Home » How to use nano mill to process tiny particles
How to use nano mill to process tiny particles
Creating and manipulating the particles that range in sizes from 1 nanometer to that of 100 nm is what the process of nanonization involves. At the level of nanoscale, it involves a lot of biology here with a nano mill.
They are often times very expensive and need to have highly specialized and dedicated equipment while the synthesis of bottom-up form in the place of the processes here involved with the high-quality nanoparticles.
Not every milling technique here is able to achieve the nanoparticles since there is not a single nano grinding mill here. The reduction of particles to the range of nano can be made with the help of the ball mills, jet mills, as well as wet and dry media mills.
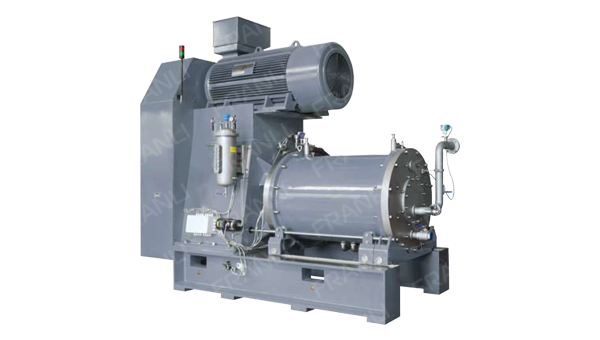
nano mill
How the smaller particles pack a strong punch
So, what is the reason behind it?
• Reduced dispersity along with the dissimilarity of the size that is measured in D or PDI along with the polydispersity index.
• The greater amount of dissolution of the compounds that are not quite water-soluble.
• Greater bioavailability and reactivity.A formulation is made a lot more effective with the reduced potential side effects and allowing the fewer compounds to be used within a product along with improving the cost of the product as well as the sustainability through these improvements here with the nano mill.
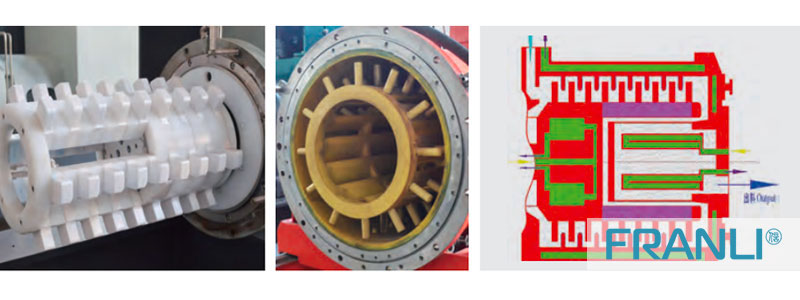
nano mill core parts
The proven technique of wet milling
The motion of the grinding bowl within the high-speed planetary ball mills effectively generates the higher energy shear forces for fracturing the already smaller particles into the nanoparticles as they are circulating through the nano grinding mill. The smaller is the end product sizes with the smaller size of the milling media. Great outcomes are produced in terms of both the fineness and tightness size distribution of the particles here with the help of the wet media milling processes.
In terms of their ability to grind the materials without they being to the ground down is how the milling media is selected here, thereby preventing the contamination of the final particles that are milled after the step of separation.
Jet milling for the nanoparticles
The nano-range of the particle sizes will also be drying the feed material that is enabled through the jet milling process.
For the materials that are sensitive to heat, this is the technique that might not be suitable, but the bed jet mills that are fluidized can be used in terms of getting the nanoparticles in a greater range of minerals as well the pigments here.
Factoring the right method for your material
The possibility to introduce the contaminants into the final end product, on the other hand, this wet milling is sure to present with the right things. They can also help in terms of achieving the desired size of the particle without making the use of the milling media all at the same time through the techniques that need a lot more energy here. To reduce the likelihood of wear to the milling media here, these wet mills can be adjusted easily.
Canonization is made possible for a greater amount of materials as well as the industries than ever before with the right team of toll processing’s that can aid you in terms of achieving the nanoparticles for the products through the milling methods as well as the technological advancements brought about by the nano mill.
The configurations of the nano mill are yet a lot more important here. For several years, Franli has been offering their production unit that has the ability to manufacture the nanoparticles. The milling machines here provide efficient nano-grinding that has higher-end yields along with the ease of operation being built in the right platform.
