Home » The Application of High-Speed Disperser in Anti-Corrosion Coatings
The Application of High-Speed Disperser in Anti-Corrosion Coatings
High Speed Disperser
Corrosion is a destructive process that affects a wide range of materials, leading to significant economic losses and safety concerns. To combat this phenomenon, the development of effective anti-corrosion coatings has gained considerable attention in recent years. The application of high-speed dispersers in the production of these coatings has emerged as a promising solution due to its ability to improve coating performance and enhance overall corrosion resistance.
Details of High Speed Disperser
- Height limit switch
- Container clamping device
- Speed Automatic
- Vacuum equipment
- Scraper
- Swiveling device
Application: Paint, Adhesive, Battery, Pharmaceutical industry, Cosmetic
A high-speed disperser is an essential piece of equipment used in the formulation and production of coatings. It consists of a rotating shaft with a dispersing blade that creates intense shear forces, resulting in the dispersion, deagglomeration, and homogenization of solid particles in a liquid medium. The high-speed disperser effectively breaks down agglomerates and promotes uniform distribution of particulate fillers in the coating formulation.
Benefits of High-Speed Disperser in Anti-Corrosion Coatings
1. Enhanced Dispersion:
The primary advantage of high-speed dispersers in anti-corrosion coatings lies in their ability to achieve efficient dispersion of particles. Agglomerates and clusters of solid particles can lead to coating defects, compromising its corrosion resistance. The high-shear forces generated by the dispersing blade effectively separate these agglomerates, reducing particle size, and promoting uniform particle dispersion throughout the coating matrix. This uniform dispersion enhances the coating’s protective properties.
2. Improved Particle Size Distribution:
Particle size distribution plays a crucial role in the performance of anti-corrosion coatings. By utilizing high-speed dispersers, manufacturers have better control over particle size distribution. The disperser’s high shear forces break down larger particles into smaller, more uniform sizes, leading to a narrower particle size distribution. This controlled distribution enhances the coating’s barrier properties, as the smaller particles can fill voids and prevent corrosive agents from reaching the substrate.
3. Better Wetting and Adhesion:
Wetting and adhesion are critical factors in the effectiveness of anti-corrosion coatings. The high-speed disperser’s intense mixing action aids in achieving excellent wetting and uniform coating coverage. It ensures that the coating fully adheres to the substrate surface, reducing the possibility of pinholes or uncoated areas that can expose the surface to corrosion. Additionally, the enhanced adhesion provided by the disperser promotes long-term durability, even under harsh environmental conditions.
4. Reduced Production Time and Cost:
The high-speed disperser’s speed and efficiency contribute to reduced production time and cost. Its ability to rapidly and effectively disperse particles minimizes the time required for mixing and homogenization, allowing for faster production cycles. Furthermore, the disperser enables increased loading of active additives, such as corrosion inhibitors, fillers, or pigments, without sacrificing dispersion quality. This higher loading capacity leads to potential cost savings by reducing the amount of raw materials required for the coating formulation.
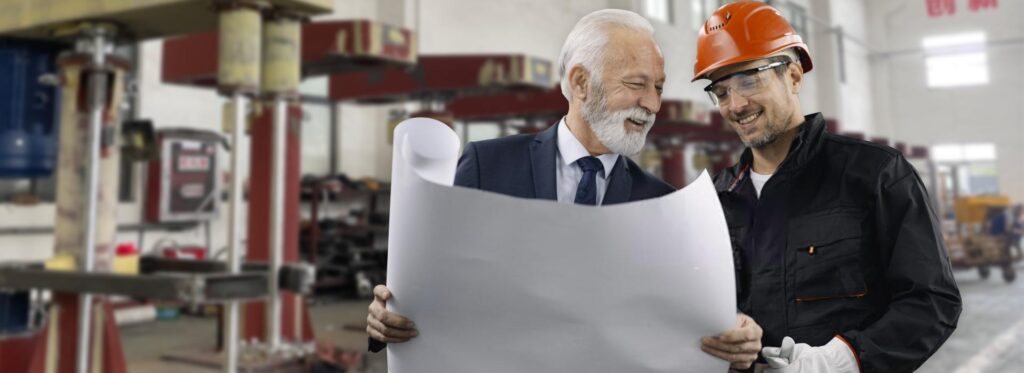
Challenges and Considerations
While high-speed dispersers offer numerous benefits, several challenges and considerations should be addressed when applying them in the production of anti-corrosion coatings.
1. Heat Generation:
The high shear forces generated by the dispersing blade can result in heat build-up during the dispersion process. This heat can alter the rheological properties of the coating formulation and even compromise the stability of sensitive additives. Manufacturers must manage the dispersion process carefully, employing techniques such as temperature control and cooling mechanisms, to mitigate these heat-related issues.
2. Material Compatibility:
Different coating formulations and materials may require specific dispersion processes. The compatibility of the disperser with the coating materials, including binders, pigments, and additives, must be considered. Some materials may be shear-sensitive or prone to degradation caused by the high-speed mixing. Careful selection of disperser speed, blade configuration, and other process parameters is necessary to ensure optimal dispersion without compromising material integrity.
