Home » Special process stainless steel reactor
Special process stainless steel reactor
Stainless Steel Reactor
Details of Stainless Steel Reactor
- Using the latest reaction technology
- It has high temperature resistance, corrosion resistance, and high durability.
- Heating methods include steam, electric heater, high temperature heat transfer oil
- Using jacket, half pipe, fan coil, and other structures
Application: Chemicals, pharmaceuticals, dyes, pesticides, petroleum, food additives, etc.
- Heating form of the stainless steel reactor
- Stainless steel reactor jacket form
- Stirring form of the stainless steel reactor
- Transmission form and discharge method of the stainless steel reactor
- Design scheme structure of stainless steel reactor
- Installation steps of the stainless steel reactor
The material and opening of the chemical reactor can be formulated according to the user’s process and special requirements. The stainless steel reactor is mainly composed of four components: the inner storage tank, the jacket, the stirring device, and the support seat, and the thermal insulation structure must be adopted according to the processing technology.
Heating form of the stainless steel reactor
Heating forms include electric heating, oil heating, gas heating, water heating (or cooling), and open flame heating.
Stainless steel reactor jacket form
The jacket type is divided into jacket type and outer half-pipe type, and the jacket oil heating type is equipped with a diversion device.
Stirring form of the stainless steel reactor
The stirring forms generally include paddle type, anchor type, frame type, ribbon type, wall scraping type, etc. High-speed types include dispersed impeller type, turbine type, high shear type, and propeller type, for customers to choose according to the process.
Transmission form and discharge method of the stainless steel reactor
The transmission forms include ordinary motors, explosion-proof motors, electromagnetic speed-regulating motors, frequency converters, etc. The reducers include cycloidal pinwheel type, worm gear type, and planetary step-less speed change type. Shaft seals are ordinary water-cooling packing seals, combined with tetrafluoro packing seals and mechanical seals. The discharge forms include a ball valve and a downward expansion valve.
1. The stainless steel reactor has a customized stirring device, and the stirring shaft adopts a pressure-resistant environmental sanitation mechanical equipment sealing device to ensure the pressure in the tank and avoid unnecessary environmental pollution and material consumption caused by the leakage of materials in the tank.
2. The supporting form shall be suspended or floor-standing support type according to the actual operation regulations.
Design scheme structure of stainless steel reactor
Stainless steel reactors are divided into strip type, paddle type, turbo type, scraper type, and combined type. The rotating structure can adopt a cycloidal pinwheel reducer, which can meet the unique reaction requirements of various materials. For an infinitely variable speed reducer, the sealing device can be the mechanical seal, and the heating and cooling can use a jacket, half pipe, fan coil, etc., wear resistance, corrosion resistance, and other technical requirements for different office environments.
Note: All styles of stainless steel reactors can be designed and manufactured according to customer process requirements.
There are many heating methods for stainless steel reactors, the most common of which are steam, electric heating, and heat transfer oil, which meet the process needs in different operating environments such as acid resistance, high-temperature resistance, wear resistance, and corrosion resistance.
The heat transfer element of the stainless steel reactor can maintain the optimal temperature of the whole reaction process. The heat exchange area of the jacket is set in the chemical reactor, which can well meet the heat transfer requirements. Cleaning does not occupy the effective volume.
Commonly used heat exchange elements are jackets and inner coils. The stainless steel reactor can be planned and manufactured according to the user’s process requirements. Stainless steel reactor is composed of a kettle body, kettle cover, jacket, stirrer, transmission equipment, shaft sealing equipment, support, and so on.
Many process elements affect the occurrence of hot cracks during the welding of stainless steel reactors, such as joint form, process specifications, preheating temperature, structural rigidity, and workpiece clamping conditions, which all have a certain impact on the thermal crack resistance of the weld. Welding procedures and specifications.
The chemical reactor adopts high current, rapid welding, single-layer welding, straight-line running, etc. Process measures that easily cause welding stress will cause hot cracks to occur. Therefore, when conditions permit, low current and multi-layer welding should be used as much as possible to reduce the tendency of hot cracks.
When welding workpieces with large structural rigidity, preheating is often used. On the one hand, preheating can reduce the cooling rate, and the chemical reactor can reduce the tensile stress that occurs during the cooling process. On the other hand, it can also improve the crystallization conditions and reduce chemical and physical inhomogeneity. The preheating temperature depends on the chemical composition of the steel grade and the size of the structural rigidity.
The higher the carbon content of the steel, the more other alloying elements, and the greater the operating rigidity of the stainless steel reactor, the higher the preheating temperature is required. The use of the circulating cooling water treatment process by chemical reactor enterprises can not only solve the problems of unstable production and low heat transfer efficiency but also greatly save production water.
If the stainless steel reactor is faulty, there is leakage at the sealing surface. It can be checked that the cause of the failure is generally that the screw thread is loose; the sealing surface is damaged. The cleaning method of the reactor is to re-tighten the screw; re-grind and polish the sealing surface. The fault phenomenon is that there is leakage at the valve. The cause of the failure is that the valve stem (needle) and the sealing surface of the valve port are damaged. Cleaning method maintenance, replacement of stem (needle), valve port.
