Home » Inline Static Mixers: A Comprehensive Product Overview
Inline Static Mixers: A Comprehensive Product Overview
Inline Static Mixer
Inline static mixers are the best devices that provide efficient and cost-effective mixing solutions for various industrial applications. These motionless mixers are designed to blend fluids within a pipeline without the need for moving parts or external power sources.
Application: Its application industries include chemical, petroleum, pharmaceutical, pesticide, food, plastic, daily chemicals, mining and metallurgy, papermaking, chemical fiber, cable, biology, environmental protection, etc.
Inline static mixers rely on the principle of dividing and radially redistributing the flow streams to achieve thorough mixing. As the fluid flows through the mixer, it encounters a series of specially designed mixing elements that create intricate flow patterns, promoting molecular diffusion and turbulence. This process results in homogeneous blending or dispersion of the fluids without the need for mechanical agitation.
The mixing elements within the static mixers are carefully engineered to optimize the mixing process based on the flow regime (laminar or turbulent), fluid properties, and desired mixing quality. The elements can be designed to induce various flow patterns, such as splitting, stretching, folding, and reorienting the fluid streams, ensuring efficient mixing in a compact space.
Types of Inline Static Mixers
Inline static mixers are available in various designs to cater to different application requirements. The most common types include:
1. Helical Mixers
Helical mixers, also known as spiral or twisted-tape mixers, consist of a series of helical elements that create a swirling motion within the fluid stream. These mixers are particularly effective for laminar flow regimes and viscous fluids, as they continuously divide and recombine the flow streams, promoting efficient mixing.
2. Blade Mixers
Blade mixers, or Kenics mixers, feature a series of alternating helical blades that create intricate flow patterns and promote radial mixing. These mixers are well-suited for turbulent flow regimes and are known for their high mixing efficiency and low-pressure drop.
3. Wafer Mixers
Wafer mixers, also known as plate mixers, consist of a series of flat, perforated plates arranged in a specific pattern within the pipeline. As the fluid flows through the perforations, it undergoes splitting, reorientation, and recombination, resulting in efficient mixing. These mixers are compact and suitable for space-constrained applications.
4. Injection Mixers
Injection mixers are designed to introduce and disperse a secondary fluid (liquid or gas) into the main fluid stream. They feature specialized injection ports or lances that direct the secondary fluid into the heart of the mixer, ensuring rapid and uniform dispersion.
5. Custom Mixers
In addition to the standard designs, inline static mixers can be customized to meet specific application requirements. This includes tailoring the mixer elements, materials of construction, and overall configuration to accommodate unique flow conditions, fluid properties, or installation constraints.
Advantages of Inline Static Mixers
Inline static mixers offer numerous advantages over traditional mixing methods, making them an attractive choice for various industrial applications:
1. No Moving Parts:
Static mixers have no moving parts, eliminating the need for mechanical agitation and reducing maintenance requirements.
2. Low Energy Consumption:
Since the mixing process is driven by the fluid flow itself, inline static mixers require minimal external energy input, resulting in significant energy savings.
3. Compact Design:
Static mixers can achieve efficient mixing in a relatively short length of pipe, making them space-efficient and suitable for installations with limited space.
4. Low-Pressure Drop:
Well-designed static mixers introduce minimal pressure drop, reducing energy costs associated with pumping.
5. Versatility:
Static mixers can handle a wide range of fluid types, viscosities, and flow rates, making them suitable for various applications across multiple industries.
6. Ease of Installation and Maintenance:
Static mixers are typically easy to install and require minimal maintenance, reducing downtime and associated costs.
7. Scalability:
Static mixers can be scaled up or down to accommodate different flow rates and pipe diameters, ensuring consistent mixing performance.
8. Sanitary Design:
Static mixers can be designed with sanitary features, such as smooth internal surfaces and crevice-free construction, making them suitable for applications in the food, beverage, and pharmaceutical industries.
Applications of Inline Static Mixers
Inline static mixers find applications in a wide range of industries due to their versatility and efficiency. Some of the key applications include:
1. Chemical Processing:
Static mixers are used for blending reactants, dispersing additives, and homogenizing mixtures in various chemical processes.
2. Water and Wastewater Treatment:
Static mixers are employed for chemical dosing, disinfection, flocculation, and ozonation in municipal and industrial water treatment facilities.
