Home » What is a Double Planetary Mixer?
What is a Double Planetary Mixer?
Double Planetary Mixer
Double Planetary Mixer is a new type of dispersion equipment with high efficiency, complete functions, and compulsory mixing. The double planetary mixer consists of a geared motor, a planetary carrier, an agitator, a wall scraper, a barrel, a hydraulic lifting system, and a frame.
Details of Double Planetary Mixer
- The common agitators include paddle type, twist type, claw type, and frame type.
- good mixing, reaction, kneading, and dissolution functions.
Application:
inks, colorants, dyes, coatings, and other industries.
The structure of the double planetary mixer is relatively complicated. This machine combines the characteristics of the planetary mixer and the powerful disperser and fully integrates the advantages of these two pieces of equipment. It realizes both the high-speed dispersion function and the low-speed stirring function; Compared with the revolution and rotation of the impeller at a lower speed than the planetary mixer, it also adds a set of high-speed dispersing shafts, and a dispersing disc is arranged on it. During operation, it realizes self-rotation and revolution at the same time, and its speed can be adjusted by frequency control.
Working principle of double planetary mixer
After the double planetary mixer is started, the planetary frame will rotate accordingly, and drive the two stirring shafts in the box to rotate. While revolving around the axis of the barrel, it will rotate at high speed, so that the materials will receive strong shearing and kneading. To achieve the purpose of full dispersion and mixing. At the same time, there is a row of wall-scraping knives on the planetary frame that rotates with the planetary frame, clings to the cylinder wall, and scrapes continuously to scrape off the material on the cylinder wall so that there is no retained material on the cylinder wall.
Application range of double planetary mixer
Coatings, inks, aerospace polymer materials, battery pastes, food, chemicals, cosmetics, emulsions, pharmaceuticals, and other fields.
Advantages of double planetary mixer
High mixing efficiency and wide application range: generally suitable for high-viscosity mixing, ordinary double planetary mixers can handle 500,000 cps of materials, and special customized models can handle viscous materials up to 5 million cps, which can easily solve the production of viscous materials problem.
Convenient and safe operation: the material does not stick to the wall, the discharge is clean, and the barrel is easy to clean.
Strong non-standard: explosion-proof type, vacuum type, heating type, and can also be customized in terms of materials.
The high degree of automation: PLC programming control can be used to automatically monitor and control the temperature and speed in the tank. The revolution and rotation of the stirring paddle adopt frequency conversion speed regulation, and different speeds can be selected according to different processes and different viscosities.
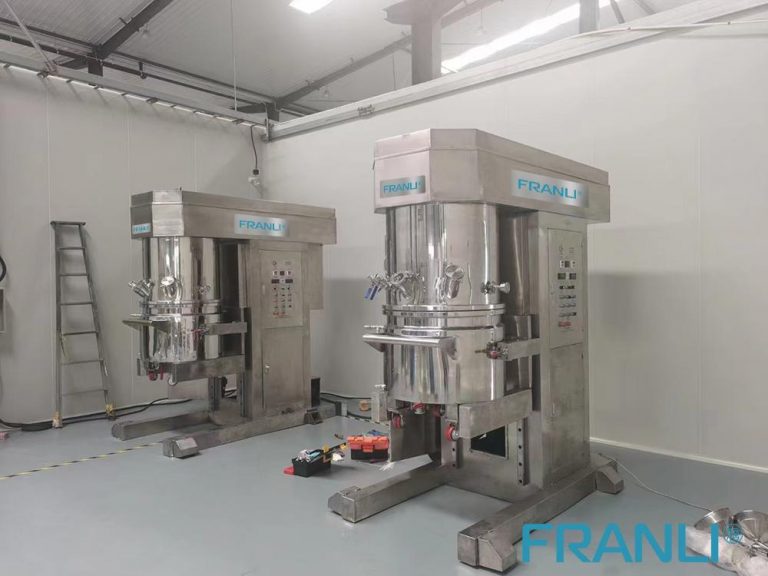
Features of double planetary mixer
1. The capacity is large enough
The manufacture of batteries requires more pole pieces and requires better consistency of batteries. This requires that the slurry needs a certain consistency. In the actual mixing process, the slurry in each pot will not be the same due to reasons such as stirring operation, time, and feeding sequence. The viscosity is not necessarily the same. Therefore, the mixer needs to have a certain capacity. At present, the large mixer can reach 2000L. When the capacity is large enough, the mixing ability and the mixing effect of materials must be considered.
2. Good vacuum sealing system
The mixer needs a good vacuum sealing system for three main reasons:
① During the whole stirring process, due to the frequent collision and friction between the materials, as well as the friction between the agitator and the materials, more heat will be generated and the temperature will rise. An increase in temperature will cause some solvents to emit and produce a strong pungent odor, such as NMP, PVDF, etc. Organic gases are very harmful to the human body.
② When the powder is in the dry powder premixing stage if the closed system is not good enough, the dust will be scattered, which will damage the working environment, affect the product quality and cause harm to employees.
③ There are large voids inside the powder, and after mixing with the solvent, there must be many bubbles inside the slurry. It is necessary to degas the slurry before coating the pole piece. Otherwise, the bubbles will burst during the coating process, the surface density will be different, and even the foil will be exposed, which is extremely detrimental to the performance of the battery.
3. The material of the mixer has strong corrosion resistance, wear resistance, and stable physical and chemical properties
Regardless of the strong alkalinity of the positive electrode material, the strong corrosion of NMP, etc., the mixer needs to have excellent corrosion resistance. During the stirring process, the continuous stirring of the powder by the agitator requires it to be wear-resistant and have a long enough service life.
4. The blade structure of the agitator is reasonable, and the agitation speed design meets the requirements.
In addition to sufficient stirring power and stirring range in the mixer, the shape and mechanical design of the mixer blades have a great influence on the slurry preparation. First of all, it must be ensured that the stirring range of the agitator is large enough, and there is no dead angle in the stirring container. Two-shaft or even three-shaft planetary agitators are currently used in larger mixers to ensure that no fines or lumps of active material are mixed uniformly into the slurry.
Secondly, the shape design of the agitator has an absolute influence on the dispersion, mixing, particle size distribution, fluidity, etc. of the material. At present, the common shapes on the market include paddle type, butterfly type, anchor type, twist type, claw type, frame type, etc. Among the equipment, it is best to be equipped with high-speed dispersion equipment, because some materials require high-speed shear force to disperse them, so it is necessary. The third requirement is that the equipment has a stirring speed that meets the requirements to meet the requirements of high molecular weight and ultrafine powder dispersion.
In addition to the design of the main stirring shaft and blades, some equipment has designs such as scraper design and container rotation to improve the efficiency of stirring and the degree of mixing of materials.
5. The safety of the mixer
The safety design of the mixer must be reasonable, including equipment explosion-proof design, equipment safety emergency stop design and equipment stability, etc., so as not to cause harm to the operator.
Welcome to send inquiry to us and let’s make a win win business together !
Guidelines For Double Planetary Mixer
FRANLI is a professional double planetary mixer manufacturer. Our double planetary mixer is especially suitable for dissolving, mixing, kneading, and reacting from powder to high-viscosity and high-density materials. According to different viscosities and material characteristics, Choose the right stirring paddle, and provide supporting equipment and production lines for double planetary mixers.

