Home » Pneumatic Mixer: Solution for Mixing Applications
Pneumatic Mixer: Solution for Mixing Applications
Pneumatic Mixers
Details of Pneumatic Mixers
- The pneumatic mixer can be adjusted steplessly.
- The pneumatic mixer can rotate forward and reverse.
- The working environment of the pneumatic mixer is not affected by vibration, high temperature, electromagnetic, radiation, etc.
- The air motor matched with the air mixer has the function of overload protection, and will not fail due to overload.
- The pneumatic mixer has a high starting torque and can be started directly with a load.
- The pneumatic mixer is easy to operate and easy to maintain and repair.
Application: petroleum, chemical, paint, paint, woodworking, food, daily chemical, and other flammable, dusty, heavy-duty, wet, and other industries.
Mixing is an essential process in various industries, including chemical, pharmaceutical, food, and paint. A pneumatic mixer is a versatile solution that offers efficient and effective mixing of liquids, powders, and other materials.
The pneumatic mixer works by using compressed air to power a motor, which in turn drives the mixing blades. The blades can be designed in a variety of shapes and sizes, depending on the specific mixing requirements of the application.
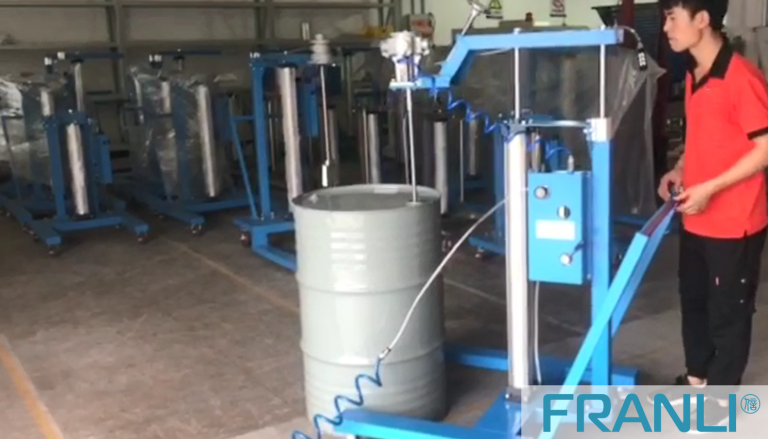
One of the primary advantages of using a pneumatic mixer is its ability to provide consistent mixing results. Because the mixer is powered by compressed air, it is not affected by fluctuations in electrical power or other external factors that can impact the performance of other types of mixers.
Additionally, pneumatic mixers are often more durable and long-lasting than other types of mixers. They are typically constructed from high-quality materials that can withstand the rigors of industrial use, and they require minimal maintenance and upkeep.
There are several different types of pneumatic mixers available, each designed for specific mixing applications. Some common types of pneumatic mixers include drum mixers, tank mixers, and paddle mixers.
Pneumatic paint mixer
Pneumatic paint mixers are widely used in the paint industry to mix different types of paints, including water-based and solvent-based paints. These mixers are designed to handle high-viscosity materials and ensure uniform mixing. They are available in different sizes and configurations, including handheld and stand-mounted models.
IBC mixer
Intermediate Bulk Containers (IBCs) are widely used in the chemical and pharmaceutical industries to store and transport liquids and powders. IBC mixers are designed to mix the contents of IBCs without the need to transfer the materials to another container. These mixers are available in different configurations, including top-mounted and side-mounted models.
Pneumatic drum mixer
Pneumatic drum mixers are used to mix liquids in drums and other containers. These mixers are ideal for applications where the mixing process needs to be done inside the container. They are available in different designs, including clamp-mounted and bung-mounted mixers. Drum mixers are designed to mix the contents of a drum or barrel, while tank mixers are used to mix the contents of larger tanks. Paddle mixers, on the other hand, are designed to mix dry or semi-solid materials.
Advantages of pneumatic mixers
Pneumatic mixers offer several advantages over other types of mixers. Firstly, they are easy to operate and require minimal maintenance. Secondly, they are versatile and can be used for a wide range of applications. Thirdly, they are cost-effective and offer a low cost of ownership.
