Home » Coating
Coating
Advantages for painting line
After repeated consideration and comparison, franli engineers will get the best solution for the whole set of equipment. We will check the height and position of the operating platform are arranged in a total amount, which is easy to operate and small in area.
Standardization
The whole manufacturing process is standardized: negotiate with customers for standardization, procurement standardization, manufacturing process standardization, inspection standardization, and after-sales service standardization. Exquisite appearance, comparable to pharmaceutical equipment and food equipment The finish, welds, piping, surface treatment, paint, etc. of the main body of the equipment and external structural parts are all included in franli’s inspection system, and every detail is not overlooked.
Strong production capacity
Paint making and paint mixing can be completed in the same mixing tank, or different mixing tanks according to process requirements.
High fineness
The secondary grinding of the horizontal bead mill ensures the fineness of the paint.
Safety
Environmental protection
The Process of Producing coating Line (painting)
Pre-dispersion
Scattered
High final fineness of coating
Standard requirements. Note: The coating mixing tank can be equipped with several according to the production process requirements.
Filter various impurities through a bag filter with simple structure and simple operation. The filter can choose the filter mesh corresponding to the paint fineness. Canning, weighing, and packaging
Automatically complete the scanning, weighing, and packaging process.
Related Products
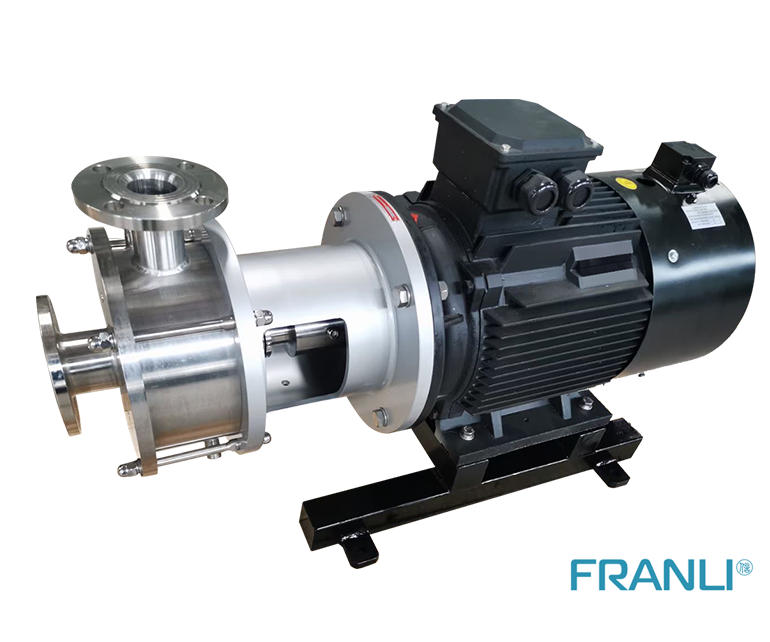
Inline Homogenizer
The Inline homogenizer is mainly used for mixing and homogenizing materials, dispersing, and emulsifying, and it is versatile and versatile. The inline homogenizer is generally used as a primary and intermediate material for mixing, and homogenizing.
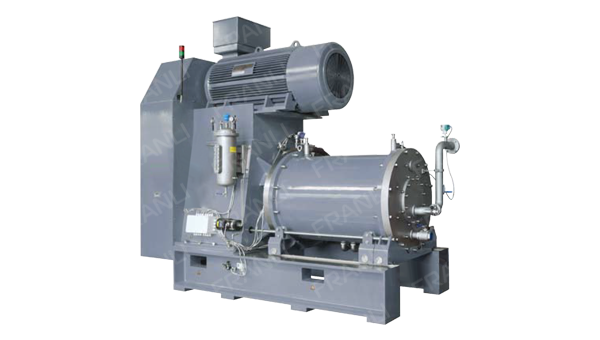
Agitator bead mill
Agitator bead mill’s pins are uniform distributed type, pre-milling your material when feeding material into chamber. The agitator bead mill has a stronger power motor, material milled by bead, and pins in the chamber.
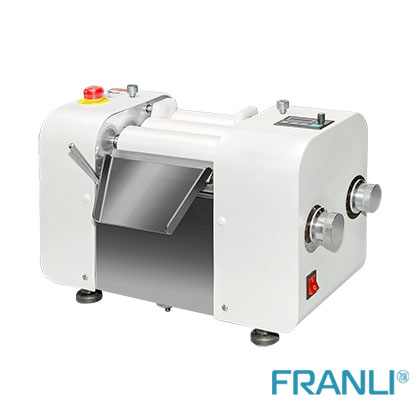
Lab Three Roller Mill
Franli Lab three roll mill machine also has a safety system. Such as hopper with handguard, drip tray with integrated handguard and safety switch, removable for easy cleaning. Also safe scraper socket, Emergency-stop pushbutton. Electronic Brake.
After Sales Support
News
Laboratory Reactor: Guide to Stirring System
The laboratory reactor is composed of a pot body, a pot cover, an agitator, a jacket, a support and transmission device, a shaft seal device, etc.
Grinding Media for Bead Mill | Zirconia Beads & Zirconium Silicate Beads
Bead mills mainly use grinding balls as media, and use impact, extrusion, and friction to achieve the final grinding effect, which mainly depends on the size and hardness of the grinding beads, the filling rate of the grinding beads, and the collision frequency adjustment between the grinding beads and the particles.
Overview of Laboratory Reactor
Laboratory reactors, also known as lab reactors, are essential tools in scientific research, product development, and process optimization. These reactors provide a controlled environment for conducting chemical reactions, mixing, dispersing, and homogenizing processes.
Bead mills | Manufacturing technology in various industries
Bead mills, also known as sand mills or grinding mills, are versatile machines widely used across various industries for the wet grinding and dispersion of solid particles in liquid media.
Ribbon Blender Mixer Equipment
A ribbon blender mixer, also known as a ribbon mixer or horizontal ribbon blender, is a powerful industrial machine designed for thorough and efficient blending of various materials.
What is A Stainless Steel Reactor?
Stainless steel reactors are essential equipment in various industries, including chemical, pharmaceutical, biotechnology, and food processing.