Home » What is an Ointment Mill ?
What is an Ointment Mill ?
Ointment Mill
The ointment mills are largely used by the pharmaceutical industry, where color changes and smaller batches are needed. The mills use a strong shear force for dispersing active ingredients, and the ointment mill is popular due to its perfect cooling surface and temperature control.
Details of Ointment Mill
- Two types: handwheel and digital control gap
- Safe scraper socket, Emergency-stop
- Space-saving desktop models
- Drip tray for easy cleaning
Application: Paint, Adhesive, Battery, Pharmaceutical industry, Cosmetic
The shear forces are formed by some horizontally placed rollers that are moving in different directions for breaking the powder clumps and ingredients. Fine dispersing is possible in ointment mills. The easy cleaning property is an amazing benefit that comes with these mills. It is perfect for removing grittiness and getting good topical. The mills can provide your customers more pharmaceutically elegant ointment.
In ointment mills, no such cross-contamination happens. Moreover, it is a small tool that has small hold-ups and clearly defined stress which is still not present in other technologies. Today’s ointment mill is way better than any other machine for fine dispersing. The mills are utilized for making suspension ointments and emulsions cream or ointments. These ointment mills provide great results for oral, suppository, and topical applications.
While preparing creams and ointments with crystallized ingredients, these mills are the best and are superior to more advanced technologies of mixing. It has a large throughput and has porcelain rollers that are chemically inert. The ointment mills also have protection from mechanical overload and provide pure fineness. It is so small that it saves a lot of space.
How Does Ointment Mill Works?
An ointment mill comprises three rolls placed horizontally and rotates in opposite directions and at multiple speeds. After that, the material is then placed between a center roll and feed. This material is then transferred to an apron roll from that center roll by adhesion. In between those adjacent rolls, some shear forces are created, which produce dispersion. Reducing the roll’s distance enhances the shear and decreases the throughput. The gap setting that is commonly used is 0.001 inches.
After that, the milled material gets pulled out from the mill’s apron roll through the take-off knife. Such a cycle is repeated for improving dispersion and is repeated until the equilibrium of the particle size is reached. The ointment mills are one of the best technologies that have low throughput as well as needs skilled operators for preparing fine particle dispersion in ointments.
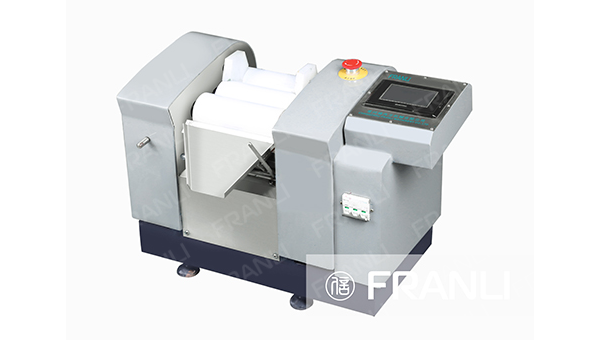
Benefits of The Ointment Mill
The ointment mill process has three parameters that are operation method, rheological behavior, and machine. The machine handles large viscosities range either with low line forces or with correct roll positioning systems. If a mill base adapts, then it can optimize the entire process. Rheological behavior is essential, but these are not always influenced.
Only ointment mills utilized during the dispersion process can guarantee that the entire product can pass through the two shear zones.
● Ointment mills’ rate of shear between all the rollers is the process’s most decisive factor.
● The shear rate is identified by the spacing between the rollers and circumferential speed.
● An ointment mill provides a controlled energy input which ensures good processing precision.
● The powder clumps of material and agglomerates are disintegrated, separated, and homogenized.
● It generates some fine particles that make a better quality product.
● It produces the least heat than other mills and has very little moisture loss.
● The noise level of the mill is also low, which is excellent for the work environment.
● Energy efficiency comes along with ointment mills.
Parameters of Ointment Milling
1. Pressure of Apron Knife:
Basically, the ointment mill’s apron knife must be set to the least pressure but consistent enough for scraping all the product from the roll. An apron knife, when it starts wearing, can become uneven. This can result in increasing the scraping of all products from the roll. Although it does not have a big influence changing the pressure of the apron knife can impact the project. While handling the ointment mill, the operator needs to take the pressure adjustment. This also affects repeatability, and for nice repeatability, the knife pressure must be maintained constant.
2. Roll Speed:
Another parameter of ointment milling is the roll speed. You should know that for certain products, the rolling speed can impact the end result. For repeatability, roll speed does not have that much role. The operators should know that at which speed the material must be run, either low or high speed. The modern ointment roll with variable speed contains the RPM indicator. The operator can also run these products at a similar speed every time.
3. Product Temperature:
The product temperature in an ointment mill is essential as it can affect the outcomes of the product. Almost all ointment mills have three valves that are used for allowing cool water to get into the roll’s annular space. This enables more cool water into the roll and decreases the temperature of the product. If the operators have handheld sensors of temperature, then they can monitor the temperatures of the roll. They can also maintain the product temperature as per the requirement when one batch is being processed.
The procedure needs diligent operators for running the mill. They can also fix a certain temperature, and fixing it is also simple. Here the system has temperatures correctly at the setpoints, which helps in maintaining the ideal temperature for the product.
