Home » Chemical Reactor For Laboratory
Chemical Reactor For Laboratory
The chemical reactor is a reactor provided for synthesizing chemical substances under certain temperatures and certain pressure conditions. It is widely used in scientific research experiments in new materials, energy, environmental engineering, and other fields, and is a commonly used small reactor for scientific research in teaching and scientific research units in colleges and universities.
In the laboratory, we usually use hydrothermal reactors, which are also known as high-pressure digestion tanks, pressure-dissolving bombs, polymerization reactors, crystallization reactors, etc. The dose synthesis reaction is also used in the strong acid or strong alkali in the tank and in a closed environment of high temperature and high pressure to achieve the purpose of quickly digesting insoluble substances.
The operation process of the chemical reactor can be divided into six steps:
- Clean the reactor
Depending on the specific experiment, different reagents are used for physical and chemical cleaning.
- Filling material
The reactants were safely transferred into the reactor in turn.
- Seal the reactor
- Heating up, keeping warm, cooling down
- Open the reactor
- Take out the material
Precautions for the use of chemical reactors
Sealing performance
The reaction kettle is precision equipment. The sealing ring adopts the form of conical contact and sealing, and the main bolts are tightened to make them press each other to achieve the purpose of sealing. Therefore, special care must be taken for the sealing cone to avoid damage caused by various collisions. When installing the cover, first place the chemical reaction kettle body, and then put the reaction kettle cover in a fixed position and carefully install it on the reaction kettle body. When tightening the main bolts, you must tighten them diagonally and symmetrically. , The force should be uniform, and it is not allowed to tilt the reaction kettle cover to one side to achieve a good sealing effect, and the specified tightening torque should not be exceeded to prevent the sealing surface from being squeezed or accelerated wear. All threaded connections need to be coated with oil or oil-mixed graphite when assembling. If the sealing surface is damaged, it needs to be reworked and repaired to restore good sealing performance.
Sealing operation
The air inlet and exhaust valve of the chemical reaction kettle are sealed with a needle valve. When closing, just turn the valve needle gently and press the cover tightly to achieve a good seal. It is forbidden to use excessive force to avoid damage to the sealing surface.
Temperature rise and pressure test
The chemical reaction kettle should be heated, pressurized, and sealed before use. The test medium can be air or nitrogen, but it is best to use inert gas. It is strictly forbidden to use oxygen or other flammable and explosive gases. The temperature increase and pressure increase must be carried out slowly. The heating rate is not more than 80 degrees/hour. During the pressure test, connect the inlet valve of the chemical reactor with the compressor (or high-pressure pump) with a connecting pipe. The pressure increase must be carried out in stages, with 20% of the working pressure as the interval, stay for 5 minutes for each liter level, and stay for 30 minutes when the test pressure is raised to check the sealing condition. The test pressure is 100-105% working pressure. If a leak is found, the pressure should be reduced first, and then the nut and joint should be properly tightened. It is strictly forbidden to tighten the nut and joint under high pressure.
Cooling process
Rapid cooling and rapid heating are prohibited in the reaction process to prevent excessive temperature stress from causing cracks in the reactor body. After the reaction is over, firstly cool down, which can be cooled by water (exothermic reaction) or air-cooled, and then release the high-pressure gas in the reaction kettle to reduce the pressure to normal pressure, and then loosen the bolts symmetrically and evenly. In the process of opening the lid, special attention should be paid to protecting the sealing surface, and the reaction kettle lid should be lifted evenly to avoid damage to the sealing ring of the reaction kettle lid and the kettle body due to collision.
Follow-up processing
After each operation, the residues on the kettle body and the kettle cover should be removed. All sealing surfaces on the chemical reaction kettle should be cleaned frequently and kept dry. Hard objects or soft objects with rough surfaces are not allowed to be cleaned.
Maintenance of laboratory reactor
Regularly check to ensure that safety valves, explosion-proof membranes, pressure gauges, thermometers, and other safety devices are accurate, sensitive, and easy to use. The red line of the pressure gauge must be correctly drawn, and the explosion-proof membrane must not have internal leakage;
- Ensure that there is no abnormal vibration and noise in the chemical reaction kettle;
- Check the start-up temperature of the reducer, motor, base bearing, and other parts: the general temperature is ≤ 40°C, and the maximum temperature is ≤60°C (the back of the hand can stay on the top for more than 8 seconds, which is normal).
- Ensure that all the inlet and outlet valves of the chemical reaction kettle are in good condition and available, and any problems must be dealt with in time;
- The flange and base of the chemical reaction kettle should not have loose bolts, and the safety shield should be intact and reliable;
- The body of the chemical reaction kettle should not have cracks, deformation, bulging, perforation, corrosion, leakage, etc.;
- l Do a good job in the sanitation of the chemical reaction kettle to ensure that there is no oil pollution and the equipment is in its true colors;
- Regularly check the stirring of the chemical reaction kettle, coils, and other accessories in the pot, tighten the loose bolts, and replace the relevant parts if necessary.
Copyright Notice :
This article only represents the author’s point of view.
This article is published under the authorization of the author.
