Home » The connection between ink and sand mill
The connection between ink and sand mill
Ink is composed of resin, pigment, solvent, and auxiliary agents. According to whether it contains pigment, it can be divided into color ink containing pigment (also white and black), thinner without pigment, gold adjusting oil, and glazing oil. The application and storage performance of the ink with a certain formula is directly related to the production process. Therefore, the purpose of ink production is to disperse the ingredients in the formula as effectively and consistently as possible. Pigments are the most difficult to be uniformly dispersed. Pigment dispersion and grinding are the core of ink production.
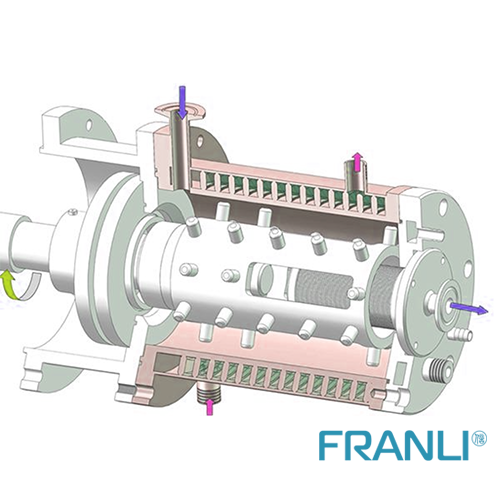
The efficiency of the sand mill to disperse liquid ink (such as plastic gravure ink, flexographic ink, etc.) is very high. Its biggest advantage is to ensure uniform quality, reduce color pollution, large output, and continuous production. At present, it is divided into three types according to its structure in the world: one is a vertical open type sand mill, the other is a vertical sealed type sand mill, and the third is a horizontal sealed type sand mill. The horizontal type is also called a horizontal type.
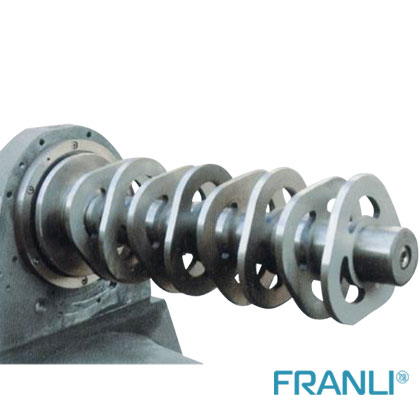
The horizontal sand mill is a kind of sand mill in which the cylinder of the vertical sand mill is placed horizontally. Because the shaft is horizontal, and the plane of the impeller is perpendicular to the horizontal plane, there is at least one advantage. When the machine is started, it will not need to overcome the gravity of the sand laminated on the plane of the impeller, like a vertical sand mill. Therefore, generally horizontal sand mills can save power more than vertical sand mills.
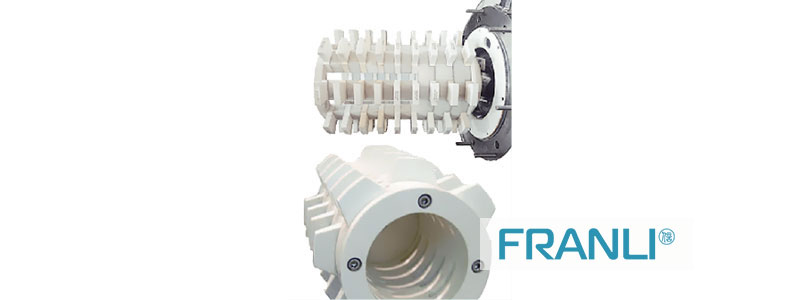
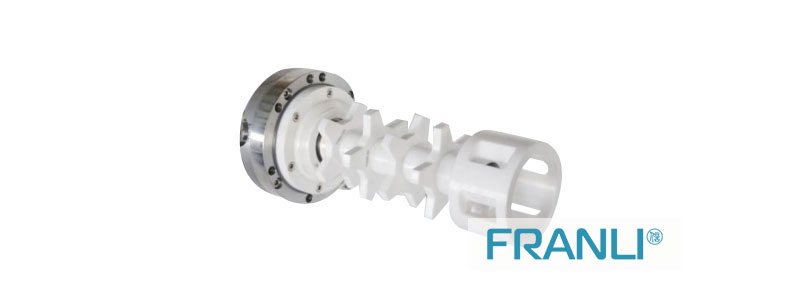
The size, shape, and density of the grinding media
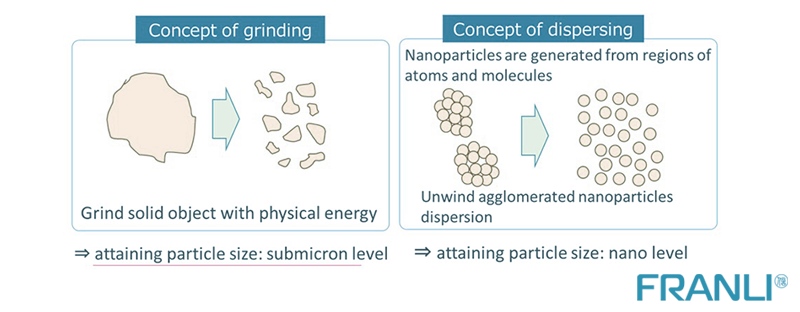
