Home » Triple Shaft Mixer | anchor type, butterfly type & frame type
Triple Shaft Mixer | anchor type, butterfly type & frame type
Triple Shaft Mixer
Advantages of Triple Shaft mixer
- Long life with a sturdy mixing bowl made by a fully automatic welding robot
Can manufacture all kinds of concrete - High uniformity even with a short mixing time
Parts with excellent durability and wear resistance - Easy maintenance with replaceable bolt lining for large maintenance doors
Automatic lubrication system - Compact design and universal compatibility with existing concrete plants
Application: Paint, Adhesive, Battery, Pharmaceutical industry, Cosmetic
The triple shaft mixer extends the working area by adding a rotating stator mixer with a large displacement or a second quick distributor. High shear stator and rotary mixer can emulsify and homogenize products that require higher shear forces to reduce particles into smaller sizes.
Different materials have different functions that include; anchor type, butterfly type, and frame type. Driven by a power unit, it turns the rudder in a fixed direction. In the process of rotation, the material rotates axially and radially. The material in the mixer moves axially and circularly at the same time.
Therefore, there are various forms of agitation that include; shear agitation and diffusion agitation. The diffusion disc rotates at high speed, causing the material to flow in a ring, creating a strong vortex. Turn to the bottom of the vortex. Strong shear, impact, and friction occur between the particles, achieving rapid dispersion and dissolution functions. The stirrer plate moves in a circular motion, generating good radial forces and accelerating the material. Based on this, let’s discuss the detailed aspects of the triple shaft mixer.
What makes the triple shaft mixer unique?
● High-speed circulation to improve distribution efficiency
The mixer has precision technology for emulsification heads, advanced rotor, and stator adjustments. A powerful motor spins at high speed, creating a vacuum between the rotor and the stator. The materials are filled to the top of the rotor and stator.
● High shear speed
Due to the high kinetic energy, the rotor achieves very high linear velocities, and the material is blown off after strong impact, crushing, centrifugation, the friction of the liquid layer, and high shift between the rotor and stator gaps. The high shear speed enhances more material mixing.
Triple shaft mixer specifications
Mixing the arm and blade with the two shafts is very difficult to maintain and replace. The mixer has unique wear-resistant centers and sieving blades made of Ultra Tungsten designated to address specific operational issues. The cast steel arm is designated to last longer in this harsh environment. Strong turbulence occurs under the action of forces in various directions. The material is subjected to repeated cycles of polymerization, dispersion, homogenization, purification, and shaving to produce a stable emulsion after some time under the appropriate amount of emulsifier and mature technique. The elevator’s hydraulic triple shaft mixer drives the hydraulic piston up and down by the operation of the hydraulic pump. The hydraulic pump rotates the entire transmission mechanism and working group up and down.
How does the triple shaft mixer work?
The mixer has a centrally mounted low-speed anchor spring or spiral blade that fights against the walls of the mixing bowl and two additional high-speed shafts. High-speed blades usually provide high shear forces to disperse or dissolve components. The low-speed rotor feeds the high-speed blade, which mixes the dough and folds into a container, and improves product uniformity by rubbing the walls. The mixers are used to mix medium to high viscosity materials. High-speed distributors require low-speed blades to obtain a uniform mixture, as they have a limited number of zones that affect viscous products. If equipped with a scraper, slow rotors also help with heat transfer.
For highly viscous materials, the mixers with different mixing elements are used for specific functions. Some designs are equipped with anchor impellers to move materials near the mixing vessel and high speed, high slip impellers that provide a high cutting action. Others can be equipped with spirals or worm screws, as well as anchors and stirrers. Depending on the application, these mixers are covered for heating or cooling. The mixer can be designed to operate in a high vacuum. Depending on the viscosity of the final mixture and the degassing method of the product, the mixer can be made with a structured surface or a solid surface. An interchangeable mixer with a device for lifting the mixing head and removing the mixing element from the mixing bowl is provided for stirring the mixing bowl after mixing. For highly viscous materials, a special hydraulic cylinder is required to remove the material from the mixing bowl.
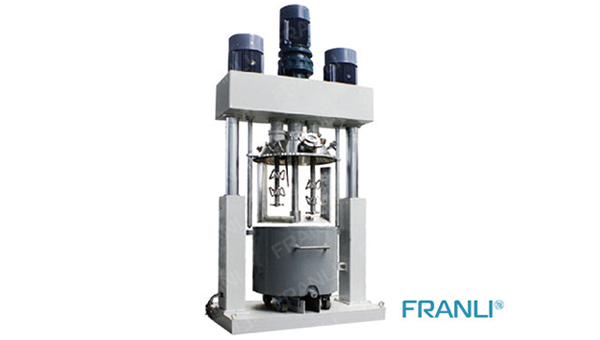
The triple shaft mixer has a high-speed and dispersing motor. The anchor feeds the product into the distributor paddle at high speed and keeps the mixture in constant motion.