4. Roll Pressure:
The main parameter is roll pressure that can be maintained through the roll set. There are handwheels that can rotate in the clockwise direction for pressurizing the nip. The more one will turn these handwheels, the more it gets pressurized. Ideally, the operators will notice the material bead on the mill’s feed roll for determining the ideal pressure amount. There are several systems that can measure the roll pressures. Most manufacturers include the handwheels, which push the hydraulic fluid in the bearing block and have an adjustment system exactly like the roll set of the ointment mill.
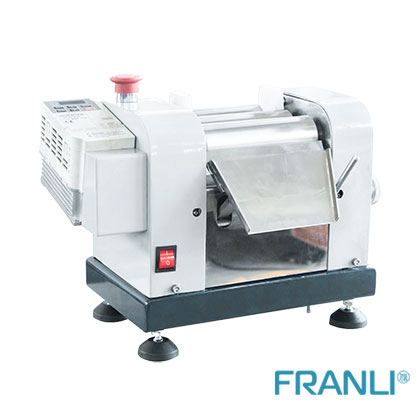
The ointment mills are robust machines that are specifically developed for the pharmaceutical industry, which need mill preparation in big volumes and in the best efficient way possible. For maximizing the reduction of particle size, these mills have excellent rollers and gap alignment systems where the calibration is easy. Therefore, you should go for only outstanding oil mills from trustable providers. Franli has been known for the best quality mills that are powerful enough for handling high-capacity compounds. Cleaning the mill is also quick and easy. For best quality mills, Franli is the ideal place to go.
Welcome to send inquiry to us and let’s make a win win business together !
Guidelines For Three Roll Mill
Three roll mills are widely used in a variety of chemical industries, from medium to high viscosity productions. FRANLI machine can break open all kinds of pigment, UV ink, offset ink, decorative paints, and Lubricants, it also can catch the greatest fineness in cosmetics/ lipstick and electronics industries.
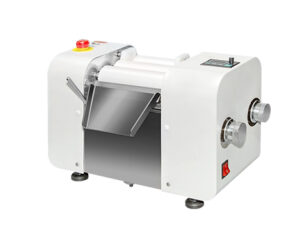
Three Roll Mill For Carbon Black|High Grinding & Dispersion
Three roll mill is the main equipment for grinding colored carbon black, as it is used extensively in rubber, plastics, paints, and inks, and some carbon black is added.
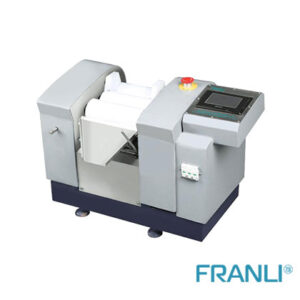
Laboratory Three Roll Mill|PLC Control System & Experimental
The laboratory three roll mill is equipped with the most advanced PLC functions to continuously improve the operability of the most primitive production equipment.
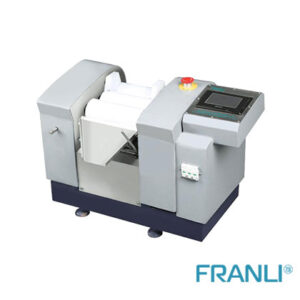
Three Roll Mill For Grease
The three roll mill plays a vital role in the grinding of grease. Grease is essentially a kind of lubricating oil, which is a solid or semi-solid product formed by one or more thickeners through the grinding and dispersing action of a three roll mill.
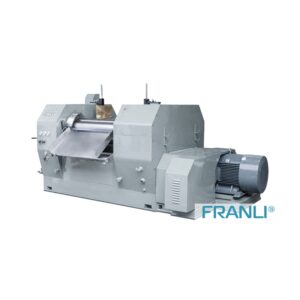
Three Roll Mill For Attapulgite
Three roll mill is the main equipment for grinding attapulgite. The attapulgite is ground and dispersed mainly because it is a natural colloid. Even if the size of the attapulgite reaches 0.1mm, it cannot be easily dispersed by the machine, so the final state of attapulgite formation has been greatly developed.
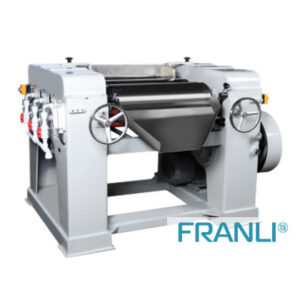
Rolls of a three-roll mill
The three-roll mill is mainly used for grinding materials of various viscosities and is one of the best wet grinding equipment. The dispersing and emulsification effect of the three-roll mill is excellent, especially for ink, paint, colloid, chocolate, plastic, cosmetics, etc., whether it is liquid slurry or paste material, the three-roll mill can work easily.
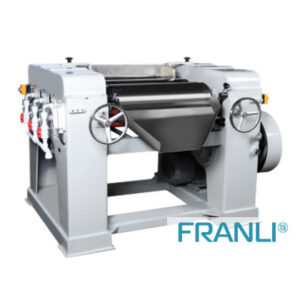
3 roll mill|Failure of the roll shaft & pulley
The 3 roll mill is a grinding and dispersing equipment, which plays an irreplaceable role in improving the quality of coating products.