Manual 3 roll mill
Franli designed and produced Lab Three Roll Mill for 20+ years. specialized in searching electronic pastes, ointment, pigment, cosmetic, solar pasty, etc.
Manual three roll mill is widely used in milling paste material including paint, inks, China ink, pigment, coatings, food, cosmetics, and so on. (Not applicable for roller corrosion material). It is also used in cable material, artificial plastics, soap, and pencil core material. It becomes the key equipment for those industries.
- High stability
- Easy operation
- Low noise, low energy consumption
Application

Coating

Cosmetic

Battery

Graphite

Agrochemistry

Adhesives
Frequently Asked Questions
The gap between fast, middle, and slow roller can be adjusted as customer products accuracy requirement, and then start the machine, feed the material between two copper blade and middle and slow roller. The material can be transferred to a fast roller after squeezed and rubbed between the middle and slow roller. The outlet blade which sticks tightly to the fast roller surface will collect the products and flow to the products tank via the outlet plate to form a milling cycling.
Operator who is responsible for this machine should be read this operation manual, and completely understanding, in case of making trouble. keep the warning and instructions marked clean, do not remove or cover them, Change a new part on time for the damaged warnings and instructions. Please do not dismantle or override the symbols on the electrical wiring code. Only in the protection device, which can Keep machine in safe condition , then start working. Before operation, please keep sure the emergency button is good, upon press”Emergency button”the main motor will be closed.
The machine is working only under the material on the rollers.
Upon hearing unusual voice, please stop and check on time.
Please keep the machine no working, then Maintain and cleaning.
Preparation before operation
Ø Set the roller in loosen condition, turn the belt wheel by hand, clean all the dirt on roller, feeding hopper and outlet blade.
Adjust hydraulic pressure(Start oil pump motor before start main motor)
Ø Checking “mixing” “milling”process, the closed roller pressure is 3Mpa, have a fibe tuning device P2 pressure switch to 2-3 mpa.
Ø Check and adjust baffle pressure to 1.2Mpa
Ø Check and adjust the blade pressure around 1Mpa. Normally it’s 0.6Mpa. Or pressure can be decided as material characteristics.
Ø The roller pressure shall set at 5Mpa or based on material characteristics. The roller pressure adjustment range is 1~5.5Mpa;
Ø Set the rotating valve HV at “Loosen” position after finish adjusting pressure, run the hydraulic system several hours, operate the rotating valve several times.
Main motor must keep still during all above operation.
Trial operation
Ø put material over than the level of ultrasonic, then star working
Ø Turn on water valve, pour enough cooling water into roller before first time operation. Set the temperature controller at 0℃.Cooling water will enter roller cavity after turn on water valve. Set the temperature as requested in temperature controller after mill operation.
Ø press “stop main motor”, operate main motor, checking roller pressure, if possible, please check again.
Ø put into mixed material, press “milling” to “milling”position. Check the roller tightening at same step. Further adjustment is possible by adjusting valve if necessary.
Ø When the mill set at “Tighten” position, outlet hopper oil tank will tighten automatically.
Ø here are material exudation at the both sides of roller when roller set at “Mixing” and “Tightening”, it means there is gap between roller shaft shoulder and baffle. Please adjust roller axial position. Adjust the part 5 and 6 in chart 15, so as to make the middle roller and slow roller shaft shoulder face in same surface, that will make hopper baffle fit well with roller shaft shoulder.
Ø Set the ink discharge state when the mill working(see chart) State 3 is best. Ink discharge adjustment is comprehensive, it’s not only related with roller pressure, but also with temperature, outlet hopper position and blade edge.
Ø Ultrasound probes is installed over the place of putting material,checking the material level, if the material level is lower than set level, the machine will be stopped, but there is some material on roller, please open by hand, upon finished material then close machine by hand, and keep separate position of rollers in case of working without material.
Hot sale three roll mill
Guidelines For Manual 3 roll mill
Three roller mill, with easy operating and safe cleaning. FRANLI nowadays has a different model of manual Triple Roller Mill, Hydraulic type, and Lab type. They have their advantages and features to meet different requirements.
