Home » Paint Production Line
Paint Production Line
8 systems in the production line
The whole production line is equipped with powder and liquid feeding system, pulping system, paint mixing, discharging and filtering system, filling system, cooling system, pipeline system, electrical control system and operation platform.
The paint production line is mainly composed of a feeding system, dispersion system, grinding system, paint mixing system, discharge and filtration system, filling system, control system, operation platform, and color paste production.
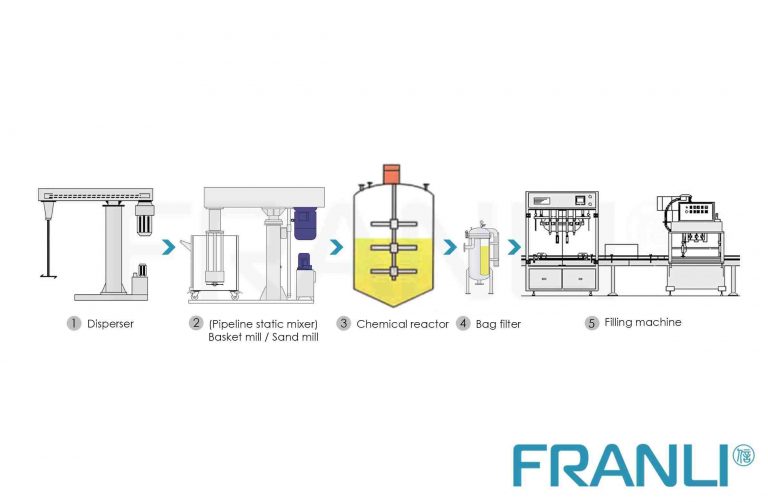
The production process of the paint production line
Before production, the factory needs to set the production formula on the industrial computer or touch screen. The operator can control the pump valve through the PLC to add resin, solvent, and powder to the high-speed dispersion tank according to the formula, and then control the frequency converter through the PLC. Operate the motor to drive the disperser to start working at the set working speed, and finally complete the pulping process.
After the dispersion of the high-speed disperser is completed, the pulping process is basically completed. The user can control the opening of the valve at the bottom of the pulping tank through the PLC. The material flows into the grinding chamber of the sand mill through the pump or by itself, and the pipeline level gauge will remind the PLC to open. The built-in diaphragm pump of the sand mill will then start feeding the sand mill. All the sand mills in the series start to work, and the user needs to add a transfer cylinder in advance and wait for the sand mill to complete the grinding, and the grinding output is pumped to the paint mixing kettle.
The user can adjust the color and paint according to the production plan. The color paste and additives can be added by a small metering feeding system, or manually. After the paint adjustment is completed, the finished paint is transported to the finished product storage tank through the filter for storage, or transported To the filling machine, directly completing the station filling.
The control system of the paint production line
1. FRANLI’s industrial computer and touch screen mainly use internationally famous brand products as the upper computer of the system to ensure the reliability of the control system.
2. The metering system adopts weighing metering or flow metering, which has high precision, good stability, fast response speed, and long service life; it can accurately measure the production links such as feeding and paint mixing, and display it on the host computer to avoid feeding, Errors caused by human factors in the paint mixing operation to improve product quality.
3. Programmable logic controller (PLC) and analog input modules are all selected from internationally famous brand products, with strong anti-interference ability, high reliability, and stability.
4. Control box (both explosion-proof and non-explosion-proof), MCC cabinet, and PLC cabinet are equipped for on-site operation.
High Speed Disperser
The first step in the paint production line is the mixing of raw materials. The dispersing system uses a high speed disperser, mainly because it has the characteristics of frequency conversion speed regulation and high efficiency. You can also choose a machine with two cylinders dispersing machine, which has the characteristics of saving space and convenient electric rotation operation. A high-speed disperser is a machine that is used to mix raw materials. This machine consists of a motor that drives a shaft with a blade at the end. The blade rotates at high speed, creating a vortex that draws in the raw materials and mixes them.
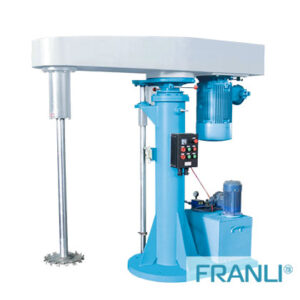
Pipeline Static Mixer
After the raw materials have been mixed, they are passed through a pipeline static mixer. This machine is used to ensure that the materials are thoroughly mixed and that there are no lumps or clumps in the mixture. The pipeline static mixer works by forcing the mixture through a series of baffles that cause the materials to mix.
