Home » Ink production line
Ink production line
Ink production line
The production of ink is generally composed of resins, pigments, solvents, and additives. Generally, the ink industry is mainly distinguished according to whether it contains pigments. It is generally divided into materials containing colors and materials without colors. Colored inks containing pigments (including white, and black), non-pigmented thinners, gilt oils, and varnishes.
The formula of the ink is directly related to its application, storage performance, and production process of the ink production line. Therefore, the production of ink in general factories is to disperse the various ingredients in the formula effectively and permanently as far as possible. Among them, pigment is the most difficult to disperse uniformly. Pigment dispersion and grinding are the core of ink production.
The main equipment of the ink production line
The main equipment of the ink production line includes material storage tanks, barrels, multi-model dispersing machines, chemical reactors, sand mills, three-roll mills, material operating platforms, filling machines, electronic process control systems, process pipelines, air compressors, A set of equipment such as cleaning equipment.
1. Ink production line | multi-style dispersing machine
There are many kinds of dispersing machines used in ink, such as high-speed dispersing machines, biaxial dispersing machines, etc. The dispersing machine is a device that disperses liquid or liquid-solid media by using the shear force generated by a high-speed rotating stainless steel turntable. The usual dispersing machines are single-rod (one turntable), and there are also double-rod (staggered arrangement, each pole has a turntable at the end), and the dispersion effect is better.
1.1 Operation of Disperser
Before using the disperser, check whether the circuit is normal and whether the speed regulating valve is reset to zero.
Fix the material tank, inject solvent, and lower the stirring plate, after it is in place, turn on the motor, rotate at low speed, and add resin, pigment, and other solid materials according to the process, after adding, increase the rotation speed. When adjusting the speed, the action should be slow, and the speed control knob should not be rotated quickly to prevent accidents.
After the material is dispersed, reduce the speed to stop, start the up button, and stop rising when the dispersing disc leaves the liquid surface, and then turn on the medium speed to throw off the material on the dispersing disc, then stop rotating, and rise until the cylinder can be pushed out.
The dispersing plate should be cleaned in time after use.
2. Ink production line | chemical reactor
The chemical reactor is a reaction vessel with design and operation functions, such as heating, cooling, and temperature control functions. The chemical reaction kettle generally has a strong pressure. The pressure has the functions of normal pressure, positive pressure, and negative pressure. It can complete multiple operations such as stirring, dispersing, solvent recovery, and reflux of materials. The design and operation are flexible, mainly based on the flexibility of the production process master.
2.1 Operation of the chemical reactor
The operation of the chemical reactor is relatively simple. We will provide a complete set of instruction manuals, which include but are not limited to the use, maintenance, maintenance, and precautions of the chemical reactor. Operate according to the instructions for use.
3. Ink production line | sand mill
The sand mill is a device that uses hard and wear-resistant zirconia beads, glass beads, etc. to rotate in a closed cavity to grind pigments. There are many types of sand mills, generally divided into horizontal type, vertical type, and basket type according to the shape.
3.1 Operation of the sand mill
When using a sand mill, you first need to ensure that the electricity, cooling water supply, and the amount of zirconium beads are sufficient. Then the user needs to place the suction pipe in the dispersed material to be ground and then turn on the sand mill. The temperature cannot exceed the process temperature, and the number of grinding depends on the fineness specified by the process. When the material reaches the final requirement, use the solvent and resin liquid specified by the process to push it out of the material in the cavity. Finally, after the machine is used, the user needs to clean it in time.
4. Ink production line | a three-roll mill
The three-roll mill is also used to grind ink. The three-roll mill mainly has three rollers installed at the same horizontal position. Under the extrusion of different speeds, it uses its strong shear force to disperse and grind the pigment.
4.1 Operation of the three-roll mill
When using a three-roll mill, the user needs to first check whether the electricity and cooling water are in good condition. Then adjust the distance between the rollers (leave a little gap) according to the fineness of the material to be ground, and clamp the scraper and the baffle. The user can pour the material into the feeding roller, start the machine again, and adjust the distance between the rollers and the tightness of the scraper again so that the ground material can flow out into the receiving barrel stably and evenly.
After the material is ground, the user needs to check whether its fineness meets the specifications. When the fineness is not enough, it needs to be ground again until it meets the requirements.
