Home » Ointment mill for paste material
Ointment mill for paste material
Ointment Mill
FRANLI Ointment mills are used for dispersion of creams, ointment, gels, suspensions, and pastes as it specializes in particle size reduction for good absorption in the body.
Details of Ointment Mill
- Two types: handwheel and digital control gap
- Safe scraper socket, Emergency-stop
- Space-saving desktop models
- Drip tray for easy cleaning
Application: Paint, Adhesive, Battery, Pharmaceutical industry, Cosmetic
After the pre-dispersion, fine dispersion of ointment takes place in the ointment mill. The mills require three passes for obtaining the required coloristic properties and particle size. Ointment mills use great shear force for dispersing the active ingredients or for homogenizing viscous materials. The shear force of ointment mills is formed by the rollers that are in different directions rotating at various speeds compared to one another.
The ointment mills allow the product’s powder clumps and active ingredients are disintegrated and homogenized. The rollers pull out the grittiness and provide top-quality particles. The ointment mill helps in providing effective ointment and is widely used by pharmaceutical manufacturers.
The Function of The Ointment Mill
The function of the ointment mill is the differential speed happening between three rollers. The speed difference between the mill’s third roll and the second roll is up to four times greater than that between the second and first roll. The dispersion happens in the mill’s second nip, and the first one regulates the second nip’s feeding. The three rolls have been positioned correctly, and if the viscosity is high to make hydraulic pressure, all the rolls are pressed together. For low viscosity and if the product has shear sensitivity, then the rolls are not pressed together.
As a result of the constant flow of volume and differential speeds of the roll, a first nip, as well as a second nip, contains the same roll speed ratio. It means when the rolls are positioned for low viscosity; then the second and first nip will be at various settings. In an ointment mill, the dispersion happens in the shear field that is over the roll’s length. There is less or no impact on the particles when these particles are smaller compared to the nip. This feature helps in easing the dispersing process and makes it uniform. It is also adjustable through the position or pressure of the three rolls.
Using the shear stress does not affect any particle. It means the shape, size, or surface of the phase that is discontinuous does not change. For various applications, it is highly needed, like for pastes or gels or creams where you may not want to transform the one particle size. Many materials do not get affected in the process of dispersion, and it is possible only due to shear stress.
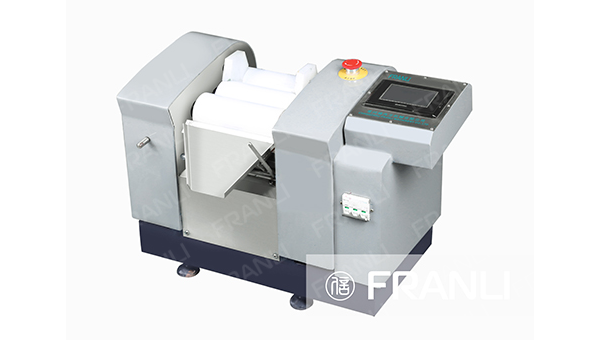
Ointment Mill Process Parameters
The ointment mill process has three parameters that are operation method, rheological behavior, and machine. The machine handles large viscosities range either with low line forces or with correct roll positioning systems. If a mill base adapts, then it can optimize the entire process. Rheological behavior is essential, but these are not always influenced.
Best Practices to Follow for Safe Ointment Milling
1. Consider Taking Proper Care:
An ointment mill usually comes completely assembled when it is normally supplied. When they are removed from the containers, ensure handling gently and with proper care so that no damage happens to the ointment mill roll’s surfaces. A damage-free and clean roll working surface are essential for the mill to work properly.
2. Take-off Knife Needs Better Handling:
The ointment mill apron’s knife has a blunt cutting edge, which needs to be managed with proper care. The take-off knife position is correct if it is parallel to the centerline and touches the roll of the apron just a little higher than the centerline.
3. Ensure Excellent Installation:
Before the ointment mill starts operating, ensure that the mill is bolted well and is in its place. Moreover, you need a solid base, particularly for the production or generation size models. After the mill is properly leveled and placed well, the installation and wiring of all electrical components need to be done through some qualified electricians.
4. Test to determine the right gap setting:
Do testing for knowing which will be the right gap setting. Testing and knowing the gap setting is crucial for a specific product to enhance the throughput without compromising the quality of dispersion.
5. Never run ointment mill dry:
One should keep in mind that running the mill dry can result in dangerous consequences. When all products have run through, then open the mill roll and correctly disengage the apron roll.
6. Lubricate bearings from time to time:
Roll journals get equipped along with roller bearings and ball. Therefore, it is better to do bearing lubrication as much as possible. Ensure that those bearings are properly lubricated every month.
7. Avoid Loose Fitting Clothes:
You must try to avoid wearing loose-fitting clothes or accessories as they can get tangled in the mill rolls.