Source: Franli
This article address : Chemical Reactor For Laboratory
Related Products
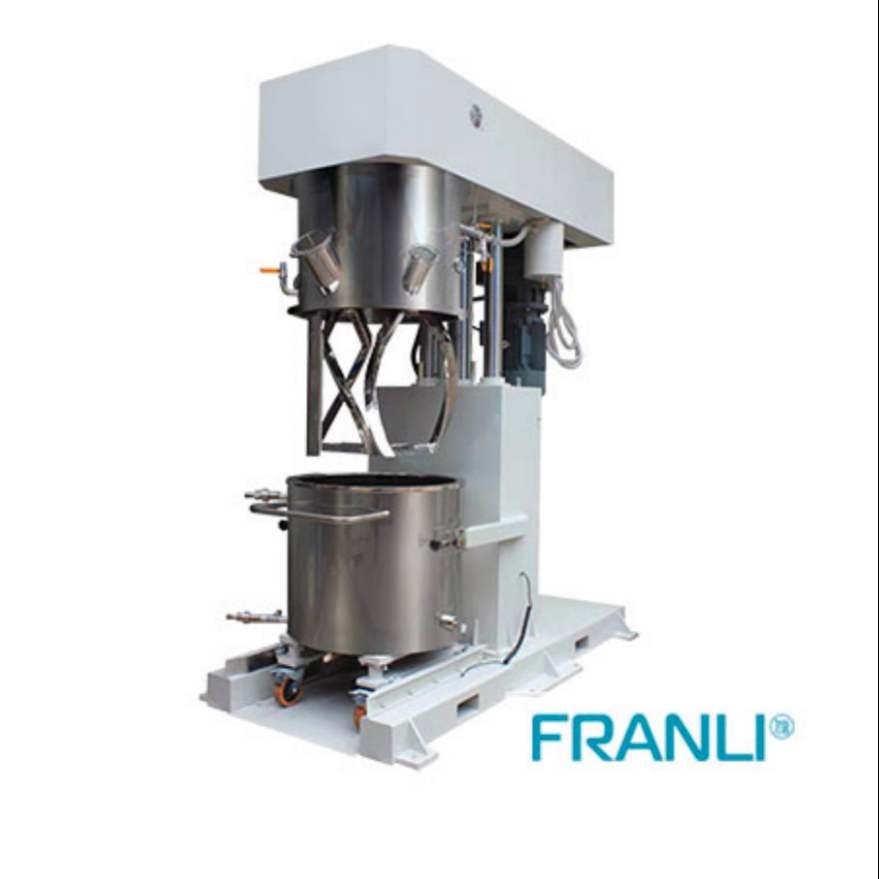
Vacuum Double Planetary Mixer
A Vacuum double planetary mixer is an essential part of any industry to mixing particular material. A double planetary mixer contains two blades that help mix by revolving on their axis in the vessel.
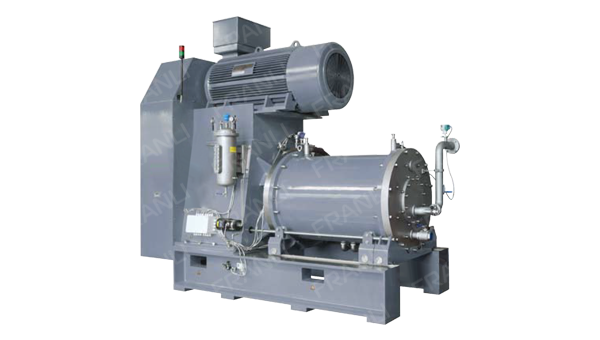
Agitator bead mill
Agitator bead mill’s pins are uniform distributed type, pre-milling your material when feeding material into chamber. The agitator bead mill has a stronger power motor, material milled by bead, and pins in the chamber.
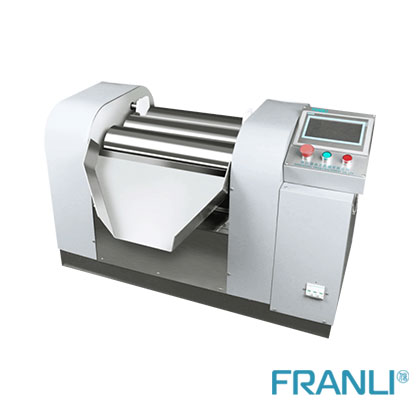
Digital Control Three Roll Mill
The roller of the digital control three roll mill is made of zirconia ceramic material and equipped with a frequency conversion speed regulating device to meet the grinding needs of different materials.
News
Laboratory Reactor: Guide to Stirring System
The laboratory reactor is composed of a pot body, a pot cover, an agitator, a jacket, a support and transmission device, a shaft seal device, etc.
Grinding Media for Bead Mill | Zirconia Beads & Zirconium Silicate Beads
Bead mills mainly use grinding balls as media, and use impact, extrusion, and friction to achieve the final grinding effect, which mainly depends on the size and hardness of the grinding beads, the filling rate of the grinding beads, and the collision frequency adjustment between the grinding beads and the particles.
Overview of Laboratory Reactor
Laboratory reactors, also known as lab reactors, are essential tools in scientific research, product development, and process optimization. These reactors provide a controlled environment for conducting chemical reactions, mixing, dispersing, and homogenizing processes.
Bead mills | Manufacturing technology in various industries
Bead mills, also known as sand mills or grinding mills, are versatile machines widely used across various industries for the wet grinding and dispersion of solid particles in liquid media.
Ribbon Blender Mixer Equipment
A ribbon blender mixer, also known as a ribbon mixer or horizontal ribbon blender, is a powerful industrial machine designed for thorough and efficient blending of various materials.
What is A Stainless Steel Reactor?
Stainless steel reactors are essential equipment in various industries, including chemical, pharmaceutical, biotechnology, and food processing.