Home » The Application of Pneumatic Mixers in Resins: Enhancing Efficiency & Quality
The Application of Pneumatic Mixers in Resins: Enhancing Efficiency & Quality
Pneumatic Mixers
Pneumatic mixers have revolutionized industrial processes, providing efficient and effective mixing solutions across various sectors. In the realm of resin manufacturing and processing, pneumatic mixers play a crucial role by simplifying the mixing process, ensuring uniformity, and improving overall quality.
Details of Pneumatic Mixers
- The pneumatic mixer can be adjusted steplessly.
- The pneumatic mixer can rotate forward and reverse.
- The working environment of the pneumatic mixer is not affected by vibration, high temperature, electromagnetic, radiation, etc.
- The air motor matched with the air mixer has the function of overload protection, and will not fail due to overload.
- The pneumatic mixer has a high starting torque and can be started directly with a load.
- The pneumatic mixer is easy to operate and easy to maintain and repair.
Application: petroleum, chemical, paint, paint, woodworking, food, daily chemical, and other flammable, dusty, heavy-duty, wet, and other industries.
Resins are composite materials widely used in industries such as automotive, construction, electrical, and aerospace due to their exceptional properties. These include high thermal resistance, durability, and chemical inertness. Resins are typically formed through a polymerization process that involves the mixing of various ingredients, such as additives, fillers, and catalysts, to achieve the desired characteristics. Efficient and uniform mixing of these components is essential to optimize the resin’s performance.
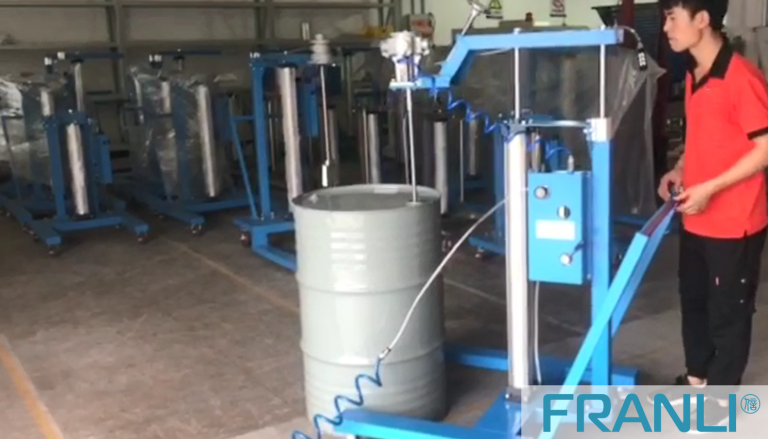
Pneumatic Mixers: Characteristics and Functionality
Pneumatic mixers, also known as air-powered mixers, employ compressed air to generate the necessary agitation for mixing applications. These mixers consist of an air motor, mixing propeller, and a shaft. The air motor drives the mixing propeller, creating a vortex that promotes efficient blending and dispersion of ingredients. Pneumatic mixers are available in different configurations, including direct-drive, gear-driven, and folding impeller designs, catering to a wide range of resin mixing requirements.
Benefits of Pneumatic Mixers in Resins
Uniform Mixing: Proper dispersion of additives, catalysts, and fillers is critical in resin production to achieve consistent product quality. Pneumatic mixers generate a high sheer force through controlled air pressure, resulting in the uniform distribution of ingredients throughout the mixture. This ensures a homogeneous resin composition, maximizing its desirable properties.
Time and Cost Efficiency: Pneumatic mixers offer excellent time and cost efficiencies. Compared to traditional mixing methods, such as manual stirring or mechanical mixers, pneumatic mixers significantly reduce the mixing time. The rapid agitation and homogenization capability of pneumatic mixers allows for quicker resin production, increasing output and reducing labor costs.
Process Flexibility: Pneumatic mixers are highly versatile and adaptable to various resin production processes. These mixers can agitate resins of different viscosities, ranging from low to high, without compromising quality. Additionally, pneumatic mixers can be easily integrated into existing production lines, requiring minimal modification or additional equipment, making them suitable for both small-scale and large-scale resin manufacturing facilities.
Quality Control and Consistency
Ensuring consistent resin quality throughout the manufacturing process is crucial to meet industry specifications. Pneumatic mixers aid in achieving this goal by providing a controlled mixing environment. The agitation generated by these mixers creates a constant flow pattern that allows for precise control over mixing time, ensuring thorough blending of ingredients and preventing batch variation. Consistency in resin production results in improved product performance, enhanced customer satisfaction, and reduced waste.