Application of triple shaft mixer
The mixer works best in mixing aggregates, cement, water, and additives for better concrete quality and less water-cement bond. The two mixing shafts, which are equipped with arms and rotating blades while at the same time, ensure that the cement is evenly distributed in the mixture to reduce the cement dosage according to the concrete strength. The geometry of the rotors and the position of the mixing arms give the mixture a spiral movement, which results in ideal, and reliable particles with an even distribution of cement on each dispersion axis, which can create an additional mixture.
On the other hand, a rotating stator can be used as a two-axis mixer in some areas. The rotating stator provides high mechanical and hydraulic shear, which is essential in breaking solids in liquids or emulsions.
The triple shaft mixer is a device available at Franli with various functions such as diffusion, emulsion, and blending. The company produces multi-shaft mixers with more than 20 years of experience. These multi-shaft mixers are ideal for mixing systems with high viscosity or high dispersion. A combination of several mixing methods can be used to complete the mixing and dispersing process faster and more completely.
Welcome to send inquiry to us and let’s make a win win business together !
Guidelines For Multi Shaft Mixer
FRANLI customized different kinds of multi-shaft mixers for more than 300+ customers. This kind of machine works in the coating industry, medicine industry, cosmetic industry, and other high technology chemical industries.
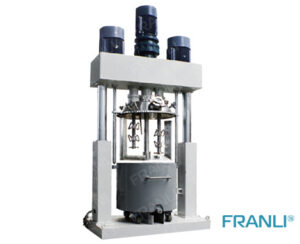
The Application of Triple Shaft Mixers in Adhesives
Triple-shaft mixers, also known as multi-shaft mixers, are innovative blending machines designed to efficiently mix and disperse various components in adhesives.
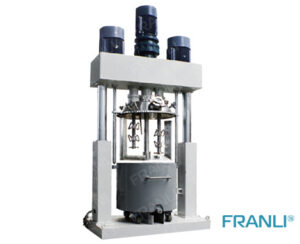
Triple Shaft Mixer: Ideal Equipment for Ink Production
Triple shaft mixers are capable of handling a wide range of ink formulations, including solvent-based, water-based, UV-curable, and hybrid inks.
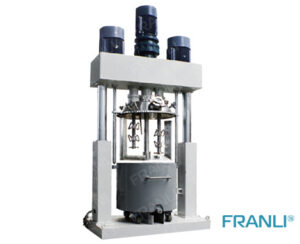
The Versatility and Application of Triple Shaft Mixers in Coatings
Triple shaft mixers have revolutionized the coating industry by providing efficient and versatile solutions for mixing raw materials.
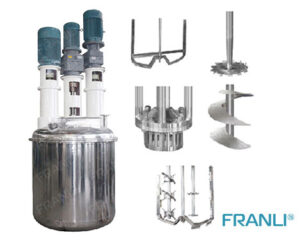
What is a Multi-Shaft Mixer?
A multi-shaft mixer is a type of industrial mixer that has more than one mixing shaft. These mixers are designed to mix multiple ingredients simultaneously, allowing for more efficient and effective mixing.
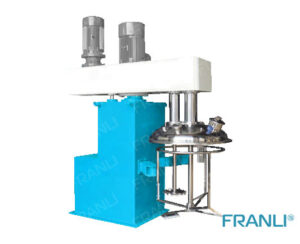
Dual Shaft Mixer – Dispersion & Stirring
The dual shaft mixer is the best mixer to dissolve the specific ingredients with appropriate shear capacity. This activity is performed by the high-speed shafts situated in the mixer and provides you with the perfect uniformity of the product. It also contains an Anchor agitator and a High-Speed Disperser that offer you the best quality and consistency.
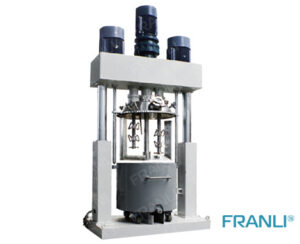
Triple Shaft Mixer | anchor type, butterfly type & frame type
The FRANLI triple shaft mixer extends the working area by adding a rotating stator mixer with a large displacement or a second quick distributor. High shear stator and rotary mixer can emulsify and homogenize products that require higher shear forces to reduce particles into smaller sizes.