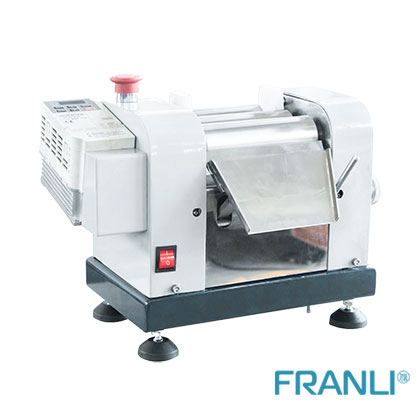
Ointment Mill Safety Regulations
The ANSI ointment mill safety regulations were revised in the year 2007, and it again got issued with some changes in the year 2017. For being completely ANSI compliant, the ointment mill should have an Emergency Braking, Washup Mode, NGSIS, safety cable for feed roll, and a Washup Stick.
The Washup Mode is the extremely slow speed used for cleaning mill rolls. NGSIS monitors functions of the mill for ensuring that when rolls are getting cleaned. A Feed roll cable assembly is needed for the production size with a mill roll length over 14 inches. The Washup Stick remains inside the feed’s nip.
The NGSIS notices an apron nip and a feed nip position, whether it is closed or open. It also senses the endplates’ position, whether it is up for the cleaning purpose or down for the running purpose. Moreover, the NGSIS can sense the Washup Stick position and also the selector switch position. ANSI also gives the procedures for ointment mill cleaning.
An ointment mill is in greater demand by the pharmaceutical sector as ointments, creams, gels, etc., are always needed. But you should always go for mills from reliable companies. Franli has the best three-roll mill or ointment mill that is perfect for fine dispersion. The mills are also easy to operate and clean. If you are searching for the ideal mills, then Franli is the best option for you.
Welcome to send inquiry to us and let’s make a win win business together !
Guidelines For Three Roll Mill
Three roll mills are widely used in a variety of chemical industries, from medium to high viscosity productions. FRANLI machine can break open all kinds of pigment, UV ink, offset ink, decorative paints, and Lubricants, it also can catch the greatest fineness in cosmetics/ lipstick and electronics industries.
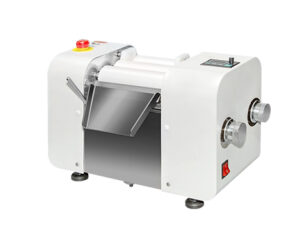
Three Roll Mill For Carbon Black|High Grinding & Dispersion
Three roll mill is the main equipment for grinding colored carbon black, as it is used extensively in rubber, plastics, paints, and inks, and some carbon black is added.
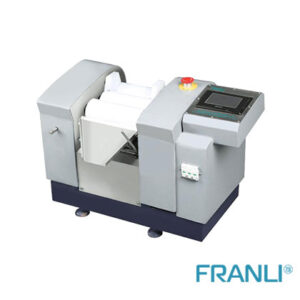
Laboratory Three Roll Mill|PLC Control System & Experimental
The laboratory three roll mill is equipped with the most advanced PLC functions to continuously improve the operability of the most primitive production equipment.
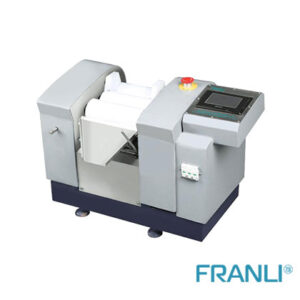
Three Roll Mill For Grease
The three roll mill plays a vital role in the grinding of grease. Grease is essentially a kind of lubricating oil, which is a solid or semi-solid product formed by one or more thickeners through the grinding and dispersing action of a three roll mill.
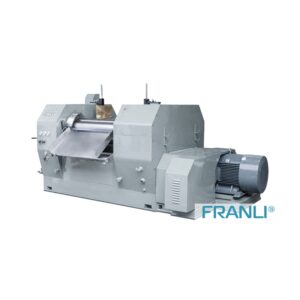
Three Roll Mill For Attapulgite
Three roll mill is the main equipment for grinding attapulgite. The attapulgite is ground and dispersed mainly because it is a natural colloid. Even if the size of the attapulgite reaches 0.1mm, it cannot be easily dispersed by the machine, so the final state of attapulgite formation has been greatly developed.
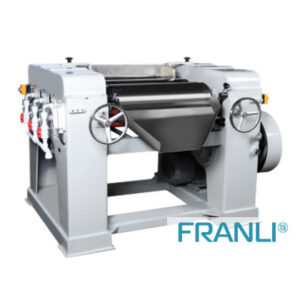
Rolls of a three-roll mill
The three-roll mill is mainly used for grinding materials of various viscosities and is one of the best wet grinding equipment. The dispersing and emulsification effect of the three-roll mill is excellent, especially for ink, paint, colloid, chocolate, plastic, cosmetics, etc., whether it is liquid slurry or paste material, the three-roll mill can work easily.
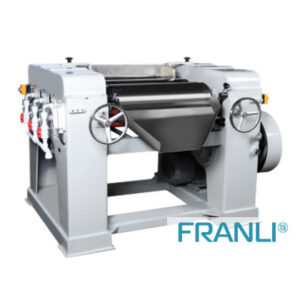
3 roll mill|Failure of the roll shaft & pulley
The 3 roll mill is a grinding and dispersing equipment, which plays an irreplaceable role in improving the quality of coating products.