for forging according to the material, such as alloy steel, ceramics, marble, etc. Different forging methods will also affect the material of the rollers. For example, the commonly used forging method in the past was the cold casting method, but now the centrifugal casting method is used. The new method can obtain a 10-18mm thick anti-wear surface This kind of surface layer has super wear resistance and can be repaired multiple times, generally, 0.3-0.5mm each time, and at least 3-4 times can be repaired. replaced or corrected. The hardness of the damage-resistant layer on the surface of the roller is controlled by the metal composition, and the good hardness is generally in the range of 550-600 Bush hardness.
(2) Dimensions of the rollers of the three roller mill
For the machining of the surface of the roller, the main problem is the height of the roller (that is, the circumferential length of the section in the middle of the roller is greater than the circumference of the two ends). The distribution on the line is uneven, so the material is unevenly discharged.
(3) Feeding method of the three roller mill
In the operation of the three roller mills, the feeding problem has always been one of the most labor-intensive tasks. It should be known that the feeding method is generally to shovel the material in the barrel little by little and put it into the feeding port by manpower. The large-scale feeding manpower can still be solved, but the large-scale feeding needs to be solved in another way, at this time, a hopper is needed. As a high-quality three roller mill manufacturer, FRANLI has dumped, pumping, and extrusion feeding devices, that can be customized according to the strength of the materials used.
Influence of parameter setting on grinding effect
(1) Set the pressure of the three roll mill
Adjusting the pressure between the rollers is the most important step in the operation of the three roller mills. When the machine is started, if it is a model with a fixed middle roller, it is necessary to adjust the pressure of the feeding roller and the discharging roller, so that the slurry is in the grinding process. If the pressure is too large or too small, the phenomenon of uneven discharge will occur. You can judge whether the pressure is reasonable according to the discharge state.
When grinding the material, it is generally ground several times according to the fineness requirements of the final product, and the set pressure of the three roller mills is usually increased one by one to ensure that the wetting and dispersing process of the agglomerated particles is a “gradual” process. This makes it more stable and controllable.
(2) Set the temperature of the three roller mill
When using a three roller mill, the adjustment of the temperature of the rollers is also very important, which includes two aspects. First, the rollers themselves are rubbed against each other, and the rollers are also rubbed with the slurry, which leads to the increase of the temperature of the rollers, and then The temperature of the slurry increases as the temperature of the roll increases so that the decrease in viscosity affects the output. On the other hand: if the slurry temperature is too high, the temperature difference between the slurry and the ambient temperature is too large, which will easily cause condensed water to condense on the surface of the product and affect the performance of the product.
Blades of a three roll mill
The blade must be flat. The uneven blade is easy to wear on the surface of the roller irregularly. At the same time, there may be too much local friction, which leads to the local temperature of the roller being too high (accelerating the wear and aging process of the surface of the roller).
The width of the knife edge is appropriate. The width refers to the width of the bevel of the knife edge. If the knife edge is too wide, it is easy to curl the edge. Or production efficiency); too narrow, and the front is not sharp, affecting the discharge efficiency.
Installation position: The installation position of the blade is generally on the horizontal connection line between two adjacent rollers. Too high or too low will affect the output. The angle of contact between the blade and the roller is also very important. This angle refers to the angle between the blade and the contact point. Too small is easy to wear, and too large is easy to wear the blade. When the new blade is just used, the angle can be smaller, and then gradually during use. Increase the angle to find a balance between efficiency and cost.
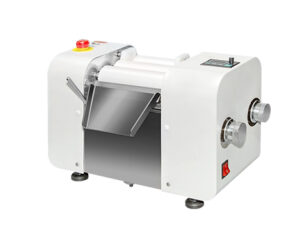
Three Roll Mill For Carbon Black|High Grinding & Dispersion
Three roll mill is the main equipment for grinding colored carbon black, as it is used extensively in rubber, plastics, paints, and inks, and some carbon black is added.
