Home » Multi-Shaft Mixers: Revolutionizing Leak-Proofing Agents
Multi-Shaft Mixers: Revolutionizing Leak-Proofing Agents
Multi Shaft Mixers
In industries where leak-proofing is crucial, such as automotive, construction, and manufacturing, the development of efficient and effective solutions is paramount. Leak-proofing agents play a vital role in preventing leakage and ensuring product integrity. Traditionally, manual mixing methods have been used, but they are time-consuming and less reliable. With advancements in technology, the application of multi-shaft mixers has revolutionized the production process for leak-proofing agents, providing consistent and high-quality results.
Advantages of Multi-Shaft Mixer
- Which can mix the material ≤1,000,000 cps, stronger power, fully mixing high viscosity.
- The Teflon scrapper on the low speed (butterfly mixer), scraping the wall of the tank also bottom of the tank.
- The stainless steel round cover with vacuum system, to remove the foam and air, sight view glass, feeding system hole.
Application: Paint, Adhesive, Battery, Pharmaceutical industry, Cosmetic
These agents are designed to seal gaps, cracks, and joints in various materials to prevent leakage. They are commonly used in sealing automotive gaskets, construction joints, and pipe connections. Leak-proofing agents can be formulated as liquid or paste-like substances, combining various chemical compounds to achieve optimal sealing properties.
The Role of Multi-Shaft Mixers
Multi-shaft mixers are a type of industrial mixing equipment specifically designed for high-viscosity materials. They are ideal for the production of leak-proofing agents due to their ability to handle thick and challenging formulations. Compared to traditional mixing methods, multi-shaft mixers offer several advantages in terms of efficiency, consistency, and versatility.
1. Enhanced Mixing Capabilities:
Multi-shaft mixers leverage multiple agitators and blades operating at different speeds and configurations. This highly efficient design ensures thorough mixing and dispersion of ingredients, resulting in a homogeneous mixture. The combination of high-speed and low-speed agitators promotes the breakup of agglomerates and guarantees a smooth and consistent texture for leak-proofing agents.
2. Effective Deaeration:
The nature of leak-proofing agents often entails the presence of entrapped air, which can compromise the sealing properties. Multi-shaft mixers incorporate vacuum capabilities to remove air bubbles during the mixing process. This deaeration feature enhances the quality of leak-proofing agents, ensuring they are free from air pockets that could compromise adhesion and sealing effectiveness.
3. Customization and Flexibility:
Multi-shaft mixers offer versatile configurations that can be tailored to specific production requirements. Manufacturers can customize the number, type, and arrangement of agitators based on the desired viscosity and characteristics of the leak-proofing agent. This flexibility enables manufacturers to optimize the mixing process, resulting in precise control over product quality, consistency, and performance.
4. High Production Capacity:
Efficiency is a key aspect of manufacturing leak-proofing agents, ensuring a continuous and cost-effective production process. Multi-shaft mixers exhibit high production capacity, allowing for large-scale and batch production. The ability to handle significant volumes of material enhances productivity while maintaining consistent quality.
5. Temperature Control:
Certain leak-proofing agents may require specific temperature conditions during mixing to facilitate chemical reactions or maintain stability. Multi-shaft mixers often incorporate temperature control features, enabling precise adjustments and maintenance of optimal mixing conditions. This aspect ensures that the chemical properties and overall performance of the leak-proofing agent are not compromised.
In the context of leak-proofing agents, multi-shaft mixers have proven to be a game-changer in terms of efficiency, consistency, and versatility. Their ability to handle high-viscosity materials, enhance mixing capabilities, enable deaeration, and provide customization options makes them an ideal choice for manufacturers in various industries. By utilizing multi-shaft mixers, manufacturers can optimize the production process, resulting in leak-proofing agents that provide superior performance and reliability. As technology advances, these mixers will continue to play a vital role in the development of leak-proofing solutions, ensuring the integrity and durability of products in a wide range of applications.
Welcome to send inquiry to us and let’s make a win win business together !
Guidelines For Multi Shaft Mixer
FRANLI customized different kinds of multi-shaft mixers for more than 300+ customers. This kind of machine works in the coating industry, medicine industry, cosmetic industry, and other high technology chemical industries.
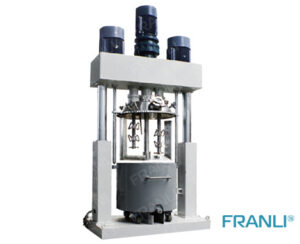
The Application of Triple Shaft Mixers in Adhesives
Triple-shaft mixers, also known as multi-shaft mixers, are innovative blending machines designed to efficiently mix and disperse various components in adhesives.
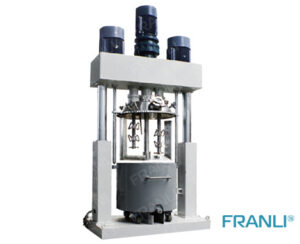
Triple Shaft Mixer: Ideal Equipment for Ink Production
Triple shaft mixers are capable of handling a wide range of ink formulations, including solvent-based, water-based, UV-curable, and hybrid inks.
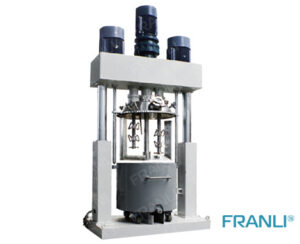
The Versatility and Application of Triple Shaft Mixers in Coatings
Triple shaft mixers have revolutionized the coating industry by providing efficient and versatile solutions for mixing raw materials.
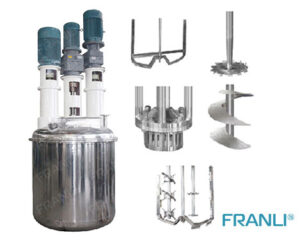
What is a Multi-Shaft Mixer?
A multi-shaft mixer is a type of industrial mixer that has more than one mixing shaft. These mixers are designed to mix multiple ingredients simultaneously, allowing for more efficient and effective mixing.
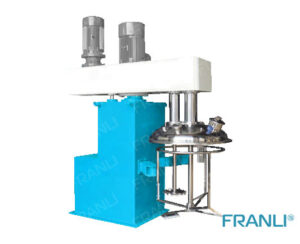
Dual Shaft Mixer – Dispersion & Stirring
The dual shaft mixer is the best mixer to dissolve the specific ingredients with appropriate shear capacity. This activity is performed by the high-speed shafts situated in the mixer and provides you with the perfect uniformity of the product. It also contains an Anchor agitator and a High-Speed Disperser that offer you the best quality and consistency.
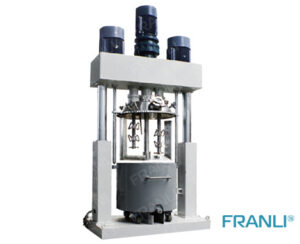
Triple Shaft Mixer | anchor type, butterfly type & frame type
The FRANLI triple shaft mixer extends the working area by adding a rotating stator mixer with a large displacement or a second quick distributor. High shear stator and rotary mixer can emulsify and homogenize products that require higher shear forces to reduce particles into smaller sizes.