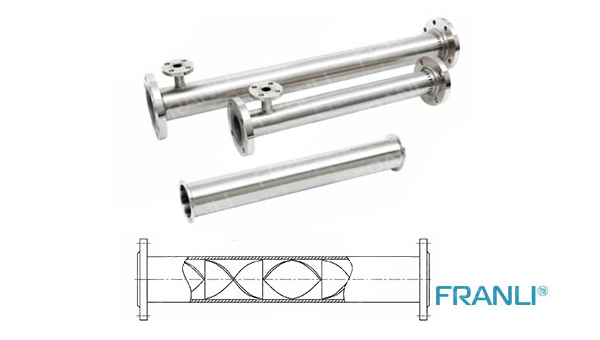
Basket Mill
The next step in the paint production line is the grinding of the mixture. A basket mill is a machine that is used to grind the mixture to a fine consistency. This machine consists of a basket that is filled with grinding beads. The mixture is passed through the basket, and the grinding beads grind the mixture to a fine consistency.
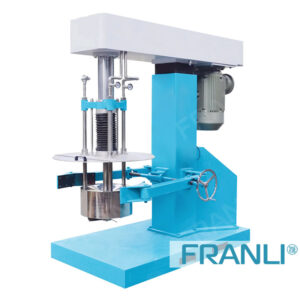
Sand Mill
Another machine that is used for grinding the mixture is a sand mill. This machine works in a similar way to the basket mill, but it uses sand instead of grinding beads. The sand mill is used for grinding the mixture to an even finer consistency. The grinding system adopts a serial horizontal sand mill, which can meet the fineness requirement at one time, and the color paste grinding can use a basket grinding or pin-type horizontal sand mill.
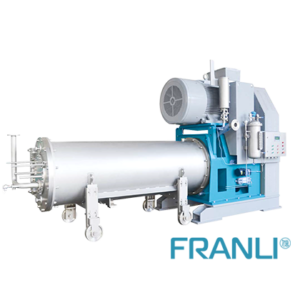
Paint Mixing Kettle
After the mixture has been ground to the desired consistency, it is transferred to a paint mixing kettle. This machine is used to mix the ground mixture with other additives, such as pigments and solvents. The paint mixing kettle ensures that the mixture is thoroughly mixed and that all the additives are evenly distributed. The paint mixing system adopts multi-functional mixing equipment, which can be applied to products with high or low viscosity, and can also produce varnish at the same time.
Bag Filter
The next step in the paint production line is the filtration of the mixture. A bag filter is a machine that is used to remove any impurities from the mixture. The mixture is passed through a series of bags, and any impurities are trapped in the bags. The filter has a bag type and vibrating type, chosen and use according to the product.
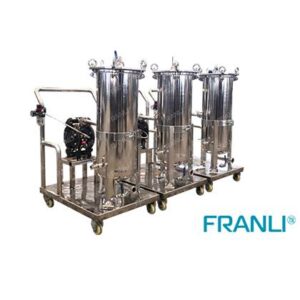
Filling Machine
The final step in the paint production line is the packaging of the finished product. A filling machine is a machine that is used to fill the paint into containers, such as cans or bottles. The filling machine ensures that the paint is filled to the correct level and that the containers are sealed properly. The filling machine has two options automatic and semi-automatic, and various packaging specifications of 0.5-1000L can meet the needs.