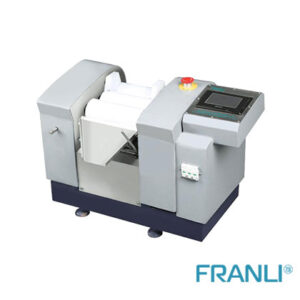
Laboratory Three Roll Mill|PLC Control System & Experimental
The laboratory three roll mill is equipped with the most advanced PLC functions to continuously improve the operability of the most primitive production equipment.
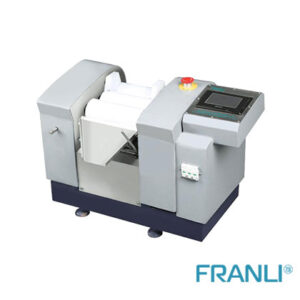
Three Roll Mill For Grease
The three roll mill plays a vital role in the grinding of grease. Grease is essentially a kind of lubricating oil, which is a solid or semi-solid product formed by one or more thickeners through the grinding and dispersing action of a three roll mill.
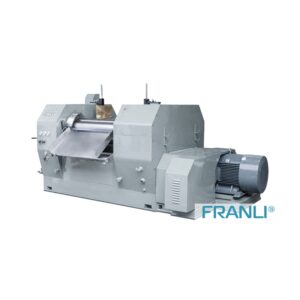
Three Roll Mill For Attapulgite
Three roll mill is the main equipment for grinding attapulgite. The attapulgite is ground and dispersed mainly because it is a natural colloid. Even if the size of the attapulgite reaches 0.1mm, it cannot be easily dispersed by the machine, so the final state of attapulgite formation has been greatly developed.
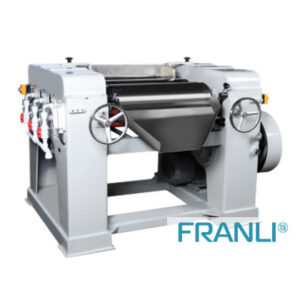
Rolls of a three-roll mill
The three-roll mill is mainly used for grinding materials of various viscosities and is one of the best wet grinding equipment. The dispersing and emulsification effect of the three-roll mill is excellent, especially for ink, paint, colloid, chocolate, plastic, cosmetics, etc., whether it is liquid slurry or paste material, the three-roll mill can work easily.
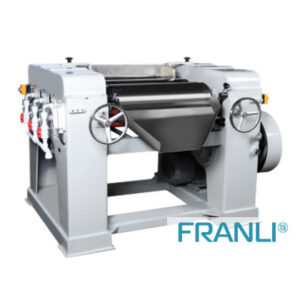
3 roll mill|Failure of the roll shaft & pulley
The 3 roll mill is a grinding and dispersing equipment, which plays an irreplaceable role in improving the quality of coating products.
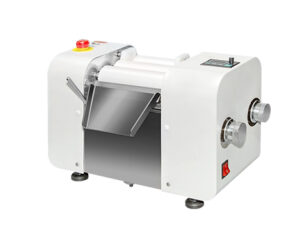
Precision Three Roll Mill – Laboratory Mill
FRANLI three roll mills have many types of styles, among which this precision laboratory three roll mill is more widely used in various fields.
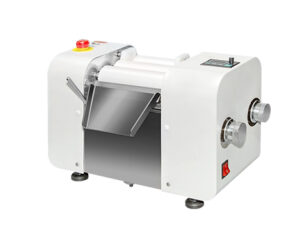
Three Roll Mill: Electronic Slurry Grinding Solution
FRANLI has various models of three roll mills, such as TRS, TRM, TRL, TRH, etc., which are suitable for grinding and dispersing various materials, and users can also customize them according to their own needs.
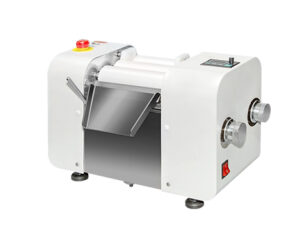
Ointment mill for paste material
FRANLI Ointment mills are used for dispersion of creams, ointment, gels, suspensions, and pastes as it specializes in particle size reduction for good absorption in the body.