We have different series of Three Roll Mill.
Franli manual three roll mill are widely sold all over the world, how about our manual three roll mill? Where we already sold out?
The roller material is made up of cold hard alloy centrifugal casting. The cold hard alloy thickness is between 15 and 25mm, hardness is between HS 68-75. The roller is grinding on a convex grinder, the effective working surface is a bit convex. During the milling process, because of hard roller and thermal expansion and contraction, it can compensate automatically to improve machine life, also improve the material accuracy and efficiency. For normal material, as its original fineness and hardness, it can be milled once, twice, and even more, times till it reaches requirement(Normally between 3 and 18 microns as gauge measured)
The machine is improved based on the same machine both in domestic and overseas markets and end-user production practice. It’s made up of good quality steel sheet welding to have nice looking, easy operation, lower labor strength, higher machine strength, and longer life.
The machine is equipped with the latest chain transmission technology in the international market. The gear is dipped inside lubricating oil to extend the machine life to the max. extent. It also reduces noise and energy consumption. The gasket part is imported. S series manual three roll mill is equipped with top adjusting roller structure, while SG series manual three roll mill is equipped with gear adjusting structure, easier and convenient and more stable operation. The water temperature display is available at both inlet and outlet to make sure the material temperature keep stable and good quality available. Cooling water recycling device or roller heating device are available as customer request. The material outlet hopper is made up of stainless steel. The machine is coated with solvent resistance paint to keep gloss.
We are focus on the grade of manual three roll mill gears, and the belt, also the motors. While if needs working smooth, no noise, and stable no moving, we have to check well the gears of manual three roll mill. We will put the gears outside to rust, then refresh to be heavy strong gears to affording the strength of driving. And our manual three roll mill is heavy cast iron of body, which make the machine more stable during operation.
Related production lines
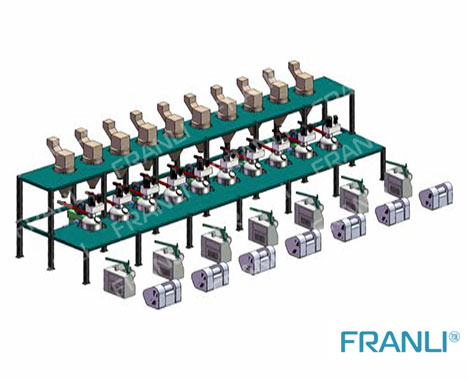
Offset Ink machine line
FRANLI is specialized in offset ink full line production for 20+ years. Helped customer save the cost, save the man power, also save the space.
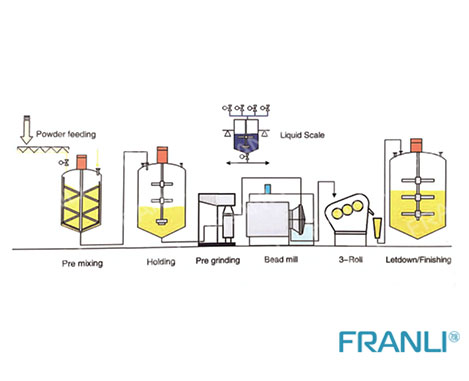
Offset Ink, UV Ink machine line
The FRANLI engineering company, offer the full set of UV INK Production Line, we can make the full drawing according with your factory size, formulas, weather and safety system.
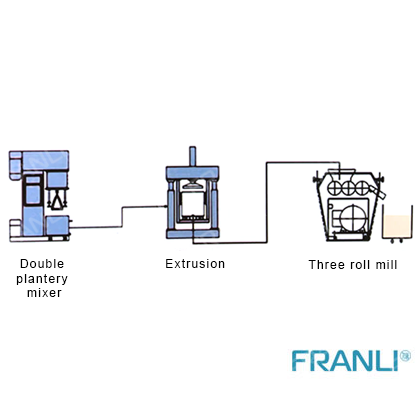
PCB INK Machine line
FRANLI supplies all equipments for the production of PCB inks, from the powder feeding station to the filling part.