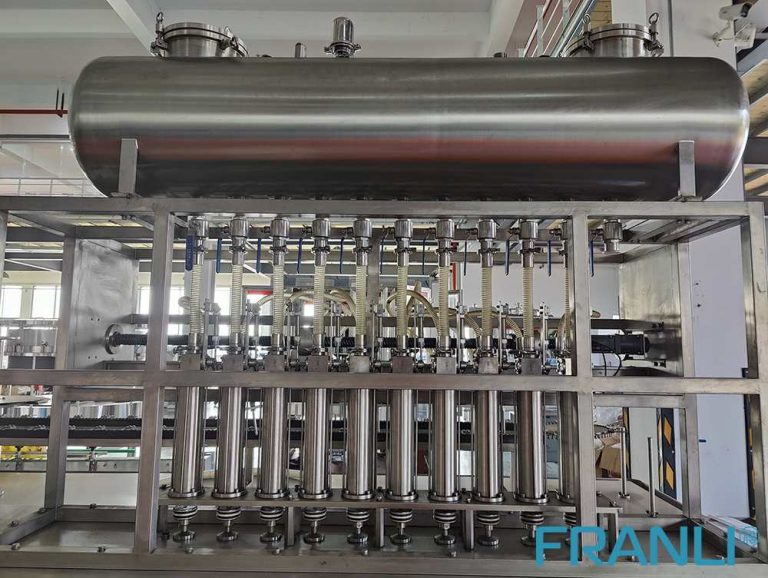
The general operation platform can be single-layer or three-layer, scattered on the top layer, grinding on the second layer, and paint mixing on the third layer, from top to bottom, which can effectively reduce the residue in the pipeline, reduce power transmission energy consumption; filtering and filling devices are installed at the bottom, which is convenient for transportation.
The paint production line is a complex system that requires a high level of precision and efficiency. The essential components of a paint production line include a high-speed disperser, a pipeline static mixer, a basket mill, a sand mill, a paint mixing kettle, a bag filter, and a filling machine. These machines work together to ensure that the paint is mixed, ground, filtered, and packaged to the highest standards.
Related Products
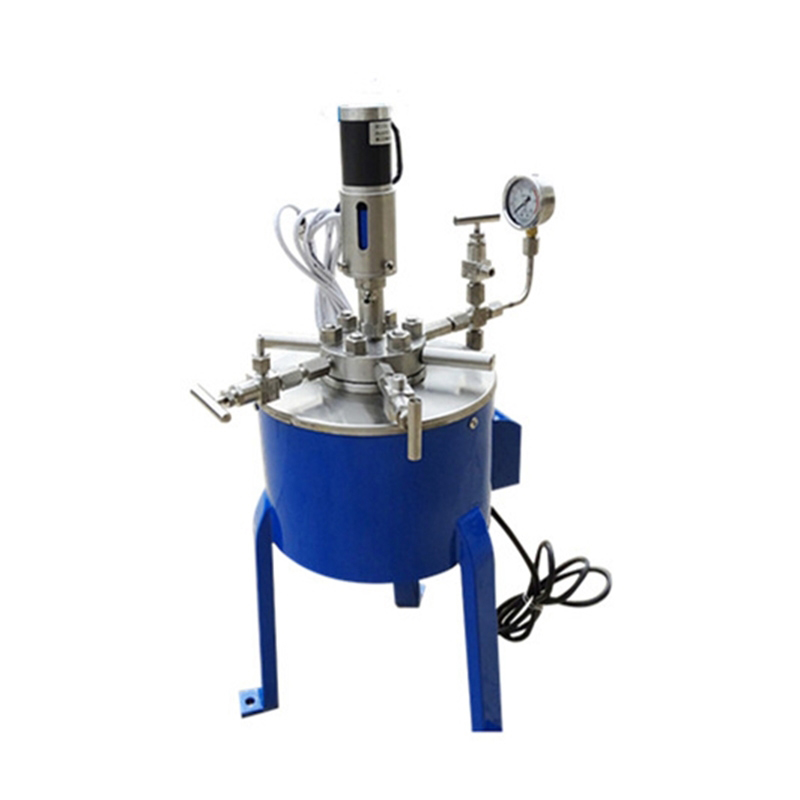
Laboratory Reactor: Guide to Stirring System
The laboratory reactor is composed of a pot body, a pot cover, an agitator, a jacket, a support and transmission device, a shaft seal device, etc.
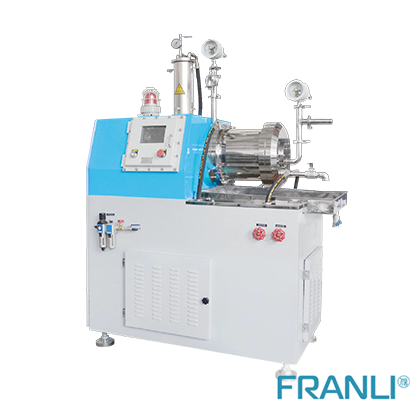
Grinding Media for Bead Mill | Zirconia Beads & Zirconium Silicate Beads
Bead mills mainly use grinding balls as media, and use impact, extrusion, and friction to achieve the final grinding effect, which mainly depends on the size and hardness of the grinding beads, the filling rate of the grinding beads, and the collision frequency adjustment between the grinding beads and the particles.