Safety Considerations
Pneumatic mixers offer several safety advantages compared to alternative mixing methods. Due to the absence of electrical power in their operation, they eliminate the risk of electrical hazards, such as short circuits or electric shocks, common in other mixing devices. Moreover, the use of compressed air as the driving force ensures that the mixing process remains relatively unaffected by fluctuations in electrical power supply. Additionally, pneumatic mixers are designed to be explosion-proof or flameproof, making them suitable for mixing hazardous resins.
In conclusion, pneumatic mixers have proven to be invaluable tools in the resin industry, contributing to enhanced efficiency and quality control. With their ability to achieve uniform mixing efficiently, pneumatic mixers streamline the resin manufacturing process, significantly reducing time and costs while maintaining consistent product quality. Furthermore, pneumatic mixers provide a safe mixing environment, complying with stringent safety regulations. As the demand for high-performance resins continues to grow across diverse industries, pneumatic mixers will continue to play a vital role in enabling the development and production of advanced resin products.
As a professional Pneumatic mixer, FRANLI has provided a complete set of mature equipment for related machines and production lines for more than 60 countries and thousands of industries in the world, and in Russia, Turkey, Spain, Brazil, Malaysia, Indonesia, and other regions, it has provided many An enterprise establishes related production lines.
Welcome to send inquiry to us and let’s make a win win business together !
Guidelines For Pneumatic Mixers
The stirring process of the pneumatic mixer is a single momentum transfer in the fluid field or a process including momentum, heat, mass transfer and chemical reaction. The agitator mainly inputs the energy of the device by making the stirring medium obtain a suitable flow field device.
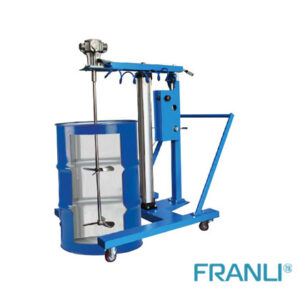
Pneumatic Mixer: Enhancing Efficiency & Productivity in Mixing Processes
A pneumatic mixer, also known as an air-driven mixer or air-powered mixer, is a type of mixer that utilizes compressed air to drive its mixing action.
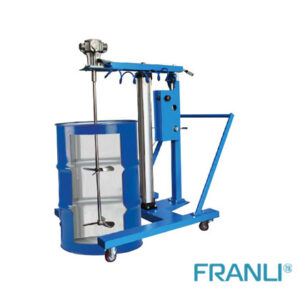
Enhance Efficiency & Quality with Pneumatic Paint Mixers
Pneumatic paint mixers utilize compressed air to generate rotational motion, enabling thorough mixing of paints and coatings. These mixers are equipped with a powerful air-driven motor that connects to a mixing shaft.
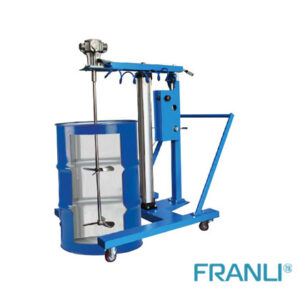
The Application of Pneumatic Mixers in Resins: Enhancing Efficiency & Quality
In the realm of resin manufacturing and processing, pneumatic mixers play a crucial role by simplifying the mixing process, ensuring uniformity, and improving overall quality.
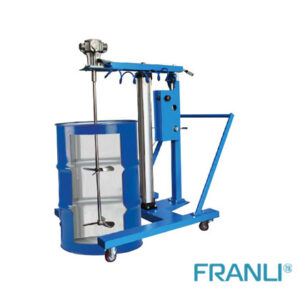
Pneumatic Mixers: Transforming Paint Application in the Coating Industry
Pneumatic mixers are mechanical devices that utilize compressed air to generate rotational motion, effectively blending and homogenizing paint.
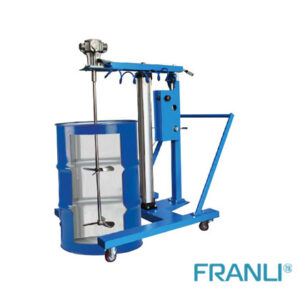
The Application of Pneumatic Mixers in Various Industries
Pneumatic mixers are widely utilized in various industries as a crucial component of the mixing process. These versatile machines utilize compressed air to rotate blades or paddles, enabling efficient and uniform blending of various substances or materials.
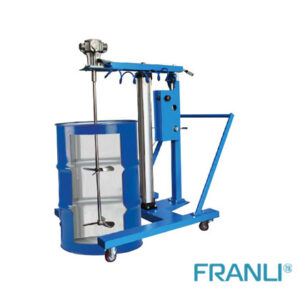
Pneumatic Mixer: Solution for Mixing Applications
A pneumatic mixer is a type of mixing equipment that uses compressed air to drive the mixing mechanism. The mixing mechanism can be a propeller, impeller, or turbine, depending on the application and viscosity of the materials being mixed.