As for the shape of the grinding media, because it runs at a high speed, it is almost unanimously considered that a spherical or nearly spherical shape is the best. Since the grinding action of the sand mill is still dominated by impact and shear forces, if the density of the grinding medium is higher, the two forces will be greater for the same size of the grinding medium, and the sanding effect will be better. Some.
At present, most of our country uses glass beads, steel balls, zirconium silicate beads, zirconia beads, as grinding media for sand mills. The density of glass beads varies with the type of metal in the glass composition, but you must not only consider glass when choosing. The strength and density of the glass should also be considered whether there are toxic metals (such as lead) in the glass composition, otherwise, the ink will be contaminated and affect the quality.
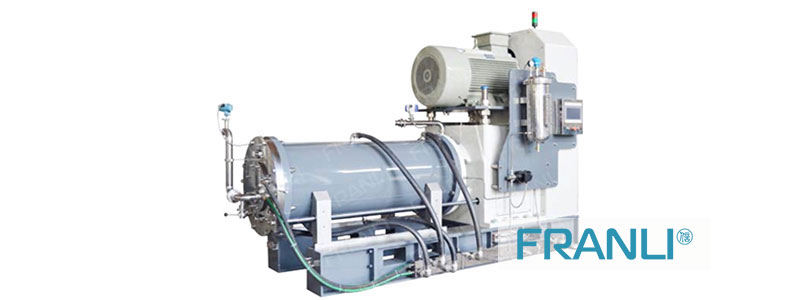
The amount of grinding media
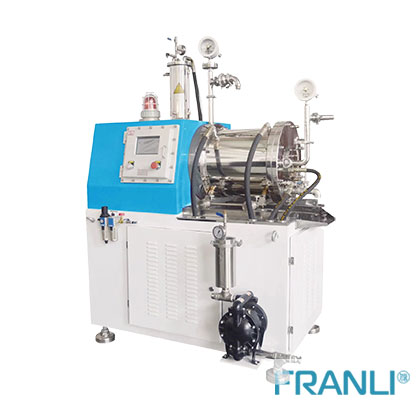
For horizontal sand mills, the amount of grinding media can start from 80% of the simplified volume, and then increase or decrease the amount of grinding media according to the discharge temperature of the material or the temperature of the cooling water. Generally speaking, when the temperature exceeds the allowable range, The amount of grinding media should be reduced. When the temperature is lower than the allowable range, before increasing the shaft speed, priority can be given to increasing the amount of grinding media. Generally, the discharge temperature of the ink is allowed within the range of 50-70°C. Adjusting the amount of media can be measured by this scale, and it is necessary to pay attention to control for some inks with poor stability. herefore, these factors must be considered when determining the amount of grinding media. The general principle is that when the ink viscosity is high, the amount of grinding media should be less, and when the viscosity is small, the amount of grinding media can be slightly more.
