Home » Dyno Mill Manufacturers & Suppliers
Dyno Mill Manufacturers & Suppliers
Dyno mill
Details of Dyno mill
- The frame of the Dyno mill
- Grinding system of Dyno mill
- Double mechanical seal of Dyno mill
- The transmission system of the Dyno mill
- Grinding cylinder of Dyno mill
Application: Paint, Adhesive, Battery, Pharmaceutical industry, Cosmetic
Every application’s mill equipmachinement, material, and grinder bead separating system may be customised to meet its specific requirements. Every other production process contributes to the end freshness. Grinding is an important part of a wide range of operations. Gone are the times when these processes could only be carried out by a working population. Machines are now available to perform all of those complicated operations that appear to be impossible to conduct manually.
The Dyno Mill is an excellent instrument for grinding and dispersing. The horizontal grinding container of this agitator bead mill facilitates dispersion as well as fine wet grinding. This whole process takes place inside a contained system to prevent materials from spilling out. Grinding is crucial in the realm of industrial material processing. As a result, the Dyno Mill Machine is a necessary piece of equipment.
The Dyno Mill may be used in a variety of ways:
● Industry of Ink
● Pigmentation and dyeing materials
● Industry of paint
● Industry of Food
● Tape coating for audio and video
● Coating for thermal and fax paper
● Paper and plastics industry fillers
● Industry of pharmaceuticals
FRANLI has established itself as a leading dyno mill suppliers and distributor, offering a diverse selection of dyno mills as well as other goods including such Planetary Mixers, Drum Lifters, and Containers. In order to satisfy our customer, the firm employs new and modern technology in the creation of this product. Every one of our products is meticulously developed to fit the particular needs and desires of our consumers, and the materials used throughout the design are sourced from reputable market suppliers. FRANLI is committed to producing high-quality goods in terms of fulfilling the increasingly complicated needs of industry.
The Dyno Mill is ideal for pumping a wide range of viscosity materials from bottom to top viscosity. Dyno Mill’s flexible characteristic allows it to be used in the manufacture of paint, ink, food, pharmaceuticals, pigments, and colourant. It is a genuinely dependable appliance due to its high consistency. In addition, this programme is simple to use. The Dyno Mill comes in a range of sizes to accommodate the various duties that each business requires. Various materials are utilised depending on the mill’s length & original intent. Wear components are made of composite materials, alloy steels stainless, and highly polished alloy steels, to name a few materials.
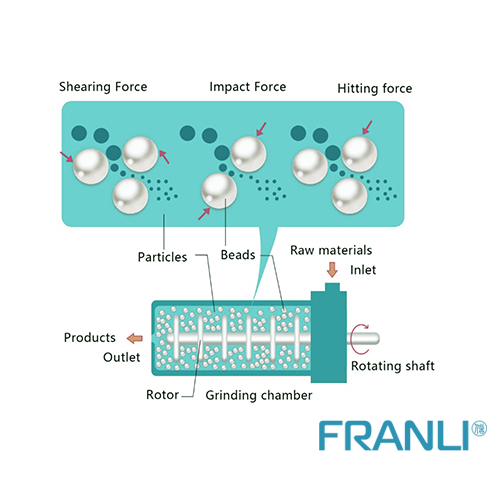
Dyno Mill is an excellent choice for variable amounts and wet milled down to nanoparticle size. When expertly crafted from high-quality components, a machine produces outstanding results. It might be difficult to find one that meets your demands while remaining within your dyno mill price. Choose a reputable dyno mill manufacturers India when compromising is not an option. Their primary goal is to ensure that all potential clients are completely satisfied. They provide a vast selection of sophisticated Dyno Mills to satisfy a wide range of requirements.
Dyno Mill’s major characteristics, as created by professional manufacturers, are as follows:
● Exceptional wear resistance
● Materials of the highest quality were used to create this product.
● Life span would be more
● As a result, product processing is enhanced.
● The arrangement of the agitator discs and the grinding container is excellent.
● Capable of easily handling extremely viscous products
● The ability to crush materials down to the nanoscale scale
● Handling is simple.
The principle of dyno mill
The dyno mill working principle is a closed cycle agitating beads mill with such a horizontally grinder vessel for dispersing and finer wet crushing. The dyno mill can handle a wide range of materials, from light to extremely sticky pumpables. The liveliness necessary for dispersing and moist granulating is transferred to the spherical crushed blobs by specially constructed initiator rings placed vertically on a pole. The material is fed into the mill by some outsource construction.
The Range of dyno mill
DYNO-Mills are available in various designs and sizes, ranging from tiny laboratories mills to huge mills for manufacturing facilities, ensuring that the right capacity is accessible for any purpose. Mill equipment, materials, and the milling bead separating system may all be customised to meet the specific requirements of every project.
The Modular construction of dyno mill
Dyno Mill suppliers and equipment that come into touch with the products and worn out are changed and come in a variety of materials. Mills that have been in operation may be quickly converted thanks to the modular design.
The Grinding containersn of dyno mill
The grinder container’s compact design ensures a limited resident time dispersion. The spiraling flow of the cooling system in the outer cover achieves the highest cooling capacity, allowing the production of very viscous thermal goods.
