Home » Overview of Laboratory Reactor
Overview of Laboratory Reactor
lab reactor
Laboratory reactors, also known as lab reactors, are essential tools in scientific research, product development, and process optimization. These reactors provide a controlled environment for conducting chemical reactions, mixing, dispersing, and homogenizing processes. They come in various types and designs, each tailored to specific applications and requirements.
Details of Lab Reactor
- Using the latest reaction technology
- It has high temperature resistance, corrosion resistance, and high durability.
- Heating methods include steam, electric heater, high temperature heat transfer oil
- Using jacket, half pipe, fan coil, and other structures
Application: Chemicals, pharmaceuticals, dyes, pesticides, petroleum, food additives, etc.
Laboratory reactors can be broadly categorized into several types based on their design and functionality. The most common types include batch reactors, continuous stirred tank reactors (CSTR), plug flow reactors (PFR), fixed bed reactors, and specialized reactors such as high-pressure reactors and microwave reactors.
Batch Reactors
Batch reactors are the simplest type of laboratory reactors. In a batch reactor, a specific quantity of reactants is loaded into the reactor vessel, and the reaction is allowed to proceed for a predetermined period. The reaction mixture is then discharged, and the reactor is cleaned and prepared for the next batch.
Operating Principles
– Loading: Reactants are introduced into the reactor vessel.
– Reaction: The reaction proceeds under controlled conditions (temperature, pressure, agitation) for a set duration.
– Discharge: The reaction mixture is removed, and the reactor is cleaned.
Applications
Batch reactors are widely used in the pharmaceutical industry for synthesizing small molecules and in the chemical industry for producing specialty chemicals and intermediates. They are also used in academic research for studying reaction kinetics and mechanisms.
Continuous Stirred Tank Reactors (CSTR)
Continuous stirred tank reactors (CSTR) consist of a vertical cylindrical vessel with an agitator. Reactants are continuously fed into the reactor, and products are continuously removed. The CSTR maintains a constant temperature and concentration of reactants, making it ideal for steady-state operations.
Operating Principles
– Continuous Feeding: Reactants are continuously introduced into the reactor.
– Agitation: The agitator ensures uniform mixing and temperature distribution.
– Continuous Removal: Products are continuously removed from the reactor.
Applications
CSTRs are commonly used in the chemical process industries for reactions that require constant conditions, such as polymerization, fermentation, and hydrogenation. They are also used in wastewater treatment and biofuel production.
Plug Flow Reactors (PFR)
Plug flow reactors (PFR) consist of a long, narrow tube through which reactants flow. The reactants move through the tube with minimal mixing, and the reaction occurs as they travel along the length of the reactor. PFRs provide precise control over reaction time and are suitable for reactions with well-defined kinetics.
Operating Principles
– Flow: Reactants flow through the reactor in a plug-like manner.
– Reaction: The reaction occurs as the reactants move along the tube.
– Product Collection: Products are collected at the reactor’s outlet.
Applications
PFRs are widely used in the petrochemical industry for processes such as catalytic cracking and reforming. They are also used in the production of polymers, pharmaceuticals, and fine chemicals.
Fixed Bed Reactors
Fixed bed reactors consist of a packed bed of catalyst particles through which reactants flow. The catalyst induces the desired reaction, and the products are collected at the reactor’s outlet. Fixed bed reactors are commonly used for catalytic processes.
Operating Principles
– Catalyst Bed: The reactor contains a packed bed of catalyst particles.
– Flow: Reactants flow through the catalyst bed.
– Reaction: The catalyst induces the desired reaction.
– Product Collection: Products are collected at the reactor’s outlet.
Applications
Fixed bed reactors are used in the chemical and petrochemical industries for processes such as hydrogenation, oxidation, and synthesis gas production. They are also used in environmental applications for catalytic converters and air pollution control.
High-Pressure Reactors
High-pressure reactors are designed to operate at elevated pressures, making them suitable for reactions that require high-pressure conditions. These reactors are typically constructed from materials that can withstand high pressures, such as stainless steel or titanium.
Operating Principles
– Pressure Control: The reactor is equipped with pressure control systems to maintain the desired pressure.
– Temperature Control: The reactor may have heating or cooling systems to control the temperature.
– Agitation: An agitator ensures uniform mixing and temperature distribution.
Applications
High-pressure reactors are used in the chemical and pharmaceutical industries for reactions such as hydrogenation, polymerization, and supercritical fluid extraction. They are also used in materials science for synthesizing high-performance materials.
Microwave Reactors
Microwave reactors use microwave radiation to heat the reaction mixture, providing rapid and uniform heating. These reactors are particularly useful for reactions that require precise temperature control and fast heating rates.
