Home » High-temperature kneader
High-temperature kneader
Kneader
Details of Kneader
- The machine comprises a motor, cover press, main body, mixing chamber and rotor mechanism, gearbox, air control system, tilting machine, heating/cooling system, rubber belt transmission and base, etc.
- The kneader can be made into vacuum, pressure, atmospheric, Normal temperature, high temperature, low temperature, etc.
- The temperature adjustment method of a kneader can be the jacket, halfpipe, far-infrared tile, steam, hot water, heat transfer oil, electric heating, cooling water, chilled water, and other methods.
Application: Paint, Adhesive, Battery, Pharmaceutical industry, Cosmetic
The kneader is equipped with a double U-shaped barrel, and the whole shape is similar to an inverted “m” shape. The intersection of this type of cylinder forms a ridge on the surface, which is a very distinctive model. The conventional cylinder is mainly made of low carbon steel or stainless steel 304, 316L. The ordinary kneader has no jacket because it does not need heating or cooling. The heating-type kneader has no jacket because it uses an electric heating wire for heating.
The heating-type kneader is loved by many users or factories. The kneader can be designed as heating or non-heating according to the needs of the material. The general heat exchange methods usually include electric heating, steam heating, circulating hot oil heating, circulating water cooling wait. The discharge methods of the high-temperature kneader include hydraulic cylinder dumping, ball valve discharge, screw extrusion, etc. The parts of the cylinder body and paddles in contact with the material are made of SUS304 stainless steel to ensure the quality of the product.
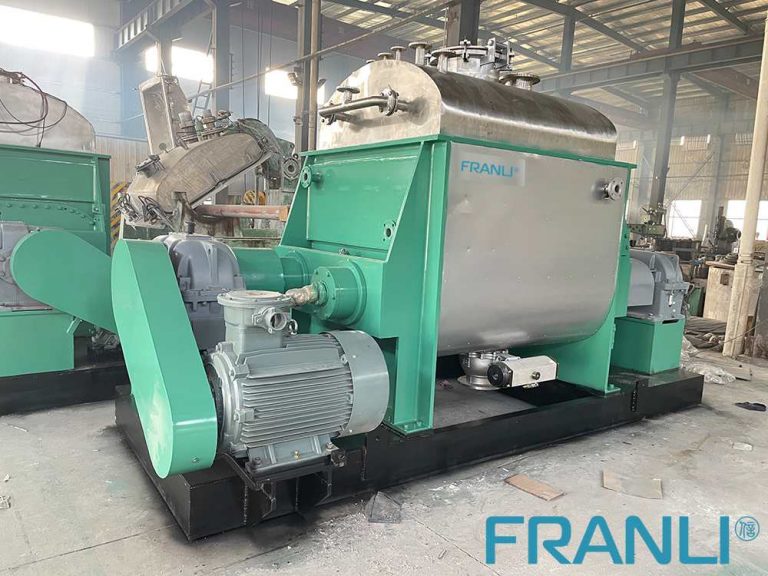
The structure of high-temperature kneader
The high-temperature kneader is composed of six parts: kneading part, machine base part, hydraulic system, transmission system, heating system, and electric control system; the electric control system includes manual and automatic electric control systems, which can be selected and requested by the user at will, easy to operate, reliable. The high-temperature kneader is equipped with the most advanced hydraulic system. This system is mainly controlled by a hydraulic station to complete the opening and closing functions of the large oil cylinder. Not only that, the hydraulic station can also be used to complete functions such as turning over the cylinder and opening the cover. For the detailed parameters of the kneader, the user can make a variety of choices according to the needs of the material.
The transmission system is composed of a motor, a reducer and a gear. Generally, kneader manufacturers will select a suitable motor according to the model. During the transmission process, the synchronous speed can be achieved by the motor, and after passing through the elastic coupling to the reducer, the output device can drive the fast paddle to make it reach the regular speed, and the frequency converter can also stop the speed.
