Home » Double Planetary Mixer
Double Planetary Mixer
Double Planetary Mixer video
Welcome to send inquiry to us and let’s make a win win business together !
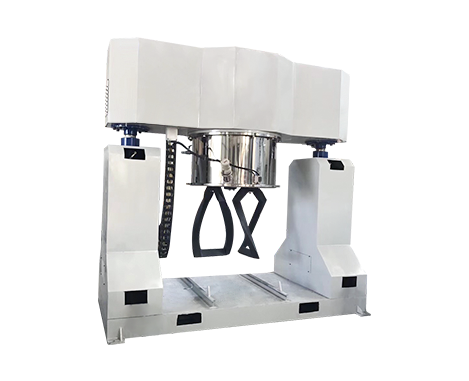
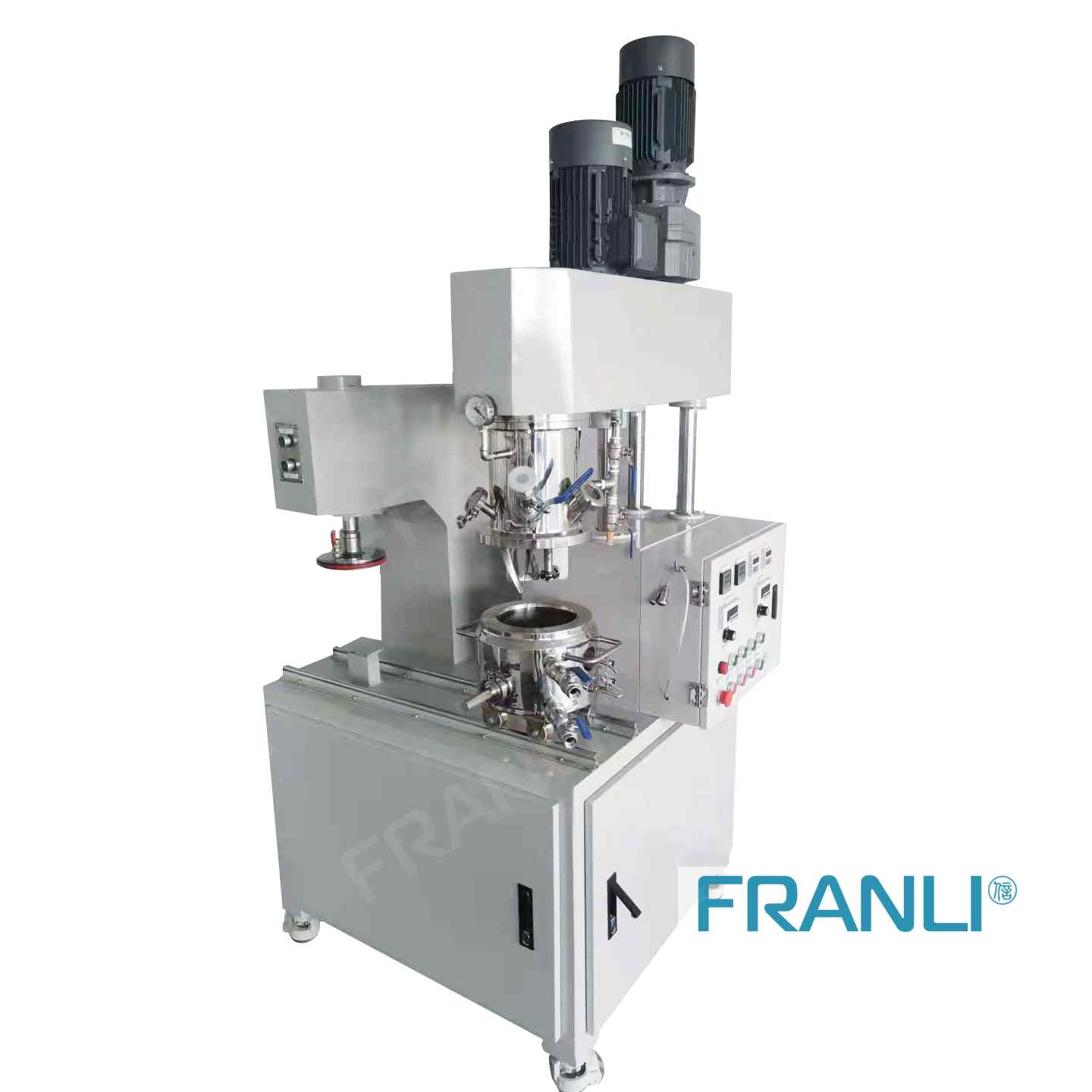
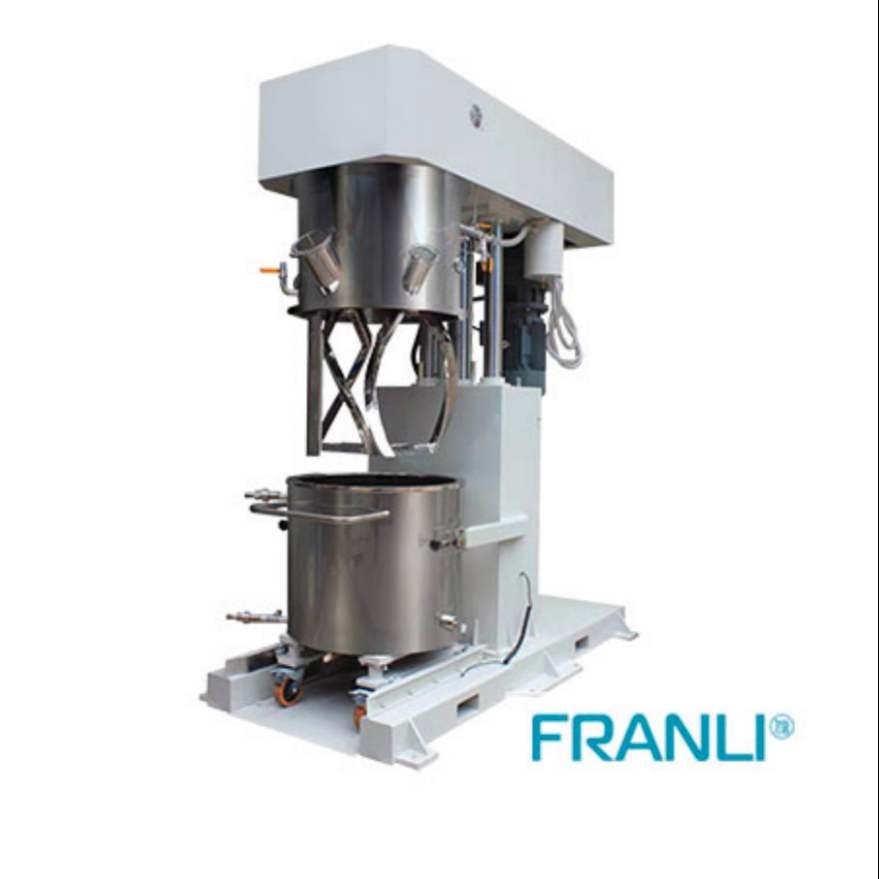
Guidelines For Double Planetary Mixer
Double planetary mixers consist of several key components that work together to ensure efficient and consistent mixing. These components include:
1. Mixing Vessel or Bowl
The mixing vessel or bowl is the central component where the raw materials are loaded and mixed. It can be made of various materials, such as stainless steel, carbon steel, or specialized alloys, depending on the application and the materials being processed.
2. Planetary Blades
The planetary blades are the primary mixing elements in a double planetary mixer. These blades rotate on their own axes while simultaneously revolving around the central axis of the mixing vessel. The design and configuration of the planetary blades can vary depending on the application and the desired mixing action.
3. Scraper Blades
Scraper blades are designed to scrape the sides and bottom of the mixing vessel, ensuring that no material remains unmixed. These blades help to prevent the formation of dead zones and ensure thorough mixing and dispersion of the materials.
4. Gearbox and Drive System
The gearbox and drive system are responsible for powering the rotational and revolving motions of the planetary blades. These components are designed to provide high torque and precise speed control, ensuring efficient mixing and consistent product quality.
5. Control System
Modern double planetary mixers are equipped with advanced control systems that allow for precise monitoring and adjustment of various parameters, such as mixing speed, temperature, and vacuum levels. These control systems often feature user-friendly interfaces and programmable recipes for consistent and repeatable mixing processes.
6. Safety Features
Double planetary mixers incorporate various safety features to ensure safe operation and protect operators from potential hazards. These features may include emergency stop buttons, interlocks, and guarding systems to prevent accidental contact with moving parts.
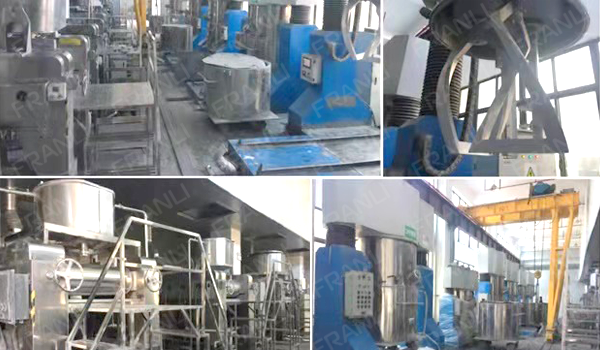
The scope of application of double planetary mixer:
Chemicals: inks, sealants, adhesives, synthetic resin rubber, putty, synthetic materials, powder materials, ceramic pigments, abrasives, etc.
Energy: battery paste, paste, etc.
Electronic devices: solder paste, ceramic paste, magnetic materials, silicone ink, electronic adhesive, PVC plastic, paste, etc.
Medicines: ointments, polymer gels, dental products, etc.
Cosmetics, daily chemicals: moisturizer, lipstick, lotion, nail polish, soap, mascara, facial mask.
Food: seasoning, jam, chocolate, etc.
