Home » How to Operation and use FRANLI bead mill
How to Operation and use FRANLI bead mill
Bead Mill(sand mill) helps many factories to improve production. Grinding for low viscosity, well-flowing material. Self-cycling cooling system. Don’t need the cooling pump. Franli produces Disc Bead Mill, Pin Bead mill, Turbine Nano Bead mill, etc.
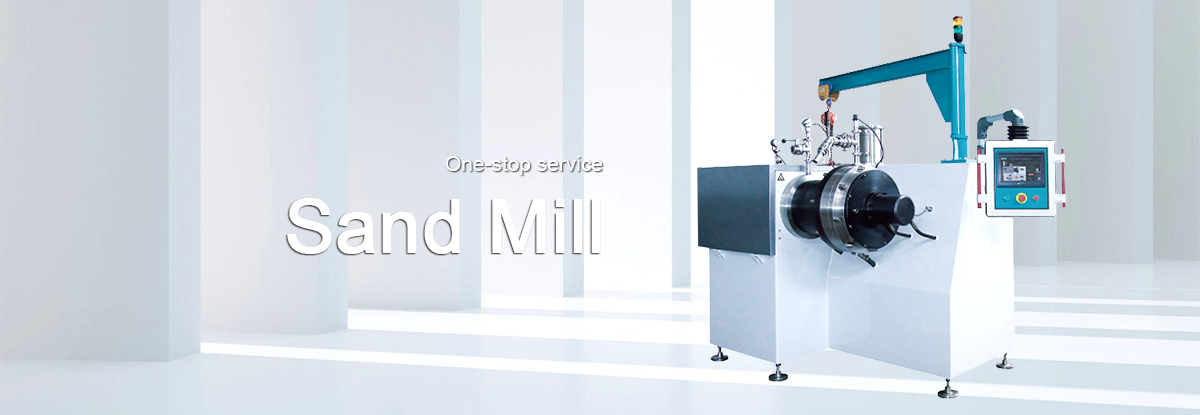
1. First-time start (commissioning)
The detailed steps are as following:
(1)Add the steam turbine oil into the mechanical sealing chamber of the sand mill.
(2)Check whether the main motor and pump motor circuits are ON.
(3)Open the water supplying valve and observe whether the water consumption reaches the user requirement.
(4)Open-air supply valve
(5)Add the mill mediate

(6)Adjust the V belt tightness and the control range of the meter.
(7)Cleaning: Due to the factory in order to keep the machine in the assembly process smoothly, often with oil, butter, and bonding agent and so on into the assembly process, so in order to guarantee the quality of the product must be clean to the whole system, including line feed pump grinding medium and grinding block and so on, the specific method is: prevent into 40 to 50 liters of solvent to the material canister, the solvent pump will pump into the grinding block, start the main motor, adjustable speed to 200 ~ 300 RPM, about 2 minutes after downtime. Then open the lid of the lower drainage hole grinding cylinder, the cylinder was first used in the solvent drained and then rotate the lid, with about 30 new solvents to clean up the second time during which start the second main motor (about 1 minute at a time), and then open the drainage opening lid row of dry cleaning solvent will tighten, cleaning work is done.
(8)After cleaning work is finished, you can operate the machine with the material. The feeding speed of the material-in pump should be decided according to the product quality and set milling cycle number.
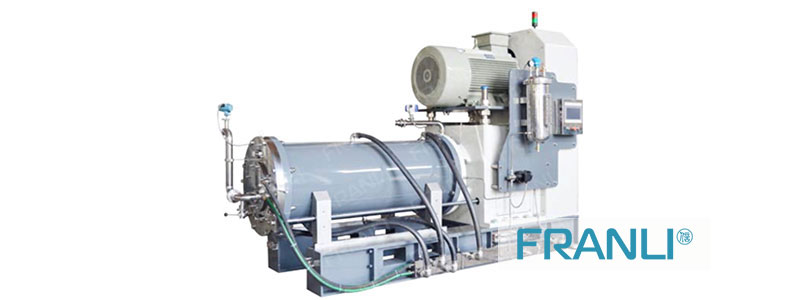
2. The operational rule of the machine
(1)The lubricating oil level is normal.
(2)V belt tightness is proper.
(3)If the sand mill has been not used for a long time, please open its back shell and bring the belt wheel rotating for 3~4 cycles by your hand.
(4)No other abnormal conditions.
Start
(1)Turn the general switch.
(2)Link the outlet of a material cylinder with the inlet of material-in pump through a hose. Open the outlet valve of the material cylinder.