These companies can help you in terms of optimizing your production process as always here, so you can surely go ahead and have your testing scheduled.
Copyright Notice :
This article only represents the author’s point of view.
This article is published under the authorization of the author.
Source: Franli
This article address : How to use nano mill to process tiny particles
Related Products
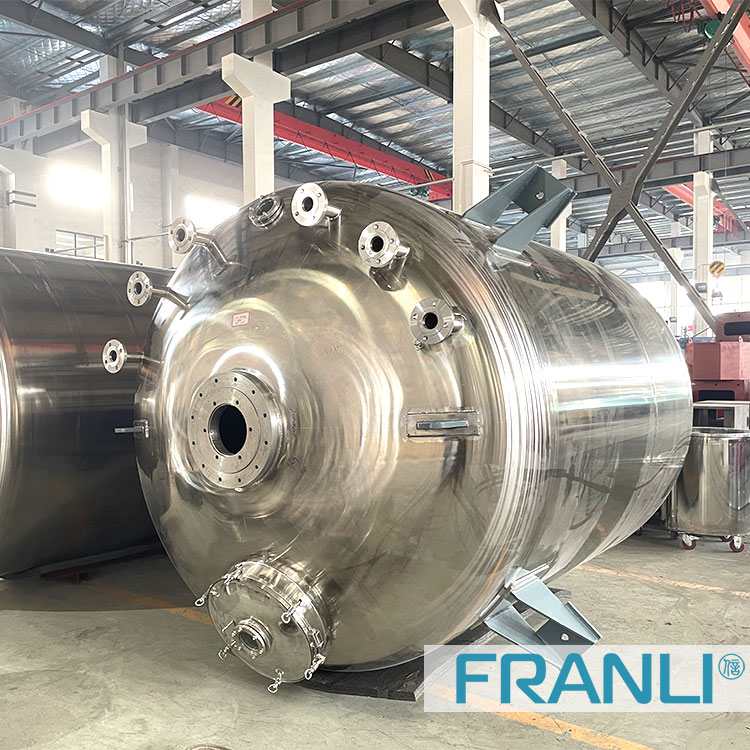
Stainless Steel Reactor
The reaction vessel is a comprehensive reaction vessel. The structure, function, and configuration accessories of the reaction vessel are designed according to the reaction conditions.
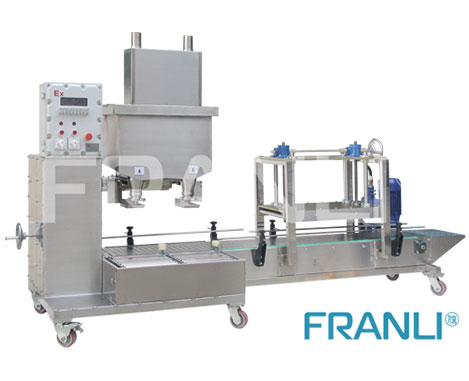
Paint Filling Machine
The paint industry has its own special design paint filling machine, normally choose weight type filling machine. One color needs one set of filling machine; also can filling different color of the painting, while it should be installed hopper
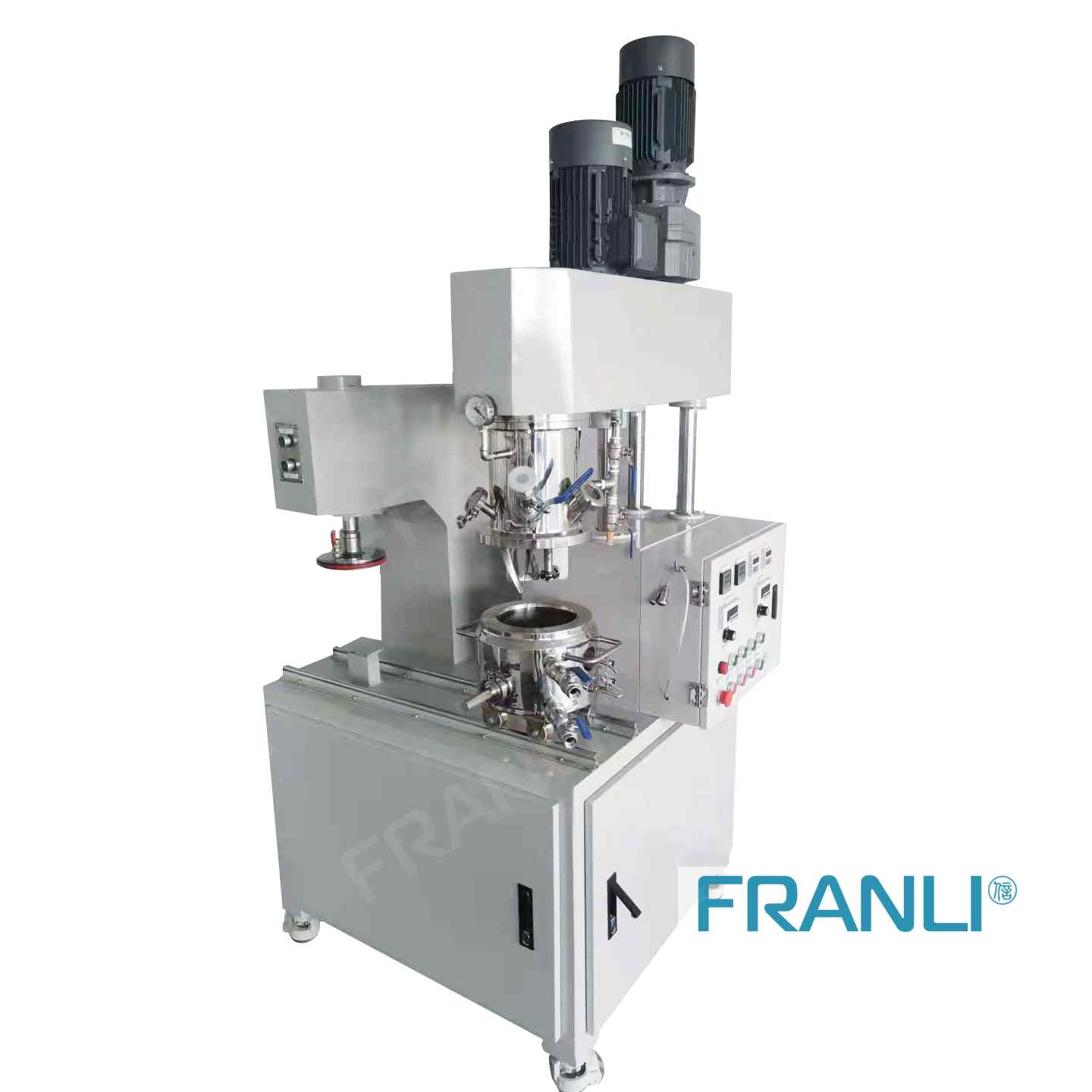
Laboratory Double Planetary Mixer
Laboratory double planetary mixer is a kind of non-standardized strong mixing and mixing equipment developed by FRANLI for universities, research institutes, and factory laboratories.
News
Laboratory Reactor: Guide to Stirring System
The laboratory reactor is composed of a pot body, a pot cover, an agitator, a jacket, a support and transmission device, a shaft seal device, etc.
Grinding Media for Bead Mill | Zirconia Beads & Zirconium Silicate Beads
Bead mills mainly use grinding balls as media, and use impact, extrusion, and friction to achieve the final grinding effect, which mainly depends on the size and hardness of the grinding beads, the filling rate of the grinding beads, and the collision frequency adjustment between the grinding beads and the particles.
Overview of Laboratory Reactor
Laboratory reactors, also known as lab reactors, are essential tools in scientific research, product development, and process optimization. These reactors provide a controlled environment for conducting chemical reactions, mixing, dispersing, and homogenizing processes.
Bead mills | Manufacturing technology in various industries
Bead mills, also known as sand mills or grinding mills, are versatile machines widely used across various industries for the wet grinding and dispersion of solid particles in liquid media.
Ribbon Blender Mixer Equipment
A ribbon blender mixer, also known as a ribbon mixer or horizontal ribbon blender, is a powerful industrial machine designed for thorough and efficient blending of various materials.
What is A Stainless Steel Reactor?
Stainless steel reactors are essential equipment in various industries, including chemical, pharmaceutical, biotechnology, and food processing.