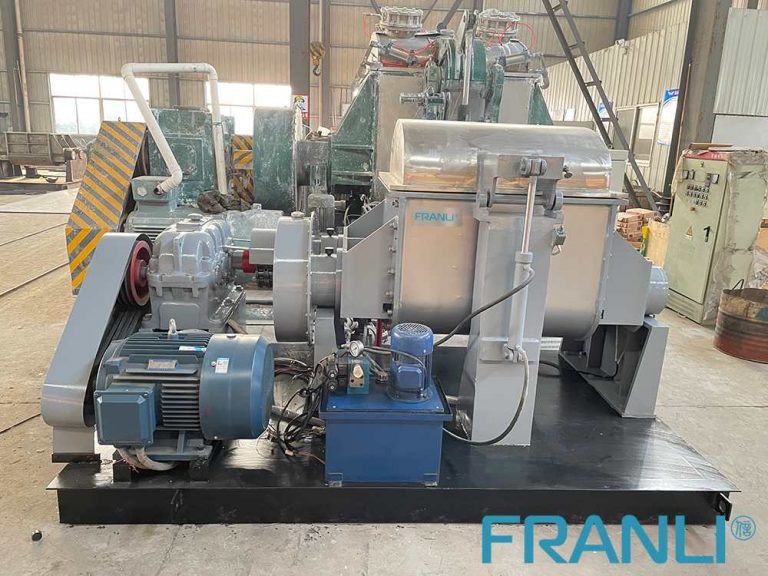
The high-temperature kneader is the same as the conventional kneader. It is composed of a pair of blades that cooperate with each other and rotate through high-speed stirring (usually Z-shaped) to generate intense shearing action, so that the semi-dry state or gelatinous thin plastic Materials, through efficient and uniform mixing and kneading, to obtain uniform and fine materials. The high-temperature kneader is mainly used for flame retardants, and can also be used for other chemical products.
The mixing parts of the kneader are mainly two Z-shaped steel-cast stirring paddles, and the stirring paddles rotate in opposite directions at different speeds (usually 3:2). When the material is put into the barrel of the kneader by the worker, it is squeezed between the two stirring paddles, the side wall and the ridge-like parts, resulting in shearing, stretching, folding, separation and recombination. Through the combined effect of the above, materials with high viscosity can be fully mixed.
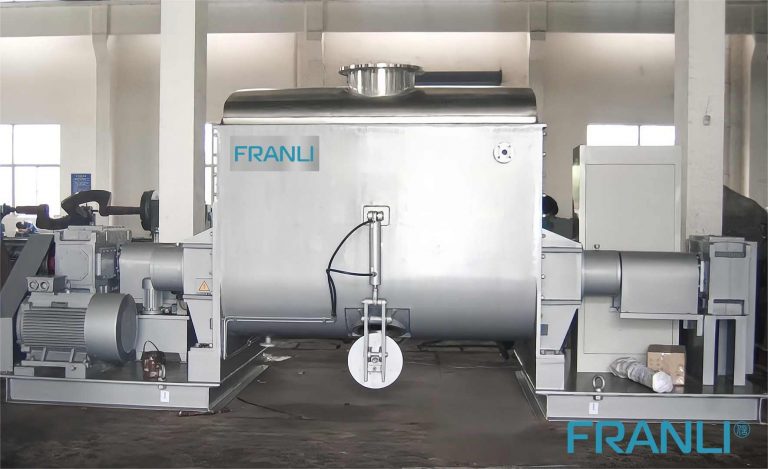
Construction characteristics of the kneader
Ordinary machines use a common chassis, which is easy to install, and use a cycloidal pin wheel or a hard-tooth surface reducer to make the transmission with the main machine stable, with low noise and long life. The stirring paddle and the inner wall of the mixing tank are made of SUS304 stainless steel or SUS316L stainless steel to ensure the purity of the product. The shaft seal has advanced structure and good sealing effect. The balanced structure of the vacuum box is jointly designed to ensure that no black material will be ground out.
Selection skills of high-temperature kneader
Due to the difference in consumption fields and product raw materials, many aspects must be considered when purchasing mixers. Therefore, when purchasing, it is necessary to consider the budget of the product, the method of use, and the final effect of the material. When using this type of horizontal mixer, after the equipment is started, ensure that there is no problem with the machine, and then add materials batch by batch.
