Best price sand mill from china
Sand Mill
Sand mill is a kind of high-efficiency grinding and dispersing equipment widely used in paint coatings, cosmetics, food, daily chemicals, dyes, inks, medicines, magnetic recording materials, ferrites, photosensitive films, and other industrial fields.
Application: Paint, Adhesive, Battery, Pharmaceutical industry, Cosmetic
Compared with grinding equipment such as ball mills, three roller mills, and colloid mills, the sand mill has the advantages of high production efficiency, strong continuity, low cost, and high product fineness. The process conditions vary greatly, and the fineness requirements can be adjusted by adding or subtracting grinding media in an appropriate amount.
A sand mill, also known as a bead mill, is mainly used for the wet grinding of chemical materials. According to its performance, it can be divided into a vertical sand mill, horizontal sand mill, basket sand mill, and rod sand mill. Wait. It is mainly composed of a machine body, grinding drum, disperser, bottom valve, motor, and feeding pump. The speed of feeding is controlled by the valve. The grinding media of this equipment are generally divided into glass beads, zirconia glass beads, zirconia beads, etc. Except for the vertical sand mill, which uses ordinary 2-3/3-4mm glass beads, other equipment uses 0.8-1.2mm glass beads. Zirconia beads. The feeding pump generally adopts a gear pump, diaphragm pump, and other thick slurry feeding pump.
How a sand mill works
A sand mill is a kind of ultra-fine particle dispersing machine for horizontal wet continuous production. The pre-stirred raw materials are sent to the grinding tank of the main machine, and the grinding tank is filled with an appropriate amount of grinding media, such as glass beads, which rotate at high speed through the dispersing blade, giving the grinding medium enough kinetic energy to collide with the dispersed particles to generate shear force. To achieve the effect of dispersion, and then through a special separation device, the dispersed material and the grinding media are separated and discharged. Because it does not require a high degree of operating skills like the three roller, it can obtain uniform and excellent quality, and it can be continuously produced in large quantities, so it can improve the quality and reduce the cost, and it can also be used for the dispersion of high-viscosity substances. Paint, ink, medicine, food, cosmetics, pesticides, and other industries can be applied.
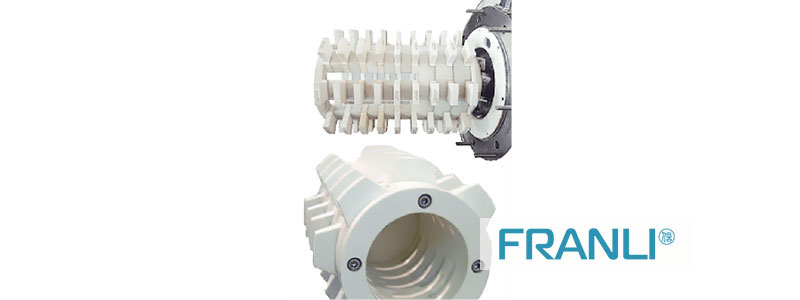
The purpose of dispersing is as follows
1. To achieve a flat surface and to micronize the solid particles dispersed in the liquid. Increase reflectivity, produce gloss, and improve hiding, such as paints, inks, color pastes, etc.
2. To improve the reaction rate and uniformity, the surface area of the particles suspended in the liquid is increased. Such as adding the granular hardener to resin, or powdery raw material in a chemical reaction.
3. To prolong the sedimentation time, the tiny particles suspended in the liquid can achieve the purpose of temporary suspension, such as water-suspended pesticides, which can increase the spreading area and prolong the efficacy, or fruit juices such as bacon juice.
Sand mill operation precautions
① if you park for a long time, check whether the dispersion disc is stuck by the medium before starting the machine. If the coupling does not turn, the solvent can be pumped into it. Start after dissolving. Do not start forcibly to avoid damaging the friction linings.
②if the machine is parked for a long time, check whether there is crusted paint slurry on the top screen before starting up the machine.