When the three-roll mill is working, do not put items such as blades and cloth on the roller shaft. Once involved, it will not only lock the three-roll grinder but also cause personal safety problems. (Very serious consequences).
FRANLI is a professional ink production line manufacturer, and we design the production ink production line, ink production complete sets of equipment, including a high-speed disperser, temperature-controlled stainless steel reactor, bead mill, filter, filling machine, three-roll mills, supporting workbenches, integrated control systems and other complete sets of equipment have been exported to Russia, Turkey, Egypt, Brazil, Malaysia, Indonesia, Spain, etc.
Welcome to send inquiry to us and let’s make a win win business together !
Guidelines For Production Line
FRANLI has several sets of wet grinding production lines, including PCB ink production line, ink production line, pesticide production line, automobile coating production line, etc.
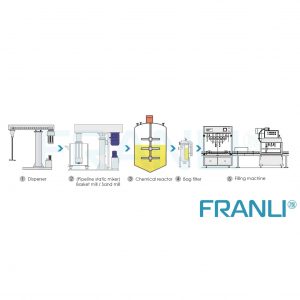
Pesticide Production Line
The production of pesticides mainly uses sand mills, emulsifiers, chemical reaction kettles, twin-shaft mixers, filling machines, and other equipment. This equipment thus constitutes a complete set of pesticide production lines, from the grinding and storage of particles to the reaction and Blending, and finally filling and packaging, the FRANLI pesticide production line is fully intelligent, with the characteristics of simple operation, safety, and stability.
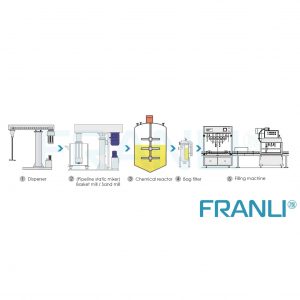
Gravure Ink Production Line: manufacturing process
The gravure ink production line is a professional manufacturing process that requires attention to detail and a commitment to quality.
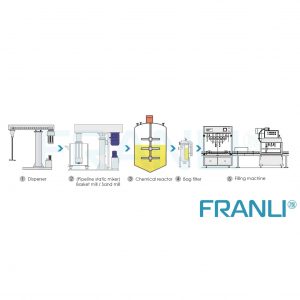
Printing ink production line
FRANLI Printing ink production line mainly takes intelligence, environmental protection, and high production efficiency as the main production standards.
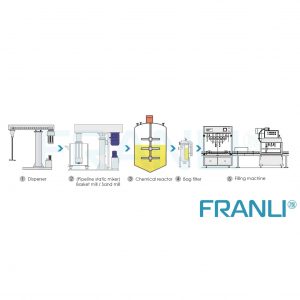
Water Ink Make equipment & production line
FRANLI water ink complete set of equipment and production line is mainly composed of an intelligent batching system, high-speed dispersion pulping system, metering system, horizontal grinding series system, multi-functional mixing and coloring system, cleaning system, automatic control system, automatic filling system, and other parts. Advanced production technology.
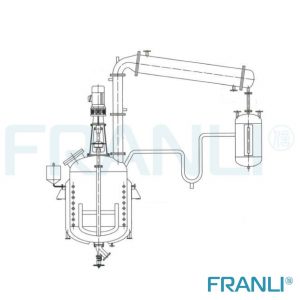
Resin Production Line & Complete Manufacturing Equipment
FRANLI provides complete sets of resin manufacturing equipment and production lines, which are mainly suitable for the synthesis of various chemical resins, such as unsaturated polyester resin, phenolic resin, epoxy resin, alkyd resin, ABS resin, etc. It can also be used for the manufacturing and production of Various types of emulsion resins, such as acrylic resin emulsion, etc.
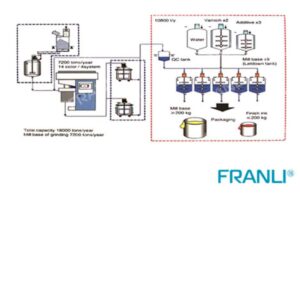
Ink production line
The main equipment of the ink production line includes material storage tanks, barrels, multi-model dispersing machines, chemical reactors, sand mills, three-roll mills, material operating platforms, filling machines, electronic process control systems, process pipelines, air compressors, A set of equipment such as cleaning equipment.