The Grinding beads of dyno mill
Grinding beads, glass or plastic, ceramic, or steel range in size from 0.15 mm to 3.0 mm, depending on the functional and mill capacity. The size and kind of grinding beads have a direct impact on the grinding outcome.
The Materials of dyno mill
The materials utilised are determined by the mill’s capacity and original intent. Alloy steels stainless, powder – coated enamelled, tungsten carbide, and synthetic products can all be used to make wear components. Wear components made of high-quality sintered materials or ceramic can be provided for pesticide dispersing and grinding mills up to 60 litres.
The Electrical Control of dyno mill
The mill is equipped with switches for local democracy of motors starting and indicators for measuring running conditions. The mill’s security restrictions are established and according to applications.
The Advantages of dyno mill
● System that is completely enclosed
● Maximum efficacy
● It’s simple to use and maintain.
● Optimal grinding container and agitator disc geometry
● Every application requires the right mill size.
● Wear components in touch with the product might be made of a variety of materials.
● Applicability fields.
Only with the aid of Dyno Mill, the grinding process could now be carried out at the top level. Change to the appropriate solutions and machinery to guarantee that the intended quality of goods is produced as per the requirement. Get these today for a reasonable price.
FRANLI is using the most appropriate, easy-to-operate, and safe functioning design. From selling a few machines to a complete line, to a spin project. We have such a technological customer service team based in another country. We want to inspire the companies we meet by demonstrating that it is possible to offer happiness, positivity, and sunshine to customers, workers, vendors, and service partners all at the same time. We are forming a team by sharing the same spirit dream. To develop and design machines.
Welcome to send inquiry to us and let’s make a win win business together !
Guidelines For Bead Mill
Bead Mill(sand mill) helps many factories to improve production. Grinding for low viscosity, well-flowing material. Self-cycling cooling system. Don’t need the cooling pump. Franli produces Disc Bead Mill, Pin Bead mill, Turbine Nano Bead mill, etc. Optional material of inner chamber and disc: hardness Alloy, Zirconia, PU.
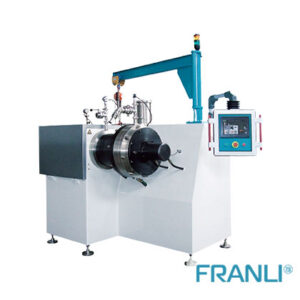
DYNO MILL – A DYNAMIC WAY TO GRIND EASIER
Dyno mill is nothing but an agitator bead mill. It is widely used in the production of paints, coatings, agrochemistry, and pharmaceutical products.
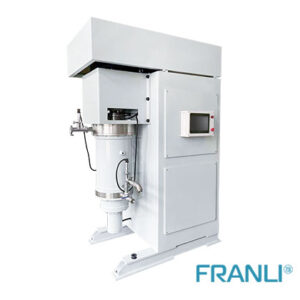
Role of Pearl Mill in the Nano Industry
Pearl Mill can handle both high and low viscosity materials. One is for Nano grinding materials, while the other is for high viscosity materials like offset ink. The operation of the Pearl Mill is straightforward, and all maintenance; may be handled quickly and efficiently. Adding grinding media from the feeding hole is simple.
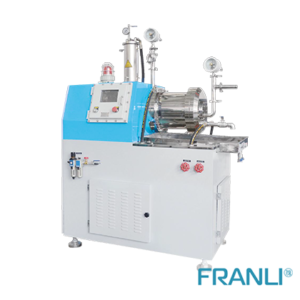
Guide to Bead Mills
The Bead mill is one of the main grindings and dispersing equipment in paint production. Bead mills for coatings are mainly divided into four categories: vertical, horizontal, basket, and special-shaped bead mills.
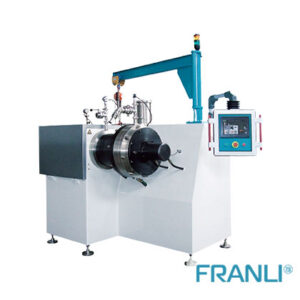
Dyno Mill|Coating & Inks
Dyno mill is a type of bead mill machine which is used in the coating industry specifically, in the manufacturing of inks products.
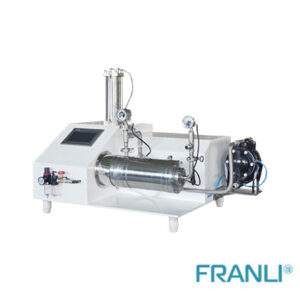
The structure and type of laboratory bead mill
The laboratory bead mill in the chemical experimental equipment, also known as the lab sand mill, is a kind of grinding equipment compared with the bead mill for industrial production.
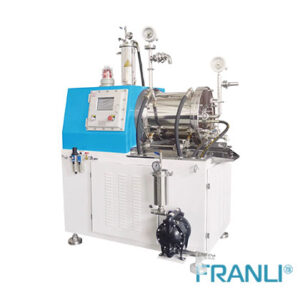
High Viscosity Material Grinding – Bar Pin Bead Mill
The bar pin bead mill is a machine suitable for ultra-fine dispersion and nano-scale grinding of water-based and solvent-based materials. The bar pin bead mill is one of the most widely used production types of equipment. With its very stable performance and sophisticated technology, it has been recognized by a wide range of users. The key thing to know is the characteristics of the bar pin bead mill, which is also the key to people’s favor of it.