③once there is a “Falling roof”. Stop immediately to clean the screen, place the pulp receiving basin, adjust the speed of the pulp pump, and restart it. Otherwise, the paint slurry may penetrate the main shaft bearing and cause bearing wear, or damage the slurry pump.
④it is strictly forbidden to start when there is no paint and grinding medium in the simplified version.
⑤ when cleaning with solvent, only rotate the disperser slightly and intermittently to avoid the wear of parts.
⑥ when using new sand, it should be sieved to remove impurities and foreign matter. The sand used in the sand mill should be cleaned and screened regularly and new sand should be added.
⑦ the observation window should be kept in good condition to prevent accidents or injuries caused by sand collapse during the operation of the sand mill.
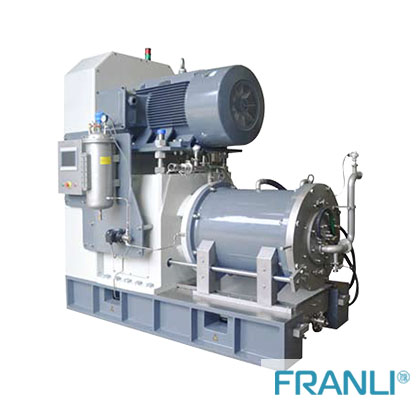
The latest development trend of sand mill
(1) advances in grinding media separation systems
With the continuous improvement of product fineness requirements, the size of the grinding media used is getting smaller and smaller. The separation of small-sized grinding media is one of the most difficult problems to solve in the development of sand mills. The gap ring (small flow area) and static screen used in traditional sand mills are difficult to separate small-sized media! Therefore, more and more dynamic centrifugal separation systems are used. The centrifugal force generated by the separation rotor driving the medium to rotate causes the medium to be thrown to the outer periphery of the rotor, and the center of the rotor is mainly slurry, and the separation screen is arranged in the center of the rotor, and the material will flow out through the screen gap smoothly, and will not flow out. Clogging and wear occur. Therefore, it is a technological leap in the history of sand mill development to apply the principle of dry air classification to the separation of sand mill media!
(2) high energy density pin-bar sand mill
In the past period, several major sand mill manufacturers at home and abroad believed that to improve the product fineness (reduce the particle size), the energy density of the sand mill must be increased! As a result, there have been many pin-bar sand mills with complex structures.
A: Sand mill dcp structure-1 has a lot of hard alloy pins densely arranged on the rotor and stator. The material enters from the top and is discharged from the bottom after going through the “N”-shaped route of twisting/collision. The wear of the medium on the pins, rotors, and stators is extremely serious, and the materials are often contaminated by metals. And only expensive zirconia grinding media can be used.
B: Sand mill dcp structure-2 is the same as structure-1, but to solve the problem of heat dissipation, a cooling jacket is set on the rotor.
C: Sand mill lmz only has pins arranged on the rotor, and cooling jackets are arranged on the stator and half rotors. The pin rod is very worn on the inner surface of the opposite stator, and metal contamination materials are inevitable!
(3) high energy density outer ring grinding area of horizontal centrifugal sand mill
After years of misguided and artificially complicated sand mill designs, people are finally back to basics! It is found that the real grinding of the material only occurs in the grinding area with a certain energy density, and the low-energy area only generates heat (playing lively). The high energy density region can only appear in the outer ring region with the largest linear velocity.
A: The r-sand mill feeds the material radially from the outer stator, and the material passing through the outer ring grinding zone is discharged axially through the dynamic medium separation screen.
B: Zr-the material of the sand mill enters the rotor through the side of the hollow shaft and reaches the outer annular grinding area. The drum (stator) of the equipment and the inner rotor rotate at different speeds. The medium separation screen (fixed on the drum) becomes a real rotary dynamic separator, and the complex double rotor structure has extremely high requirements on the coaxiality error of each rotating body.
