Home » What is a pneumatic mixer?
What is a pneumatic mixer?
Pneumatic Mixers
Details of Pneumatic Mixers
- The pneumatic mixer can be adjusted steplessly.
- The pneumatic mixer can rotate forward and reverse.
- The working environment of the pneumatic mixer is not affected by vibration, high temperature, electromagnetic, radiation, etc.
- The air motor matched with the air mixer has the function of overload protection, and will not fail due to overload.
- The pneumatic mixer has a high starting torque and can be started directly with a load.
- The pneumatic mixer is easy to operate and easy to maintain and repair.
Application: petroleum, chemical, paint, paint, woodworking, food, daily chemical, and other flammable, dusty, heavy-duty, wet, and other industries.
The electric appliance drives the agitator to rotate at a certain speed after the speed is changed by the reducer. According to the different agitation speeds, fluids with different speeds are discharged from the impeller. Flow is involved in it, thus forming a complex flow of movement. This synthetic motion flow has both horizontal circulation flow and up-and-down circulation flow along the wall surface and the stirring shaft. This circulation flow can involve a large range in the stirring tank and play a role in volume circulation.
Advantages of pneumatic mixer
1. The pneumatic mixer can be adjusted steplessly. As long as the opening of the intake valve or exhaust valve is controlled, that is, the flow rate of compressed air is controlled, the output power and speed of the motor can be adjusted. The purpose of adjusting the speed and power can be achieved.
2. The pneumatic mixer can rotate forward and reverse. As long as the simple use of the control valve changes the direction of the air motor intake and exhaust, the forward rotation and reverse rotation of the output shaft of the air motor can be realized, and the direction can be reversed instantaneously.
3. The working environment of the pneumatic mixer is not affected by vibration, high temperature, electromagnetic, radiation, etc. It is suitable for harsh working environments and can work normally under adverse conditions such as flammable, explosive, high temperature, vibration, humidity, and dust.
4. The air motor matched with the air mixer has the function of overload protection, and will not fail due to overload. When overloaded, the air motor only slows down or stops, and when the overload is removed, it can immediately resume normal operation without any failures such as device damage. It can run continuously with a full load for a long time, and the temperature rise of the air motor is small.
5. The pneumatic mixer has a high starting torque and can be started directly with a load. The start and stop are quick, and it can be started with load, and it will not affect the use due to the burner sometimes like the electric mixer.
6. The pneumatic mixer is easy to operate and easy to maintain and repair. The air motor has a simple structure, small in size, lightweight, high horsepower, and uses air as the medium, which is easy to operate and easy to maintain.
The rotational power of the pneumatic mixer affects the quality of the mixing product, so it is necessary to ensure that the power of the pneumatic mixer remains stable during use. Do you know the working principles of the pneumatic mixer? What are the factors and applications that affect the power of a pneumatic mixer? What are the factors that affect the power of the pneumatic mixer?
1. The diameter of the stirrer.
2. The number, shape blade length, and width of the agitator blades.
3. Container diameter.
4. The height of the liquid in the container.
5. The distance between the agitator and the bottom of the container.
6. The number and width of the baffles.
How pneumatic mixer Work
The stirring blades of the pneumatic lift mixer are driven by the power unit to rotate in a fixed direction; during the rotation process, the materials are driven to rotate axially and radially. The materials in the mixer have axial movement and circular movement at the same time, so there are several stirring forms such as shear stirring and diffusion stirring at the same time. It can effectively disperse and stir materials. Pneumatic Lifting Pneumatic Mixer The mixer realizes the work of the cylinder through the rotation of the air valve or the jog control of the solenoid valve and uses the lifting of the cylinder to drive the motor and the working head to rise and fall.
Application of Pneumatic Mixer
The mixing impeller and mixer blades can be replaced in a variety of styles, specifically listed as the following more than 20 types: three-blade propulsion type, three-wide blade detachable propeller type agitator, six straight-blade stable rings, elliptical bottom frame type, three-wide blade type Stabilizing ring, semi-arc detachable disc, toothed disc type, square frame agitator, gear type, anchor belt type agitator, turbine type, dispersing disc, disc type, defoaming type, anchor type, frame type, Inclined leaf open turbine agitator, six curved leaf open turbine, curved leaf open turbine, integral stable ring, split stable ring, curved leaf detachable disc turbine, curved leaf detachable disc turbine, three-blade propulsion Mode. All the above paddles can be replaced quickly to meet the needs of various process requirements. At the same time, the agitator can be raised and lowered pneumatically, and the lifting device is flexible and light. One device can be equipped with several stirring containers, and the paddles can be replaced quickly. Pneumatic mixers are suitable for stirring and mixing fluid liquids, such as color mixing, mixing various raw materials, and other mixing operations.
Pneumatic mixers are a good substitute for manual mixing in practical applications. According to different scenarios, there are differences in the size, power, and other specifications of pneumatic mixers. Therefore, the design must be combined with the actual use scenarios.