Advantages and Applications Of Dual Planetary Mixer
A dual planetary mixer is a versatile and efficient machine that is used in various industries, including food, pharmaceuticals, and cosmetics.

How to buy a double planet mixer?
This double planetary mixer can mix all types of viscosity of the material in no time. This double planetary mixer contains high-capacity blades that can work from 1 million centipoises to 8 million centipoises.

Double Planetary Mixer For Sale
FRANLI double planetary mixer is a high-efficiency, multi-purpose, and no-dead angle mandatory mixing and dispersing equipment.

Electronic Slurry & Double Planetary Mixer
Double planetary mixers are widely used, especially in the field of electronic slurry, whether it is stirring or mixing, the final output effect has been recognized by all walks of life.
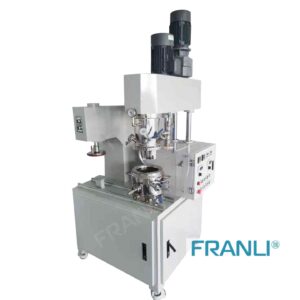
Double Planetary Mixer: Laboratory & Production
There are two types of double planetary mixers produced by FRANLI, which mainly involve two major application fields, one is laboratory research type, and the other is a factory production line

Structural Adhesive Production Equipment & Double Planetary Mixer
The double planetary mixer is one of the ideal types of equipment for low-viscosity materials. This facility has a low and fast mixing dispersing disc, which can complete the functions of high shear and dispersing low viscosity materials at the same time.