Home » Ribbon Blender Mixer: The Right Choice for a High-Quality Blender
Ribbon Blender Mixer: The Right Choice for a High-Quality Blender
Ribbon Blender Mixer
Ribbon blender mixers are widely used in various industries for blending dry powders and granules. They consist of a U-shaped trough with a horizontal agitator consisting of inner and outer helical ribbons that rotate at different speeds. This unique design creates a fluidized mixing action that ensures thorough blending of materials within the mixing chamber.
Advantages of Ribbon Blender
- fast and efficient
- safe and stable
Application: chemical, pesticide, dye, medicine, feed, fertilizer, metallurgy, mining, food, plastic, additives, and other industries.
In the world of industrial mixing, ribbon blender mixers have gained immense popularity for their versatility, efficiency, and effectiveness in blending powders, granules, and other solid materials. Whether you are in food processing, pharmaceutical, chemical, or any other industry that requires homogeneous mixing, choosing the right ribbon blender mixer is crucial for achieving consistent and high-quality results.
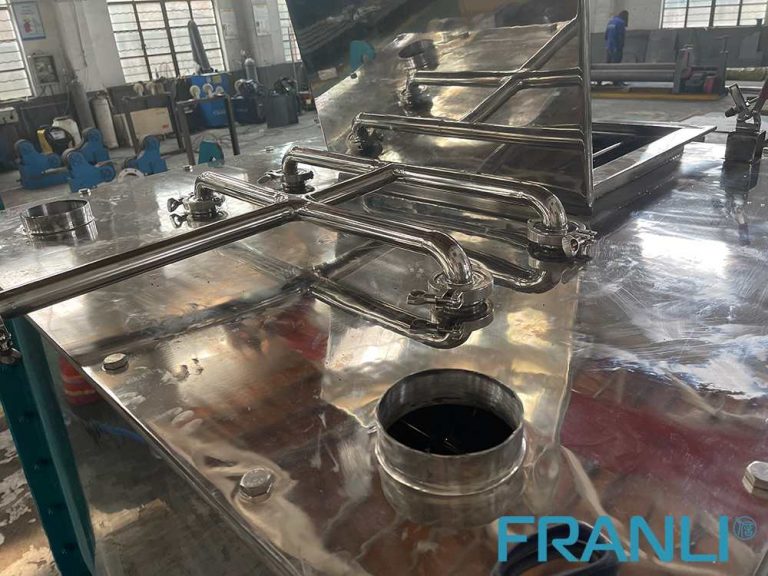
Understanding Ribbon Blender Mixers
Ribbon blender mixers, also known as ribbon mixers or ribbon blenders, are horizontal mixing devices characterized by their unique ribbon-shaped agitators. These agitators consist of inner and outer helical ribbons that rotate in opposite directions, creating a gentle and efficient mixing action. The design of the ribbons ensures the thorough blending of ingredients, eliminating dead spots and producing a homogeneous mixture.
Considerations before Choosing a Ribbon Blender Mixer
1. Blending Capacity: Assess your production requirements to determine the necessary blending capacity. Ribbon blender mixers are available in a wide range of sizes, from small laboratory-scale models to large industrial-scale units capable of handling several tons of materials.
2. Material Characteristics: Consider the physical and chemical properties of the materials you intend to blend. Factors such as particle size, density, flowability, and abrasive nature can influence the design and specifications of the ribbon blender mixer, ensuring optimal blending performance and minimizing equipment wear.
3. Mixing Time and Efficiency: Evaluate the desired mixing time and efficiency. Ribbon blender mixers offer different mixing intensities, ranging from gentle blending to high shear mixing. Understanding your product’s mixing requirements will help you select a blender with the appropriate agitation speed, power, and shear capabilities.
4. Hygiene and Safety: In industries such as food processing and pharmaceuticals, strict hygiene and safety standards must be met. Ensure that the ribbon blender mixer is designed with easy cleaning and sanitation in mind, featuring smooth surfaces, removable parts, and suitable sealing mechanisms to prevent cross-contamination.
5. Customization Options: Some applications may require additional features or customization to meet specific needs. Consider whether the ribbon blender mixer can be modified to accommodate specialized requirements such as heating, cooling, vacuum operation, or the inclusion of liquid additives.
Performance and Design Features
1. Construction Materials: Ribbon blender mixers are typically constructed using stainless steel, which offers excellent durability, corrosion resistance, and easy cleanability. However, certain applications may require alternative materials such as carbon steel or exotic alloys.