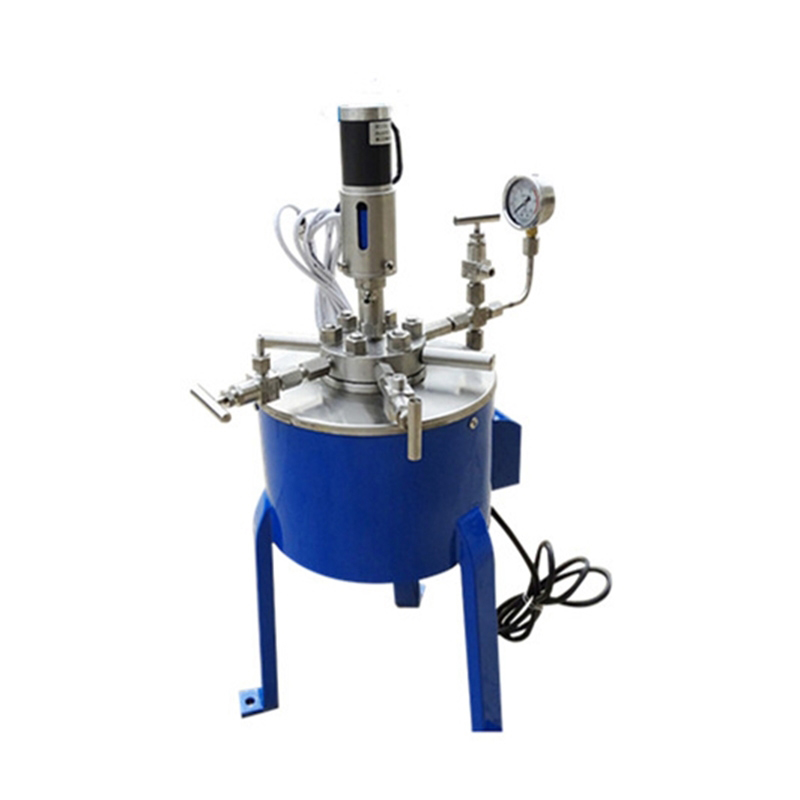
Overview of Laboratory Reactor
Laboratory reactors, also known as lab reactors, are essential tools in scientific research, product development, and process optimization. These reactors provide a controlled environment for conducting chemical reactions, mixing, dispersing, and homogenizing processes.
Related production lines
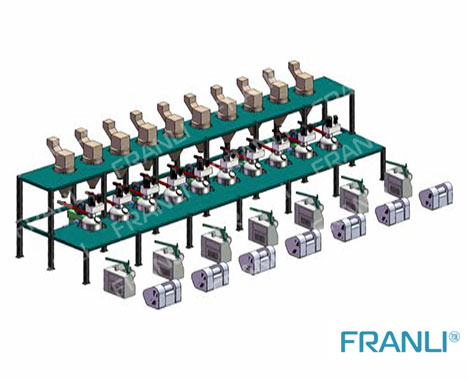
Offset Ink machine line
FRANLI is specialized in offset ink full line production for 20+ years. Helped customer save the cost, save the man power, also save the space.
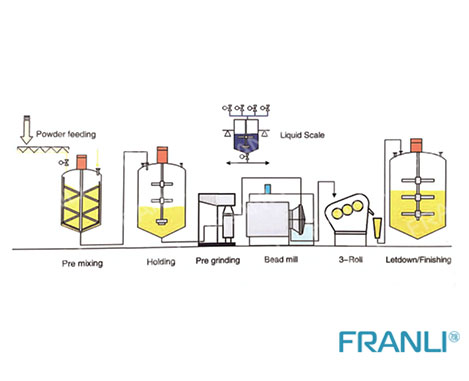
Offset Ink, UV Ink machine line
The FRANLI engineering company, offer the full set of UV INK Production Line, we can make the full drawing according with your factory size, formulas, weather and safety system.