1. Determine the purpose of stirring: such as liquid-liquid mixing, solid-liquid suspension, gas-liquid or liquid-liquid dispersion, whether it is necessary to achieve heat transfer, absorption, extraction, dissolution, crystallization, and other process purposes. Choose the form of the stirring paddle according to the process characteristics.
2. Calculate the stirring power: that is, the power required during the stirring process
Reference formula: power = power quasi-number * liquid density * 3rd power of revolutions * 5th power of pulp diameter.
The calculation of the power standard is complicated and is related to the tank diameter, slurry diameter, blade width, angle, number of layers, viscosity, number of baffles, and size of baffles.
3. Select the power of the air motor: the calculated value after considering the efficiency should be greater than or equal to 1.5 times the stirring power.
4. Determination of the minimum number of stirring rotations on the street: this number of rotations is the minimum number of rotations to meet the purpose of stirring rather than the critical number of rotations of the stirring shaft.
5. Select and check the stiffness and strength of the stirring shaft and paddle according to the power.
6. When using the reducer, the service factor of the reducer and the carrying capacity of the reducer should also be considered.
7. For slender shafts, consider adding support, middle or bottom support.
8. Also consider the installation method (top entry or bottom entry or side entry), this is determined first.
9. Design support
10. Select the sealing form (filling or mechanical seal)
As a professional Pneumatic mixer, FRANLI has provided a complete set of mature equipment for related machines and production lines for more than 60 countries and thousands of industries in the world, and in Russia, Turkey, Spain, Brazil, Malaysia, Indonesia, and other regions, it has provided many An enterprise establishes related production lines.
Welcome to send inquiry to us and let’s make a win win business together !
Guidelines For Pneumatic Mixers
The stirring process of the pneumatic mixer is a single momentum transfer in the fluid field or a process including momentum, heat, mass transfer and chemical reaction. The agitator mainly inputs the energy of the device by making the stirring medium obtain a suitable flow field device.
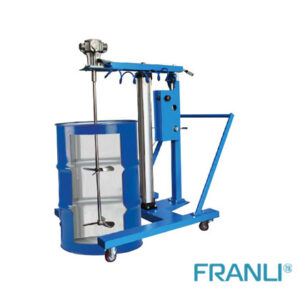
Pneumatic Mixer: Enhancing Efficiency & Productivity in Mixing Processes
A pneumatic mixer, also known as an air-driven mixer or air-powered mixer, is a type of mixer that utilizes compressed air to drive its mixing action.
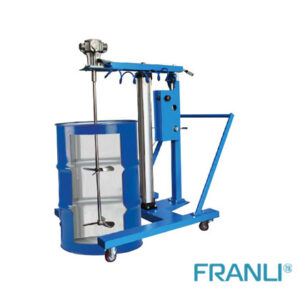
Enhance Efficiency & Quality with Pneumatic Paint Mixers
Pneumatic paint mixers utilize compressed air to generate rotational motion, enabling thorough mixing of paints and coatings. These mixers are equipped with a powerful air-driven motor that connects to a mixing shaft.
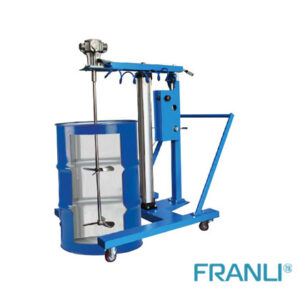
The Application of Pneumatic Mixers in Resins: Enhancing Efficiency & Quality
In the realm of resin manufacturing and processing, pneumatic mixers play a crucial role by simplifying the mixing process, ensuring uniformity, and improving overall quality.
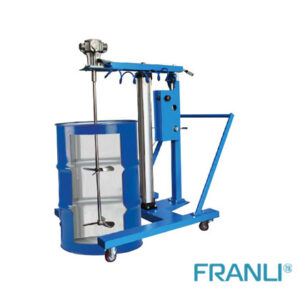
Pneumatic Mixers: Transforming Paint Application in the Coating Industry
Pneumatic mixers are mechanical devices that utilize compressed air to generate rotational motion, effectively blending and homogenizing paint.
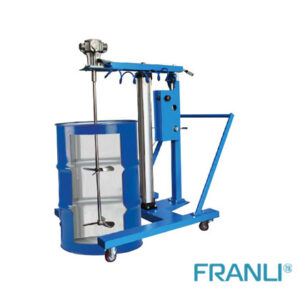
The Application of Pneumatic Mixers in Various Industries
Pneumatic mixers are widely utilized in various industries as a crucial component of the mixing process. These versatile machines utilize compressed air to rotate blades or paddles, enabling efficient and uniform blending of various substances or materials.
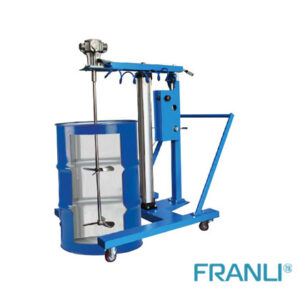
Pneumatic Mixer: Solution for Mixing Applications
A pneumatic mixer is a type of mixing equipment that uses compressed air to drive the mixing mechanism. The mixing mechanism can be a propeller, impeller, or turbine, depending on the application and viscosity of the materials being mixed.