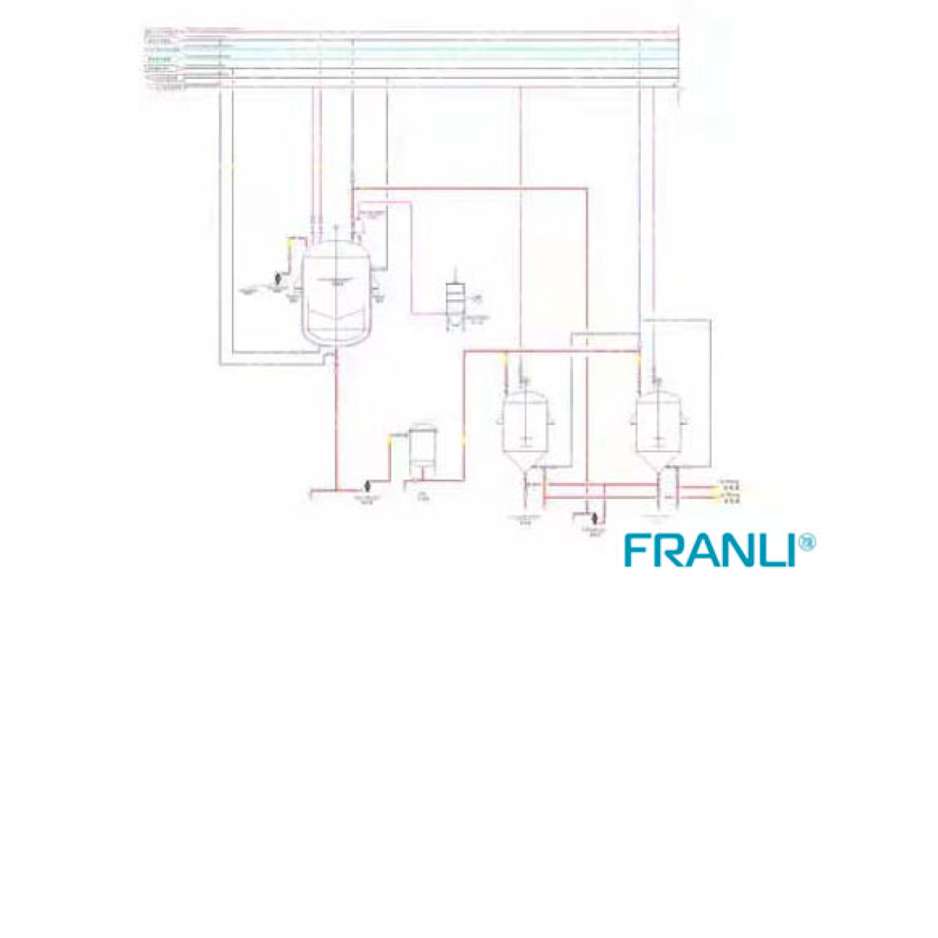
EW-pesticide line
The EW production line mainly mixes raw materials, solvents, and emulsifiers through a reactor (oil-based).