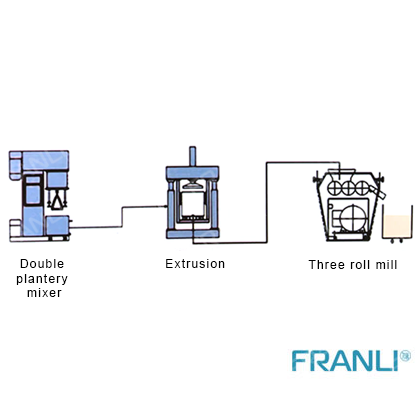
PCB INK Machine line
FRANLI supplies all equipments for the production of PCB inks, from the powder feeding station to the filling part.
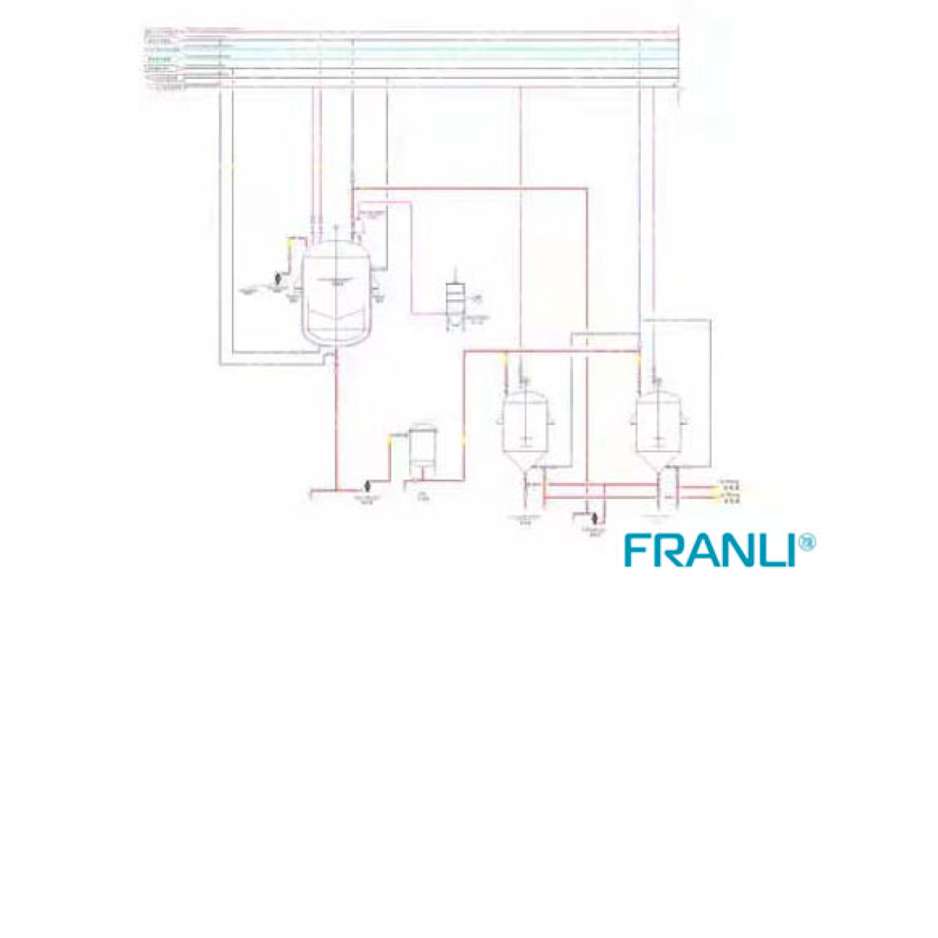
EW-pesticide line
The EW production line mainly mixes raw materials, solvents, and emulsifiers through a reactor (oil-based).