Operating Principles
– Microwave Heating: Microwave radiation heats the reaction mixture.
– Temperature Control: The reactor is equipped with temperature sensors and control systems.
– Agitation: An agitator ensures uniform mixing.
Applications
Microwave reactors are used in organic and inorganic synthesis, polymer chemistry, and materials science. They are also used in the pharmaceutical industry for rapid synthesis and optimization of drug compounds.
Key Components of Laboratory Reactors
Laboratory reactors consist of several key components that work together to ensure efficient and controlled reactions. These components include the reactor vessel, agitator, heating and cooling systems, pressure control systems, and control systems.
1. Reactor Vessel
The reactor vessel is the central component of a laboratory reactor, where the reaction takes place. It can be made from various materials, such as borosilicate glass, stainless steel, or specialized alloys, depending on the application and the materials being processed.
Features
– Material: The choice of material depends on the chemical resistance and temperature requirements.
– Volume: Reactor vessels come in various sizes, from small laboratory-scale vessels to large industrial-scale vessels.
– Design: The design of the vessel can vary, including cylindrical, spherical, or custom shapes.
2. Agitator
The agitator is responsible for mixing the reactants and ensuring uniform temperature and concentration distribution within the reactor vessel. Different types of agitators are used depending on the viscosity and nature of the reactants.
Types
– Impellers: Commonly used for low to medium-viscosity fluids.
– Anchor Agitators: Suitable for high-viscosity fluids and pastes.
– Turbine Agitators: Used for high-shear mixing and dispersion.
3. Heating and Cooling Systems
Heating and cooling systems are essential for maintaining the desired temperature within the reactor vessel. These systems can include electric heaters, steam jackets, or cooling coils.
Features
– Temperature Control: Precise temperature control is crucial for many reactions.
– Heating Methods: Options include electric heaters, steam, and high-temperature heat transfer fluids.
– Cooling Methods: Options include water jackets, cooling coils, and refrigeration systems.
4. Pressure control systems
Pressure control systems are used to maintain the desired pressure within the reactor vessel, especially in high-pressure reactors. These systems include pressure sensors, relief valves, and pressure regulators.
Features
– Pressure Sensors: Monitor the pressure within the reactor vessel.
– Relief Valves: Prevent overpressure by releasing excess pressure.
– Pressure Regulators: Maintain a constant pressure within the reactor.
5. Control Systems
Modern laboratory reactors are equipped with advanced control systems that allow for precise monitoring and adjustment of various parameters, such as temperature, pressure, and agitation speed. These control systems often feature user-friendly interfaces and programmable recipes for consistent and repeatable processes.
Features
– User Interface: Touchscreen displays and control panels for easy operation.
– Programmable Recipes: Allow for the automation of complex processes.
– Data Logging: Record and store process data for analysis and optimization.
Applications of Laboratory Reactors
Laboratory reactors are used in a wide range of applications across various industries, including pharmaceuticals, chemicals, food and beverages, and materials science.
1. Pharmaceutical Industry
In the pharmaceutical industry, laboratory reactors are used for the synthesis and optimization of drug compounds. They are essential for developing new drug formulations, scaling up production processes, and ensuring product quality and consistency.
Applications
– Drug Synthesis: Batch and continuous reactors are used for synthesizing active pharmaceutical ingredients (APIs).
– Formulation Development: Reactors are used for developing and optimizing drug formulations, such as tablets, capsules, and injectables.
– Process Optimization: Laboratory reactors help optimize reaction conditions, such as temperature, pressure, and agitation, to improve yield and purity.
2. Chemical Industry
The chemical industry relies on laboratory reactors for the development and optimization of chemical processes. These reactors are used for synthesizing specialty chemicals, intermediates, and polymers.
Applications
– Specialty Chemicals: Batch and continuous reactors are used for producing specialty chemicals and intermediates.
– Polymerization: Reactors are used for polymerization processes, such as the production of polyethylene, polypropylene, and polystyrene.
– Catalysis: Laboratory reactors are used for studying catalytic reactions and developing new catalysts.
3. Food and Beverage Industry
In the food and beverage industry, laboratory reactors are used for developing and optimizing food products, such as sauces, dressings, and beverages. They are also used for studying food processing techniques and improving product quality.
Applications
– Product Development: Reactors are used for developing new food products and formulations.
– Process Optimization: Laboratory reactors help optimize food processing techniques, such as mixing, homogenization, and pasteurization.
– Quality Control: Reactors are used for studying the effects of different processing conditions on product quality and shelf life.