(3)Start the water supply valve and air supply valve.
(4)Start the material-in pump till the pressure meter displays the material flowing.
(5)Start the main motor, confirm no abnormal conditions.
(6)Start the main motor, confirm no abnormal conditions.
(7)Adjust the pump speed.
(8)Adjust the water speed.
After the machine runs smoothly and stable, check the material quality and make adjustments.
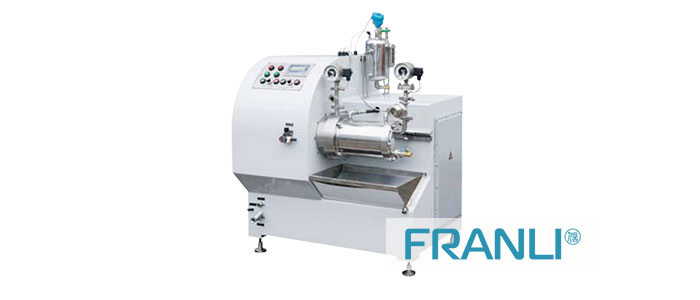
Water speed:
High: material outlet temperature is low.
LOW: material outlet temperature is high.
Pump speed
High: material-in volume is big, quality is low, outlet temperature is
Low: material-in volume is small, quality is high, outlet temperature is low.
Piston position
In: the quality is improved, the produced heat is high.
Out: the quality falls down, the produced heat is low.
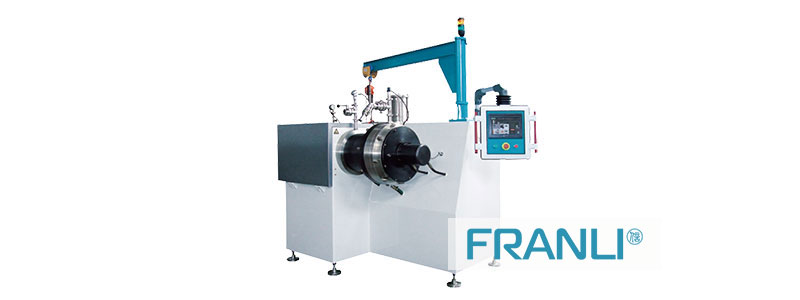
3.Stop the machine
(2)Stop the main motor
(3)Adjust to reduce the material-in pump speed
(4)Stop pump
(5)Close the water supply valve and the air supply valve
(6)Close the material cylinder outlet valve
(7)Disassemble the material convey hose, close the main switch
(8)Clean up the equipment surface
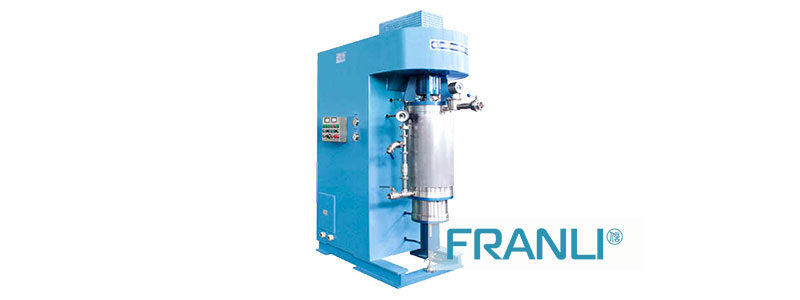
When cleaning is made with cleaning liquids foreign to the product, it has to be checked if the seals can cope with the cleaning liquid. When cleaning with pure solvent, water, or other liquids with low lubricating abilities, the agitator must be switched on only for a short time, because in this case, excessive wear occurs.
2.All pipelines have to be cleaned thoroughly in order to avoid contamination during the changing of the batch, also pipelines might plug when processing products that harden within a short period of time.
3.In order to keep the sealing surfaces of the sliding rings in contact pressure, the sealing pressure has to be maintained after switching off the machine as long as the grinding tank is filled with liquid.
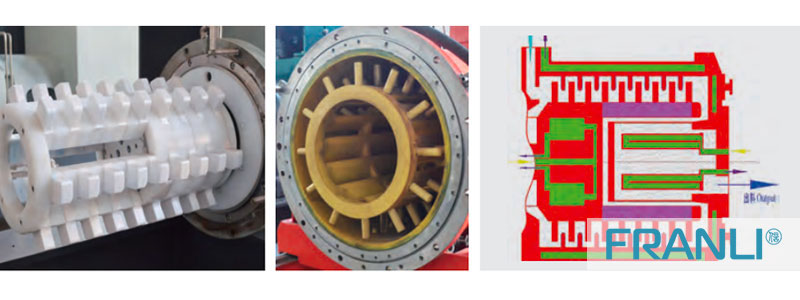
Operational Speeds
If the speeds stated in the above table are exceeded, the grinding system might be damaged.