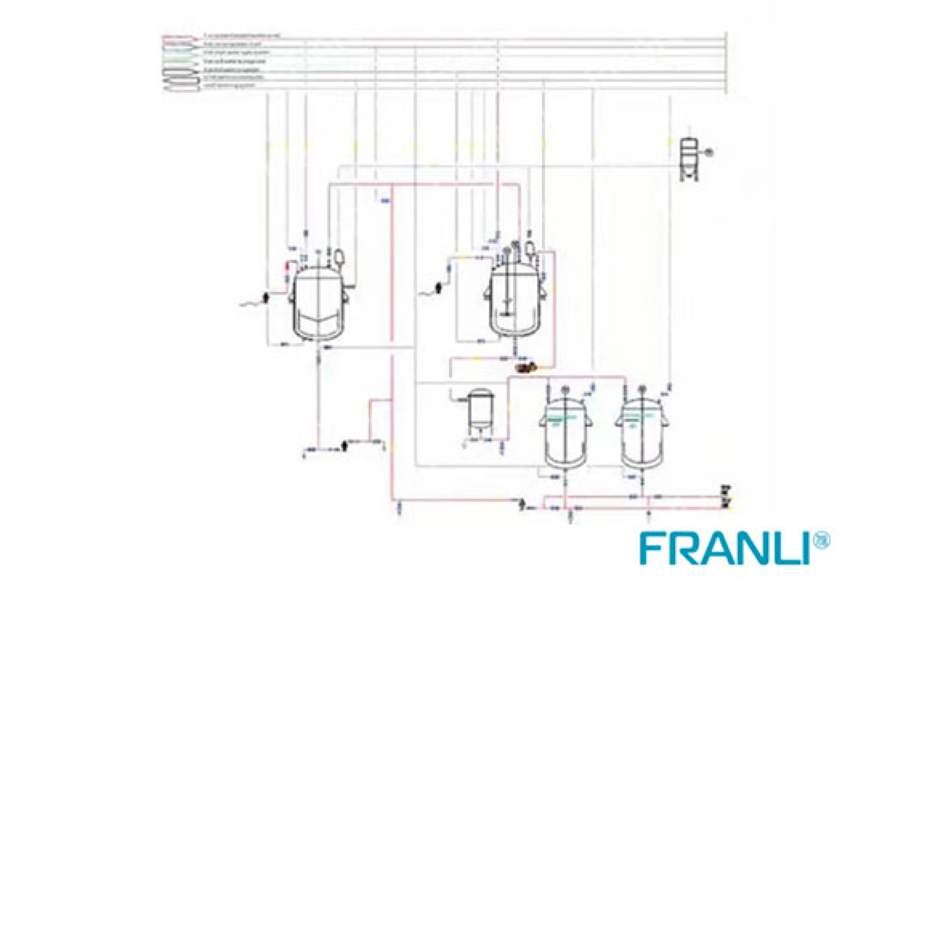
SL_EC pesticide line
The EC production line is mainly composed of an agitator mixer, bag filter, filling machine, etc.
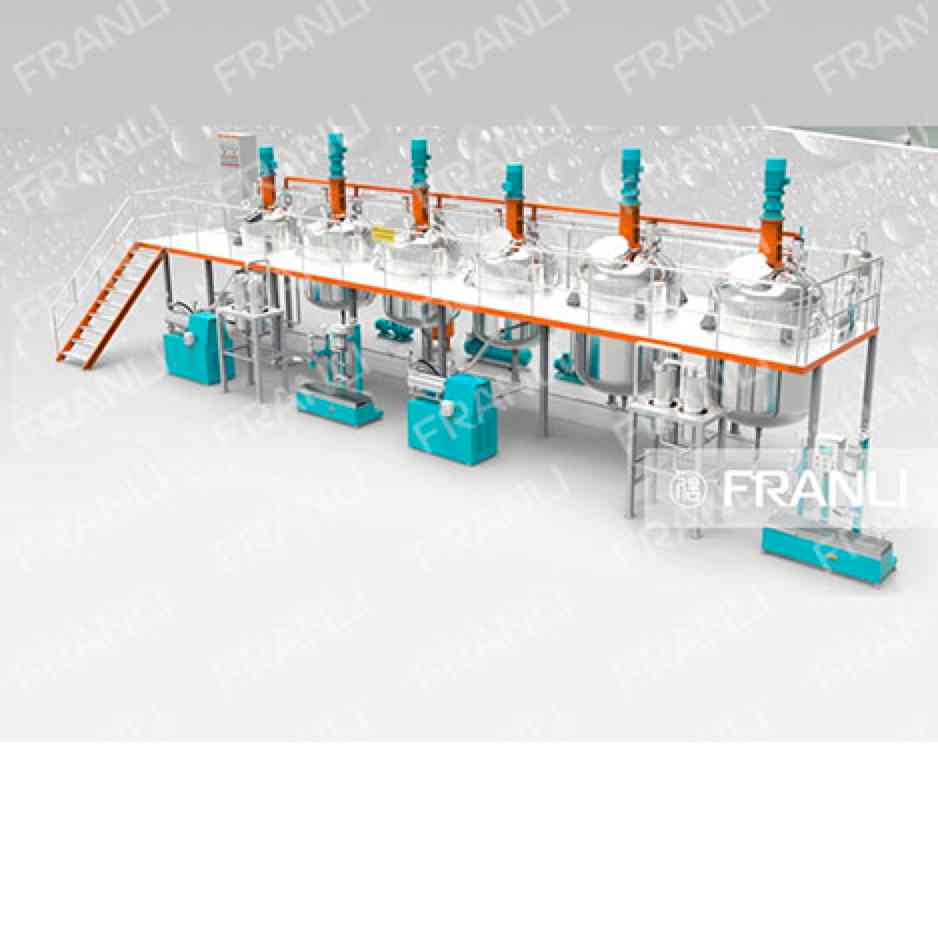
Automotive Paint machine line
The automotive paint machine line is mainly for the production and grinding of automotive paint, Automotive paint has many layers, such as Primer/electrophoretic layer, Medium coat, Colored coat, and Clearcoat.