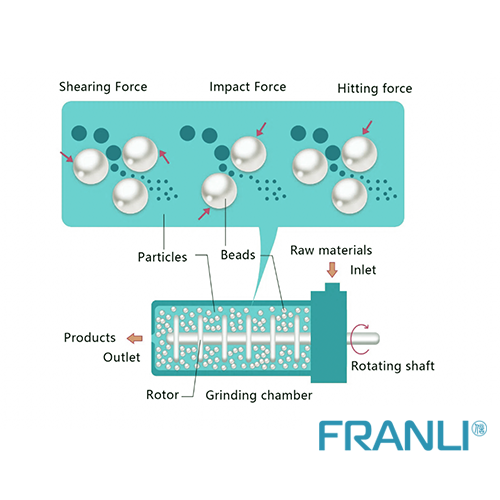
Copyright Notice :
This article only represents the author’s point of view.
This article is published under the authorization of the author.
Source: Franli
This article address : The connection between ink and sand mill
Related Products
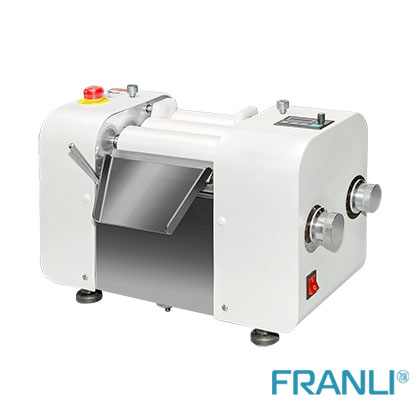
3 Roll Mill: Manual, Hydraulic, Lab
3 Roll Mill is a great tool that is used to mix, refine, and disperse any material through three horizontal rolls situated opposite sides with different speeds.
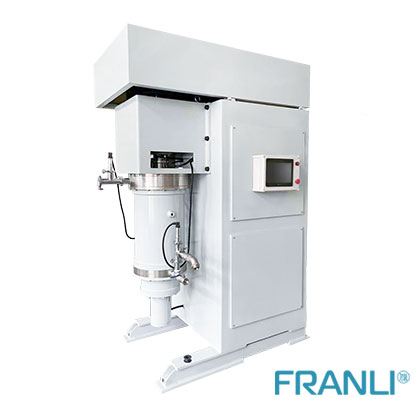
Pearl Mill
The pearl mill grinding chamber with pins, specially designed grinding shaft. We install an advanced cooling system for high temperature of viscosity material. Pearl mill has a German mechanical seal, NSK bearings. Which avoids the leaking of material.
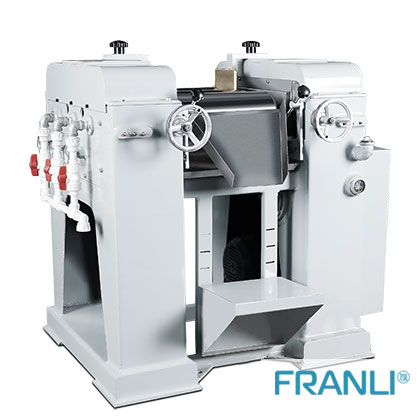
TRS-Three Roll Mill For Lipstick
TRS Three roll mill is widely used in milling paste material including paint, inks, China ink, pigment, coatings, food, cosmetics, and so on.
News
Laboratory Reactor: Guide to Stirring System
The laboratory reactor is composed of a pot body, a pot cover, an agitator, a jacket, a support and transmission device, a shaft seal device, etc.
Grinding Media for Bead Mill | Zirconia Beads & Zirconium Silicate Beads
Bead mills mainly use grinding balls as media, and use impact, extrusion, and friction to achieve the final grinding effect, which mainly depends on the size and hardness of the grinding beads, the filling rate of the grinding beads, and the collision frequency adjustment between the grinding beads and the particles.
Overview of Laboratory Reactor
Laboratory reactors, also known as lab reactors, are essential tools in scientific research, product development, and process optimization. These reactors provide a controlled environment for conducting chemical reactions, mixing, dispersing, and homogenizing processes.
Bead mills | Manufacturing technology in various industries
Bead mills, also known as sand mills or grinding mills, are versatile machines widely used across various industries for the wet grinding and dispersion of solid particles in liquid media.
Ribbon Blender Mixer Equipment
A ribbon blender mixer, also known as a ribbon mixer or horizontal ribbon blender, is a powerful industrial machine designed for thorough and efficient blending of various materials.
What is A Stainless Steel Reactor?
Stainless steel reactors are essential equipment in various industries, including chemical, pharmaceutical, biotechnology, and food processing.