3. Food and Beverage:
Static mixers are used for blending ingredients, dispersing flavors, and homogenizing mixtures in the food and beverage industry.
4. Pharmaceutical and Biotechnology:
Static mixers are utilized for mixing and dispersing active ingredients, buffers, and reagents in pharmaceutical and biotechnology processes.
5. Polymer Processing:
Static mixers are employed for blending resins, dispersing additives, and homogenizing polymer melt in the plastics industry.
6. Petroleum and Gas:
Static mixers are used for mixing and blending various petroleum products, as well as for gas dispersion and injection applications.
7. Pulp and Paper:
Static mixers are utilized for mixing and dispersing chemicals, dyes, and additives in the pulp and paper industry.
8. Environmental Applications:
Static mixers are employed for mixing and dispersing chemicals in various environmental applications, such as soil remediation, air pollution control, and wastewater treatment.
Maintenance and Upkeep
One of the key advantages of inline static mixers is their low maintenance requirements. Since they have no moving parts, static mixers are virtually maintenance-free. However, periodic inspections and cleaning may be necessary to ensure optimal performance and prevent fouling or buildup.
Proper material selection is crucial to ensure compatibility with the fluids being mixed and to prevent corrosion or degradation. Common materials used for static mixers include stainless steel, plastics (such as PVDF, PP, and PEEK), and specialized alloys for highly corrosive environments.
In applications involving viscous or fouling fluids, static mixers may require more frequent cleaning or replacement of the mixing elements. Specialized cleaning procedures, such as chemical cleaning or pigging, may be employed to maintain the mixer’s efficiency.
The inline static mixers offer a reliable, efficient, and cost-effective mixing solution for a wide range of industrial applications. Their unique design, versatility, and low maintenance requirements make them an attractive choice for various mixing and dispersion processes.
Welcome to send inquiry to us and let’s make a win win business together !
Guidelines For Static Mixer
Static mixer is a new type of online, high-efficiency mixing equipment in the process. A static mixer is a high-efficiency mixing device without moving parts. Its basic working mechanism is to use the mixing unit fixed in the tube to change the flow state of the fluid in the tube, so as to achieve good dispersion and full mixing of different fluids.
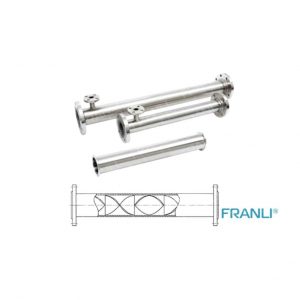
Inline Static Mixers: A Comprehensive Product Overview
Inline static mixers are the best devices that provide efficient and cost-effective mixing solutions for various industrial applications. These motionless mixers are designed to blend fluids within a pipeline without the need for moving parts or external power sources.
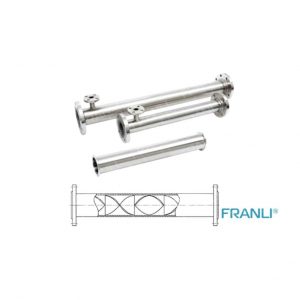
Inline Static Mixer: Application Range in Various Industries
The Inline Static Mixer is a device that mixes two or more streams of fluids or gases inside a pipeline without any moving parts. The device is usually a long pipe with carefully placed baffles that create turbulence to mix the fluids.
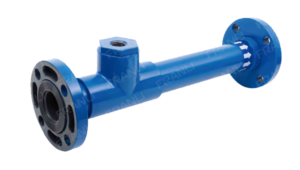
Application of Static Mixer Tubes in various industries
A Static Mixer Tube is an essential component in the process industry, with applications ranging from chemical processing to wastewater treatment.
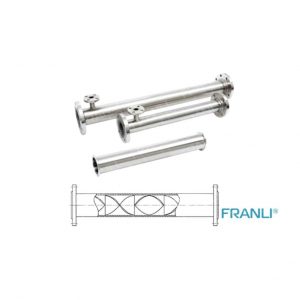
Static Mixer: The Solution for Efficient Mixing
A static mixer is a device that uses stationary blades or elements to mix fluids or gases. Unlike traditional mixers, static mixers do not have moving parts, such as agitators or impellers. Instead, they rely on the geometry and placement of the mixing elements to create turbulence and promote mixing. Static mixers come in various shapes and sizes, depending on the application and flow rate.