C: Sc- the material of the sand mill is added from the axial center and reaches the outer ring grinding area, and the ground material is discharged through the outer ring screen ring. The grinding track is also the ceramic separating ring. Although the filter area is increased, the separation ring is severely worn and easily blocked.
Welcome to send inquiry to us and let’s make a win win business together !
Guidelines For Sand Mill
The sand mill mainly uses friction, shearing, and collision as effective grinding methods. It is one of the grinding equipment currently applicable to a wide range of material particle sizes and has high grinding efficiency. The energy density per unit volume is large. The control system can complete the continuous grinding and continuous discharging of the slurry, which greatly improves the production efficiency of the sand mill. It has the advantages of high energy density, fine product granularity, small environmental pollution, simple equipment structure, and convenient maintenance.
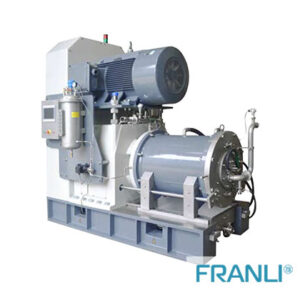
Sand Mill: Enhancing the Efficiency of Grinding & Dispersion
Sand mills, also known as bead mills or media mills, are mechanical devices used in the field of grinding and dispersion.
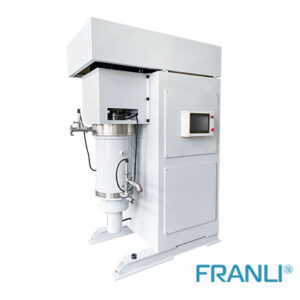
Instructions for use of vertical sand mill
The vertical sand mill is a nano-sand mill whose grinding cylinder adopts a suspended structure, raw materials enter from the bottom and discharge from the top.
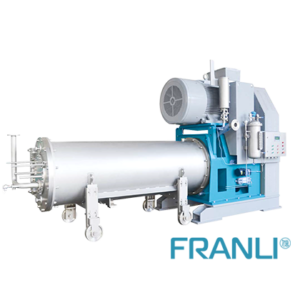
How to choose the right vertical sand mill & horizontal sand mill?
Vertical sand mills and horizontal sand mills are commonly used equipment for grinding in paint, coating, ink, and other industries. They all rely on the high-speed rotation between the grinding medium and the material for grinding work.
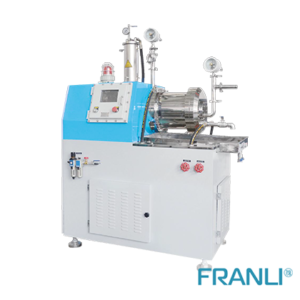
How to deal with the problem of sand mill?
The sand grinding machine, also known as the pearl grinding machine, is used to grind the paint of the pigment with hard wear -resistant beads, glass balls, etc. in a closed cavity.
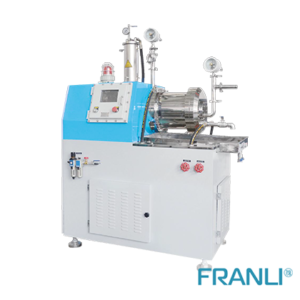
How to choose a sand mill for paint?
Sand mills are mainly used in industrial fields such as paint coatings, cosmetics, food, daily chemicals, dyes, inks, pharmaceuticals, magnetic recording materials, ferrites, photosensitive films, oxide ceramics, and new energy.
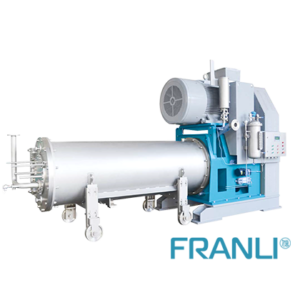
Grinding media for sand mills
Sand mill is a kind of high-efficiency grinding equipment, which is mainly used for grinding materials, and the particle size of the final grinding can reach the nanometer level.