Pesticides: pesticide powder, chemical fertilizers, etc.
The production process using double planetary mixers typically involves the following steps:
1. Material Loading: The raw materials, such as powders, liquids, or pastes, are loaded into the mixing vessel or bowl of the double planetary mixer.
2. Mixing and Dispersion: The mixer’s planetary blades rotate on their own axes while simultaneously revolving around the central axis of the mixing vessel. This dual rotational motion creates a powerful kneading and shearing action, ensuring thorough mixing and dispersion of the materials.
3. Temperature Control (Optional): Depending on the application, the mixing vessel can be equipped with a heating or cooling jacket to maintain the desired temperature during the mixing process. This is particularly important for temperature-sensitive materials or processes that require specific temperature ranges.
4. Vacuum Degassing (Optional): For applications that require the removal of air bubbles or volatile components, the double planetary mixer can be integrated with a vacuum system. This process, known as vacuum degassing, helps to eliminate entrapped air and improve the quality of the final product.
5. Discharge and Packaging: Once the desired consistency and homogeneity are achieved, the mixed product is discharged from the mixing vessel and transferred to the appropriate packaging or further processing stages.
Double planetary mixers are available in various types and configurations to meet the diverse requirements of different industries and applications. Some common types include:
1. Laboratory-Scale Double Planetary Mixers
These mixers are designed for small-scale operations, such as research and development, pilot plant production, or small-batch manufacturing. They typically have mixing vessel capacities ranging from a few liters to several gallons.
2. Industrial-Scale Double Planetary Mixers
pacities ranging from several gallons to hundreds of gallons. These mixers are commonly found in commercial manufacturing facilities and are often integrated into larger production lines.
3. Vacuum Double Planetary Mixers
Vacuum double planetary mixers are equipped with a vacuum system that allows for mixing under vacuum conditions. This type of mixer is particularly useful for applications that require the removal of air bubbles or volatile components, such as in the production of certain adhesives, sealants, or coatings.
4. Heated Double Planetary Mixers
Heated double planetary mixers feature a heating system, typically a jacketed mixing vessel, that allows for temperature control during the mixing process. These mixers are essential for applications involving temperature-sensitive materials or processes that require specific temperature ranges.
Industrial-scale double planetary mixers are designed for large-scale production and can handle mixing vessel ca

