Home » Pesticide Production Line
Pesticide Production Line
Pesticide Production Line
The first step in pesticide production is the formulation of the active ingredients. This involves mixing various chemicals in precise proportions to create the desired effect. The active ingredients are then combined with other additives such as surfactants, emulsifiers, and stabilizers to create the final product. The formulation process is critical to the effectiveness of the pesticide, and it requires the use of specialized equipment such as sand mills, twin shaft dispersers, blenders, and homogenizers.
Pesticide suspension concentrates production equipment
(1) Pesticide storage tank: Its material is mainly composed of the stainless steel storage tank or carbon steel storage tank and other forms. Generally, its function is mainly used to store and transport the original medicine, additives, and so on.
(2) Powder conveying equipment: The powder conveying equipment uses strong pressure to convey the energy of the compressed air to the conveyed material through the pressure transmitter. This method can easily overcome various resistances and transport the material sent to the specified location.
(3) Twin shaft disperser: It is widely used in the medicine and chemical industry for mixing, dispersing, and dissolving equipment, and is widely used in adhesive chemical products.
(4) Sand mill: Sand mill is also called bead mill. This machine is mainly used for wet grinding chemical liquid products. According to the performance, it can be roughly divided into a vertical sand mill, a horizontal sand mill, a basket mill, a rod sand mill, etc.
(5) Emulsification kettle: The intermittent high-shear dispersing emulsification homogenizer is through the high-speed and stable rotation of the rotor to form high-frequency, strong circumferential tangential velocity, angular velocity, and other comprehensive kinetic energy performance.
(6) Blending kettle: blend the liquid medicine, add additives, etc. according to the process. Through the structural design and parameter configuration of the container, the heating, evaporation, cooling, and low-speed mixing functions required by the process are realized.
)
Twin shaft dispersers are used to blend the active ingredients and other additives together. They come in different sizes and shapes, depending on the volume of the product being produced. Some mixers use a simple paddle or ribbon blade to mix the ingredients, while others use more complex mechanisms such as high-shear mixers, which can create a more uniform and consistent blend.
Ribbon Blenders are used to mix dry ingredients, such as powders or granules. They work by tumbling the ingredients together, ensuring that each particle is coated with the active ingredient. Ribbon Blenders can be either batch or continuous, depending on the production volume and the desired level of automation.
Homogenizers are used to create a stable emulsion of oil and water-based ingredients. They work by applying high pressure and shear forces to the mixture, breaking down the droplets and creating a uniform dispersion. Homogenizers are essential for creating products such as insecticides and fungicides, which require a stable emulsion to be effective.
Once the formulation is complete, the next step is to fill the product into containers. This involves the use of filling machines, which can fill bottles, cans, or drums with the product. Filling machines come in different types, including volumetric, gravity, and piston fillers. Volumetric fillers use a predetermined volume of product to fill each container, while gravity fillers rely on the weight of the product to fill the container. Piston fillers use a piston to push the product into the container, ensuring precise filling.
After filling, the containers are sealed using capping machines. Capping machines come in different types, including screw cappers, snap cappers, and crimping machines. Screw cappers use a rotating head to screw the cap onto the container, while snap cappers use a press to snap the cap onto the container. Crimping machines are used for metal containers and use a crimping head to seal the lid onto the container.
The final step in pesticide production is labeling and packaging. This involves the use of labeling machines, which can apply labels to the containers automatically. Labeling machines come in different types, including wraparound labelers, front and back labelers, and top labelers. Wraparound labelers apply a label that wraps around the container, while front and back labelers apply labels to the front and back of the container. Top labelers apply labels to the top of the container.
The production of pesticides involves complex machinery and sophisticated technology. From the formulation of the active ingredients to the filling, sealing, labeling, and packaging of the final product, each step requires specialized equipment and skilled operators. The use of these machines ensures that the pesticides produced are effective, safe, and of high quality, helping farmers to protect their crops and feed the world’s growing population.
Welcome to send inquiry to us and let’s make a win win business together !
Guidelines For production line
FRANLI has several sets of wet grinding production lines, including PCB ink production line, ink production line, pesticide production line, automobile coating production line, etc.
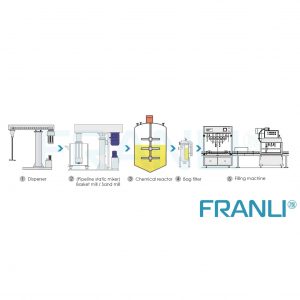
Pesticide Production Line
The production of pesticides mainly uses sand mills, emulsifiers, chemical reaction kettles, twin-shaft mixers, filling machines, and other equipment. This equipment thus constitutes a complete set of pesticide production lines, from the grinding and storage of particles to the reaction and Blending, and finally filling and packaging, the FRANLI pesticide production line is fully intelligent, with the characteristics of simple operation, safety, and stability.
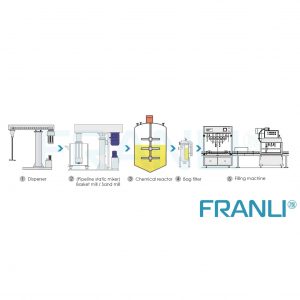
Gravure Ink Production Line: manufacturing process
The gravure ink production line is a professional manufacturing process that requires attention to detail and a commitment to quality.
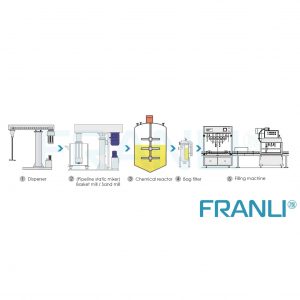
Printing ink production line
FRANLI Printing ink production line mainly takes intelligence, environmental protection, and high production efficiency as the main production standards.
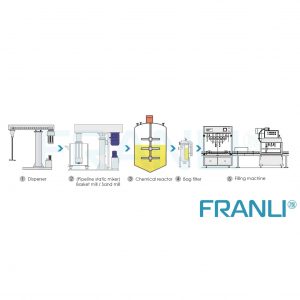
Water Ink Make equipment & production line
FRANLI water ink complete set of equipment and production line is mainly composed of an intelligent batching system, high-speed dispersion pulping system, metering system, horizontal grinding series system, multi-functional mixing and coloring system, cleaning system, automatic control system, automatic filling system, and other parts. Advanced production technology.
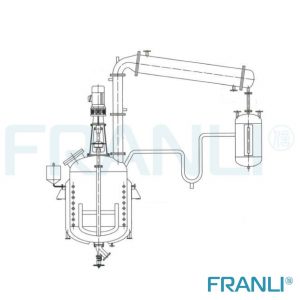
Resin Production Line & Complete Manufacturing Equipment
FRANLI provides complete sets of resin manufacturing equipment and production lines, which are mainly suitable for the synthesis of various chemical resins, such as unsaturated polyester resin, phenolic resin, epoxy resin, alkyd resin, ABS resin, etc. It can also be used for the manufacturing and production of Various types of emulsion resins, such as acrylic resin emulsion, etc.
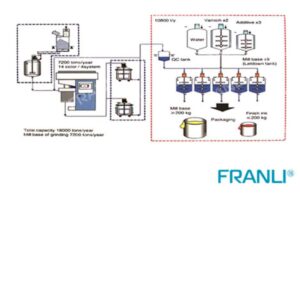
Ink production line
The main equipment of the ink production line includes material storage tanks, barrels, multi-model dispersing machines, chemical reactors, sand mills, three-roll mills, material operating platforms, filling machines, electronic process control systems, process pipelines, air compressors, A set of equipment such as cleaning equipment.