Home » Pneumatic Mixers: Efficient Mixing Equipment
Pneumatic Mixers: Efficient Mixing Equipment
Pneumatic Mixers
A pneumatic mixer is a machine that has revolutionized the way liquids are mixed in various industries. The mixer uses compressed air to create a vortex in the liquid, which then mixes the contents of the container. Pneumatic mixers are mainly used in industries with explosion-proof requirements, such as petroleum, chemical, paint, paint, woodworking, food, daily chemical, and other flammable, dusty, heavy-duty, humid, and other workplaces.
Details of Pneumatic Mixers
- The pneumatic mixer can be adjusted steplessly.
- The pneumatic mixer can rotate forward and reverse.
- The working environment of the pneumatic mixer is not affected by vibration, high temperature, electromagnetic, radiation, etc.
- The air motor matched with the air mixer has the function of overload protection, and will not fail due to overload.
- The pneumatic mixer has a high starting torque and can be started directly with a load.
- The pneumatic mixer is easy to operate and easy to maintain and repair.
Application: petroleum, chemical, paint, paint, woodworking, food, daily chemical, and other flammable, dusty, heavy-duty, wet, and other industries.
This pneumatic mixe has been widely adopted in industries such as food and beverage, pharmaceuticals, and chemical processing.
Advantages of pneumatic mixers
1. The pneumatic mixer can be adjusted steplessly.
2. The pneumatic mixer can run forward and reverse.
3. The working environment of the pneumatic mixer is not affected by vibration, high temperature, electromagnetic, radiation, etc. It is suitable for harsh working environments and can work normally under adverse conditions such as flammable, explosive, high temperature, vibration, humidity, and dust.
4. The air motor matched with the air mixer has an overload protection function, and will not fail due to overload.
5. The pneumatic mixer has a high starting torque and can be started directly with a load.
6. The pneumatic mixer is easy to operate and easy to maintain and repair. The air motor has the advantages of simple structure, small size, lightweight, and high horsepower, and uses air as the medium, so it is easy to operate and easy to maintain.
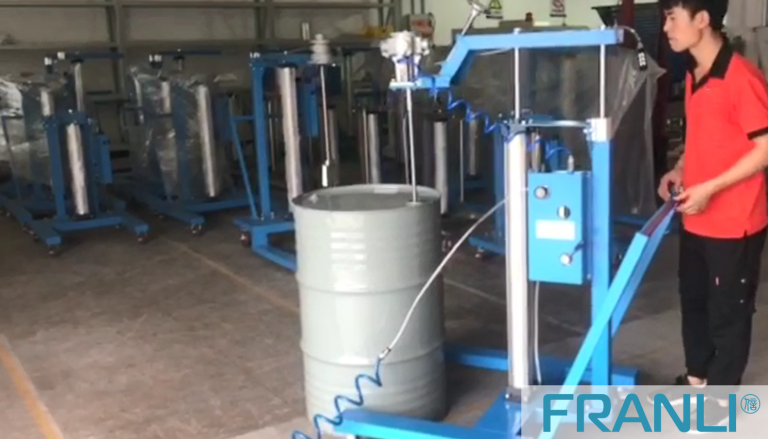
The pneumatic mixer is also more versatile than other mixers. It can be used to mix a wide range of liquids, including those that are highly viscous. This is because the mixer creates a vortex in the liquid, which ensures that all the contents of the container are mixed evenly. The mixer can also be used to mix liquids that are sensitive to heat or shear. This is because the mixer does not generate heat or shear forces, which can damage the contents of the container.
The pneumatic mixer is also more cost-effective than other mixers. This is because it requires less maintenance than other mixers. The mixer has fewer moving parts, which means that there are fewer parts that can break down. This reduces the need for repairs and maintenance, which in turn reduces the overall cost of operating the mixer.
The pneumatic mixer has several applications in various industries. In the food and beverage industry, the mixer is used to mix ingredients for various products such as sauces, dressings, and beverages. The mixer is also used to mix ingredients for bakery products such as bread and cakes. In the pharmaceutical industry, the mixer is used to mix ingredients for medicines and other healthcare products. The mixer is also used in the chemical processing industry to mix chemicals and other substances.
The pneumatic mixer has several components that work together to ensure that it operates efficiently. The main components of the mixer are the motor, the pneumatic mixer, and the mixing head. The motor is responsible for driving the mixing head, which creates the vortex in the liquid. The pneumatic mixer is responsible for providing the compressed air that is used to create the vortex. The mixing head is the part of the mixer that comes into contact with the liquid and mixes the contents of the container.
The motor used in the pneumatic mixer is usually an electric motor. The motor is connected to the mixing head through a shaft. The shaft is responsible for transmitting the rotational force from the motor to the mixing head. The motor is usually mounted on a frame, which is designed to provide support and stability to the mixer.
