Home » Resin Production Line & Complete Manufacturing Equipment
Resin Production Line & Complete Manufacturing Equipment
Resin Production Line
The PLC system can realize functions such as self-storage, thermal insulation of the storage tank, liquid level monitoring, and automatic discharge, and the input and output of the chemical reactor can be automatically batched and transported. Through the metering tank matched with FRANLI, the material is metered and transported to enter the chemical reaction. After the synthesis reaction is completed, the final product is controlled by PLC and transported to the filling workshop for packaging.
In the production of resin, the most used equipment is the chemical reactor, and the resin reactor can be divided into high-temperature resin reactors (150°C-300°C) according to the reaction temperature. ℃) and low-temperature resin reactor (60℃-150℃). The whole set of equipment of the resin production line includes a high tank, reaction kettle, dilution tank, oil-water separator, condenser (vertical horizontal), vertical fractionation column, heat transfer oil system, steam system, water circulation system, oil overflow tank, or electric It is composed of many original parts such as heaters, and its feeding and discharging, temperature adjustment can be automatically controlled through the PLC control system.
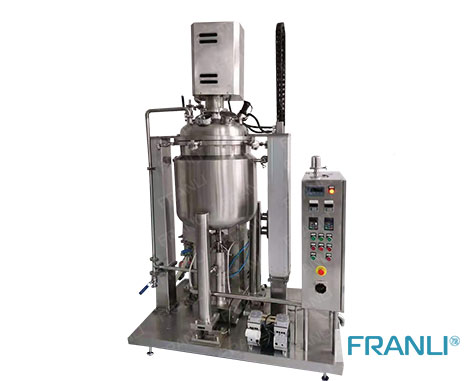
For this type of production line, we generally use non-standard customized forms according to the process requirements. Among them, the structure of the reactor can be selected from various types, such as coils or jackets for heating and cooling, and can also be equipped with inner coils for heating and cooling. However, this kind of inner coil is difficult to clean, and the resin solidifies and scales seriously, so it is generally not recommended.
After years of experience accumulation, FRANLI engineers design the heat source of the chemical reactor according to the process requirements. If it exceeds 140°C, heat conduction oil can be used to raise and lower the temperature. When it is between 80-140°C, steam can be selected. When it is below 80°C, steam and heat can be used. Two kinds of water can be selected, and users can also choose matching electric heating and infrared heating according to their own needs. To meet the convenience and safety of users, temperature control can be realized by PLC, temperature sensors, automatic regulating valves, and many other components, which have the characteristics of accuracy, convenience, and stable system.
For the stirring anchor of the chemical reactor, the most suitable one can be selected according to the process requirements. The common forms include anchor type, paddle type, pusher type, frame type, etc., and it can also be equipped with a two-stage reducer to reduce or an Acceleration and deceleration machine for frequency conversion speed regulation.
The manufacturing process of the resin production line
Resin synthesis is a process in which monomers are added to various additives in a reactor, and then heated, stirred, and shaken for the final synthesis reaction. The most critical part is the temperature control and the addition of additives. (drop reaction)!
The production line we design and recommend has two configurations: automatic production and manual control production:
1. Ingredients unit
The addition of monomer components is transported into the high-level tank, measured by a weighing scale or flow meter, and then input into the reactor;
Solvent, water, etc. are added through weighing measurement or flow meter measurement;
The powder is automatically conveyed or manually added, weighed, and measured by the metering bin, the proportion is determined, and then added to the reactor;
Small metered raw materials such as additives pass through the high-level tank, and the feeding speed is controlled by a dripping pump and a flow meter;
FRANLI water ink automatic production line
1. The batching unit of the production line
The batching unit is mainly carried out in four aspects, including resin, solvent, powder, and additives.
(1) The storage of resin is measured by liquid level gauge, and the addition is measured by weighing or flow meter;
(2) The storage of solvent is measured by liquid level gauge, and the addition is measured by weighing or flow meter;
(3) The storage level gauge of the powder is measured, conveyed by pneumatic force, screw, or pipe chain, and weighed and measured by the metering bin to determine the proportion;
(4) Small-scale raw materials such as additives are completed manually or by small-scale delivery units;
2. Production unit
The user needs to set the required temperature on the industrial computer or touch screen before production, and the PLC also receives signals such as temperature and pressure sensors, and can also control the pump valve to adjust the temperature change, or the user can also according to the synthesis reaction effect, carry out The temperature of the reaction was gradually adjusted. The condenser needs to recover the components in the waste gas, so we can eliminate the air bubbles and discharge the waste gas through the vacuum.
