Home » Pneumatic Mixer: Enhancing Efficiency & Productivity in Mixing Processes
Pneumatic Mixer: Enhancing Efficiency & Productivity in Mixing Processes
Pneumatic Mixers
A pneumatic mixer, also known as an air-driven mixer or air-powered mixer, is a type of mixer that utilizes compressed air to drive its mixing action. The primary components of a pneumatic mixer include an air motor, an impeller, and a mixing vessel. The air motor converts the energy from compressed air into mechanical motion, which in turn drives the impeller to agitate the liquid or powder mixture in the vessel.
Details of Pneumatic Mixers
- The pneumatic mixer can be adjusted steplessly.
- The pneumatic mixer can rotate forward and reverse.
- The working environment of the pneumatic mixer is not affected by vibration, high temperature, electromagnetic, radiation, etc.
- The air motor matched with the air mixer has the function of overload protection, and will not fail due to overload.
- The pneumatic mixer has a high starting torque and can be started directly with a load.
- The pneumatic mixer is easy to operate and easy to maintain and repair.
Application: petroleum, chemical, paint, paint, woodworking, food, daily chemical, and other flammable, dusty, heavy-duty, wet, and other industries.
In various industries such as chemical manufacturing, pharmaceuticals, food processing, and water treatment, the mixing of liquids or powders is a critical step in the production process. Achieving a homogeneous mixture is essential to ensure product quality, consistency, and efficiency. One technology that has revolutionized the mixing processes is the pneumatic mixer.
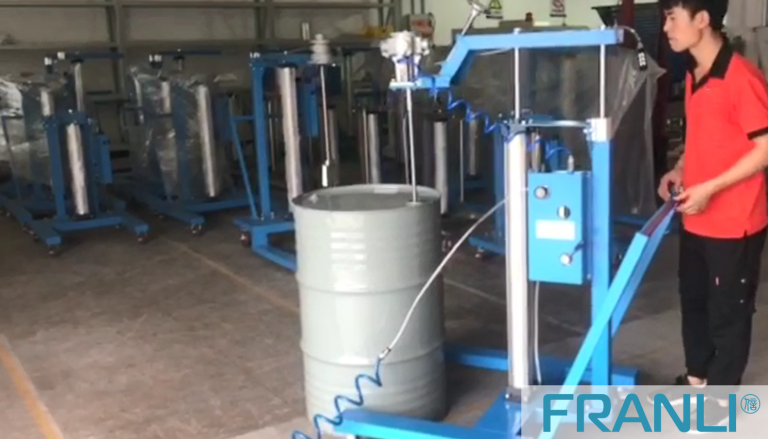
Advantages of pneumatic mixers
1. Versatility and flexibility: Pneumatic mixers are highly versatile and can be used for various types and sizes of mixing applications. With interchangeable impellers and adjustable speed controls, these mixers can handle a wide range of viscosities, from low to high. This versatility allows for efficient mixing across different industries and applications.
2. Safety: Pneumatic mixers are considered safer than their electric counterparts, especially in hazardous environments. Since they do not generate sparks or have exposed electrical components, the risk of explosions or fires is significantly reduced. This makes pneumatic mixers an ideal choice for industries dealing with flammable materials or operating in potentially explosive atmospheres.
3. Easy maintenance: Pneumatic mixers have simple and robust designs, consisting of fewer moving parts compared to electric mixers. This simplifies their maintenance and reduces downtime, thereby increasing overall productivity. Additionally, due to the absence of electrical components, the risk of malfunctions associated with moisture, heat, or vibration is minimized.
Applications of pneumatic mixers
4. Water treatment: Pneumatic mixers play a key role in water treatment plants for mixing chemicals used in coagulation, flocculation, and pH adjustment processes. The efficient and homogeneous blending of chemicals allows for effective water purification, removing contaminants and impurities.
3. Food processing: In the food industry, pneumatic mixers are employed for batch mixing of ingredients, emulsifying liquids, and blending powders. From sauces and dressings to beverages and confectionery products, pneumatic mixers ensure uniform distribution of ingredients, resulting in consistent taste, texture, and quality.
2. Pharmaceuticals: In the pharmaceutical industry, precise and controlled mixing is crucial for producing drugs with the desired efficacy and uniformity. Pneumatic mixers are utilized for blending active pharmaceutical ingredients (APIs), excipients, and other additives. Their versatility allows for efficient mixing of even the most delicate and shear-sensitive pharmaceutical materials.
1. Chemical manufacturing: Pneumatic mixers are widely used in the chemical industry to ensure consistent blending of various chemicals and solvents. From small-scale laboratory applications to large-scale production, pneumatic mixers offer the flexibility to meet the specific mixing requirements of different chemical processes.
Enhancing efficiency and productivity
1. Faster mixing times: Pneumatic mixers offer rapid mixing capabilities due to their high power-to-weight ratio. The powerful air-driven motor and specially designed impellers generate intense agitation that speeds up the mixing process. This translates into shorter cycle times, higher throughput, and increased overall productivity.
