Home » The mixing process of the kneader
The mixing process of the kneader
Kneader
Details of Kneader
- The machine comprises a motor, cover press, main body, mixing chamber and rotor mechanism, gearbox, air control system, tilting machine, heating/cooling system, rubber belt transmission and base, etc.
- The kneader can be made into vacuum, pressure, atmospheric, Normal temperature, high temperature, low temperature, etc.
- The temperature adjustment method of a kneader can be the jacket, halfpipe, far-infrared tile, steam, hot water, heat transfer oil, electric heating, cooling water, chilled water, and other methods.
Application: Paint, Adhesive, Battery, Pharmaceutical industry, Cosmetic
For dispersion of products, kneader can be the significant machine that can be used here effectively. The processors involved here can rapidly understand its additional profits with the use of the right kind of disperser equipment for increasing the yield of the final product.
The other set of considerations involved here while buying a disperser is the servicing if you are achieving something that is more uptime with the help of the low-wear bearings, which can be maintained easily, having a competitive benefit overall your competitors who are there.
Today we would be discussing the dispersion kneader that would be offering a series of the aseptic mixers out there offering the unit set of product offerings in terms of the rest with the varied set of benefits and features that are out there, including the savings in energy along with the maximization of the product yield that would be explored in details here making the processing applications of the kneader in the laboratories a lot more significant.
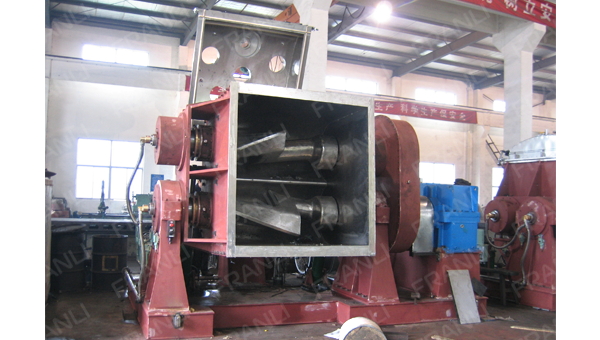
Understanding industrial dispersion with a kneader
Contemporary industrial processing would at all times be involved in some kind of product mixing, especially with the help of the laboratory kneader. The efficiencies involved in the mixing of a solid, gas, or liquid are also made possible here. There would be a lot of difficulties that would be involved in terms of the efficient mixing process over the industrial scaling. A massive deal of the efforts involved with engineering would get into the improvement as well as the designing of the mixing processes here.
It is mostly in the hygienic processing industries that the mixing of the liquids is made a frequent matter. The kneader mixer is now being supplied and manufactured with the help of prominent companies like Franli that are used over large-scale industries.
It is generally in batches. Lining up with the processor with the aid of the static mixers is how industrial mixing is done here as there is a massive range of technologies that are being used in the industrial kneader or mixer that are designed specifically for hygienic applications.
The following are being included under the commonest mixing technologies here:
1. ROTARY JET
These are specially designed for their use in several industries, including the brewery or beverage as well as the personal care and more. These dispensers can be used effectively for gas dispersion, powder mixing, tank cleaning, and even in liquid mixing.
The kneader here would be somewhat quite unique in which they would be applied over the cleaning industries. It is due to their pressure and flows attained over the transferor the circulation of the pump with the mix in-tank that has no requirement for any kind of agitator.
2. EDUCTORS
These are the set of jet-like pumps that would not require any kind of moving part for mixing together either the gases or the liquids.
3. POWDER MIXERS
These are commonly used over a diversified industry as they are also considered as the shear mixers that are able to mix liquid into the powders.
To gain a significant amount of efficiencies along with the consumption of the lowest amount of energy here, the product flow here through this mixer is optimized significantly.
The clean in place would be optimized distinctively through the open-design, complete drainability, and low-speed rotation of the kneader as it is effective for the removal of residue with less amount of contaminations through the wearing particles.
Keeping the ease of maintenance in their mindset is how they are designed here. The mixer would be experiencing less downtime over the normal production options, along with the requirement for spare impellers with the tools that are prepared for servicing is also made available here.
The machines here are significantly configurable to be used within the tanks that range in terms of their volumes as it would depend on their duty in terms of the media properties.
The kneader mixer rubber model arrives with its ability in terms of tailoring over the configuration for meeting the specific requirement of the customers.