4. Materials Science
Laboratory reactors play a crucial role in materials science for synthesizing and studying new materials, such as nanomaterials, composites, and high-performance polymers. They are used for developing new materials with improved properties and performance.
Applications
– Nanomaterials: Reactors are used for synthesizing nanomaterials, such as nanoparticles, nanowires, and nanotubes.
– Composites: Laboratory reactors help develop and optimize composite materials with enhanced mechanical, thermal, and electrical properties.
– High-Performance Polymers: Reactors are used for synthesizing high-performance polymers, such as polyimides, polyamides, and polyurethanes.
Laboratory reactors are versatile and essential tools in scientific research, product development, and process optimization. They come in various types and designs, each tailored to specific applications and requirements. From batch reactors to continuous stirred tank reactors, plug flow reactors, and specialized high-pressure and microwave reactors, these machines provide controlled environments for conducting a wide range of chemical reactions and processes. With advanced control systems and key components such as reactor vessels, agitators, heating and cooling systems, and pressure control systems, laboratory reactors ensure efficient and consistent mixing, dispersing, and homogenizing processes.
Welcome to send inquiry to us and let’s make a win win business together !
Guidelines For Chemical Reactor
FRANLI has several complete Chemical reactor production lines. Our Chemical reactor adopts the latest infinitely variable speed reducer device, the sealing device can be a mechanical seal, and the heating and cooling can adopt the structure of a jacket, half pipe, fan coil, etc., The heating methods include steam, electric heater, and high-temperature heat transfer oil to achieve different safe processing environments such as acid resistance, heat resistance, wear resistance, and corrosion resistance.
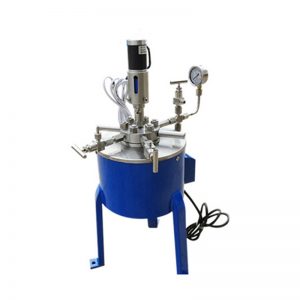
Laboratory Reactor: Guide to Stirring System
The laboratory reactor is composed of a pot body, a pot cover, an agitator, a jacket, a support and transmission device, a shaft seal device, etc.
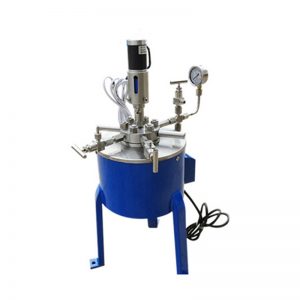
Overview of Laboratory Reactor
Laboratory reactors, also known as lab reactors, are essential tools in scientific research, product development, and process optimization. These reactors provide a controlled environment for conducting chemical reactions, mixing, dispersing, and homogenizing processes.
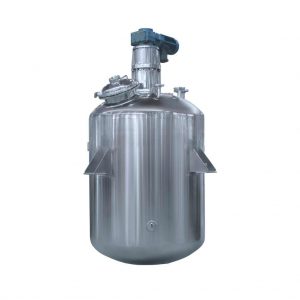
What is A Stainless Steel Reactor?
Stainless steel reactors are essential equipment in various industries, including chemical, pharmaceutical, biotechnology, and food processing.
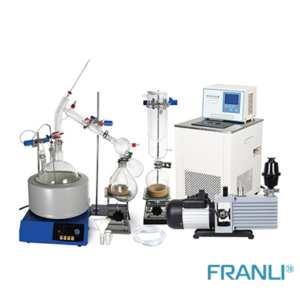
Glass Reactor & Chemical Equipment
Glass reactors are essential equipment widely used in the chemical, pharmaceutical, and biotechnology industries. They come in various types, suitable for different applications.
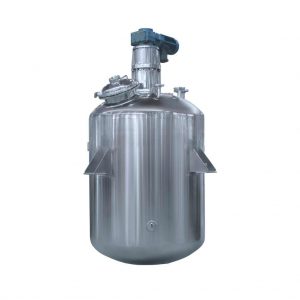
Operating Guide for Laboratory Reactors
Laboratory reactors play a crucial role in chemical research and development. Understanding the proper operating procedures is essential to ensure accurate results and maintain a safe working environment.
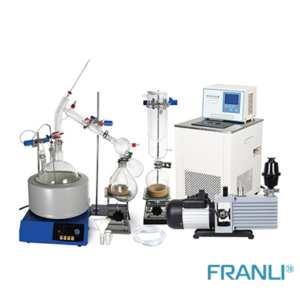
Glass Reactors and Selection of Stirring Blades
Glass reactors, also referred to as glass reaction vessels, are vessels made from high-quality borosilicate glass material.