Home » The Application of Double Planetary Mixers for Battery Adhesives
The Application of Double Planetary Mixers for Battery Adhesives
Double Planetary Mixer
Battery adhesives play a crucial role in the structural integrity and performance of batteries. The mixing process of battery adhesives requires precision and efficiency to achieve a homogeneous and high-quality mixture. Double planetary mixers have emerged as a popular choice for this application due to their unique design and capabilities.
Details of Double Planetary Mixer
- The common agitators include paddle type, twist type, claw type, and frame type.
- good mixing, reaction, kneading, and dissolution functions.
Application:
inks, colorants, dyes, coatings, and other industries.
Double planetary mixers are a type of industrial mixing equipment specifically designed for handling viscous and high-density materials. They consist of two planetary blades that rotate on their own axes while revolving around a central axis. This dual rotation creates a highly efficient and thorough mixing action, ensuring the uniform distribution of ingredients throughout the mixture The design of double planetary mixers allows for precise control over the mixing process, resulting in consistent and high-quality adhesive formulations.
Advantages of Double Planetary Mixers in Battery Adhesive Mixing
Homogeneous Mixing: One of the primary advantages of double planetary mixers in battery adhesive production is their ability to achieve a homogeneous mixture. The dual rotation of the planetary blades ensures that all ingredients, including resins, fillers, and additives, are uniformly dispersed throughout the adhesive. This results in a consistent quality of adhesive, with improved bonding strength and performance.
Efficient Mixing of High-Density Materials: Battery adhesives often consist of high-density materials that can be challenging to mix effectively. Double planetary mixers are specifically designed to handle such materials, to their robust construction and powerful mixing action. The planetary rotation and revolution create a shearing and kneading effect, breaking down any agglomerates and ensuring thorough of the adhesive components.
Precise Temperature Control: Temperature control is crucial in battery adhesive production as certain adhesives require specific temperature ranges for optimal performance. Double planetary mixers offer precise temperature control through various heating and cooling options. The mixing vessel can be jacketed, allowing for the circulation of hot or cold fluids to maintain the desired temperature during the mixing process. This ensures that the adhesive remains within the specified temperature range, preventing any adverse effects on its properties.
Versatility and Flexibility: Double planetary mixers offer a high degree of versatility and flexibility battery adhesive mixing. The mixing speed and blade configuration can be adjusted to accommodate different adhesive formulations and viscosities. This flexibility allows manufacturers to adapt to production requirements and produce customized adhesive formulations for specific battery applications.
Reduced Mixing Time and Improved Efficiency: Double planetary mixers are known for their mixing capabilities, significantly reducing the overall mixing time. The dual rotation and revolution of the planetary blades create a powerful mixing action that accelerates the blending process. This not only improves production efficiency but also allows for higher throughput and shorter lead times.
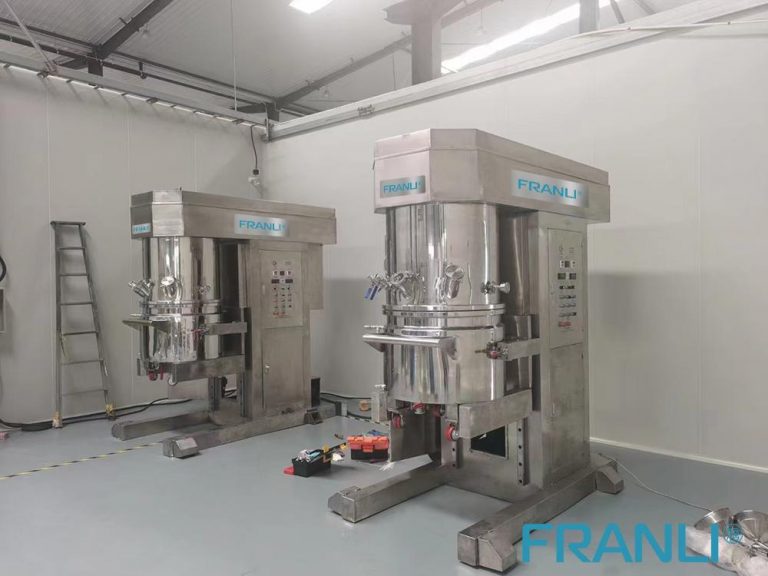
Double Planetary Mixers in Battery Adhesive Production
To illustrate the practical application of double planetary mixers in battery adhesive production let’s consider a case study of a battery manufacturing company. The company in producing adives for lithium-ion batteries, which require precise mixing to ensure optimal performance and safety.
FRANLI decides to invest in a double planetary mixer for their adhesive production process. The mixer is equipped with two planetary blades and a jacketed mixing vessel for temperature control. The adhesive components, including resins, fillers, and additives, are loaded into the mixer, and the mixing process begins.
The dual rotation and revolution of the planetary blades create a powerful mixing action, ensuring the uniform dispersion of the adhesive components. The jacketed mixing vessel allows for precise temperature control, maintaining the adhesive within the specified temperature range. The homogeneous mixture produced by the double planetary mixer meets the company’s stringent quality standards, ensuring the structural integrity and performance of the batteries.
Double planetary mixers have revolutionized the battery adhesive mixing process, offering numerous advantages over traditional mixing methods. Their ability to achieve a homogeneous mixture, efficient mixing of high-density materials, precise temperature control, versatility, and reduced mixing time make them an ideal choice for battery adhesive production. The case study presented in this essay demonstrates the practical application of double planetary mixers in a battery manufacturing company, highlighting their effectiveness in producing high-quality adhesive formulations. As the demand for batteries continues to rise, double planetary mixers are likely to play an increasingly important role in battery adhesive production, contributing to the development of efficient and reliable energy storage solutions.
As a professional double planetary mixer manufacturer, FRANLI provides a complete set of mature equipment for related machines and production lines for more than 60 countries and thousands of industries in the world, and in Russia, Turkey, Spain, Brazil, Malaysia, Indonesia, and other regions, for Many enterprises have established related production lines.
Welcome to send inquiry to us and let’s make a win win business together !
Guidelines For Double Planetary Mixer
FRANLI is a professional double planetary mixer manufacturer. Our double planetary mixer is especially suitable for dissolving, mixing, kneading, and reacting from powder to high-viscosity and high-density materials. According to different viscosities and material characteristics, Choose the right stirring paddle, and provide supporting equipment and production lines for double planetary mixers.