Once the material synthesis reaction is completed, the material can be sent into the dilution kettle, and then still needs to add solvents, additives, etc. to stir and adjust the finished product. The finished resin is filtered and transported to the storage tank of the finished product for storage, and can also be transported to the filling machine station for filling;
Equipment parameters of the production line
Through our experiments and factory usage statistics, the conventional production line can meet the design output of more than 1,000 tons, and then provide different configurations according to the process and output. The functions of the resin production line include the whole process of automatic feeding, automatic production, automatic filling, and so on (manual intervention in the detection part).
As for the temperature control in the production process, it can generally be adjusted automatically, and it can also be used with PLC to control heat source pumps, regulating valves and other equipment to visually adjust the temperature rise and fall.
The equipment is completely designed according to the production process, which minimizes human factors and facilitates production management. The materials of the equipment include 304 and 316 materials, which can be manufactured according to requirements. The interior of the kettle body is mirror-polished, and the discharge is clean and easy to clean; the on-site operation is equipped with a control box ( Explosion-proof and non-explosion-proof), MCC cabinet, and PLC cabinet.
There are many classifications according to the preparation method, examples are as follows:
(1) Self-emulsification method and external emulsification method
The self-emulsification method, also known as the internal emulsification method, refers to a method in which the polyurethane segment contains hydrophilic components so that a stable emulsion can be formed without an emulsifier. The external emulsification method is also called the forced emulsification method. If the molecular chain contains only a small amount of hydrophilic segments or groups that are not sufficient for self-emulsification or do not contain hydrophilic components at all, an emulsifier must be added to obtain an emulsion.
In comparison, in the emulsion prepared by the external emulsification method, the residual hydrophilic small molecule emulsifier affects the performance of the cured polyurethane film, while the self-emulsification method eliminates this disadvantage. The preparation of waterborne polyurethane is mainly based on the ionic self-emulsification method.
(2) Prepolymer method, acetone method, melt dispersion method
The most commonly used methods for preparing waterborne polyurethane by self-emulsification are the prepolymer dispersion method and the acetone method. The prepolymer method is to introduce hydrophilic components into the prepolymer to obtain a prepolymer with a certain viscosity range, emulsify in water and carry out chain growth at the same time, and prepare stable water-based polyurethane (water-based polyurethane-urea).
The acetone method belongs to the solution method, which is a method of diluting or dissolving polyurethane (or prepolymer) with an organic solvent, and then emulsifying it. In the presence of a solvent, the prepolymer and the hydrophilic chain extender undergo a chain extension reaction to generate a higher molecular weight polyurethane. During the reaction process, a solvent can be added to reduce the viscosity of the polyurethane solution to make it easy to stir, and then add water to disperse, form an emulsion, and finally evaporate the solvent. Most of the solvents are acetone and methyl ethyl ketone, so it is called the acetone method.
The advantages of the acetone method are that acetone and methyl ethyl ketone have low boiling points, are compatible with water, are easy to recycle, and the whole system is uniform and easy to operate. Because the viscosity is reduced and the concentration is also reduced, it is beneficial to prepare high molecular weight prepolymers before emulsification Or polyurethane resin, the film performance of the obtained emulsion is better than that of the simple prepolymer method. Due to the limitation of the viscosity of the prepolymer method, to facilitate shear dispersion, the molecular weight of the prepolymer should not be too high, which may affect the performance of waterborne polyurethane. For example, if the viscosity is high, emulsification is difficult, the particle size is large, and the emulsion stability is poor; The smaller the molecular weight, the higher the NCO group content, and the more urea bonds formed after emulsification, the hard film and lack of flexibility.
The main difference between the acetone method and the prepolymer method is that in the acetone method, the polyurethane is pre-polymerized into a prepolymer with a larger molecular weight. Because the prepolymer with a large molecular weight has a high viscosity, it must be diluted to reduce the viscosity; while in the prepolymer method, A small number of solvents such as acetone can be added or not added as needed. The concepts of the two are intersected, and some emulsification methods are both the acetone method and the prepolymer method.
The melt dispersion method is also called the melt dispersion method and the prepolymer dispersion formaldehyde chain extension method. Pre-synthesize the NCO group-terminated prepolymer containing tertiary amine groups (or ionic groups), and then react with urea (or ammonia water) in the bulk system to form polyurethane biuret (or urea-terminated urea groups containing ionic groups) ) oligomer, and add chlorpropamide to continue the reaction in a high-temperature molten state to continue quaternization. Polyurethane biuret ionomer has sufficient hydrophilicity, and dilute aqueous solution with acid is added to form a homogeneous solution, and then reacts with formaldehyde aqueous solution to carry out methylation. Polyurethane biuret containing methylol can be Diluted with infinite water at 130°C to form a stable emulsion. When the pu value of the system is reduced, the polycondensation reaction can be carried out in the dispersed phase to form high molecular-weight polyurethane. After the ionic group-terminated NCO prepolymer forms a urea-terminated or biuret-based polyurethane oligomer, it is directly emulsified in water in a molten state, and then added with formaldehyde aqueous solution for methylation and chain extension reactions.