Pneumatic mixers are a versatile solution for mixing applications in various industries. Whether you need to mix paints, liquids in drums, or contents of IBCs, there is a pneumatic mixer that can meet your needs. With their ease of operation, versatility, and cost-effectiveness, pneumatic mixers are an excellent investment for any business that needs to mix materials.
As a professional Pneumatic mixer, FRANLI has provided a complete set of mature equipment for related machines and production lines for more than 60 countries and thousands of industries in the world, and in Russia, Turkey, Spain, Brazil, Malaysia, Indonesia, and other regions, it has provided many An enterprise establishes related production lines.
Welcome to send inquiry to us and let’s make a win win business together !
Guidelines For Pneumatic Mixers
The stirring process of the pneumatic mixer is a single momentum transfer in the fluid field or a process including momentum, heat, mass transfer and chemical reaction. The agitator mainly inputs the energy of the device by making the stirring medium obtain a suitable flow field device.
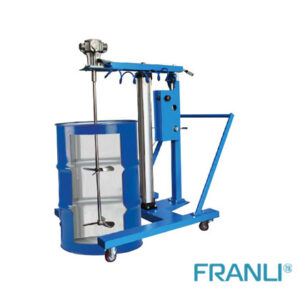
Pneumatic Mixer: Enhancing Efficiency & Productivity in Mixing Processes
A pneumatic mixer, also known as an air-driven mixer or air-powered mixer, is a type of mixer that utilizes compressed air to drive its mixing action.
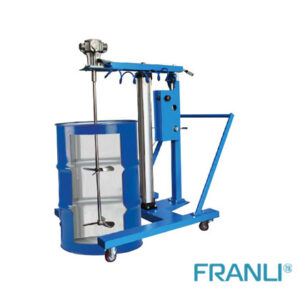
Enhance Efficiency & Quality with Pneumatic Paint Mixers
Pneumatic paint mixers utilize compressed air to generate rotational motion, enabling thorough mixing of paints and coatings. These mixers are equipped with a powerful air-driven motor that connects to a mixing shaft.
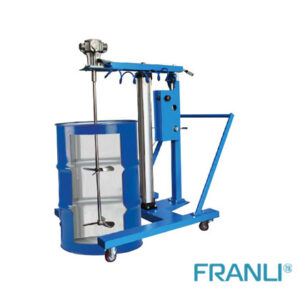
The Application of Pneumatic Mixers in Resins: Enhancing Efficiency & Quality
In the realm of resin manufacturing and processing, pneumatic mixers play a crucial role by simplifying the mixing process, ensuring uniformity, and improving overall quality.
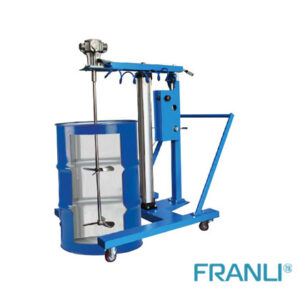
Pneumatic Mixers: Transforming Paint Application in the Coating Industry
Pneumatic mixers are mechanical devices that utilize compressed air to generate rotational motion, effectively blending and homogenizing paint.
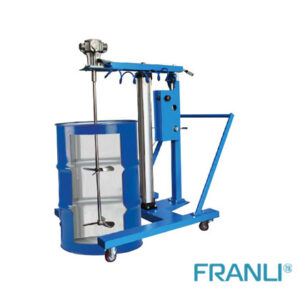
The Application of Pneumatic Mixers in Various Industries
Pneumatic mixers are widely utilized in various industries as a crucial component of the mixing process. These versatile machines utilize compressed air to rotate blades or paddles, enabling efficient and uniform blending of various substances or materials.
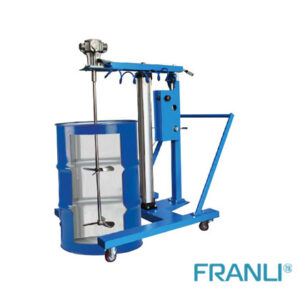
Pneumatic Mixer: Solution for Mixing Applications
A pneumatic mixer is a type of mixing equipment that uses compressed air to drive the mixing mechanism. The mixing mechanism can be a propeller, impeller, or turbine, depending on the application and viscosity of the materials being mixed.