Advantages and Applications Of Dual Planetary Mixer
A dual planetary mixer is a versatile and efficient machine that is used in various industries, including food, pharmaceuticals, and cosmetics.

How to buy a double planet mixer?
This double planetary mixer can mix all types of viscosity of the material in no time. This double planetary mixer contains high-capacity blades that can work from 1 million centipoises to 8 million centipoises.

Double Planetary Mixer For Sale
FRANLI double planetary mixer is a high-efficiency, multi-purpose, and no-dead angle mandatory mixing and dispersing equipment.

Electronic Slurry & Double Planetary Mixer
Double planetary mixers are widely used, especially in the field of electronic slurry, whether it is stirring or mixing, the final output effect has been recognized by all walks of life.
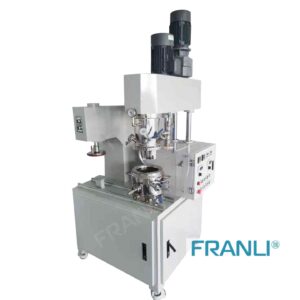
Double Planetary Mixer: Laboratory & Production
There are two types of double planetary mixers produced by FRANLI, which mainly involve two major application fields, one is laboratory research type, and the other is a factory production line

Structural Adhesive Production Equipment & Double Planetary Mixer
The double planetary mixer is one of the ideal types of equipment for low-viscosity materials. This facility has a low and fast mixing dispersing disc, which can complete the functions of high shear and dispersing low viscosity materials at the same time.