Operational Parameters
Because the parameters frequently influence each other, only one value should be changed at one time.
(1) Changes in the filling level should be made in steps of max. 2 % of the tank volume.
(2) This is valid only for dispersions with easily breakable amorphous solid materials or agglomerates, where due to the speed and the kind of grinding media used the energy is sufficient for breakage (e.g. carbonates, paints, sulfates, etc.). If dispersions with very hard solid materials are concerned, the selection of grinding media has to be made in the opposite direction, because in this case, the energy in the grinding media has to be increased (e.g. iron oxides, strontium ferrites, hard metals, etc.).
(3) The opposite is valid if a highly viscous medium forms an isolating layer at the outer coating.
(4) Assumed viscosity in the grinding tank under working conditions, not in quiescent condition.
(5) The opposite is valid, if the viscosity (see 4)) increases very heavily due to over-grinding.
(6) The current intake could be assigned to the temperature parameter without any problems because their curves are running parallel on the whole.
(7) Should the diameter ratio of the beads exceed the value 1:2 due to wear and refilling of new beads after a longer production process, the whole batch should be replaced, resp. screened. Mixed grinding media often result in worse throughput rates, higher temperatures, and higher wear.
(8) This is essentially valid for dispersing. During comminution grinding contrary tendencies become visible.
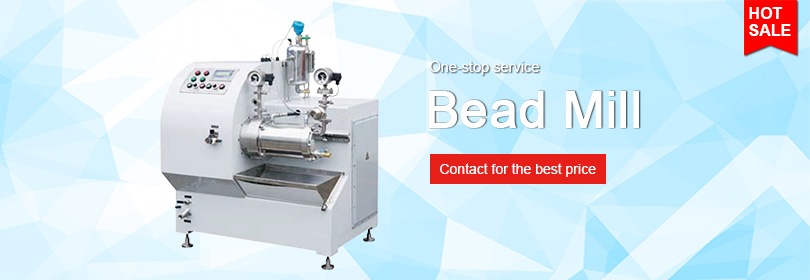
Copyright Notice :
This article only represents the author’s point of view.
This article is published under the authorization of the author.
Source: Franli
This article address : How to Operation and use FRANLI bead mill
Related Products
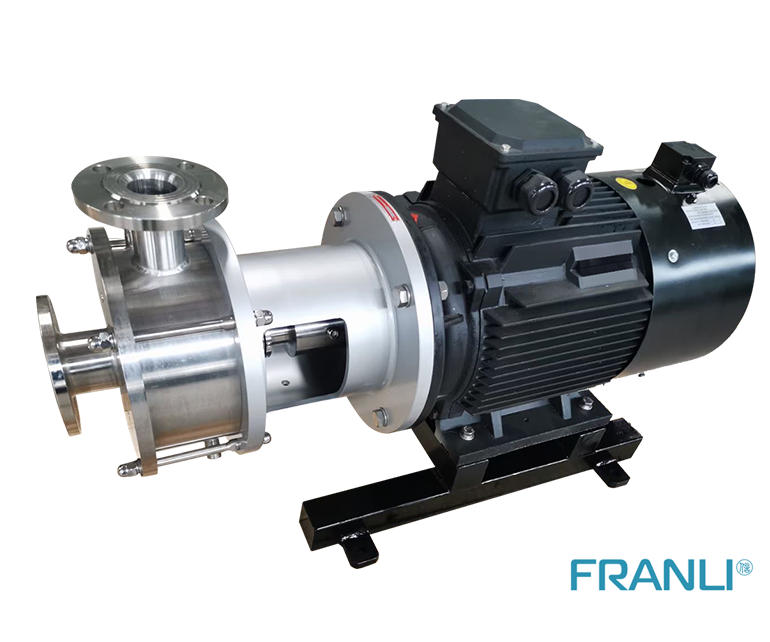
Inline Homogenizer
The Inline homogenizer is mainly used for mixing and homogenizing materials, dispersing, and emulsifying, and it is versatile and versatile. The inline homogenizer is generally used as a primary and intermediate material for mixing, and homogenizing.