The pneumatic mixer used in the pneumatic mixer is responsible for providing the compressed air that is used to create the vortex in the liquid. The pneumatic mixer is usually a reciprocating or rotary compressor. The compressor is connected to the mixing head through a hose. The hose is designed to deliver compressed air to the mixing head. The pneumatic mixer is usually mounted on a frame, which is designed to provide support and stability to the mixer.
The mixing head used in the pneumatic mixer is part of the mixer that comes into contact with the liquid and mixes the contents of the container. The mixing head is usually made of stainless steel, which is durable and easy to clean. The mixing head is designed to create a vortex in the liquid, which ensures that all the contents of the container are mixed evenly. The mixing head is usually mounted on a shaft, which is connected to the motor through a coupling.
A pneumatic mixer is a machine that has revolutionized the way liquids are mixed in various industries. The mixer uses compressed air to create a vortex in the liquid, which then mixes the contents of the container. The pneumatic mixer has several advantages over traditional mixers, including being more efficient, hygienic, versatile, and cost-effective. The mixer has several applications in various industries, including the food and beverage, partial, and chemical processing industries. The main components of the mixer are the motor, the air compressor, and the mixing head, which work together to ensure that the mixer operates efficiently.
As a professional Pneumatic mixer, FRANLI has provided a complete set of mature equipment for related machines and production lines for more than 60 countries and thousands of industries in the world, and in Russia, Turkey, Spain, Brazil, Malaysia, Indonesia, and other regions, it has provided many An enterprise establishes related production lines.
Welcome to send inquiry to us and let’s make a win win business together !
Guidelines For Pneumatic Mixers
The stirring process of the pneumatic mixer is a single momentum transfer in the fluid field or a process including momentum, heat, mass transfer and chemical reaction. The agitator mainly inputs the energy of the device by making the stirring medium obtain a suitable flow field device.
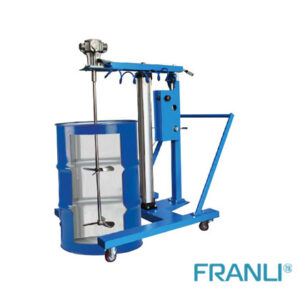
Pneumatic Mixer: Enhancing Efficiency & Productivity in Mixing Processes
A pneumatic mixer, also known as an air-driven mixer or air-powered mixer, is a type of mixer that utilizes compressed air to drive its mixing action.
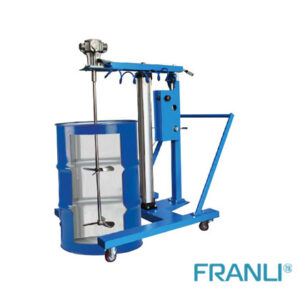
Enhance Efficiency & Quality with Pneumatic Paint Mixers
Pneumatic paint mixers utilize compressed air to generate rotational motion, enabling thorough mixing of paints and coatings. These mixers are equipped with a powerful air-driven motor that connects to a mixing shaft.
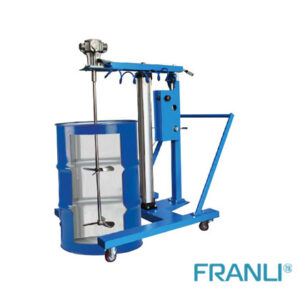
The Application of Pneumatic Mixers in Resins: Enhancing Efficiency & Quality
In the realm of resin manufacturing and processing, pneumatic mixers play a crucial role by simplifying the mixing process, ensuring uniformity, and improving overall quality.
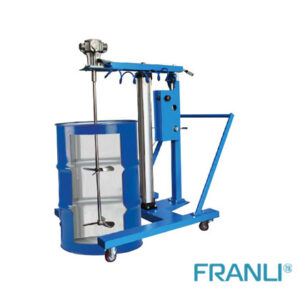
Pneumatic Mixers: Transforming Paint Application in the Coating Industry
Pneumatic mixers are mechanical devices that utilize compressed air to generate rotational motion, effectively blending and homogenizing paint.
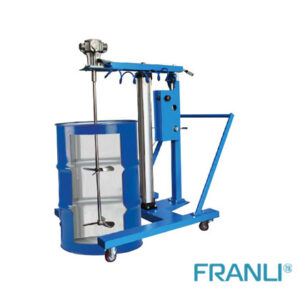
The Application of Pneumatic Mixers in Various Industries
Pneumatic mixers are widely utilized in various industries as a crucial component of the mixing process. These versatile machines utilize compressed air to rotate blades or paddles, enabling efficient and uniform blending of various substances or materials.
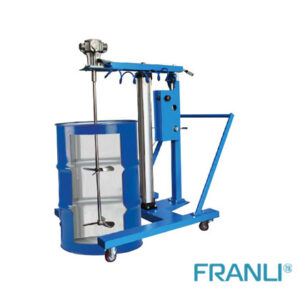
Pneumatic Mixer: Solution for Mixing Applications
A pneumatic mixer is a type of mixing equipment that uses compressed air to drive the mixing mechanism. The mixing mechanism can be a propeller, impeller, or turbine, depending on the application and viscosity of the materials being mixed.