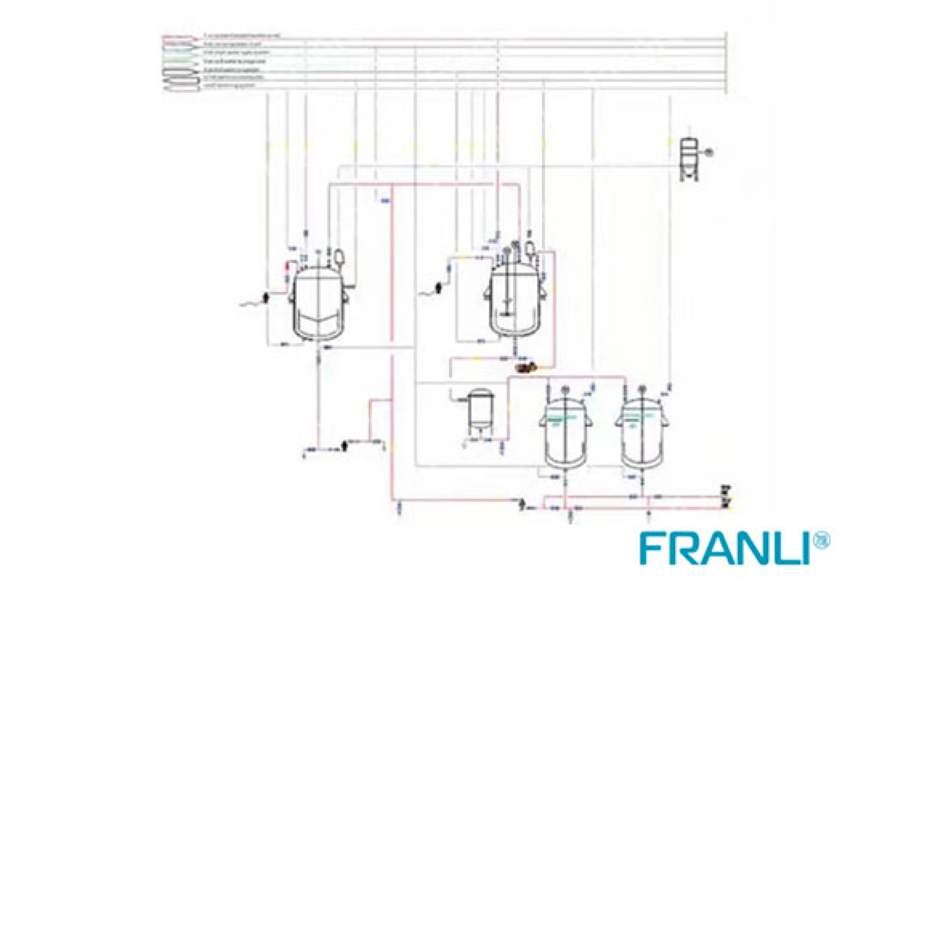
SL_EC pesticide line
The EC production line is mainly composed of an agitator mixer, bag filter, filling machine, etc.
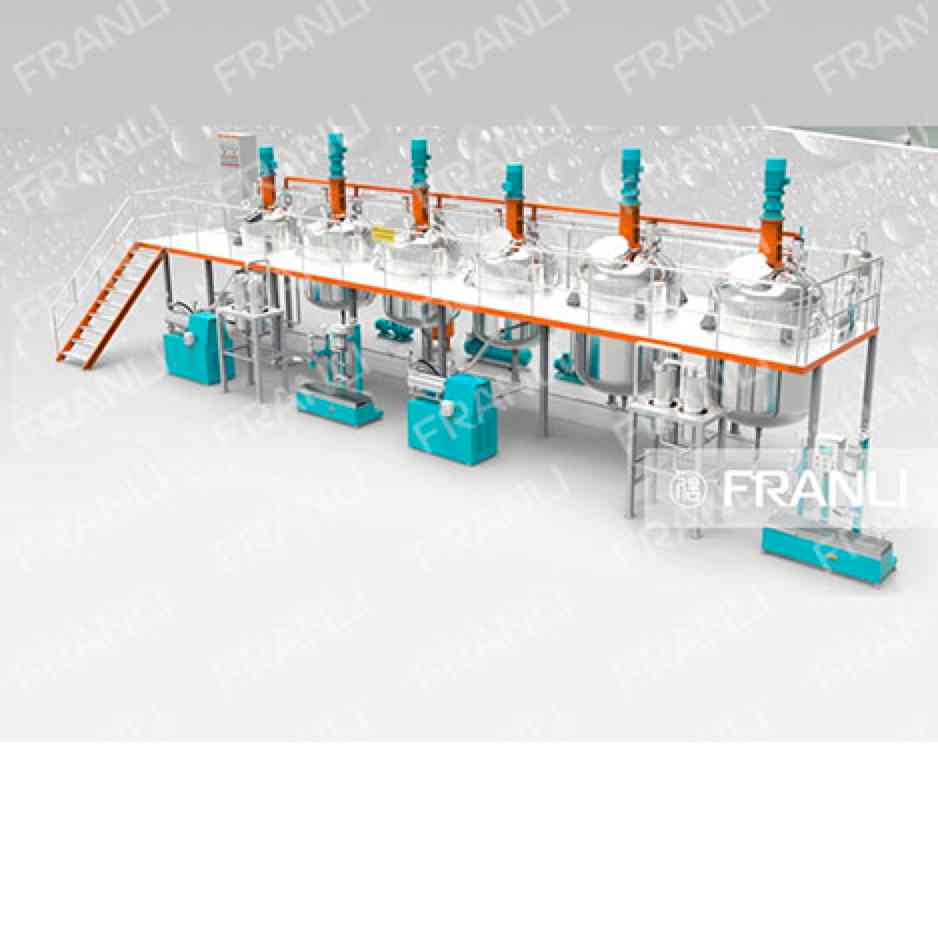
Automotive Paint machine line
The automotive paint machine line is mainly for the production and grinding of automotive paint, Automotive paint has many layers, such as Primer/electrophoretic layer, Medium coat, Colored coat, and Clearcoat.