2. Improved mixing quality: Pneumatic mixers ensure efficient and thorough mixing, resulting in homogeneous blends with consistent properties. The high-speed impeller creates turbulence and a strong mixing action, breaking up clumps and distributing particles uniformly. This eliminates the need for manual intervention, reduces the risk of human errors, and improves the overall product quality.
3. Energy efficiency: Compared to electric mixers, pneumatic mixers consume less energy. The compressed air used to drive the mixer is readily available in many industrial settings and can be harnessed efficiently. This not only reduces energy costs but also contributes to a more sustainable and environmentally friendly production process.
4. Easy scalability: Pneumatic mixers offer flexibility in scale-up operations. Whether it is a small-scale laboratory experiment or a large-scale production process, pneumatic mixers can be easily adapted to different vessel sizes. This scalability allows for seamless transitions between different production stages, ensuring consistent mixing performance and efficient operations.
Pneumatic mixers have revolutionized the mixing processes in various industries by providing efficiency, versatility, and safety. These air-driven mixers offer significant advantages such as faster mixing times, improved mixing quality, energy efficiency, and easy scalability. Their applications span across chemical manufacturing, pharmaceuticals, food processing, and water treatment, contributing to enhanced productivity and consistent product quality. With ongoing advancements in technology, pneumatic mixers continue to be an indispensable tool for achieving optimal mixing results in countless industrial processes.
As a professional Pneumatic mixer, FRANLI has provided a complete set of mature equipment for related machines and production lines for more than 60 countries and thousands of industries in the world, and in Russia, Turkey, Spain, Brazil, Malaysia, Indonesia, and other regions, it has provided many An enterprise establishes related production lines.
Welcome to send inquiry to us and let’s make a win win business together !
Guidelines For Pneumatic Mixers
The stirring process of the pneumatic mixer is a single momentum transfer in the fluid field or a process including momentum, heat, mass transfer and chemical reaction. The agitator mainly inputs the energy of the device by making the stirring medium obtain a suitable flow field device.
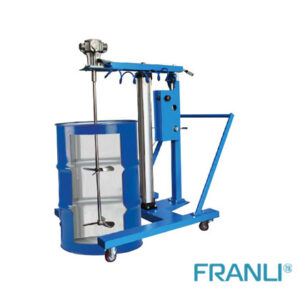
Pneumatic Mixer: Enhancing Efficiency & Productivity in Mixing Processes
A pneumatic mixer, also known as an air-driven mixer or air-powered mixer, is a type of mixer that utilizes compressed air to drive its mixing action.
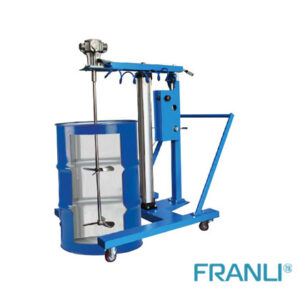
Enhance Efficiency & Quality with Pneumatic Paint Mixers
Pneumatic paint mixers utilize compressed air to generate rotational motion, enabling thorough mixing of paints and coatings. These mixers are equipped with a powerful air-driven motor that connects to a mixing shaft.
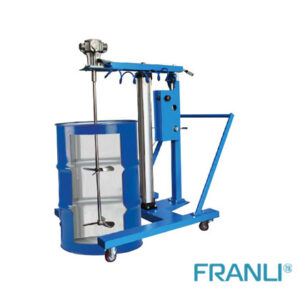
The Application of Pneumatic Mixers in Resins: Enhancing Efficiency & Quality
In the realm of resin manufacturing and processing, pneumatic mixers play a crucial role by simplifying the mixing process, ensuring uniformity, and improving overall quality.
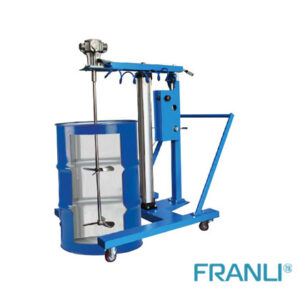
Pneumatic Mixers: Transforming Paint Application in the Coating Industry
Pneumatic mixers are mechanical devices that utilize compressed air to generate rotational motion, effectively blending and homogenizing paint.
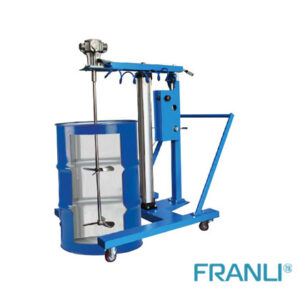
The Application of Pneumatic Mixers in Various Industries
Pneumatic mixers are widely utilized in various industries as a crucial component of the mixing process. These versatile machines utilize compressed air to rotate blades or paddles, enabling efficient and uniform blending of various substances or materials.
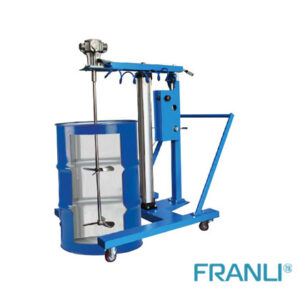
Pneumatic Mixer: Solution for Mixing Applications
A pneumatic mixer is a type of mixing equipment that uses compressed air to drive the mixing mechanism. The mixing mechanism can be a propeller, impeller, or turbine, depending on the application and viscosity of the materials being mixed.