There are a few specific drive units that are available in terms of the configuration of the units here, with the other room that is cleaner in terms of the finishes along with a treatment for sealed conversion. There would be an extended console that would be specified to be used over the tanks that are insulated within the kneader.
4. RIBBON KNEADER
These units are being used effectively over the low shear mixing of various elements ranging from the dry powders to the highly viscous pastes that would consume anything in its midst. There are several kneaders out there that can help with the dispersion process, even with the mixing with the help of a rubber kneader. These are considered the variations involving the designs where the agitators here would be making use of the plows as well as the paddles that can help with the mixing work.
These dispersion kneaders are now being manufactured efficiently with the help of the kneader mixer manufacturer, who can efficiently understand the need of it in this industry. One can easily make use of this in the production of the rubber materials as well as in the laboratories aiding the process of dispersion here.
The kneader is considered to be highly reliable and effective, known for its consistencies and versatilities as they have had them proven over the time-lapse in the work of the industrial dispersing processes. They are extremely critical machines that are being used over the vast industries known for their significance over the dispersion and mixing process.
Welcome to send inquiry to us and let’s make a win win business together !
Guidelines For Kneader
The dispersion kneader is suited for rubber and plastic mastication, as well as the blending of different rubber and plastic components. Small and medium-sized rubber and plastics manufacturers with a wide range of product types and colours, as well as food, dyes, pharmaceuticals, and ceramics, can benefit from the internal mixer.
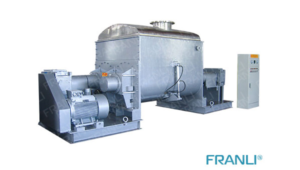
Sigma Kneader: The Solution for Mixing and Kneading
Sigma kneader is a versatile machine that can be used for mixing, kneading, and homogenizing a wide range of materials, including high-viscosity products.
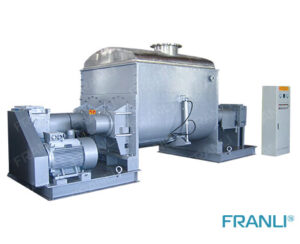
Sigma Mixer: Indispensable Equipment For Manufacturing
Sigma Mixer is a type of mixer that uses a unique mixing principle to achieve an efficient blending of materials. The mixer consists of two blades that rotate in opposite directions, creating a kneading and folding action that ensures thorough mixing. The blades are shaped like the Greek letter Sigma, hence the name Sigma Mixer.
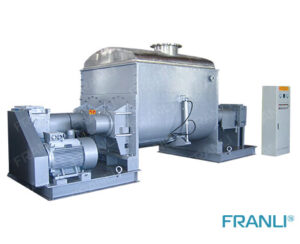
Sigma Blade Mixer: The Mixing Solution
The Sigma Blade Mixer is a robust and reliable mixing machine that uses a unique mixing principle to achieve superior results. It is a type of double-arm kneading mixer that features two blades that rotate in opposite directions.
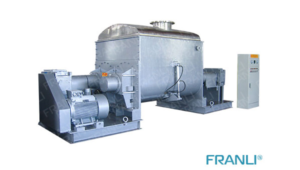
Vacuum Kneader: A Machine for Your Mixing Needs
The Vacuum Kneader is a type of mixer that utilizes a vacuum chamber to create a homogeneous mix of ingredients. It is designed to knead, mix, and disperse high-viscosity materials under vacuum conditions, resulting in a superior product.
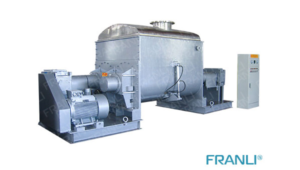
Efficiency and Effectiveness of Dispersion Kneader
The dispersion kneader has complete control over the mixing and blending of the raw materials to create an even mix that allows for better distribution. This device contains a mixing chamber with rotating blades made of high-quality steel.
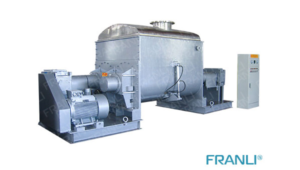
Vacuum kneader: high efficiency and environmental protection
A vacuum kneader is mainly used for stirring, mixing, and kneading high-viscosity and elastic-plastic materials. The most common fields include high-viscosity sealant, silicone rubber, neutral acid glass glue, chewing gum, bubble gum, aluminum silver paste, silica gel, paper pulp, cellulose, and other materials. It covers food, agrochemical, pharmaceutical, cosmetics, electronic paste, and other industries, and has been sought after by the industry.