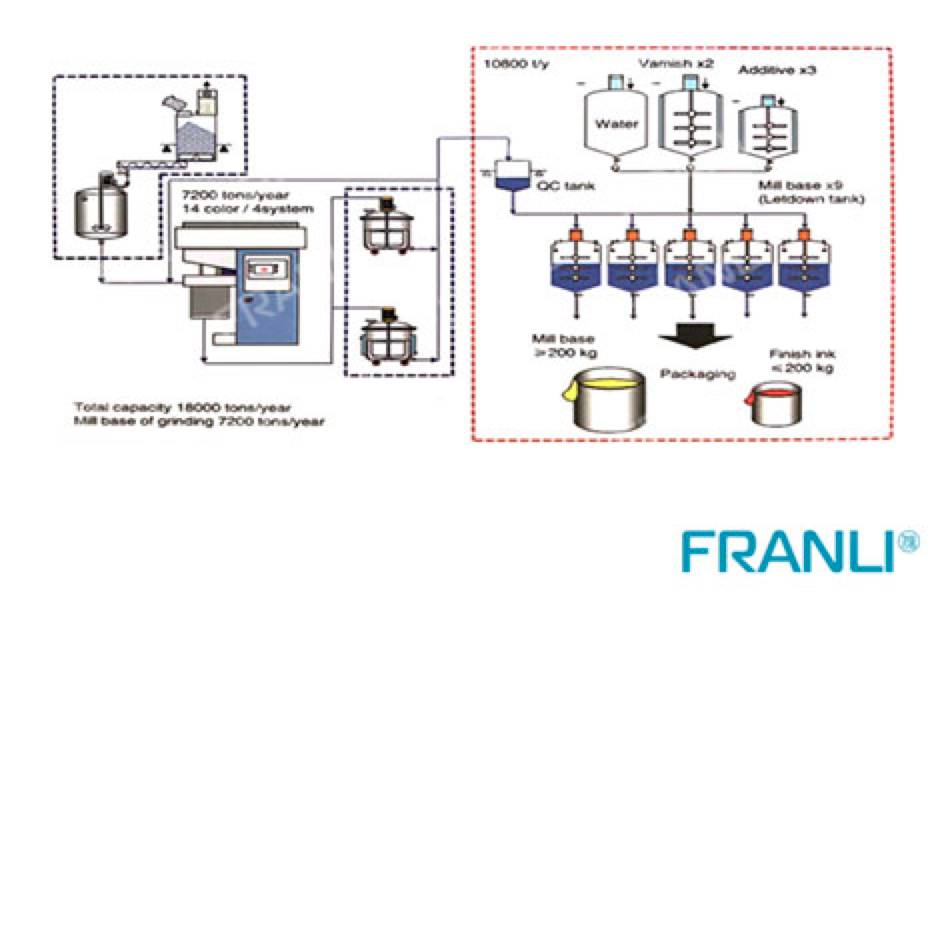
Digital Ink machine line
Franli has professional experience for digital ink machine line, we offered hundreds customers to expand production, or build up new project.