Installation steps of the stainless steel reactor
(1) First check the quality of the seal of the reactor (whether there are scratches on the end faces of the dynamic and static rings).
(2) Wipe the O-ring of the moving ring and foreign objects on the surface of the moving and static rings with a clean soft cloth, and apply a small amount of lubricating oil to the surface according to the application requirements of the medium in the reaction tank.
(3) Review the levelness of the static ring of the mechanical seal and the verticality of the sealing section of the mixing shaft with a spirit level and a dial gauge, and correct them to the specified requirements.
(4) Install and fix the base of the mechanical seal and the fixing ring, and adjust the hexagonal set screws of the fixing ring on the mixing shaft, so that the tension spring of the mechanical seal is evenly stressed, and the end faces of the dynamic and static rings of the mechanical seal are tightly combined.
(5) If the balance tank is set on the frame as required, connect the pipeline between the inlet and outlet of the sealing liquid and the mechanical seal, connect the pipeline of the nitrogen cylinder, the pressure reducer, and the balance tank, and connect it after the static pressure test meets the requirements. The water jacket, through cooling water, waits for the whole machine to test.
(6) When the temperature of the medium in the stainless steel reactor is below 80°C, add oil to the cooling tank for cooling. The type of refueling should not affect the quality of the materials in the tank. Generally, it should have high vaporization heat, less clean impurities, and good quality. Lubrication function. When the medium temperature is higher than 80℃, the bottom cooling water jacket and the cooling tank are cooled by circulating water.
Welcome to send inquiry to us and let’s make a win win business together !
Guidelines For Stainless Steel Reactor
FRANLI has several complete stainless steel reactor production lines. Our stainless steel reactor adopts the latest infinitely variable speed reducer device, the sealing device can be a mechanical seal, and the heating and cooling can adopt the structure of a jacket, half pipe, fan coil, etc., The heating methods include steam, electric heater, and high-temperature heat transfer oil to achieve different safe processing environments such as acid resistance, heat resistance, wear resistance, and corrosion resistance.
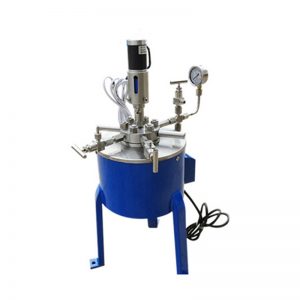
Laboratory Reactor: Guide to Stirring System
The laboratory reactor is composed of a pot body, a pot cover, an agitator, a jacket, a support and transmission device, a shaft seal device, etc.
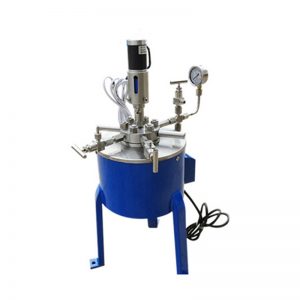
Overview of Laboratory Reactor
Laboratory reactors, also known as lab reactors, are essential tools in scientific research, product development, and process optimization. These reactors provide a controlled environment for conducting chemical reactions, mixing, dispersing, and homogenizing processes.
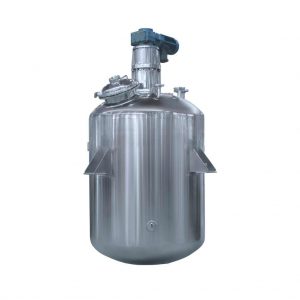
What is A Stainless Steel Reactor?
Stainless steel reactors are essential equipment in various industries, including chemical, pharmaceutical, biotechnology, and food processing.
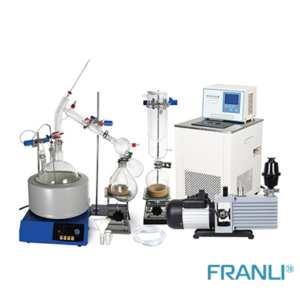
Glass Reactor & Chemical Equipment
Glass reactors are essential equipment widely used in the chemical, pharmaceutical, and biotechnology industries. They come in various types, suitable for different applications.
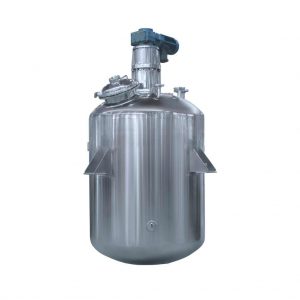
Operating Guide for Laboratory Reactors
Laboratory reactors play a crucial role in chemical research and development. Understanding the proper operating procedures is essential to ensure accurate results and maintain a safe working environment.
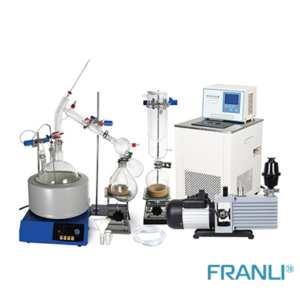
Glass Reactors and Selection of Stirring Blades
Glass reactors, also referred to as glass reaction vessels, are vessels made from high-quality borosilicate glass material.