Choose the right kneader according to the daily output. Because the processing time of each batch of raw materials of the kneader is about 6 minutes, so adding the time of discharging and feeding materials, the processing time of each of raw materials can be calculated as 10 minutes, and then 6 batches of materials can be processed in 1 hour. If you choose a mixer with a processing capacity of 100 kg per batch, it can process 600 kg per hour. Customers can choose the most suitable high-temperature kneader according to their needs.
As a professional kneader manufacturer, FRANLI has provided a complete set of mature equipment for related machines and production lines for more than 60 countries and thousands of industries in the world, and in Russia, Turkey, Spain, Brazil, Malaysia, Indonesia, and other regions, it has provided many An enterprise establishes related production lines.
Welcome to send inquiry to us and let’s make a win win business together !
Guidelines For Kneader
The dispersion kneader is suited for rubber and plastic mastication, as well as the blending of different rubber and plastic components. Small and medium-sized rubber and plastics manufacturers with a wide range of product types and colours, as well as food, dyes, pharmaceuticals, and ceramics, can benefit from the internal mixer.
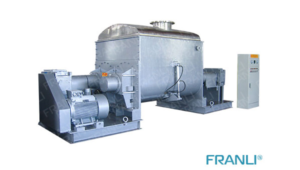
Sigma Kneader: The Solution for Mixing and Kneading
Sigma kneader is a versatile machine that can be used for mixing, kneading, and homogenizing a wide range of materials, including high-viscosity products.
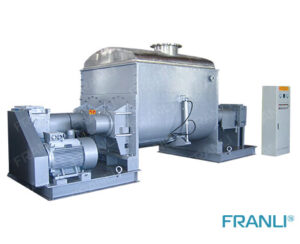
Sigma Mixer: Indispensable Equipment For Manufacturing
Sigma Mixer is a type of mixer that uses a unique mixing principle to achieve an efficient blending of materials. The mixer consists of two blades that rotate in opposite directions, creating a kneading and folding action that ensures thorough mixing. The blades are shaped like the Greek letter Sigma, hence the name Sigma Mixer.
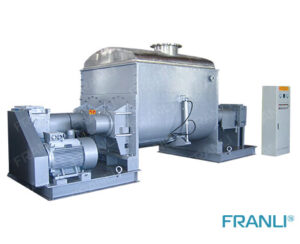
Sigma Blade Mixer: The Mixing Solution
The Sigma Blade Mixer is a robust and reliable mixing machine that uses a unique mixing principle to achieve superior results. It is a type of double-arm kneading mixer that features two blades that rotate in opposite directions.
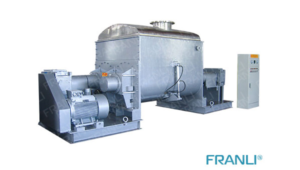
Vacuum Kneader: A Machine for Your Mixing Needs
The Vacuum Kneader is a type of mixer that utilizes a vacuum chamber to create a homogeneous mix of ingredients. It is designed to knead, mix, and disperse high-viscosity materials under vacuum conditions, resulting in a superior product.
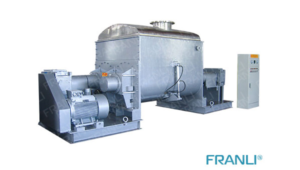
Efficiency and Effectiveness of Dispersion Kneader
The dispersion kneader has complete control over the mixing and blending of the raw materials to create an even mix that allows for better distribution. This device contains a mixing chamber with rotating blades made of high-quality steel.
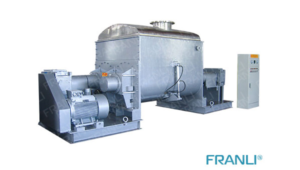
Vacuum kneader: high efficiency and environmental protection
A vacuum kneader is mainly used for stirring, mixing, and kneading high-viscosity and elastic-plastic materials. The most common fields include high-viscosity sealant, silicone rubber, neutral acid glass glue, chewing gum, bubble gum, aluminum silver paste, silica gel, paper pulp, cellulose, and other materials. It covers food, agrochemical, pharmaceutical, cosmetics, electronic paste, and other industries, and has been sought after by the industry.