(3) Direct chain extension of diamines and ketimine-ketazine method
In the prepolymer dispersion method, if a water-soluble binary primary amine chain extender is used for chain extension, due to the fast reaction speed of -NCO and -NH2, it is difficult to obtain a fine and uniform emulsion, and ketimine or ketone can be used The azine method solves this problem. The ketimine-ketazine method means that the prepolymer is mixed with the diamine (ketimine system) or hydrazine (ketazine system) protected by ketone, and then dispersed with water. During the dispersion process, the ketimine, Ketazine is hydrolyzed at a certain rate, releasing free diamine or hydrazine to react with dispersed polymer particles, and the obtained water-based polyurethane-urea has good performance.
FRANLI is a water ink production line manufacturer, and we design the production ink production line, ink production complete sets of equipment, including a high-speed disperser, temperature-controlled stainless steel reactor, bead mill, filter, filling machine, three-roll mills, supporting workbenches, integrated control systems and other complete sets of equipment have been exported to Russia, Turkey, Egypt, Brazil, Malaysia, Indonesia, Spain, etc.
Welcome to send inquiry to us and let’s make a win win business together !
Guidelines For production line
FRANLI has several sets of wet grinding production lines, including PCB ink production line, ink production line, pesticide production line, automobile coating production line, etc.
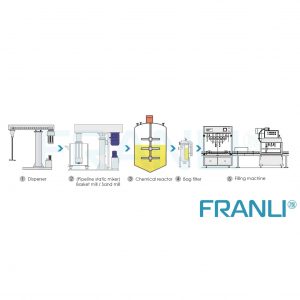
Pesticide Production Line
The production of pesticides mainly uses sand mills, emulsifiers, chemical reaction kettles, twin-shaft mixers, filling machines, and other equipment. This equipment thus constitutes a complete set of pesticide production lines, from the grinding and storage of particles to the reaction and Blending, and finally filling and packaging, the FRANLI pesticide production line is fully intelligent, with the characteristics of simple operation, safety, and stability.
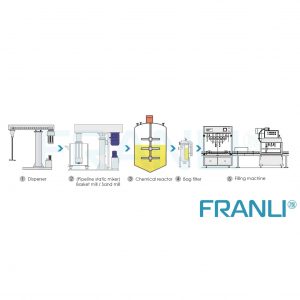
Gravure Ink Production Line: manufacturing process
The gravure ink production line is a professional manufacturing process that requires attention to detail and a commitment to quality.
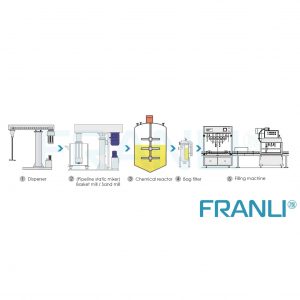
Printing ink production line
FRANLI Printing ink production line mainly takes intelligence, environmental protection, and high production efficiency as the main production standards.
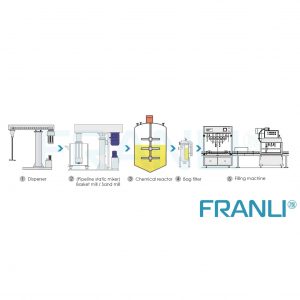
Water Ink Make equipment & production line
FRANLI water ink complete set of equipment and production line is mainly composed of an intelligent batching system, high-speed dispersion pulping system, metering system, horizontal grinding series system, multi-functional mixing and coloring system, cleaning system, automatic control system, automatic filling system, and other parts. Advanced production technology.
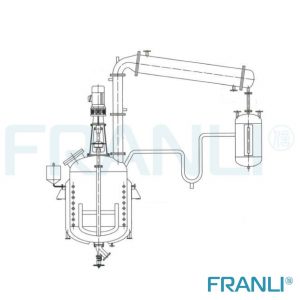
Resin Production Line & Complete Manufacturing Equipment
FRANLI provides complete sets of resin manufacturing equipment and production lines, which are mainly suitable for the synthesis of various chemical resins, such as unsaturated polyester resin, phenolic resin, epoxy resin, alkyd resin, ABS resin, etc. It can also be used for the manufacturing and production of Various types of emulsion resins, such as acrylic resin emulsion, etc.
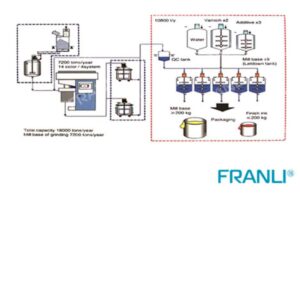
Ink production line
The main equipment of the ink production line includes material storage tanks, barrels, multi-model dispersing machines, chemical reactors, sand mills, three-roll mills, material operating platforms, filling machines, electronic process control systems, process pipelines, air compressors, A set of equipment such as cleaning equipment.