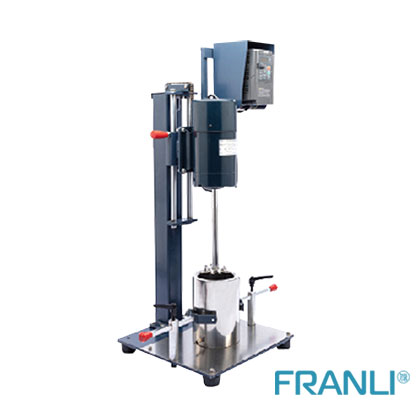
Laboratory high speed disperser
The laboratory high speed disperser can realize multiple functions in one machine, and perfectly realize the functions of dispersion, grinding, stirring, etc.
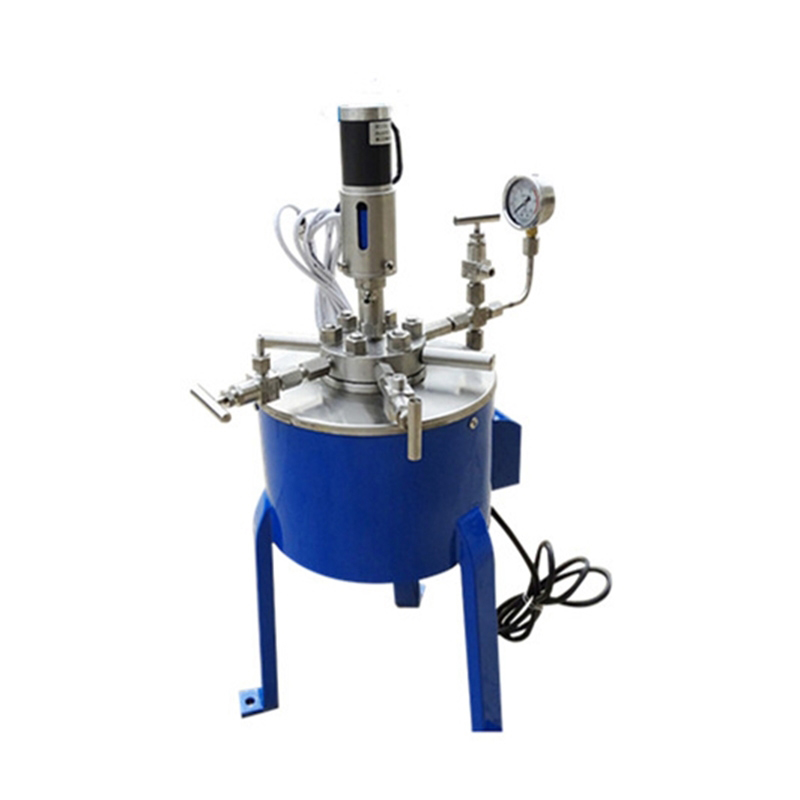
Laboratory Reactor
FRANLI laboratory reactor is composed of a pot body, pot cover, stirrer, heating jacket, support and transmission device, shaft seal device, etc. The pot body, pot cover, stirrer, shaft seal, etc. are all made of 1Cr18Ni9Ti stainless steel. A laboratory reactor is mainly suitable for hydrolysis, neutralization crystallization, distillation, evaporation, storage, and other production links in medicine, bioengineering, fine chemical industry, chemical synthesis, food, and other industries.
News
Laboratory Reactor: Guide to Stirring System
The laboratory reactor is composed of a pot body, a pot cover, an agitator, a jacket, a support and transmission device, a shaft seal device, etc.
Grinding Media for Bead Mill | Zirconia Beads & Zirconium Silicate Beads
Bead mills mainly use grinding balls as media, and use impact, extrusion, and friction to achieve the final grinding effect, which mainly depends on the size and hardness of the grinding beads, the filling rate of the grinding beads, and the collision frequency adjustment between the grinding beads and the particles.
Overview of Laboratory Reactor
Laboratory reactors, also known as lab reactors, are essential tools in scientific research, product development, and process optimization. These reactors provide a controlled environment for conducting chemical reactions, mixing, dispersing, and homogenizing processes.
Bead mills | Manufacturing technology in various industries
Bead mills, also known as sand mills or grinding mills, are versatile machines widely used across various industries for the wet grinding and dispersion of solid particles in liquid media.
Ribbon Blender Mixer Equipment
A ribbon blender mixer, also known as a ribbon mixer or horizontal ribbon blender, is a powerful industrial machine designed for thorough and efficient blending of various materials.
What is A Stainless Steel Reactor?
Stainless steel reactors are essential equipment in various industries, including chemical, pharmaceutical, biotechnology, and food processing.