2. Drive Systems: Evaluate the available drive systems, which can vary from direct drive to belt or chain-driven mechanisms. Each system has its advantages and considerations regarding maintenance, efficiency, and noise levels.
3. Mixing Chamber Design: Consider the shape and dimensions of the mixing chamber. Options include U-shaped, tubular, or cylindrical chambers, each offering different benefits in terms of material movement, discharge efficiency, and ease of cleaning.
4. Safety Features: Pay attention to safety features such as emergency stop buttons, interlocking mechanisms, guarding, and overload protection systems. These features ensure the safe operation of the ribbon blender mixer and protect operators from potential hazards.
After-sales Support and Maintenance
1. Supplier Reputation: Research the reputation and track record of the equipment supplier or manufacturer. Look for companies with a history of providing reliable products, excellent customer service, and readily available spare parts.
2. Maintenance Requirements: Understand the maintenance requirements of the ribbon blender mixer, including routine cleaning, lubrication, and replacement of wearing parts. Easy access to components and clear maintenance guidelines can prolong the equipment’s lifespan and optimize its performance.
3. Technical Support: Assess the availability of technical support and after-sales service, including troubleshooting assistance, spare parts availability, and equipment upgrades. Prompt and reliable support ensures minimal downtime and maximizes productivity.
Choosing the right ribbon blender mixer is paramount to achieving efficient and consistent mixing results in various industrial applications. By considering factors such as blending capacity, material characteristics, mixing time, hygiene, customization options, construction, drive systems, safety features, supplier reputation, and after-sales support, you can make an informed decision that meets your specific blending needs. Remember to prioritize quality, reliability, and performance to ensure a successful blending process and enhance productivity in your operations.
Welcome to send inquiry to us and let’s make a win win business together !
Guidelines For Ribbon blender
Ribbon blenders are essential equipment in various industries where the quality and consistency of the final product are critical factors. They are highly efficient, customizable, and reliable mixing solutions that offer unsurpassed performance and versatility. By integrating a ribbon blender into your production line, you can ensure consistent and reliable product quality, increased productivity, and reduced manufacturing costs.
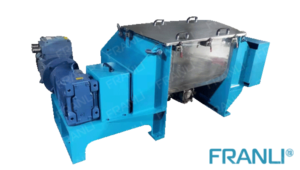
Ribbon Blender Mixer Equipment
A ribbon blender mixer, also known as a ribbon mixer or horizontal ribbon blender, is a powerful industrial machine designed for thorough and efficient blending of various materials.
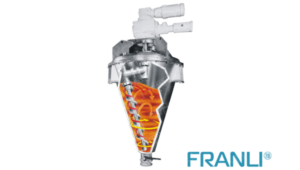
Ribbon Blender Mixer: The Right Choice for a High-Quality Blender
Ribbon blender mixers, also known as ribbon mixers or ribbon blenders, are horizontal mixing devices characterized by their unique ribbon-shaped agitators.
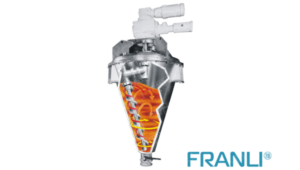
Vertical Ribbon Blender: Efficient mixing equipment for solids and powders
A vertical ribbon blender, also known as a vertical mixer, is a type of mixing machine widely used in various industries for the homogeneous blending of dry, free-flowing solids.
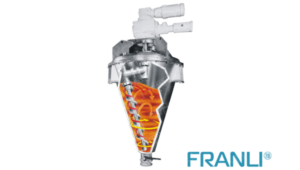
Powder Ribbon Mixer: Whirling Agitator and Horizontal U-shaped Housing
A powder ribbon mixer, also known as a ribbon blender, is a versatile and widely used machine for combining different powders, powder with liquid, powder with granules, and dry solids.
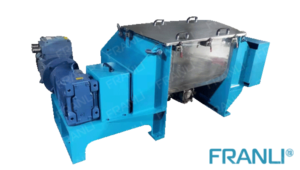
Small Ribbon Blender: A Versatile and Efficient Processing Equipment
The small ribbon blender is a versatile and efficient processing equipment used in the food, pharmaceutical, and cosmetic industries for blending, mixing, and uniformizing various types of materials.
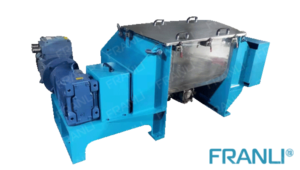
What is A Small Ribbon Blender?
The small ribbon blender is a versatile and efficient machine used for the mixing of various materials such as powders, pastes, and dried granules.