Advantages and Applications Of Dual Planetary Mixer
A dual planetary mixer is a versatile and efficient machine that is used in various industries, including food, pharmaceuticals, and cosmetics.

How to buy a double planet mixer?
This double planetary mixer can mix all types of viscosity of the material in no time. This double planetary mixer contains high-capacity blades that can work from 1 million centipoises to 8 million centipoises.

Double Planetary Mixer For Sale
FRANLI double planetary mixer is a high-efficiency, multi-purpose, and no-dead angle mandatory mixing and dispersing equipment.

Electronic Slurry & Double Planetary Mixer
Double planetary mixers are widely used, especially in the field of electronic slurry, whether it is stirring or mixing, the final output effect has been recognized by all walks of life.
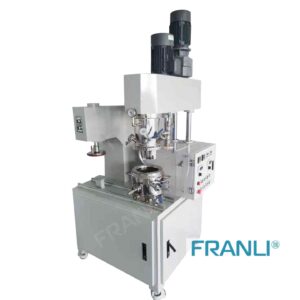
Double Planetary Mixer: Laboratory & Production
There are two types of double planetary mixers produced by FRANLI, which mainly involve two major application fields, one is laboratory research type, and the other is a factory production line

Structural Adhesive Production Equipment & Double Planetary Mixer
The double planetary mixer is one of the ideal types of equipment for low-viscosity materials. This facility has a low and fast mixing dispersing disc, which can complete the functions of high shear and dispersing low viscosity materials at the same time.