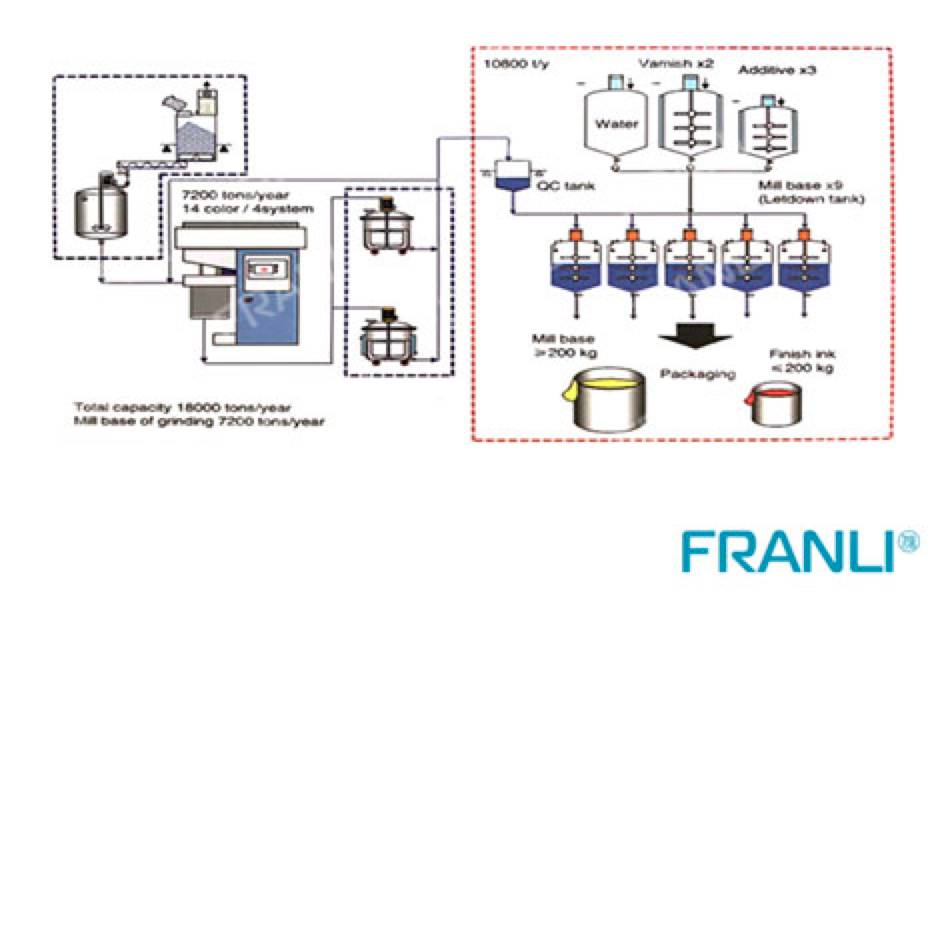
Digital Ink machine line
Franli has professional experience for digital ink machine line, we offered hundreds customers to expand production, or build up new project.