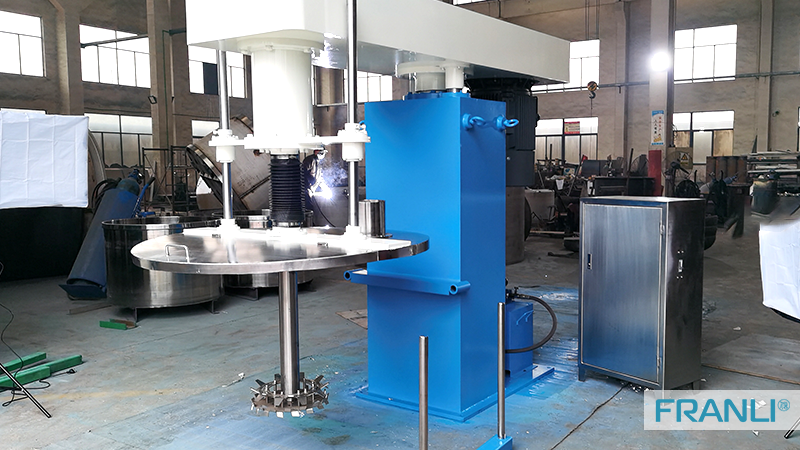
The application of high-speed dispersers in the production of anti-corrosion coatings represents a significant advancement in the field of surface protection. The dispersers’ ability to enhance dispersion, improve particle size distribution, promote wetting and adhesion, and reduce production time and cost makes them valuable tools for coating manufacturers. Despite certain challenges, careful consideration of dispersion process parameters and material compatibility allows the efficient and effective utilization of high-speed dispersers, leading to improved anti-corrosion coatings, extended asset lifecycles, and reduced economic losses.
Welcome to send inquiry to us and let’s make a win win business together !
Guidelines For High Speed DIsperser
We produce a high-speed disperser according to the industrial standard, Franli HSD’s frame is bigger than the marketing machine, the blade is double layers, hydraulic part is an engineering oil tank, which is more stable lifting up and down. The operation box for Water-based material is stainless steel, which also has ex-proof operation for solvent based material.
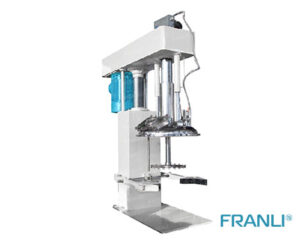
A High Speed Disperser & Efficient Mixing and Dispersion
A high speed disperser is a type of industrial equipment used for mixing and dispersing materials that are used to disperse, emulsify, and blend different types of materials.
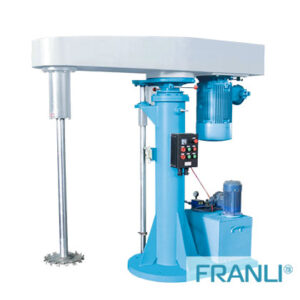
High Speed Disperser: An Essential Tool in the Manufacturing Industry
A high speed disperser is a machine used for dispersing, mixing, emulsifying, and homogenizing materials in the manufacturing process.It is also called a high-speed mixer or agitator, and its versatility makes it a valuable tool in various industries, including coatings, paints, inks, adhesives, pharmaceuticals, food, and cosmetics.
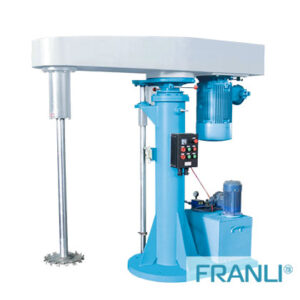
The high speed disperser chosen by the chemical industry
The high speed disperser is the indispensable equipment in the production and dispersion process of chemical products. Because of its high speed, it can not only effectively improve the dispersion efficiency of materials, but also make the materials more fully dispersed, to meet the final requirements of the materials.
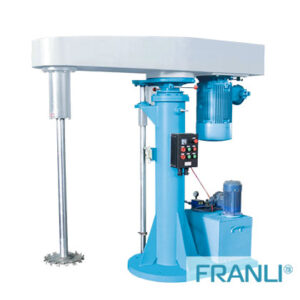
How to choose a suitable high-speed disperser for coatings?
A high speed paint disperser is one of the chemical equipment for stirring, dispersing, and dissolving paint raw materials, slurry, and paint mixture.
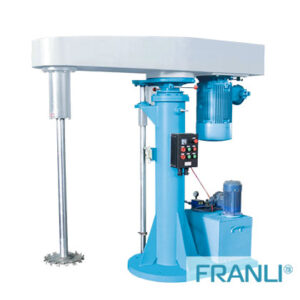
How to use the high speed disperser (new machine)?
The high speed disperser is composed of a frame, a bearing seat, a dispersing shaft, a dispersing wheel, an oil cylinder, a hydraulic station, and a control cabinet. The lifting of the frame adopts hydraulic transmission, and the lifting is stable and reliable.
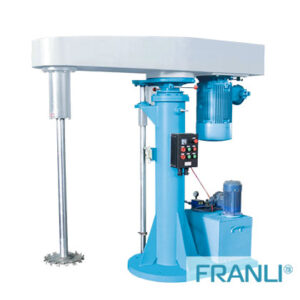
High speed disperser: dispersing, stirring, grinding, dissolving
High speed disperser is common mechanical equipment in chemical production. It is widely used in architectural coatings, chemicals, water-based coatings, oil-soluble architectural coatings, inks, inks, adhesives, etc.